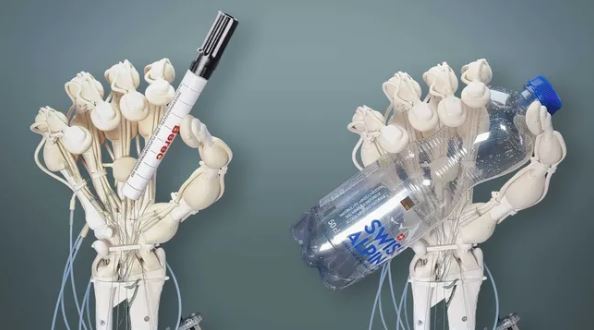
3D printing has found applications in many fields like aerospace, healthcare, construction etc. Now a team of researchers from ETH Zurich showed how a robotic hand can be made more ‘human like’ with 3D printed structures.
It is important to know how researchers used slow-curing 3D printing technology to make robotic hands made of plastics more accurate and human-like.
Slow-curing gives plastics more time to set, helping them capture the details of the human hand and enhancing their durability.
Making automated factories safe with 3D printed robotic hands
The scientists involved in the process used 3D printed bones, tendons and ligaments to create a complete human-like robotic hand structure. To make this happen, the researchers mixed 3D printed hard and soft parts by cross-layering up to four plastics. The same strategy can be employed to create a more durable and complex robotic structure.
The combination of soft and hard 3D printed parts created a soft robotic part that can be scaled up. However, the soft robotic parts made through this process retain their physical properties at large sizes unlike other robots.
This was achieved through the vision-controlled jetting (VCJ) 3D printing technique that can be used to make automated industries safer as they have soft materials robots.
Scientists tried to address the issue of stiffness between robotic 3D printed parts and human bodies with its 3D printed parts that mimic the complexity of nature. 3D printed slow-curing plastics are created by VCJ, giving every layer enough time to set, ultimately delivering a more durable elastic component. The 3D printer involved in the process is guided by cameras and lasers which build each layer in the correct thickness.
With 3D printed parts mimicking the human hand, robots can have the necessary intricate internal structures required for tasks and complex movements.
One of the authors of the Nature paper, Robert Katzschmann, a robotics professor at ETH Zurich said: “Robots made of soft materials, such as the hand we developed, have advantages over conventional robots made of metal. Because they’re soft, there is less risk of injury when they work with humans, and they are better suited to handling fragile goods”.
Robots working in automated factories can cause deadly accidents if they malfunction. One such tragic incident unfolded recently when a South Korean man was crushed to death on a conveyor belt as a robot confused him with a bell peppers box.
Thomas Buchner, a doctoral student at ETH Zurich who worked on this project said: “We wouldn’t have been able to make this robotic hand with the fast-curing polyacrylates we’ve been using in 3D printing so far. We’re now using slow-curing thiolene polymers. These have very good elastic properties and return to their original state much faster after bending than polyacrylates [the standard polymers used in 3D printing”.
Remember, you can post job opportunities in the AM Industry on 3D ADEPT Media free of charge or look for a job via our job board. Make sure to follow us on our social networks and subscribe to our weekly newsletter : Facebook, Twitter, LinkedIn & Instagram ! If you want to be featured in the next issue of our digital magazine or if you hear a story that needs to be heard, make sure to send it to contact@3dadept.com