Acknowledged for its materials expertise, Schunk has added another string to its bow by becoming a service provider for 3D metal printing. Two years ago, the company expanded its portfolio of metal injection moulding process chain with metal 3D printing to meet the production requirements in terms of bionic construction applications and topology optimisation. As part of the new machines installed, there were an ExAM 255 multi-material 3D printing system from AIM3D that came to complete the composite extrusion modelling process (CEM).
During the past two years, both companies have been working together on multiple fronts to enhance the production service at Schunk. These fronts included for instance material developments, such as copper materials and nickel-based materials, extruder cooling or vacuum clamping table applications, and various ways to further develop the service of Schunk as a supplier of 3D metal parts with production batch sizes right down to single items. Indeed, for such small production (rapid prototyping and low-volume production), it’s always interesting to minimize costs to rely on metal 3D printing rather than conventional sintering technology.
In this specific case, the focus was on copper metal 3D printing.
The use of copper in AM
As explained in this exclusive feature dedicated to copper & AM, several manufacturing techniques can be used to process pure copper. For those who are not familiar with this process, let’s note that copper remains one of the rare metals that can be found in nature in a directly usable metallic form. It is a soft, malleable, and ductile material that integrates a very high thermal and electrical conductivity. Its high thermal conductivity is what drives applications with AM but it is also what makes it challenging to process in the AM industry.
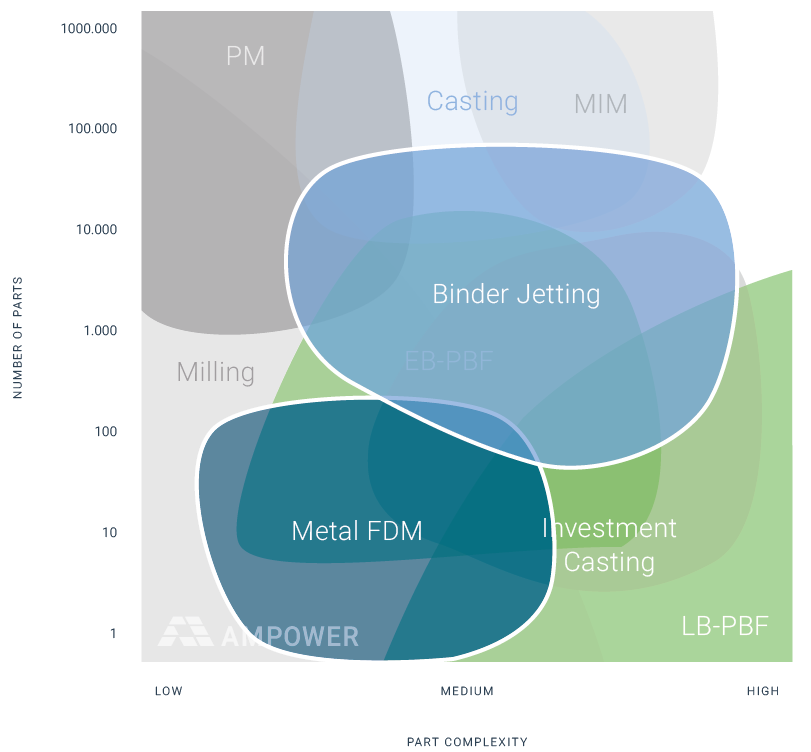
However, the range of industries and applications is wide, including applications focusing on thermal management, primarily in mechanical and plant engineering. There are also applications with an emphasis on low-loss energy transmission, such as e-mobility, welding and hardening technology, as well as in the field of energy supply, AIM3D explains.
According to Christian Stertz, project manager for systems engineering at Schunk, the ExAM 255 system from AIM3D featuring CEM technology enables thermal or electrical conductivity advantages to be retained in 3D printing processes. He sees this as a unique selling point, highlighting better and higher conductivity values on the surface and within the components compared to other additive manufacturing processes. In addition, the CEM process offers material price and resource conservation benefits.
Taking the example of an application, Shunk explains that their team has developed induction hardeners (inductors) for gear wheels in the automotive sector and for chain wheels on chainsaws. This involves induction hardening of a component through partial surface hardening for the highest mechanical requirements. The physical properties of these copper components are a density of approx. 8.5 g/cm³ (rel. approx. 95-96%) with 75-80% conductivity (% IACS). The density values achieved are comparable to metal injection moulding (MIM) processes. The density of the copper, in particular, affects conductivity as well as mechanical properties, such as hardness or wear resistance, a press communication explains.
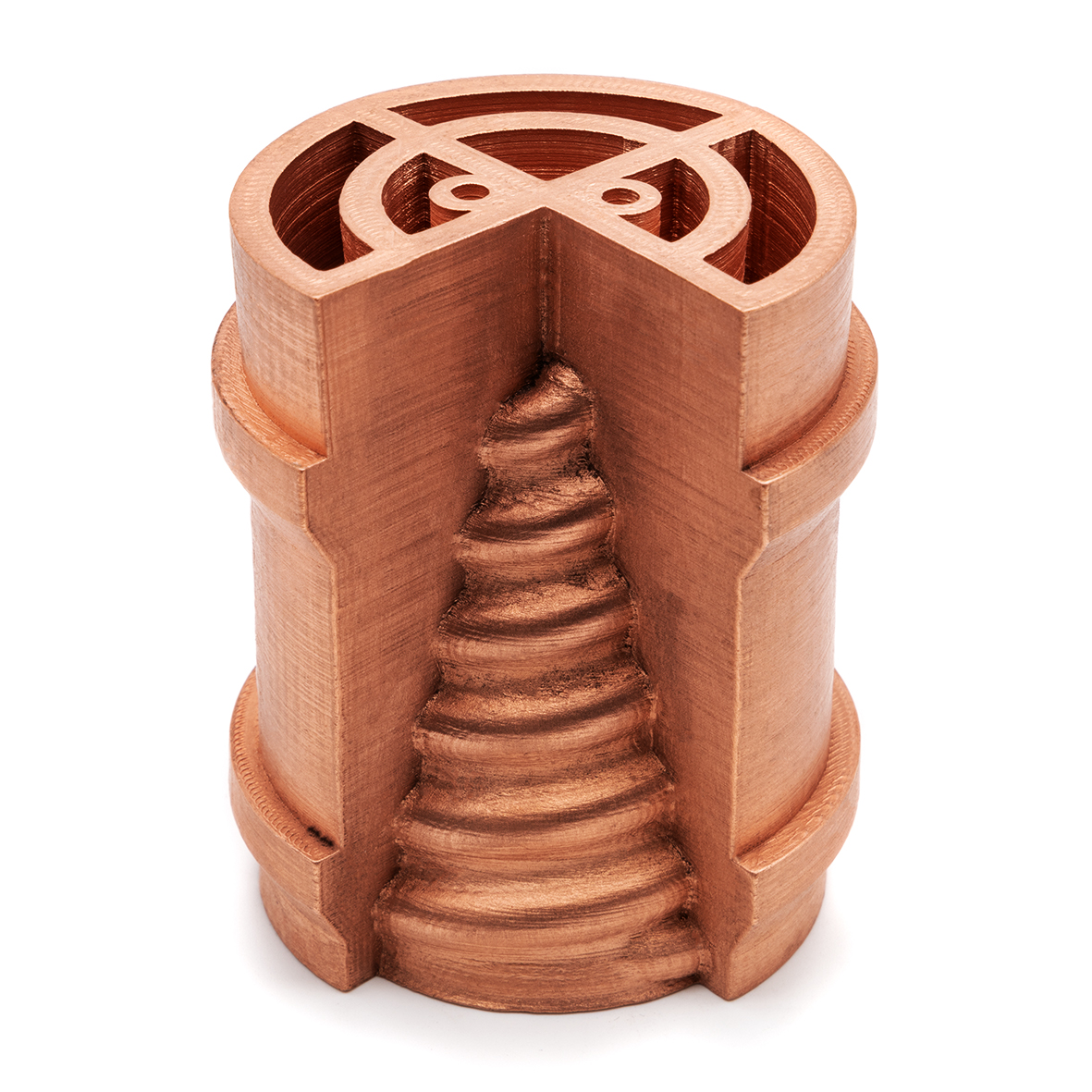
While comparing with conventional manufacturing processes, Stertz notes the benefits of this AM process include a high degree of geometric freedom in the internal channels or undercuts. Bionic structures that save weight and material while increasing functionality are also worth mentioning as they enable cost savings.
As is the case with any AM process, using CEM systems from AIM3D results in savings on machining and tooling costs as it is not a mould-based process. However, the following also applies: the CEM process tends not to be suitable for very simple geometries and for large batches, since well-established series-production processes such as MIM are more advantageous in these cases, the company notes.
“With the further development of customer demands regarding new design and material options, such as bionic design, the range of 3D printing technologies will also continue to evolve. Certain applications favour processing with certain AM methods. Niches will also emerge and competition that squeezes out niches using established processes will continue to drive technology development forwards”, Christian Stertz concludes.
The results of this partnership follows a series of improvements announced by AIM3D for its multi-material 3D printers.
Remember, you can post job opportunities in the AM Industry on 3D ADEPT Media free of charge or look for a job via our job board. Make sure to follow us on our social networks and subscribe to our weekly newsletter : Facebook, Twitter, LinkedIn & Instagram ! If you want to be featured in the next issue of our digital magazine or if you hear a story that needs to be heard, make sure you send it to contact@3dadept.com