Comme un grand nombre de tâches de post-traitement utilisées pour les pièces imprimées en 3D, la galvanoplastie vise à améliorer les propriétés physiques de la pièce en augmentant la résistance à l’usure, la protection contre la corrosion ou l’attrait esthétique, ainsi que l’épaisseur. Le problème, c’est que très peu de personnes dans l’industrie savent exactement ce qu’est le processus, comment il fonctionne et comment il peut être appliqué aux pièces imprimées 3D. Cet article a pour objectif de lever le voile sur ce concept.
Également connue sous le nom d’électrodéposition ou de dépôt électrochimique, la galvanoplastie est un procédé de revêtement de surface électrochimique qui utilise un courant électrique pour réduire les cations métalliques dissous à la surface d’une électrode, appelée cathode, et former une fine couche de métal cohérente. En d’autres termes, ce procédé permet de réduire les ions métalliques sur la surface d’une pièce conductrice afin d’y appliquer un revêtement métallique.
Il existe un grand nombre de métaux pouvant faire l’objet d’une galvanoplastie, mais les plus couramment utilisés sont le cuivre, le nickel, le chrome, l’étain, le plomb, le zinc, le laiton (un alliage de Cu et de Zn), l’or, l’argent et le platine. En termes simples, le processus vise à répondre à deux objectifs principaux : décoratif et fonctionnel.
Par exemple, la galvanoplastie décorative est souvent utilisée dans l’industrie automobile, où un revêtement chromé décoratif peut être reconnu sur des éléments en plastique tels que les grilles, les pare-chocs, les jantes ou les poignées de porte. On peut également utiliser la galvanoplastie décorative pour le dépôt de métaux précieux (par exemple, l’or et l’argent) sur des articles de luxe tels que les montres ou les bijoux en général. En outre, la plupart des gens utilisent la galvanoplastie pour donner à leurs pièces en plastique l’aspect de pièces métalliques polies.
Le processus de galvanoplastie fonctionnelle vise à obtenir un revêtement métallique qui, entre autres propriétés, empêchera la corrosion des matériaux du substrat cible. Dans l’industrie aéronautique, par exemple, où les métaux les plus courants sont le cadmium, le chrome dur, le zinc, le zinc-nickel, le platine, l’étain-zinc, etc., quelques exemples de pièces pouvant être revêtues par galvanoplastie sont les trains d’atterrissage, les turbines de moteur ou les roulements.
Ce but fonctionnel peut également impliquer plusieurs autres objectifs : la nécessité d’augmenter la capacité de température de l’impression, le blindage EMI, l’amélioration des propriétés mécaniques (rigidité et résistance), une meilleure durabilité, un revêtement barrière pour arrêter le dégazage (c’est-à-dire un environnement sous vide) ou empêcher l’attaque de produits chimiques sur les substrats de résines imprimées. Il peut également réduire l’inflammabilité et les fumées toxiques provenant de la combustion. Cela signifie qu’une pièce imprimée en 3D qui a subi une galvanoplastie peut également servir de pièce de remplacement pour un composant donné qui avait une fonction spécifique dans un assemblage.
Dans le post-traitement des pièces imprimées en 3D, la galvanoplastie n’est qu’un moyen de finition de surface, tout comme l’impression 3D n’est qu’un outil de fabrication. Pour réussir à obtenir un revêtement métallique sur une pièce imprimée en 3D par le processus de galvanoplastie, il faut savoir à quel type de matériau de substrat on a affaire, s’il s’agit d’une pièce en plastique ou d’une pièce à base de métal, et quelle est la fonction de la couche métallique déposée, décorative ou fonctionnelle, et nous sommes prêts à commencer.
Avec quelle technologie d’impression 3D peut-on utiliser la galvanoplastie ?
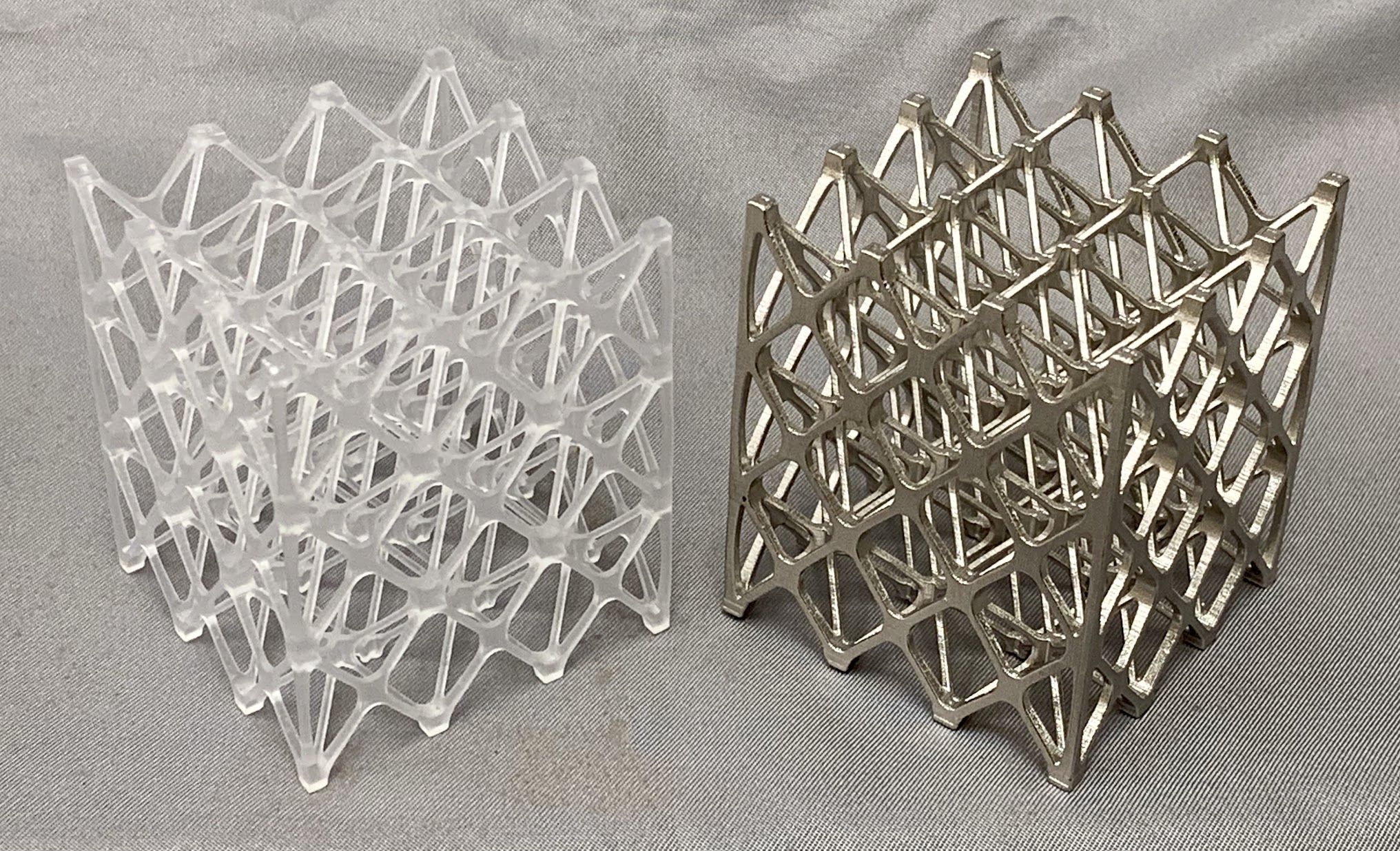
En général, la technologie d’impression 3D utilisée pour la fabrication des pièces n’a pas vraiment d’impact sur la tâche d’électrodéposition. Cependant, on se rend compte que les pièces imprimées en 3D en photopolymère, en poudre fusionnée/frittée ou en filament peuvent être plaquées. Les pièces photopolymères sont les plus faciles à revêtir, mais elles doivent être nettoyées et bien durcies. La complexité des pièces fusionnées/frittées réside dans le fait qu’elles peuvent présenter une certaine porosité et que les surfaces peuvent être rugueuses. La plupart des imprimantes 3D peuvent être configurées pour rendre la peau extérieure de la pièce étanche, mais il peut y avoir une certaine variabilité dans les lots. La rugosité de la surface peut améliorer l’adhérence, mais il est plus difficile d’obtenir une finition brillante. Le procédé de fabrication FDM reste le plus difficile à traiter via la galvanoplastie, car la pièce présente presque toujours une porosité et la taille des pores peut être très importante dans certaines parties de la pièce. Les pièces doivent être scellées avant la métallisation, ce qui augmente le coût du traitement.
Cela dit, quel que soit le procédé de FA utilisé pour la fabrication des pièces imprimées en 3D, ce qui compte vraiment, c’est le matériau du substrat dont la pièce est faite et sa géométrie : les pièces métalliques ne posent guère de problèmes par rapport aux pièces en plastique, pour lesquelles l’opérateur doit s’assurer que le matériau utilisé pour la fabrication peut résister au bain chimique qui sera utilisé pour le processus de galvanoplastie.
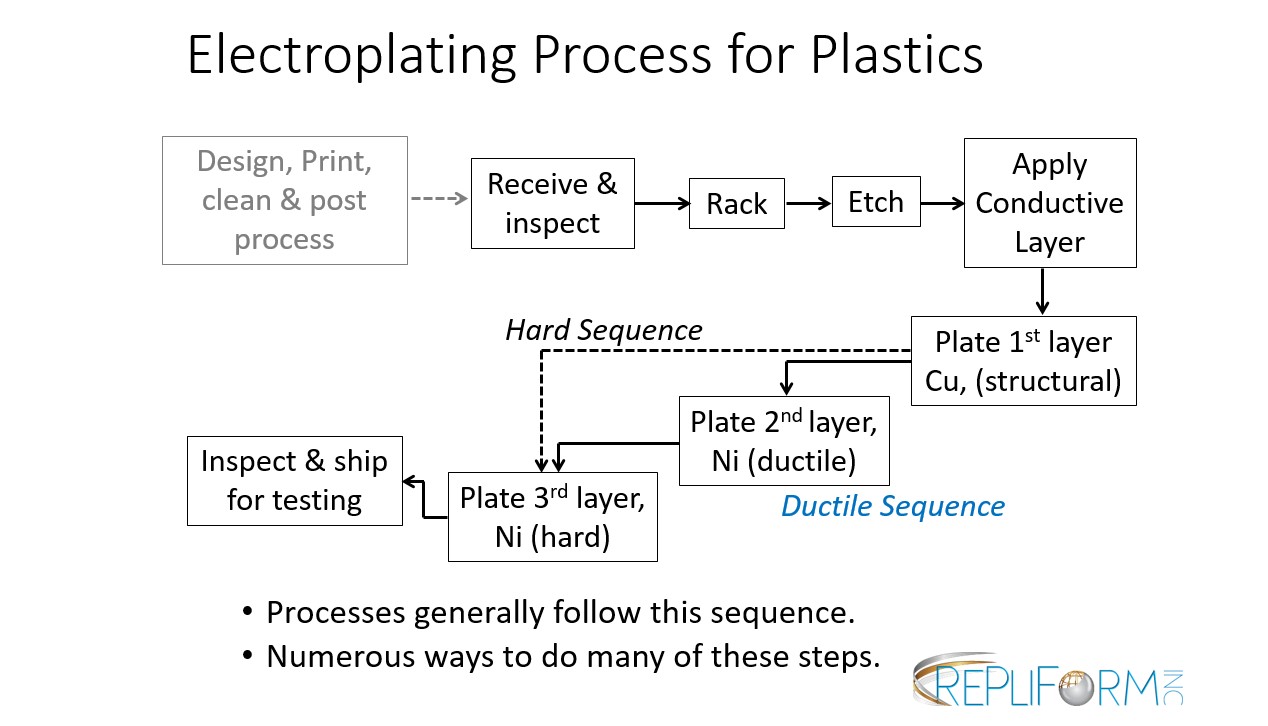
En outre, plus la géométrie de la pièce est complexe, plus la non-uniformité du métal déposé sur sa surface est importante. Cela rend le processus d’électrodéposition difficile à contrôler, et il n’est pas toujours possible d’obtenir une distribution uniforme de la couche de métal sur toutes les surfaces actives à électrodéposer sans développer des stratégies d’atténuation spécifiques.
Les pièces imprimées en 3D étant généralement complexes, il est souvent recommandé d’utiliser une approche d’ingénierie assistée par ordinateur pour la galvanoplastie. Une telle approche vise à assurer l’analyse du processus en amont afin de reconnaître les zones de surface sous-plaquées et sur-plaquées. De cette manière, il est possible de prévoir la distribution de l’épaisseur de la couche de métal sur la pièce imprimée en 3D avant que le processus de galvanoplastie ne soit exécuté. Cela donne à l’opérateur la possibilité d’optimiser le réglage du processus et de s’assurer que la pièce est plaquée correctement du premier coup et qu’elle est conforme aux spécifications requises en matière d’épaisseur de la couche métallique.
Comment appliquer la galvanoplastie sur des pièces imprimées en 3D ?
La galvanoplastie sur les pièces imprimées en 3D est assez similaire aux procédés de galvanoplastie utilisés pour les pièces en plastique ou en métal. Il faut commencer par des pièces non contaminées, puis graver la surface, appliquer une couche conductrice avec du nickel ou du cuivre autocatalytique, puis appliquer une séquence de métallisation pour obtenir la fonctionnalité souhaitée.
De plus, pour les pièces en plastique imprimées en 3D, il est important de s’assurer que la pièce est métallisée au préalable afin que la surface puisse conduire le courant. Comme le montre l’image ci-dessus, cette étape de métallisation est généralement réalisée par un dépôt chimique et après une préparation adéquate de la surface, composée d’un certain nombre d’étapes de prétraitement : nettoyage, prétrempage, gravure, neutralisation, pré-activation, activation et accélération. Une fois le prétraitement de la surface effectué, on peut passer à l’étape de la galvanoplastie.
Déterminer comment la galvanoplastie modifie les propriétés mécaniques des pièces imprimées en 3D
Par ailleurs, pour déterminer comment la galvanoplastie modifie les propriétés mécaniques des pièces imprimées en 3D, il faut comprendre plusieurs mécanismes. L’électrodéposition sur des plastiques imprimés en 3D, par exemple, permet de créer un composite renforcé et d’ajouter une fonctionnalité métallique à des métaux non conducteurs. Pour créer un composite métal-résine à partir du procédé SLA et d’une galvanoplastie, par exemple, il faut déterminer si un plastique plaqué peut combler un vide entre le métal imprimé et le plastique, comprendre la règle des mélanges pour estimer les propriétés de traction à partir des constituants ou apprendre à faire de la place pour le revêtement lorsque l’on a déjà la conception.
Pour comprendre ce type de mécanique et bien d’autres, des entreprises comme RePliForm Inc. travaillent avec de nombreux fournisseurs de systèmes et fabricants de résine pour tester la résistance à la traction et à la flexion. En effet, lorsque les propriétés de la résine changent, celles du revêtement changent également, ce qui influe sur la façon dont la conception de la pièce change.
Cela dit, en ce qui concerne la création d’un composite métal-résine, il s’avère que traiter la pièce plaquée comme un composite et utiliser la règle des mélanges – une équation très basique utilisée pour estimer la résistance des pièces composites – fonctionne étonnamment bien.
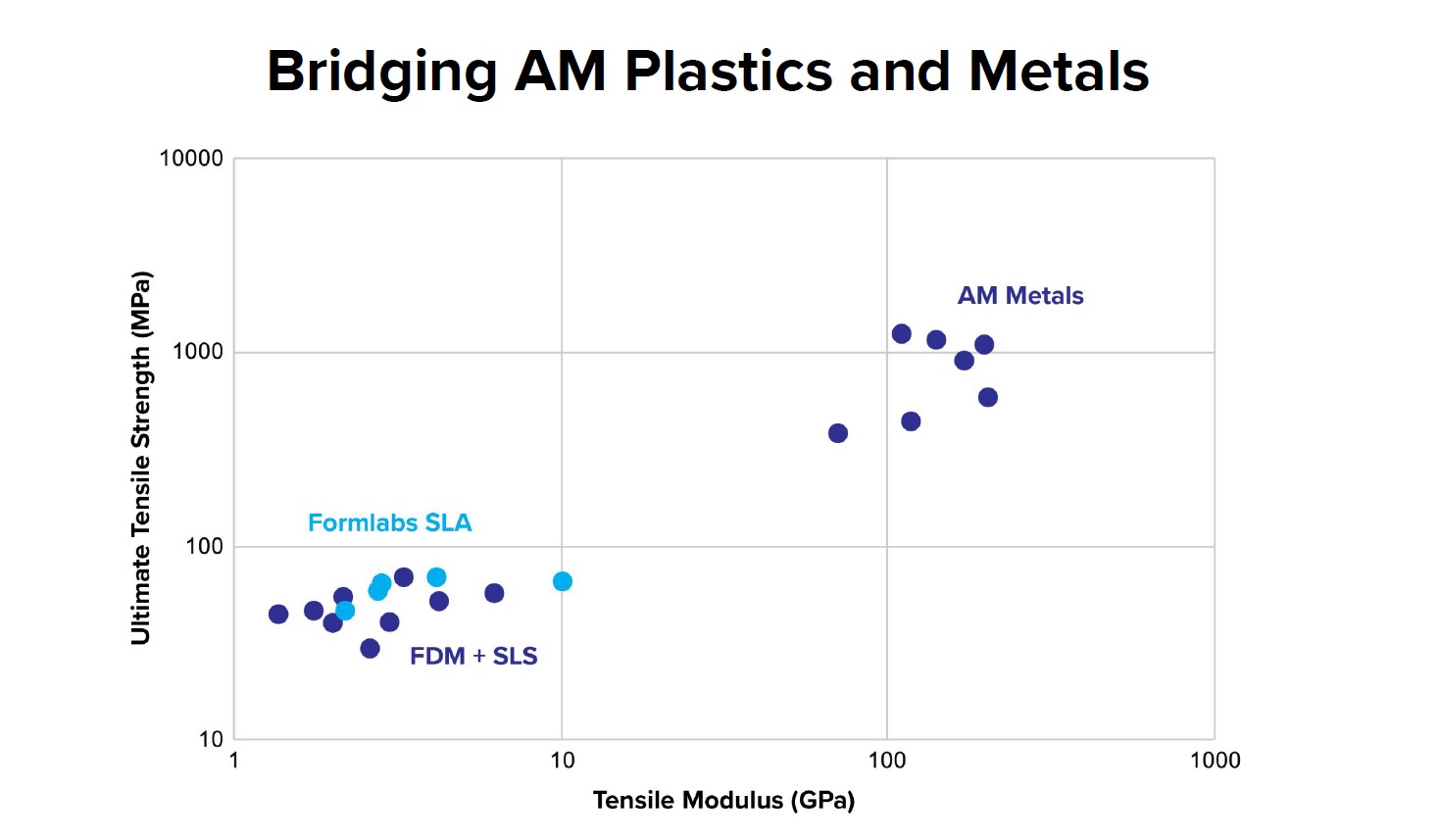
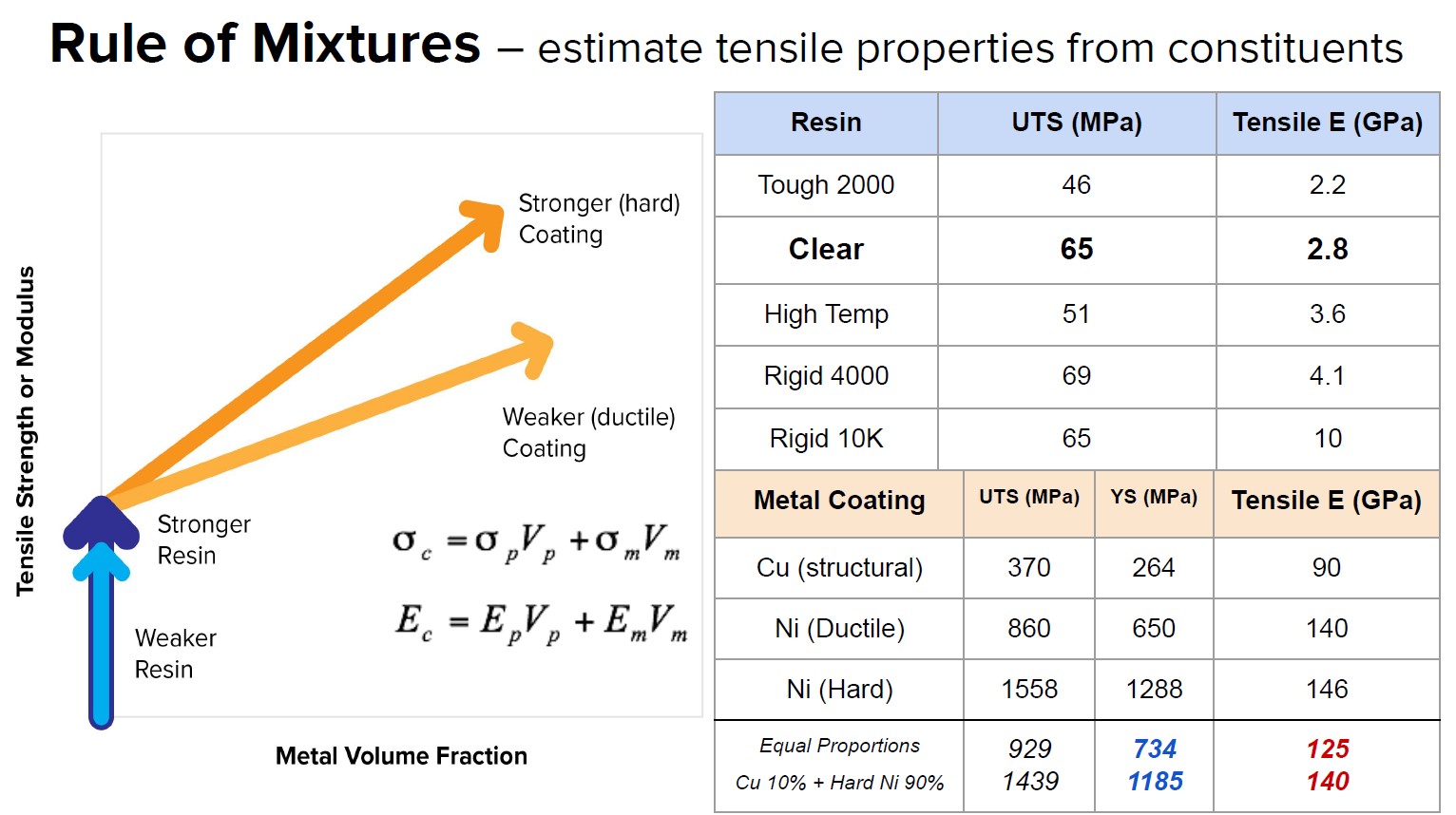
Améliorer la galvanoplastie grâce à une approche d’ingénierie assistée par ordinateur
L’amélioration de la galvanoplastie via une approche d’ingénierie assistée par ordinateur est importante alors que nous naviguons dans l’ère de l’industrie 4.0 et des concepts de fabrication intelligente, dont l’impression 3D et le jumeau numérique font tous deux partie.
L’approche de l’ingénierie assistée par ordinateur repose sur la reconnaissance des performances du processus de galvanoplastie et sur son optimisation ultérieure avant tout passage au mouillé réel. Cela peut se faire en créant une représentation virtuelle (jumeau numérique) de l’installation réelle du procédé de galvanoplastie dans un environnement informatique. Ce jumeau numérique est basé sur les informations techniques provenant du site de traitement réel, en tenant compte de l’infrastructure de la ligne de placage, des paramètres de fonctionnement du processus de placage, des performances électrochimiques du bain de placage utilisé, des caractéristiques géométriques du composant à revêtir et d’une disposition spécifique du rack que nous avons envisagée.
Grâce à cette approche, il est possible de prévoir la densité du courant et la répartition de l’épaisseur de la couche métallique sur toutes les surfaces actives à revêtir, en reconnaissant les problèmes de risque de surface en termes de sur- et de sous-revêtement. Une fois cette connaissance acquise, il est possible de concevoir et d’évaluer une stratégie d’atténuation appropriée, adaptée à la configuration du processus et aux spécificités de la géométrie de la pièce. Ceci est extrêmement important dans le cas de pièces géométriquement complexes telles que les pièces imprimées en 3D, pour lesquelles ni la modification de l’agencement du bâti ni l’ajustement des paramètres du processus ne permettront d’obtenir une couverture de revêtement homogène.
Pour ces pièces complexes, la configuration du processus devra être améliorée et un concept d’outillage dédié devra être développé et testé. Dans la vie réelle des procédés, l’évaluation des risques et l’élaboration d’une stratégie d’atténuation appropriée, y compris les essais, nécessitent des mois et des mois de travail acharné et de ressources gaspillées. L’approche de l’ingénierie assistée par ordinateur nous permet de le faire en quelques minutes, en éliminant un nombre excessif d’essais humides et en économisant ainsi du temps, de l’argent et des ressources de toutes sortes. En utilisant l’ingénierie assistée par ordinateur, nous améliorons notre connaissance du processus et nous contrôlons ses performances, ce qui nous permet d’obtenir la meilleure qualité possible, à chaque fois.
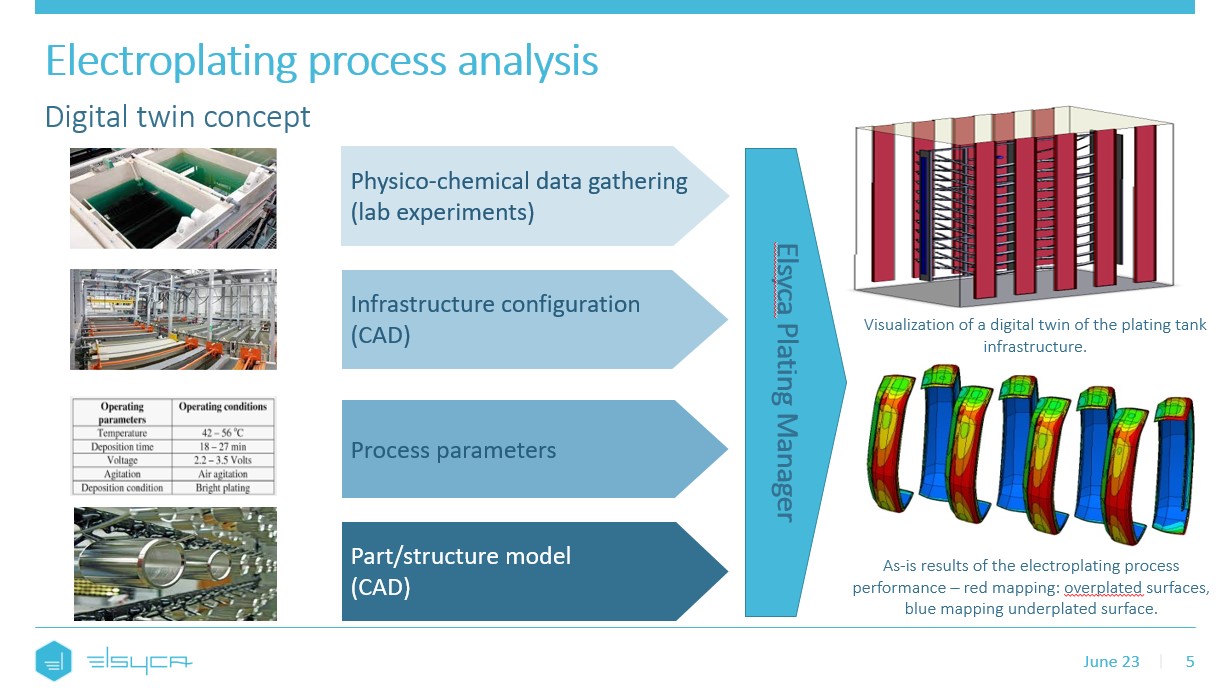
Alors… ?
Le processus de galvanoplastie est sans aucun doute une tâche puissante en matière de post-traitement. Même si une approche IAO peut contribuer à accélérer le processus, il convient de noter qu’il ne semble pas y avoir de méthode populaire pour automatiser les étapes du processus. Comme on l’a vu avec l’enlèvement de poudre, il faudra beaucoup de collaboration entre les fabricants de machines et de matériaux et les experts en galvanoplastie pour faire progresser les étapes du processus et favoriser son utilisation dans les applications d’impression 3D industrielle.
Ce dossier a été initialement publié dans le numéro de Mai/Juin de 3D ADEPT Mag.
Auteurs
Ce dossier exclusif a été co-écrit par Sean Wise, président de RePliForm Inc. et Agnieszka Franczak, responsable de la division Surface Finishing chez Elsyca N.V..
RePliForm est un expert de la galvanoplastie des plastiques imprimés en 3D ainsi que d’autres matériaux non conducteurs. Dans le but d’aider ses clients à créer une pièce composite qui peut élargir l’enveloppe de ce qui est possible avec un plastique imprimé en 3D, RePliForm adapte continuellement les processus de galvanoplastie à une variété de matériaux et de géométries complexes. L’entreprise a récemment mis au point un moyen inattendu de fabriquer un composite renforcé et d’ajouter une fonctionnalité métallique à des matériaux non conducteurs grâce à l’électrodéposition de plastiques imprimés en 3D. Vous pouvez contacter l’entreprise ici pour plus d’informations sur le sujet : info@RePliFormInc.com.
Elsyca est spécialisée dans l’électrochimie et les solutions d’ingénierie assistée par ordinateur. L’électrodéposition, qui est l’un des processus électrochimiques, est l’un des principaux centres d’intérêt de l’entreprise, car elle est largement utilisée dans une variété d’applications, à travers plusieurs industries. L’équipe d’Elysca développe des solutions logicielles dédiées à l’analyse et à l’optimisation des procédés de galvanoplastie et fournit des services d’ingénierie assistée par ordinateur à ceux qui sont confrontés à des défis en matière de contrôle des procédés, de qualité des revêtements et de reproductibilité. La galvanoplastie des pièces imprimées en 3D s’inscrit donc parfaitement dans le champ d’intérêt de l’entreprise. Elysca a récemment présenté comment elle aide les industriels à faire passer les procédés de galvanoplastie au niveau supérieur grâce à une approche d’ingénierie assistée par ordinateur. Vous pouvez contacter l’entreprise ici pour plus d’informations sur le sujet : info@elsyca.com.