Avec la fabrication additive grand format, on ne s’attend généralement pas à autre chose qu’à une grande pièce imprimée en une seule fois, mais avec Thermwood, il y a souvent plus que ça. La dernière réalisation de l’entreprise est la production additive d’un outil de forme allongée, fruit d’une collaboration avec Spirit AeroSystems, Inc. et Techmer PM.
Au cas où vous ne les connaîtriez pas, sachez que Spirit AeroSystems est l’un des plus grands fabricants d’aérostructures pour les avions commerciaux, les plateformes de défense et les jets d’affaires/régionaux. Techmer PM, quant à elle, est une société de conception de matériaux qui travaille en partenariat avec des transformateurs de plastique, des équipementiers et des concepteurs pour résoudre certains de leurs problèmes de fabrication les plus urgents.
Avec le fournisseur et développeur de systèmes de fabrication additive à grande échelle, les deux entreprises réalisent ce qui est décrit comme le plus grand outil de forme extensible jamais imprimé en 3D. Mesurant 6 ½ pieds de large sur 15 pieds de long (195 x 366 cm), le projet d’outil permet plusieurs améliorations à plusieurs niveaux du processus de fabrication.
L’un des éléments cruciaux de ce projet a été le matériau polymère utilisé. Les partenaires ont d’abord misé sur le polycarbonate chargé de fibres de carbone en raison de sa capacité à offrir une résistance suffisante et à supporter les forces importantes utilisées dans le processus de formage par étirement. Le fait est que travailler avec ce matériau aurait conduit à une plus grande lubrification. Techmer PM a donc mis à profit son expertise dans les matériaux pour élaborer une nouvelle formulation de polycarbonate contenant un lubrifiant interne en plus de la fibre de carbone, supprimant ainsi tout besoin de lubrification supplémentaire.
Le processus de fabrication lui-même a nécessité l’utilisation du LSAM 1020 de Thermwood, un système d’impression et de découpe à double portique qui a également joué un rôle clé dans un programme délivré à Boeing, pour le développement d’un outil de cuisson. Fait intéressant, pour gagner du temps, l’équipe de Thermwood a décidé d’imprimer la pièce en quatre sections. Thermwood explique que, malgré le fait que la machine soit basée sur la technologie d’impression par couches verticales, l’impression de l’outil en une seule pièce aurait obligé l’opérateur à attendre que chaque couche imprimée refroidisse suffisamment avant d’ajouter la couche suivante – ce qui aurait donc entraîné 58 heures d’impression continue pour produire un outil d’une seule pièce. En imprimant section par section, ils ont obtenu un temps d’impression total de 29 heures et 20 minutes – pour 3 613 livres (1639 kg) de matériau.
Après cette étape, les étapes suivantes étaient évidemment l’usinage et l’assemblage. « Les faces d’accouplement ont été usinées à plat, à l’exception de bossages légèrement surélevés qui garantissent un bon espacement pour l’adhésif. L’adhésif n’est qu’une partie d’une approche multipartite utilisée pour fixer de manière permanente et sûre les pièces les unes aux autres. Toutes ces surfaces sont d’une grande précision », note Thermwood.
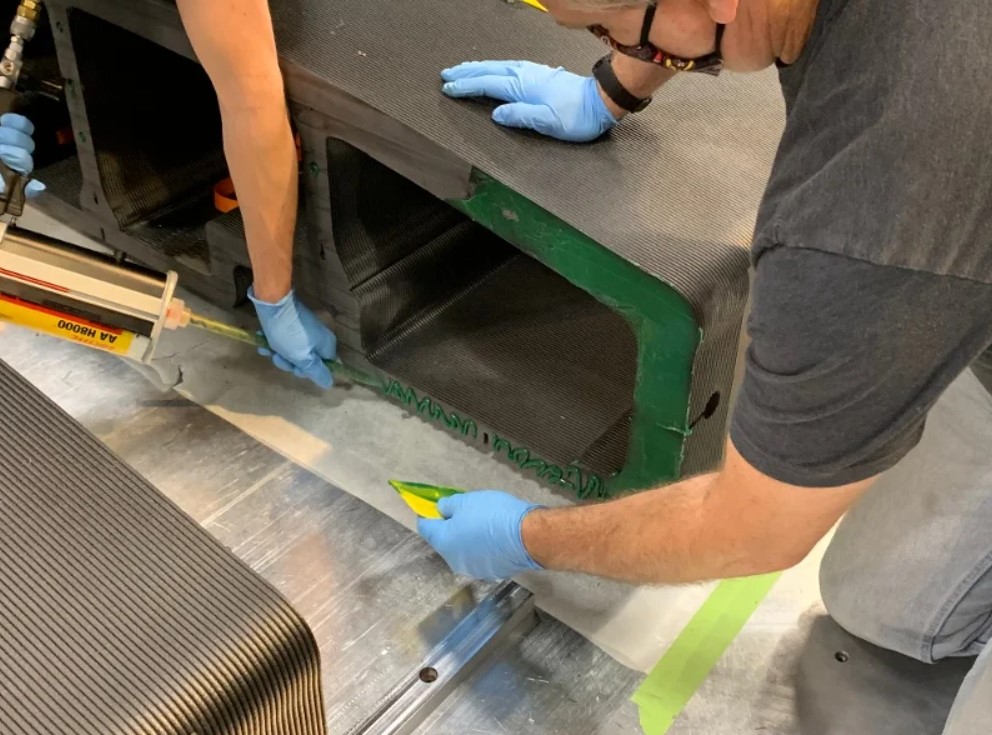
En outre, en raison du poids lourd des pièces et du temps ouvert relativement court de l’adhésif, « le temps disponible pendant l’assemblage pour appliquer l’adhésif et assembler solidement les pièces est limité. » « Les pièces doivent être poussées l’une contre l’autre tout en étant alignées, littéralement à quelques millièmes de pouce près, et doivent être accouplées de manière absolument égale et carrée. Cela s’est avéré assez facile grâce au mécanisme de table d’impression en couches verticales installé sur la machine LSAM.
Les pièces ont été soigneusement ajustées à la main. Ensuite, une pièce a été fixée à la table de la machine et l’autre au mécanisme qui déplace la table verticale. Le mécanisme de la table verticale a ensuite écarté les pièces d’une vingtaine de centimètres, de la colle a été appliquée et le mécanisme de la table verticale a remis les pièces ensemble, d’équerre et parfaitement alignées », peut-on lire dans un rapport.
Au final, Spirit AeroSystems a étiré 10 panneaux de revêtement en aluminium 2024 T3 de 0,050″ (0,13 cm) d’épaisseur jusqu’à 5 % d’allongement. Le contrôleur de la presse a montré que chaque mâchoire saisissant la feuille d’aluminium supportait une charge de ~100 tonnes, soit ~200 tonnes au total. Tout a été maintenu dans les mêmes conditions que pour une pièce de production et, même si l’outil imprimé est considérablement plus léger que leurs outils traditionnels, il a semblé fonctionner de manière similaire.
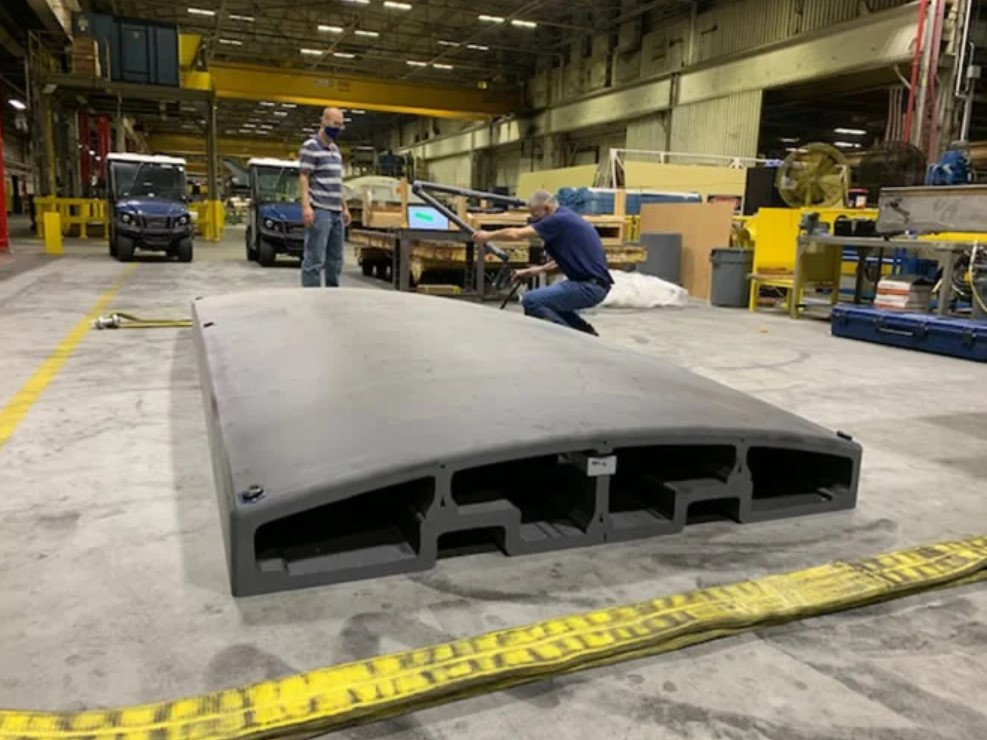
Le projet pourrait être un succès, mais Thermwood a déclaré qu’il restait encore beaucoup de chemin à parcourir. Il y a d’autres tests à effectuer et d’autres données à collecter, mais il semble que de grands outils de formage par étirement en composite imprimés en 3D peuvent être produits en utilisant les matériaux et les équipements actuels, ce qui permet d’économiser beaucoup de temps et d’argent et ouvre une nouvelle application à cette nouvelle technologie passionnante, conclut la société.
N’oubliez pas que vous pouvez poster gratuitement les offres d’emploi de l’industrie de la FA sur 3D ADEPT Media ou rechercher un emploi via notre tableau d’offres d’emploi. N’hésitez pas à nous suivre sur nos réseaux sociaux et à vous inscrire à notre newsletter hebdomadaire : Facebook, Twitter, LinkedIn & Instagram ! Si vous avez une innovation à partager pour le prochain numéro de notre magazine numérique ou si vous avez un article à faire connaître, n’hésitez pas à nous envoyer un email à contact@3dadept.com.