Two years ago, when we discussed the fundamentals at the heart of micro 3D printing technologies, we didn’t realize how strong the impact of these technologies would be across different industries. When you think you’ve seen it all, you stumble upon something smaller and smaller. Whether miniaturized devices are made for electronics, MedTech or consumer goods, product designers demonstrate that certain technologies can deliver the desired accuracy and micron-level precision cost-effectively. Yet, micro 3D printing remains one of the least highlighted sectors in the AM industry. This observation is particularly striking when one realizes that most companies operating in the market of professional and large industrial 3D printing technologies are dealing with corporate restructuring or financial struggles. To understand why the micro 3D printing niche is on a steady path, we asked John Kawola, CEO of Boston Micro Fabrication (BMF) a few technical questions.
Simply put, BMF focuses on scaling micro-3D printing technology to a range of industries that demand a high level of resolution and precision. The company develops a Projection Micro Stereolithography (PµSL) technology that can hold micro-precision injection molded tolerance, down to +/-10µm tolerance. To do so, it utilizes ultra-high resolution 3D printing technology, software, specialty materials and precision motion control to rapidly manufacture parts. Founded in 2016, the company, 3D ADEPT Media has been following the key milestones of the company (its various funding rounds, the launch of its microArch S350 solution, its debut on the dental market or even its partnership with Horizon) over time and was eager to discover how it perceives this market and where it is heading.
3DA: Industrials are looking to adopt AM to foster industrialization. What would you say the key objectives of micro 3D printing are?
John Kawola (JK): For many years, molding for prototyping was the only solution available for micro-sized parts, but it was a time-consuming and expensive process. Today, manufacturers and engineers are using micro 3D printing as a cost-effective option that allows them to quickly move from prototyping to production and push the boundaries of innovation in their industries.
In some instances, engineers are looking for a level of precision that is simply impossible to achieve with traditional manufacturing methods. Many of our customers are looking for a solution that allows them to consistently achieve extremely small features and complex geometries with high-precision, resolution and accuracy.
3DA: Where does micro 3D printing currently excel – in terms of applications?
JK: Micro 3D printing is a unique solution for creating high-precision parts across a diverse range of industries from medical devices and technology, electronics, optics and photonics, microfluidics, and consumer packaged goods. Many of these parts and resulting products are important pieces in our modern world – from high-performance electrical connectors to personalized healthcare devices.
As products and technology get smaller, so do the intricacies of the parts that hold them together. Micro 3D printing excels in allowing manufacturers to produce innovative, micro-scale parts and products with unprecedented precision and design flexibility. At BMF, we are committed to offering solutions that allow engineers and product designers to innovate with micro-sized parts that are highly precise and accurate. For example, we recently launched the industry’s first hybrid micro-precision 3D printer series, the microArch D1025, to offer more flexibility for customers looking for high precision 3D printing solutions. The dual-resolution printer allows users across industries and applications to print two resolutions, either in 10µm or 25µm, within a single layer or in different layers.
3DA: BMF recently partnered with micro component and coatings expert Horizon Microtechnologies to create an end-to-end offering that begins with initial product design through manufacturing. Could you provide further details on this collaboration?
JK: Horizon Microtechnologies specializes in in-house coating processes that enhance the functionality of microstructures, including coatings in copper, ceramic-like metal oxide, and transparent conductive coatings. These coatings can be applied precisely and selectively to parts of virtually any shape. The company acquired a BMF microArch S240 micro-precision 3D printer last year, allowing them to produce intricate micro-AM parts and apply proprietary coatings. The microArch S240 offers high precision and is designed for industrial production. This acquisition enables Horizon to act as a one-stop-shop for design, manufacturing, and delivery, streamlining R&D and improving customer interaction. Some of the benefits of vertical integration include reduced development time and costs, improved quality control, and elimination of dependencies on external vendors, delivering highly accurate components. Horizon can support customer development efforts by designing functional parts best suited to their 3D micro-printing and coating capabilities.
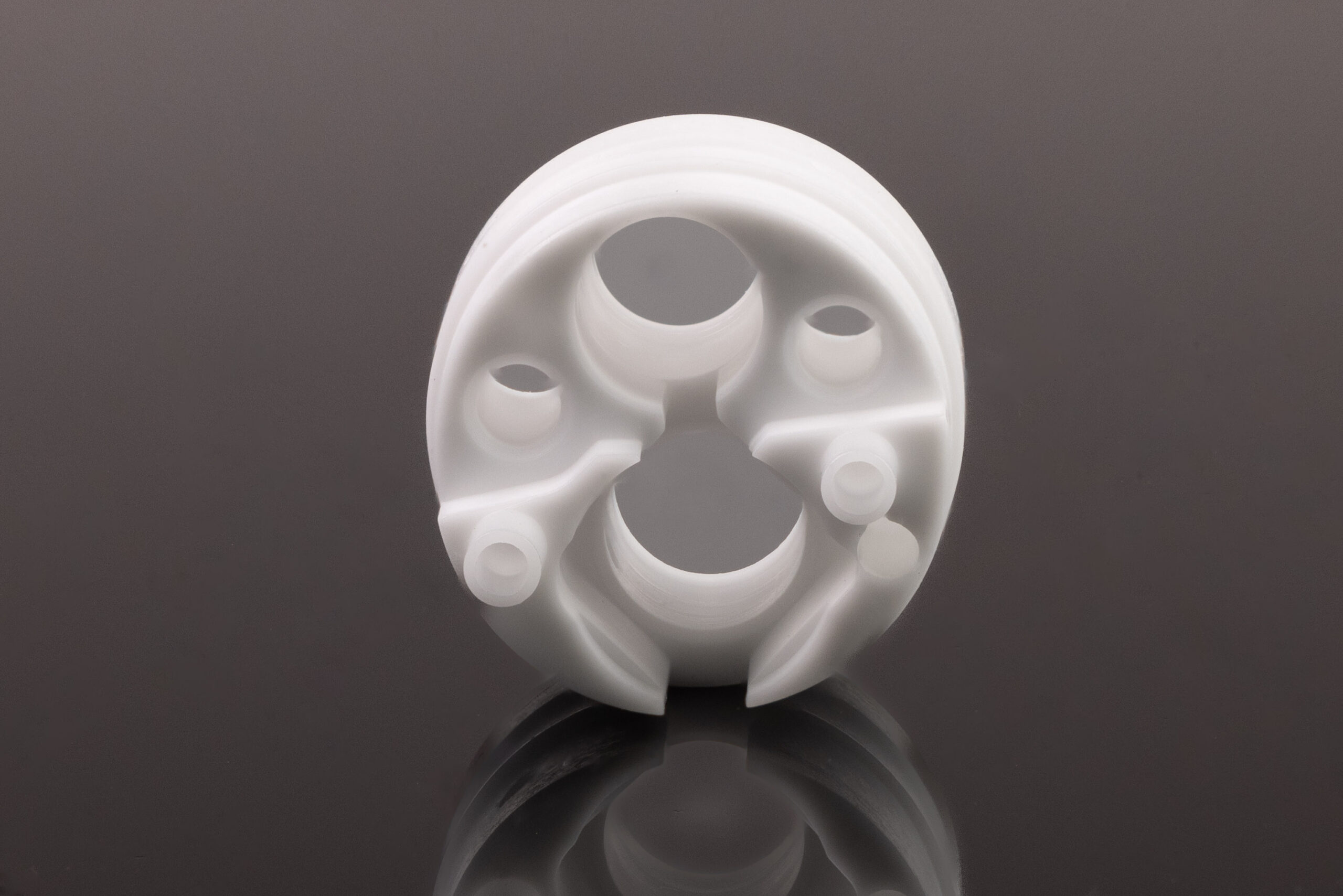
3DA: What advancements can we expect to foster the adoption of micro 3D printing?
JK: Trends of miniaturization and personalization are sweeping across industries and propelling product innovation. Regardless of industry, there’s an urgent need for highly precise and accurate manufacturing methods that allow engineers and product designers to consistently create small-scale parts with the precision, resolution and accuracy needed to move industries forward. Micro 3D printing is one such solution.
From advancements in consumer goods – such as our shrinking cell phones that are simultaneously more powerful with each iteration – to innovative drug delivery methods – such as micro-needle patches – the adoption of micro 3D printing as a manufacturing solution is well underway.
3DA: What can we expect from BMF moving forward?
In 2023, BMF experienced a landmark year where the company experienced 30% sales growth, secured its Series D funding, launched in new markets, such as in dental with the world’s thinnest cosmetic dental veneer (3x thinner than alternatives), and expanded its San Diego Research Institute (SDRI), growing to 200+ team members globally and serving more than 1,800 companies worldwide. A huge component of BMF’s success lies in our ability to not only cater to our customers’ needs, but also our dedication to creating solutions to meet future market needs by actively seeking out opportunities to innovate.
In April 2024, BMF received U.S. FDA 510(k) clearance for its innovative UltraThineer zirconia material, which allows dental labs to offer this highly precise alternative to traditional veneers for dental practices across the U.S., so that patients can experience a more comfortable and less invasive option for tooth restoration and aesthetic improvement. BMF has secured partnerships with dental labs across the country to start piloting test cases and has begun construction of a new dental lab facility at their headquarters outside of Boston, MA, due to be completed by the end of the summer.
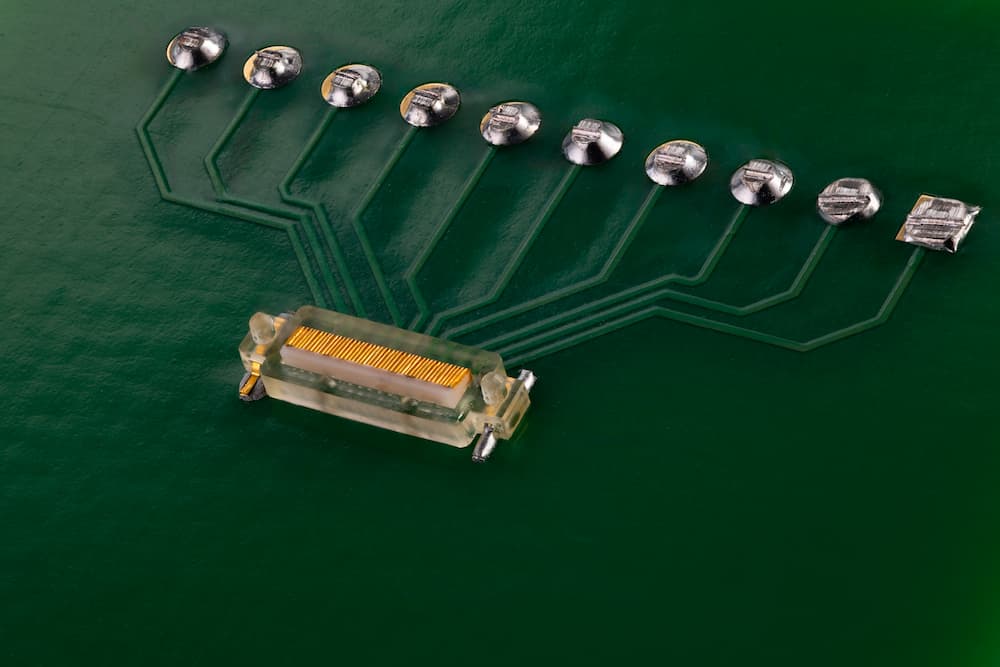
To better support the use of highly precise, microfluidic solutions in advanced drug development, pharmaceutical and cosmetic research, BMF recently introduced BMF Biotechnology Inc., which is dedicated to developing and commercializing innovative BioChips (organ-on-a-chip platforms) to help accelerate new drug and cosmetic development. BMF Biotechnology will be continuously innovating to enhance the functionality and performance of the BioChip platforms, with a focus on improving human tissue replication, disease modelling, and drug response validation and prediction capabilities.
As the AM industry continues to evolve, BMF is committed to providing technological solutions that can solve real-world problems and looking for the ways in which its PµSL technology is uniquely suited to enable innovation and end-use products across industries.
This interview has first been published in the July/August edition of 3D ADEPT Mag.