Given the expensive cost of metal additive manufacturing, applications in demanding sectors generally remain the same. They are carried out with materials such as titanium, Inconel, aluminium or steel. Surprisingly, the recent years saw the emergence of Copper 3D Printing/Additive Manufacturing. How? Why now? And for what type of applications? That’s what we are going to discuss in this dossier.
This paper aims to present a detailed insight into the use of pure copper in additive manufacturing and how professionals can make the most of it. To explore this topic, we have invited a 3D printer manufacturer, Farsoon Technologies, and a material producer, Elementum 3D. Wenyu Guo, Metal Product Line Manager at Farsoon Technologies will speak on behalf of the company whereas Jacob Nuechterlein, President & CEO of Elementum 3D will share the company’s expertise in this dossier.
Researches and the latest developments from Optomec, Fraunhofer Institute for Laser Technology (ILT) and The Virtual Foundry have also been mentioned.
Pure Copper vs Copper?
Among all metals that exist, copper is one of the rare ones that can be found in nature in a directly usable metallic form. It is described as a soft, malleable, and ductile material that integrates a very high thermal and electrical conductivity.
To test if copper is pure, those who do not have a technical background use what we like to call the “good old grandma recipe”: they apply lemon juice over it, then rinse it with water and if it glows like reddish colour, then it is a sign of pure copper.
Otherwise, the density of the metal enables to determine its “purity”. The professional just has to weigh the component on electronic weight measurement machine and volume by dimension.
In the manufacturing industry, this metal enables a certain range of industrial applications.
Which manufacturing technique for pure copper?
Interestingly, it should be noted that the use of pure copper in production processes does not start with additive manufacturing.
Prior to be leveraging by additive manufacturing experts, copper can be utilized in various processes: the old traditional process for instance – which is based on roasting, smelting in reverbatory furnaces or electric furnaces for more complex ores. It enables the production of matte and converting for production of blister copper which is further refined to cathode copper.
Furthermore, sometimes the end product and production volume determine the ideal process route to leverage.
For copper tubes for instance, if a company plans a production with high annual output, therefore the production process will include vertical continuous caster, hot forming with extrusion, and subsequent drawing.
For smaller production volumes and thin-walled tubes with small diameters, manufacturers can envision the use of a horizontal continuous caster in the process.
Looking at these explanations, the reasons why one should use a dedicated production process for pure copper makes sense but do they have to be the main criteria measurements?
Using additive manufacturing for pure copper
In additive manufacturing, the need to achieve the technical complexity required for some parts tilts the balance towards this manufacturing process.
When asked the main reasons why pure copper raises interest in manufacturing, Jacob Nuechterlein, President & CEO of Elementum 3D replies with a key focus on additive manufacturing:
“Heat exchangers are a primary use in additive manufacturing due to complex designs and internal channeling. Pure copper has one of the highest thermal conductivities of any metal. The extremely high conductivity of over 350 W/mK drives the applications for this material.”
In terms of AM technologies, the most-known technique used to process pure copper is metal AM technology, especially Direct Metal Laser Sintering (DMLS).
However, metal AM technology is not the only technique that can process pure copper
It turns out that some material producers have managed to develop a copper-infused filament, that can be processed on an FDM 3D Printer. One interesting example that can illustrate this point is Filamet™, a Copper Filament that would contain around 90% metal. With a density of 4.3g/cc, the producer, the Virtual Foundry, explained that once fired in a sintering furnace, the printed part becomes 100% metal.
One of the challenges raised by this technique would be the loss of the PLA binder that would lead to a 15-20% shrinkage of the printed component but that’s something that can be overcome before the printing process.
Furthermore, as it is not possible to cast two metals at the same time in a foundry, one of the main advantages of such type of filament would be the ability to 3D printing shapes with more than one metal at a time. Lastly, even though it is not pure copper, the printed part obtained with this material achieves the same electrical conductivity as pure copper.
Pure copper processed by a metal additive manufacturing process
As seen with FDM 3D Printing, the manufacturing process raises its share of problems. In metal additive manufacturing, there are still some challenges but at a different level. There are mainly reflectivity and high thermal conductivity.
We will look at the use of pure copper processed by DMLS. As a reminder, DMLS requires the use of a high power-density laser to melt and fuse metallic powders together. The manufacturing process produces stronger and denser parts than investment casted metal parts while enabling complex geometries that are not always possible to achieve with other metal manufacturing methods.
Despite its great advantages, it should be noted that the process requires tools similar to those that are leveraged for a sandblasting system. Also, health safety conditions should be taken into account before leveraging DMLS-based systems.
Based on their expertise, Farsoon has observed two main challenges regarding the use of pure copper in DMLS:
“Pure copper has a high laser reflectance rate of over 90% with standard Metal Laser Sintering (MLS) systems. It is difficult for the laser to continuously and regularly melt pure copper powder, which leads to issues such as interface failure and internal holes.
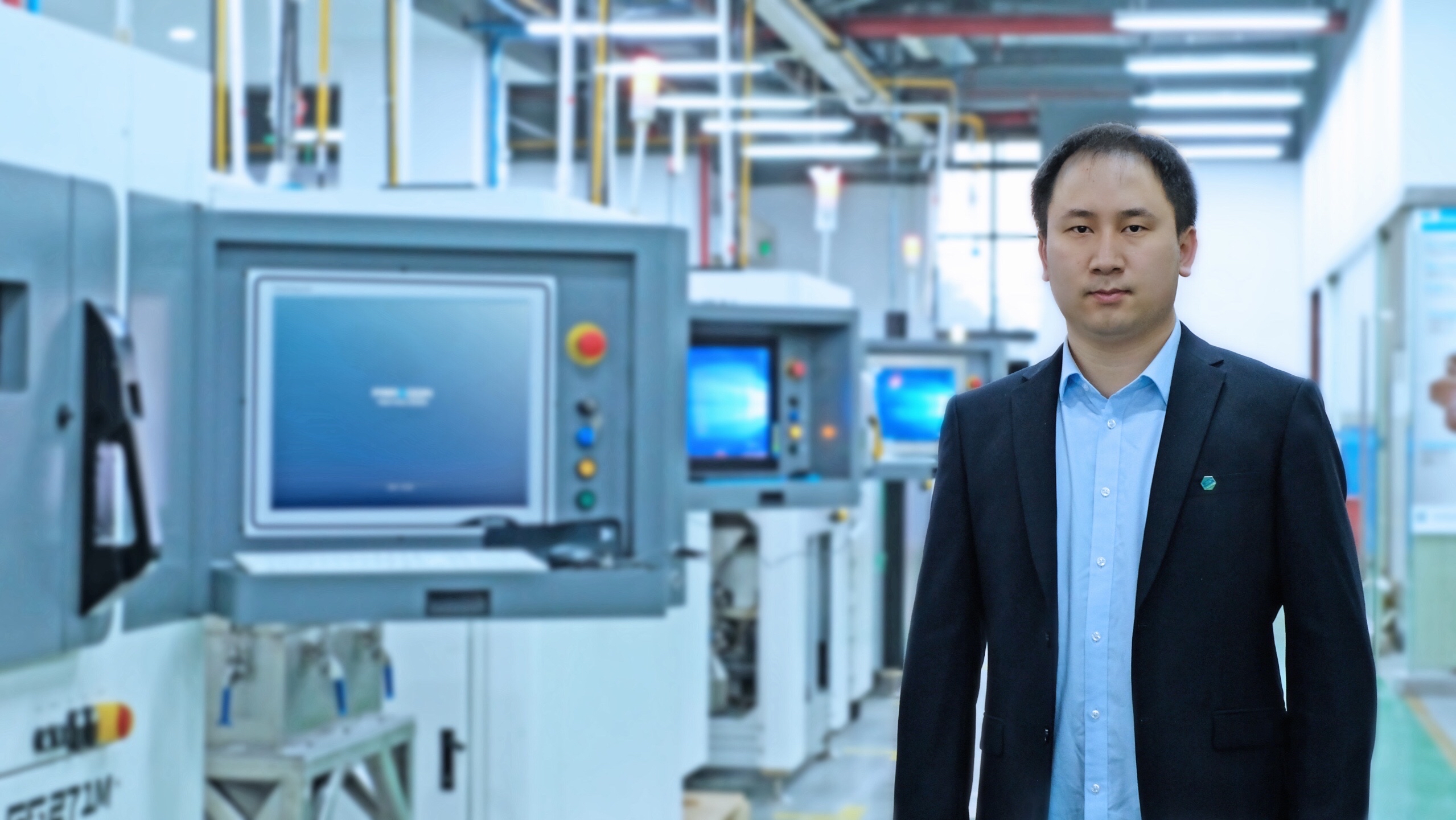
Due to the nature of copper material, pure copper power tends to oxidize in open air, this includes the formation of an oxidized layer of material that prevents further corrosion, but will hinders key properties sought after with pure copper such as electrical conductivity”, explained Wenyu Guo, Metal Product Line Manager at Farsoon Technologies.
he truth is, pure copper is an interesting choice for end users, given the fact that it is more electrically and thermally conductive than copper alloys. However, due to the obtained surface properties, the material can reflect most of the laser radiation in “traditionally” used wavelengths of 1 micron.
According to a research from the Fraunhofer Institute for Laser Technology (ILT) in Aachen, Germany, the material can only receive a small portion of the laser energy – which is also leveraged for the melting process. Therefore, the reflected radiation can destroy the components of the AM system, not to mention that the receptivity of the material for the infrared light increases as the material transition from a solid to liquid plate. In a nutshell, a complicated situation that leads to unstable remelting process.
Addressing the reflectivity issue
In its open platform system, Farsoon has integrated build parameters, scanning and processing parameters that can reduce this reflectivity issue and achieve the desired performance of the application.
The solution has been developed based on a standard fiber laser. According to Wenyu Guo, their solution is cost-effective as to process pure copper, the user will not invest in further key optical systems and will be able to expand the capacity of AM applications.
“Copper’s thermal stress during printing is less than of other materials. Adjusting parameters of heat treatment process such as temperature, holding time and atmosphere/vacuum conditions can affect the micro structure and give preferred properties including strength and conductivity. The composition of raw material, such as oxygen content and purity of copper, also have a big influence on the conductivity behavior.
During the laser melting process of pure copper, the machine build plate is set to a higher temperature which helps relieving the thermal residual stress. The finished pure copper part will require certain level of processing state according to the application to further releasing the stress and solidify the mechanical/electric performances. Under current development, the build copper parts can achieve a density of over 97%”, explains Farsoon’s spokesperson.
Another one that addresses this high-reflectance issue is Optomec. The metal AM and electronics 3D printed specialist has developed a pure copper additive manufacturing (AM) process using its LENS directed energy deposition (DED) systems.
‘Pure copper is a big challenge for DED systems because of its high reflectance.’ said Tom Cobbs, product manager for Optomec LENS systems. ‘The infrared wavelengths on most standard, laser-based AM systems are not readily absorbed by copper, making it difficult to establish a melt pool as the laser energy is reflected back into the source, causing all kinds of havoc.’
According to the product manager, the American company’s new process protects against this high-reflectance issue. Therefore, the laser can operate at full power on reflective surfaces and includes process parameters to account for thermal conductivity differences and large changes in absorption.
What about high thermal conductivity?
Optomec and Farsoon’s solutions might be interesting to explore. The only thing is that, they seem to only lay emphasis on one part of the challenge: reflectivity.
“Copper is more difficult to process due to high thermal conductivity of the fused part and high natural reflectivity of copper. Many claims suggest better productivity with green lasers, but that only addresses reflectivity and not the bigger problem of high thermal conductivity”, explains the materials producer Elementum 3D.
Indeed, Nuechterlein, strongly believes that reflectivity can be solved by many techniques, but the high thermal conductivity makes this material difficult for most users.
On their side, they have developed a pure copper that is for now, only printable on the AM systems of a manufacturer that develops laser powder bed fusion technology. Moreover, the company declares that their product is designed to be used with off-the-self printers using red or green lasers.
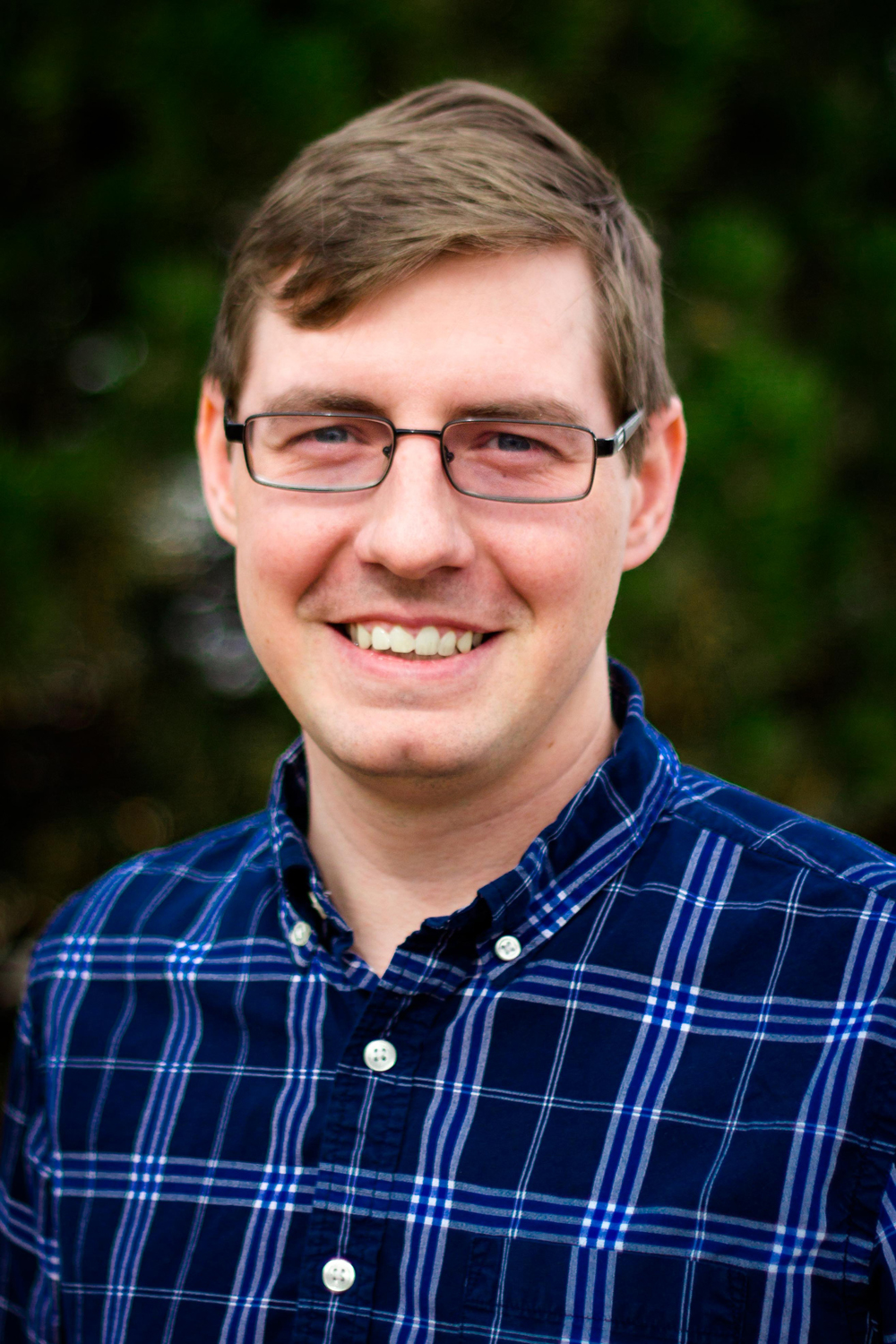
Possible applications with pure copper
Pure copper 3D printed parts are proven to be suitable for heat exchangers in a variety of industrial applications. Induction welders and electronic components are also other examples that can be mentioned.
“The goal of these applications is to achieve production numbers in thousands, or building up second/advanced tier of manufacturing-supply chain”, explains Wenyu Guo.
Over time, we could envision a broader range of applications. In the area of jewelry design for instance, if the manufacturing process enables a more reproducible process that can fabricate complex geometries, therefore, the use of pure copper in additive manufacturing would enable to produce better products.
Concluding thoughts
There are not many companies that can fabricate pure copper-based products using additive manufacturing. This dossier shows that the manufacturing of pure copper 3D printed parts is still nascent and raises challenges that are not always addressed in their entirety but the first solutions that are undertaken, already enable to achieve viable production. High-volume production is definitely the next point on the list.
This dossier was initially published in the March/April issue of 3D ADEPT Mag.