While metal additive manufacturing has incredible capabilities, a few notable restrictions ultimately inhibit its progress: part resolution, minimum wall thickness, and surface quality, naming a few. Some advanced technologies seek to resolve these issues, including pulsed electrochemical machining (PECM). As a postprocessing technique, PECM can produce thinner-walled features, greatly improved surface quality, and higher-tolerance machining of complex geometries. PECM is inherently designed to produce all these results for higher-volume applications.
How Does PECM Work?
PECM is an advanced material removal process utilizing electrochemistry, as opposed to heat or friction, to dissolve a metal workpiece to the desired shape. By running a charged electrolytic fluid in a microscopic gap between the tool (cathode) and workpiece (anode), the pulsed current removes the workpiece material microscopically, and the size of this inter-electrode gap is correlated with the intensity and precision of the material removal rate.
There are two reasons for charging the electrolytic fluid. First, the fluid acts as the conduit for the electrochemical reaction ultimately machining the part. Secondly, this fluid also acts as a flushing agent eliminating any residual heat and flushes out waste products, leaving no possibilities for heat malformation or a recast layer; PECM simultaneously machines and finishes with a burr-free surface.
As a result, PECM is a non-contact, non-thermal process. There is no tool wear, meaning the tool can potentially machine thousands of parts without affecting the accuracy and repeatability of the process, making the process ideal for higher part volumes.
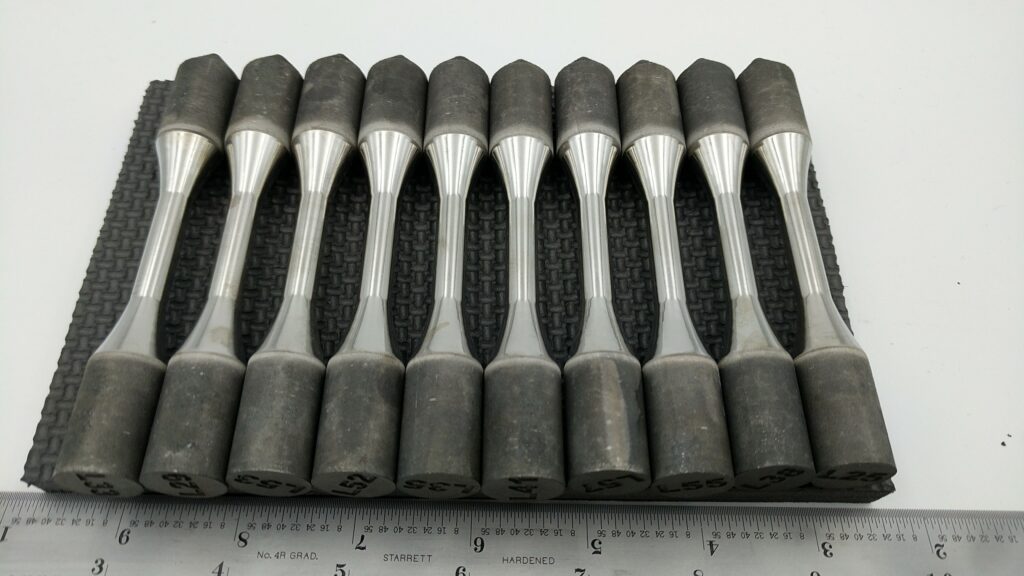
PECM as a Secondary Machining Process
For many applications, AM’s capabilities are sufficient. Most metal 3D printers can produce wall thicknesses down to .3-.5mm (.012-.02in), and for many applications, pristine surface quality is not required for the part to function. However, AM alone is not always effective in producing critical components with difficult tolerances and tougher surface quality requirements. With PECM as a postprocessing operation, manufacturers can produce high-resolution geometry: improved surface quality on downskin features and minimum wall thicknesses reduced to <100µm.
Consider how PECM was utilized as a secondary machining process for a nickel alloy turbine blade. PECM allowed more precise features via thinner trailing edges on the blades, and the part’s performance was noticeably improved, alongside improved surface quality. PECM can replicate these features across hundreds or even thousands of parts (down to <10µm repeatability). Since PECM has higher initial development costs than competing technologies, it is not ideal for low-volume or rapid prototyping. Rather, PECM is ideal for metal AM applications transitioning into higher-volume production. For many AM manufacturers, the transition into high volumes comes at the price of lower resolution, feature size and surface quality by utilizing larger powders, thicker layer lines and more vigorous re-coating methods all aimed at cost reduction. However, combining these higher-volume, lower-resolution additive processes with PECM can greatly improve part performance and cost efficiency.
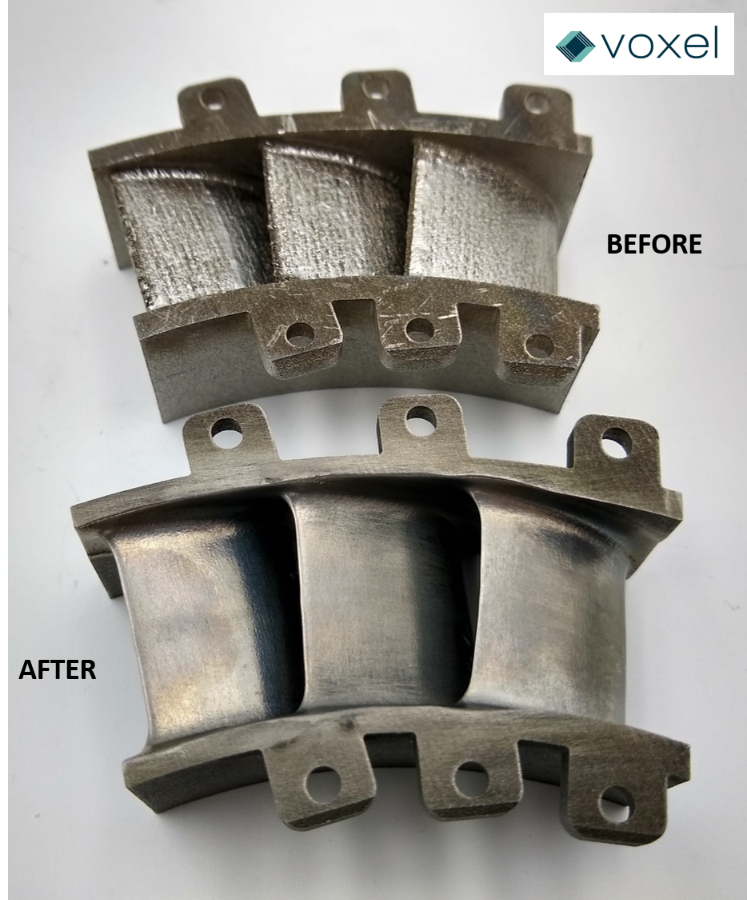
PECM as a Surface Finishing Process
For some critical components, there are obstacles inherent to the AM process that can cause failures from unnecessary friction, fatigue, or corrosion. Powder particle size, support structure remnants, and layer lines can all negatively affect the surface quality of a component. PECM, however, can improve the surface quality of AM parts from 5 – 10 µm (196 – 393 µin) Ra down to 0.1 µm (3.9 µin) Ra, all without affecting the tooling, allowing repeatability. PECM is also generally quicker than competing finishing processes.
A good example can be found in the orthopedic device industry. Femoral stems are a part of a hip replacement attaching a synthetic ball joint to a patient’s hip. These devices are awkward to manufacture, as different aspects of a part require varying levels of surface quality. For example, the ball joint requires an ultrasmooth surface to reduce joint friction and wear on the bearing surfaces. Conversely, other aspects should possess surface qualities promoting “osseointegration”, a porous surface that assists fusion with the surrounding bone. By integrating PECM as a secondary finishing operation, orthopedic device manufacturers could allow PECM to selectively finish a given part—avoiding the porous surfaces on the stem, and superfinishing the ball joint.
Kirk Gino Abolafia is the technical marketing manager of Voxel Innovations in Raleigh, North Carolina, United States. For additional content on electrochemical machining, see Voxel’s education portal.
Remember, you can post free of charge job opportunities in the AM Industry on 3D ADEPT Media or look for a job via our job board. Make sure to follow us on our social networks and subscribe to our weekly newsletter : Facebook, Twitter, LinkedIn & Instagram ! If you want to be featured in the next issue of our digital magazine or if you hear a story that needs to be heard, make sure to send it to contact@3dadept.com