Un regard sur les solutions de post-traitement de GF Machining et les applications médicales
Le grand monde de la fabrication exige en permanence des entreprises qu’elles adoptent de nouvelles façons de penser, de nouveaux processus et de nouvelles machines. Fort de plusieurs siècles d’expérience dans le secteur manufacturier, Georg Fischer (alias GF) a consacré son activité principale à relever les défis de cet univers. Par le biais de ses trois divisions GF Piping Systems, GF Casting Solutions et GF Machining Solutions, la société suisse fournit ses services dans 33 pays, avec 140 entreprises, dont 57 sites de production. Cependant, c’est la division GF Machining Solutions qui attire notre attention aujourd’hui. Forte de son expertise en matière d’EDM (electrical discharge machining = usinage par électroérosion), de machines de texturation laser, de fraisage et d’unité de fabrication avancée, la société fonctionne en mode furtif depuis ses débuts sur le segment de la fabrication additive.
Bien que sa vaste expérience en matière d’usinage ait contribué à renforcer sa présence dans le domaine de la fabrication additive, comme d’autres sociétés du même milieu, GF Machining Solutions a également compté sur des collaborations avec d’autres sociétés de FA, la plus importante étant celle avec 3D Systems.
Dans cette quête permanente de répondre aux besoins uniques des entreprises qui se battent pour adopter la FA dans leur environnement de production, l’unité de fabrication avancée procède en permanence à des ajustements et à des améliorations des environnements matériels et logiciels ; des améliorations en bref qui simplifieront la voie vers un flux de production continu et efficace.
Ces ajustements nécessitent également de se concentrer sur « les produits d’automatisation que sont l’outillage et la robotique – ainsi que la transformation numérique qui est tout à fait transversale à toutes les technologies », a déclaré Romain Dubreuil, responsable des technologies additives, à 3D ADEPT Media dans une interview.
De plus, bien que l’entreprise en parle généralement dans le cadre de ses « solutions de fabrication intégrées » et rarement comme une solution individuelle, notre conversation avec Dubreuil nous éclaire sur le matériel spécifique qui a été développé pour l’étape de post-traitement très demandée.
« Cette étape du processus de fabrication peut se faire soit par dépoudrage, soit par finition des pièces imprimées 3D par des opérations d’usinage.
En ce qui concerne la finition, nous pouvons compléter l’impression de la pièce avec l’une des machines de fabrication conventionnelles de notre gamme. Il peut s’agir d’une fraiseuse standard ou d’une machine d’électroérosion à fil standard. Dans de nombreux cas, elles peuvent convenir à de nombreux opérateurs après l’étape d’impression, en usinant la pièce, il est possible d’améliorer la finition dans un certain domaine par exemple », souligne Dubreuil.
Comme nous le découvrirons plus tard, dans les lignes ci-dessous, la FA offre tellement de possibilités pour les implants et les produits biomédicaux complexes que les pièces imprimées en 3D nécessitent parfois un usinage et une finition supplémentaires. À ce niveau, des dispositifs de fixation de la pièce sont souvent utilisés pour traiter la pièce et faciliter les processus ultérieurs.
« Nous avons également développé une solution spécifique qui peut couvrir les besoins spécifiques de la FA à cet égard », souligne M. Dubreuil.
Baptisée CUT AM 500, cette machine de post-traitement est conçue pour répondre aux besoins spécifiques de la FA et s’appuie sur l’expertise de la société en matière d’usinage par électroérosion. Décrit comme une alternative automatisée à l’EDM standard, le procédé ressemble à une scie à ruban qui sépare les pièces fabriquées de manière additive de la plaque de construction. La CUT AM 500 est un bon complément aux imprimantes 3D métal à fusion laser sur lit de poudre (LPBF).
« Bien qu’elle ait été développée en tenant compte de la LPBF, cela ne signifie pas nécessairement que notre gamme ne peut pas être utilisée pour d’autres technologies de fabrication telles que la fusion par faisceau d’électrons ou simplement des applications métalliques en général », note le responsable des technologies additives.
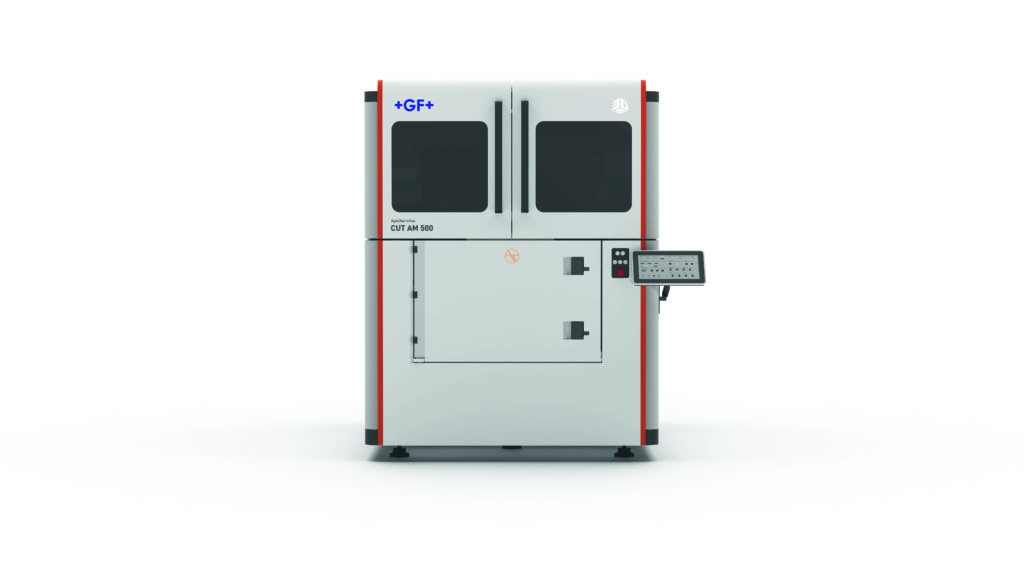
D’une taille de 510 x 510 x 510 mm, le système permet de retirer proprement et sans effort de coupe des produits sur des plaques de grande taille dont le poids peut atteindre 500 kg. Selon le fabricant, le procédé garantirait l’intégrité des pièces grâce à la table basculante, au procédé d’électroérosion à fil horizontal et aux paniers personnalisables. De plus, contrairement aux autres systèmes de post-traitement, celui-ci permet l’intégration d’un système de serrage pour faciliter le serrage et le référencement ainsi que la préparation à l’automatisation.
Choix de fabrication
Passer de l’idée à la conception de l’impression 3D nécessite à la fois de l’expérience et les technologies appropriées. Bien que nous ne nous concentrions ici que sur le post-traitement, rappelons que le processus idéal d’AM inclut l’écosystème entier, des processus de contrôle de la qualité de la poudre entrante aux logiciels, au post-traitement et aux contrôles des processus sur les produits finis. Nous ne le soulignerons jamais assez, mais chacun de ces éléments est crucial pour une production réussie dans des secteurs très réglementés.
« En général, nous nous concentrons davantage sur les applications de production. Nous sommes très actifs dans différents segments : les moules et matrices, l’énergie et l’aérospatiale, bref, les industries où la FA peut apporter des avantages pour augmenter les performances et le poids, et améliorer la précision des pièces. Cela étant dit, nous nous concentrons également sur l’industrie médicale. L’une des principales applications dans ce domaine reste les implants rachidiens qui nécessitent des technologies répondant aux exigences de la FA », déclare Dubreuil.
Un bref aperçu de la fabrication d’un implant dentaire.
Comme les applications restent une bonne preuve de concept du fonctionnement de la technologie, le responsable des technologies additives et son collègue Dogan Basic nous donnent quelques détails sur la production d’un implant dentaire ainsi que sur plusieurs tâches de post-traitement qui peuvent être réalisées avant d’obtenir la pièce finie souhaitée.
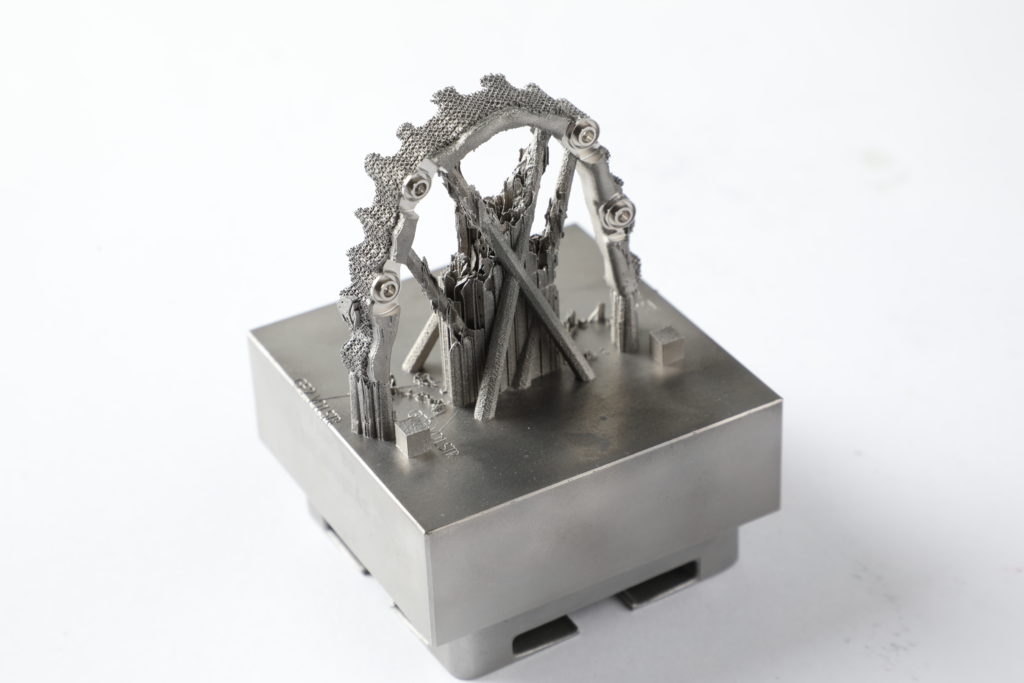
Bien que nous ne sachions pas à quelle fin l’implant a été produit (que ce soit à des fins de recherche ou de commercialisation), l’équipe de fabrication a utilisé la célèbre DMP Flex 350, une imprimante industrielle 3D métal basée sur la fusion sur lit de poudre qui a fait peau neuve la dernière fois que nous l’avons vue à Emo Hannover 2019. Pendant le processus d’impression, le système garantit non seulement un environnement à faible teneur en oxygène mais aussi une très haute densité. Nous savons par le fabricant que la pièce a été produite en utilisant le matériau LaserForm® CoCrF7 et a été imprimée avec une épaisseur de couche de 30um.
Cependant, ce qui nous intéresse le plus, c’est à la fois la précision en termes de temps de fabrication et d’opérations de post-traitement.
« Il faut 34 minutes pour imprimer une pièce, mais il est évident que vous imprimerez plusieurs pièces en même temps. (9 heures pour imprimer 20 pièces). Nous les imprimons sur nos petites plaques System 3R afin de faciliter les opérations de post-traitement. Il faut environ 23 minutes pour fraiser chaque pièce et seulement quelques-unes pour les séparer avec la CUT AM 500 », explique Dogan Basic de GF Machining.
Comme mentionné précédemment, les implants complexes nécessitent parfois un usinage supplémentaire. Pour résoudre ce problème, les opérateurs peuvent utiliser cet équipement appelé « System 3R » disponible dans une gamme de tailles de palettes. À l’aide d’un tour conventionnel, ils peuvent couper chaque palette directement de la pile, ce qui permet d’utiliser les BuildPals séparés pour d’autres travaux de fabrication additive pendant que le post-traitement se poursuit.
Dans ce cas précis, Dogan explique qu’avant l’opération de fraisage, la pièce passe traditionnellement par une opération de traitement thermique et ensuite, par une opération de fraisage 5 axes pour s’assurer que les « raccords » sont fraisés pour les vis.
Par la suite, « vous aurez éventuellement une finition manuelle pour enlever les éventuels supports résiduels et une opération de nettoyage ».
Ce n’est qu’après ces tâches que l’implant peut être facilement fixé dans la mâchoire.
Réflexions finales
La fabrication additive est certainement l’une des industries où il y aura toujours quelque chose de nouveau à apprendre et la perspective de GF Machining dans ce segment de post-traitement montre qu’il n’y a pas de « solution plug-and-play ». C’est pourquoi se lancer dans la FA est une chose, et prendre les bonnes mesures pour intégrer toute sa chaîne de processus en est une autre, mais si cela est bien fait, les récompenses que l’on peut obtenir ne peuvent être qu’avantageux.
Ce dossier a été initialement publié dans le numéro de Janvier/Février 2021 de 3D ADEPT Mag.