If you work in the engineering field, you are probably already familiar with 3D scanning, this process that consists in capturing a physical subject to represent its geometry in a digital environment. The 3D scan data captured can serve for visualization, analysis, or Additive Manufacturing. The question is, what are the essentials one should keep in mind when using 3D scanning in an Additive Manufacturing production process?
Most of the time, beginners in AM (usually or unconsciously) go through a well-known route for the manufacture of parts: design, manufacture and post-processing. The more you acquaint yourself with the technology, the more you realize that specific stages of the manufacturing process may require the use of 3D scanning.
One of the first applications that justifies the use of 3D scanning in Additive Manufacturing is reverse engineering. In such cases, a 3D scanner helps to create drawings of parts that are not originally available.
Another reason why it makes sense to use 3D scanning in AM is quality control. Simplifying this process is important to maintain consistency and repeatability in manufacturing operations. “Additive Manufacturing like other manufacturing processes can present many challenges in dimensional conformity. For example, the stress created in a printed part when it cools down can generate deformation that could cause quality issues. Having a better understanding of those deformations is extremely useful to correct and compensate for them. It is clear to me that 3D scanning and 3D printing are two technologies that benefit from each other,” Creaform’s Product Manager, Simon Côté explains.
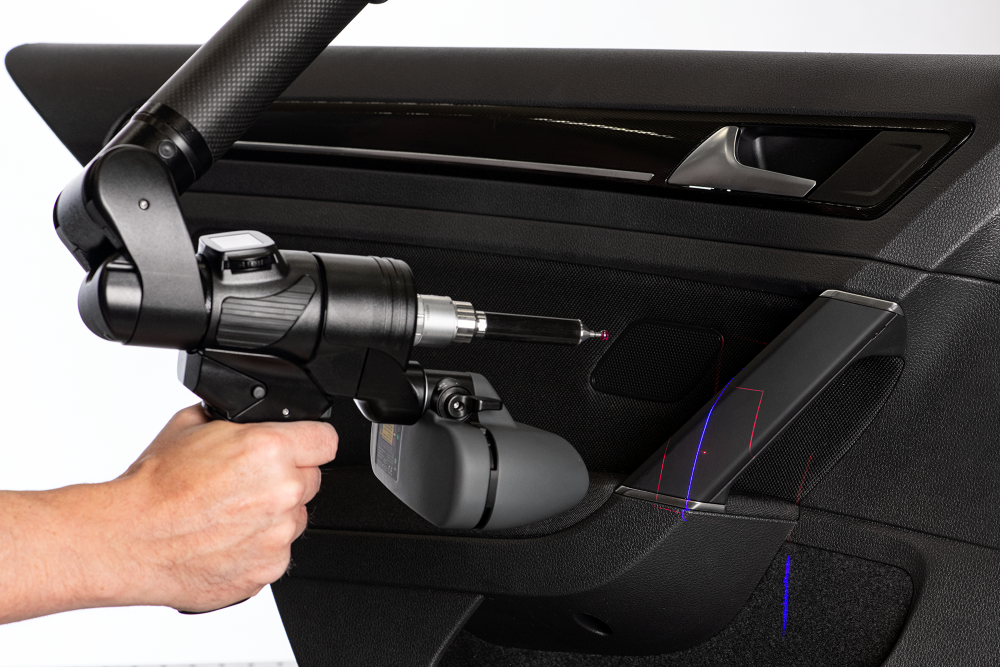
That being said, it’s important to keep in mind that achieving precise quality control requires standardized methods to assess functionality, reliability, safety, and other factors. Establishing these standards for additive manufacturing is inherently challenging due to the significant variation in manufacturing processes across different AM technologies. Issues such as support structure and build plate removal, heat flux, trapped powder or resin, and post-processing add other complexities.
On another note, measuring parts with complex shapes can be challenging and time-consuming with traditional tactile inspection methods. “Due to their optical and non-contact nature, 3D scanning devices are ideal for measuring these complex surfaces,” Kristof Peeters, Product Manager at Nikon said. Measuring overstock on 3D printed parts, intermediate inspection during the printing process and final inspection of 3D printed parts are other applications where it makes sense to consider using 3D scanning. Peeters provides further clarification about each of these items:
“a. Measuring overstock on 3D printed parts: when printing high-accuracy parts, the 3D printing step is typically followed by machining to remove overstock on the “rough” 3D printed part and machine it to its final specification. Using a laser scanner to capture the precise freeform surface of the rough 3D printed part allows generating exact machining paths to finalize the part. This combination of additive manufacturing and subtractive manufacturing (also called hybrid machining) with intermediate measurements using a laser scanner in between these 2 steps, is not only applied for new parts but also for repairing broken parts. In this case the damaged part is first roughly repaired by adding material through 3D printing in the worn or damaged area. This repaired area is then laser scanned, which gives the exact information needed to machine the part back to its original condition.
- Intermediate inspection during the printing process: especially for parts that take a very long time to print or are highly expensive, it is beneficial to check the dimensional quality of the part regularly during the printing process, i.e. while the part is still on the 3D printer. If deviations are detected, appropriate measures can be taken (e.g. adjusting printing parameters, scrapping the part, …) to avoid wasting time and effort on a part that wouldn’t pass final quality control. This application is specific to 3D printing technologies such as Direct Energy Deposition (DED) or Wire Arc Additive Manufacturing (WAAM), where the part remains accessible during the printing process, unlike powder bed printing technologies, where the printed part is covered in powder.
- Final inspection of AM parts: the previous 2 applications focus on inspection of the 3D printed part during the manufacturing process and are therefore typically performed on or close to the 3D printing machine. There is of course also the final inspection of the AM part after all the machining is finished. 3D laser scanners are ideal for digitizing the often very complex outer shape of an AM part quickly and in great detail. This digital copy can then be compared to the CAD model to create an easy-to-interpret color map, providing an overview of the part’s dimensional quality.
For the final inspection of both the outer shape as well as the inner shape of the part, 3D CT scanning is a great solution: with its ability to “look through parts”, CT scanning is a technology that allows not only to inspect the outer dimensions of the part but also detect internal defects, which is critical given that AM parts are often functional parts.”
The different types of 3D scanning hardware
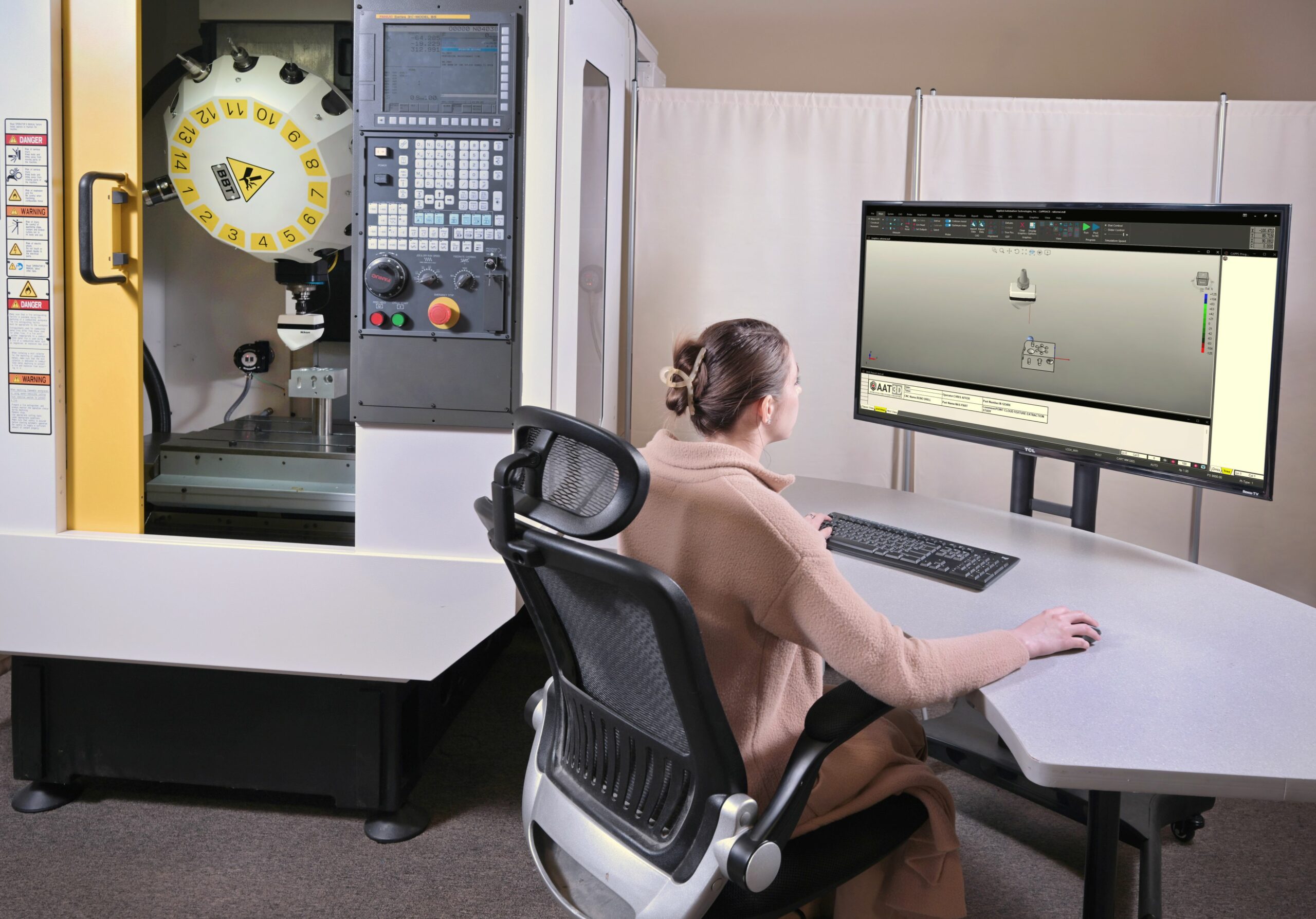
The more 3D scanning hardware is being developed, the more complex it becomes to assess their pros and cons in specific use cases. However, among the most widely used 3D scanning techniques, one can identify laser triangulation, fringe projection, structured light 3D scanners, photogrammetry, and contact-based methods. Other specialized scanners rely on X-rays, sonars or other sensing methods for niche applications.
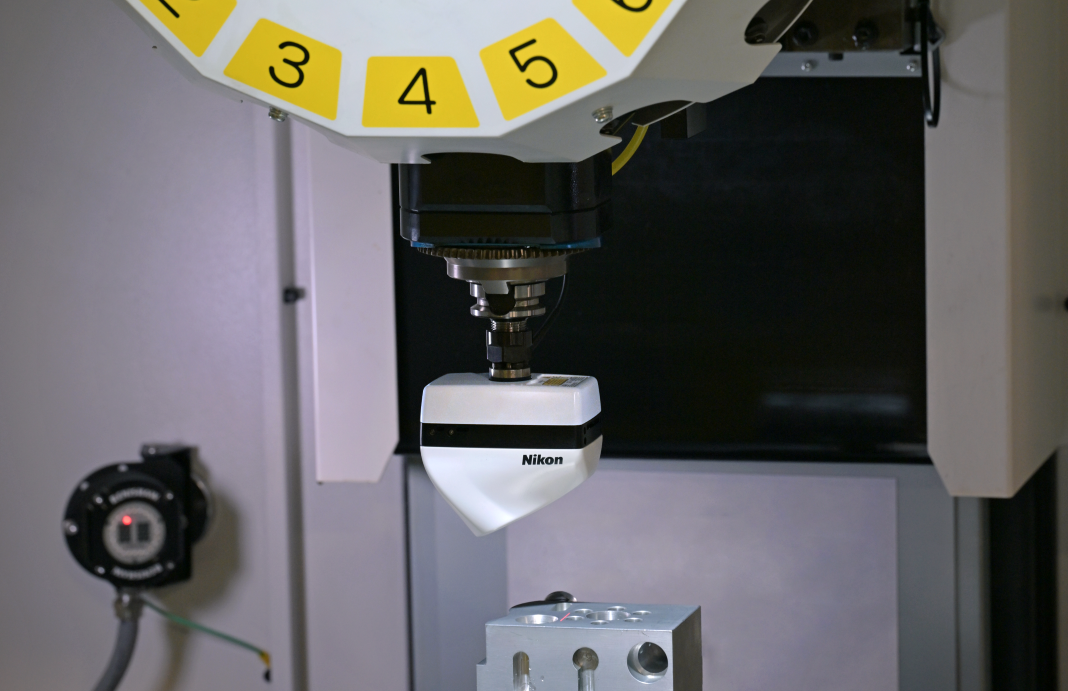
Speaking of laser 3D scanners and structured light 3D scanners, Creaform’s Côté explains:
“Laser 3D scanners use laser beams to capture the precise dimensions and shapes of objects, making them highly accurate and effective for detailed work. Structured light 3D scanners, on the other hand, project a pattern of light onto an object and measure the deformation of the pattern to create a 3D model. While structured light 3D scanners offer a balance of speed and precision, they may not always match the high level of detail and accuracy required for many manufacturing applications.”
Nikon’s product manager completes:
“Laser triangulation scanners use a laser line that is moved across the part. A camera records the shape of the laser line to dynamically digitize the part. At Nikon, we offer laser triangulation scanners known for their exceptional performance in measuring “difficult” materials, such as very shiny or dark surfaces, without requiring the operator to change scanner parameters or prepare the surface. Additionally, Nikon optics in these laser scanners ensure the highest accuracy data.
Fringe projection scanners project a rectangular pattern of stripes onto the part. One or more cameras record the deformation of the pattern caused by the object’s surface geometry and can as such create a digital copy.
3D Scanners can also be categorized by their type of operation into handheld devices and automated devices.
- Handheld 3D scanners: These devices require an operator to “move” the laser scanner over the part to perform a measurement. The main benefit is that these devices are very quick and easy to deploy. They are fully mobile, so can be used anywhere.
- Automated 3D scanners: These devices are typically mounted onto a Coordinate Measurement Machine (CMM), but more recently also onto CNC machines or Additive Manufacturing machines. They can be programmed to automatically perform the laser scanning measurement. The obvious benefit is that they don’t require an operator to be present during the measurement, making them ideal for automated setups that run continuously and autonomously. Furthermore, automated systems tend to be more accurate than their handheld counterparts because they operate in a more controlled environment.”
Considerations and limitations to keep in mind before investing in a 3D scanning technology
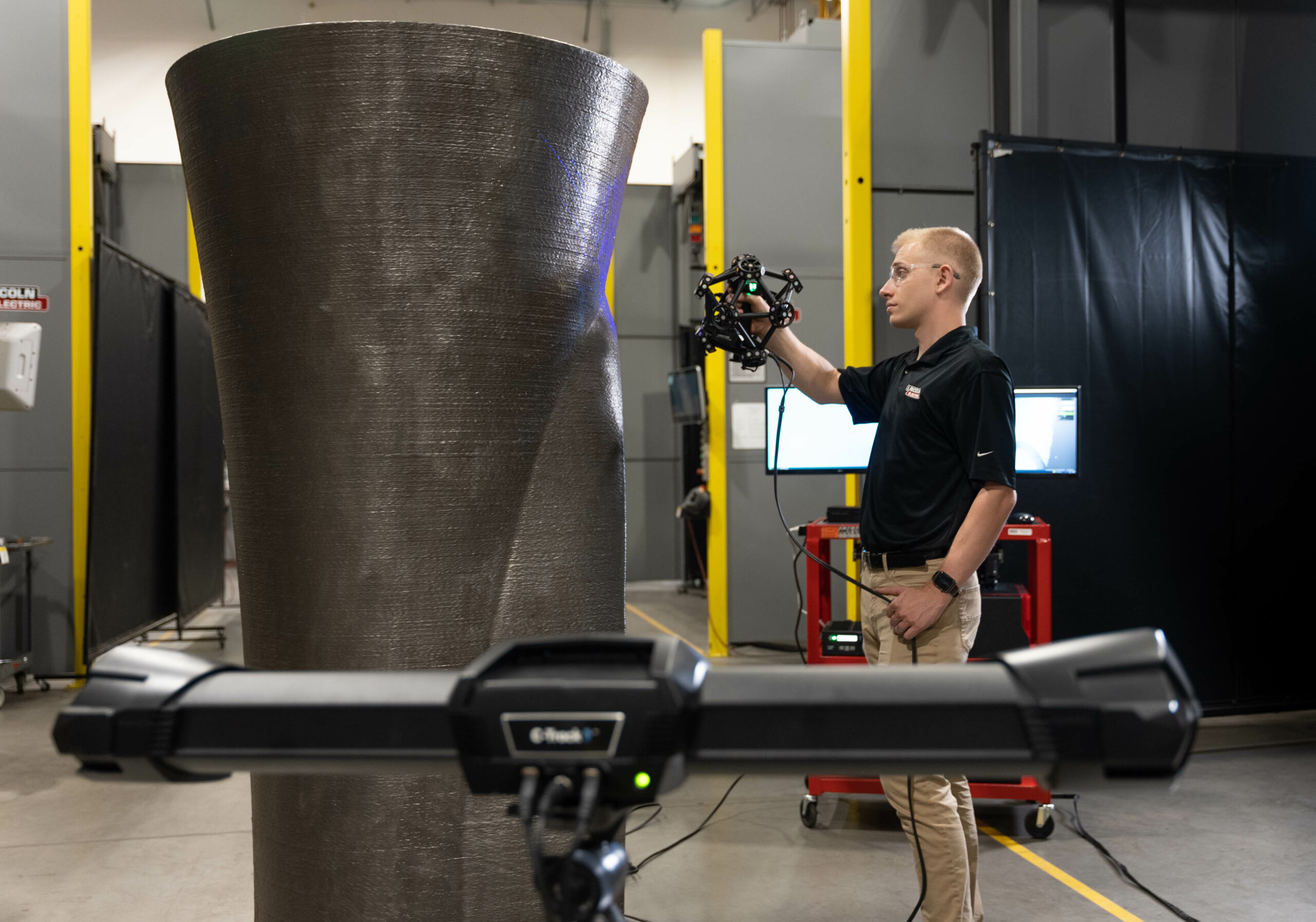
As you may guess, it’s one thing to know the different types of 3D scanning, it’s another one to know in which solution to invest for your AM applications. Obviously, budget, 3D scanning details, subject type and size are some of the important factors to consider before buying, but depending on one’s situation, some factors simply overshadow others.
For Peeters, “the decision on whether the inspection of the part with a laser scanner is to be performed by an operator or needs to be performed fully autonomously is an additional important factor for the selection of a 3D scanner.”
For Côté, “the accuracy is also a fundamental characteristic. Simply using a scanner that delivers a good level of detail does not guarantee the accuracy of the scan data. The accuracy is definitely crucial for inspection application, but also for integrating physical objects to a new product design. Another important factor to consider is the user-friendliness of the software and the availability of local support from different vendors, which can significantly impact your overall experience and satisfaction.”
3D scanners are becoming more and more accessible because of the growing use of smartphone apps that can use cameras or LiDAR sensors to act as a 3D scanner or simply competition on the market.
However, just like any technology, 3D scanning techniques still require some areas for improvement. If for Creaform’s expert, translucid material is still a big challenge for most 3D scanners, Nikon’s expert lays emphasis on the need to adapt laser scanners so that they can withstand harsh conditions and can be used effectively inside or near the AM machine. Key areas for improvement include enhancing the scanner’s resistance to the harsh AM environment and simplifying its integration into AM machines, he said.
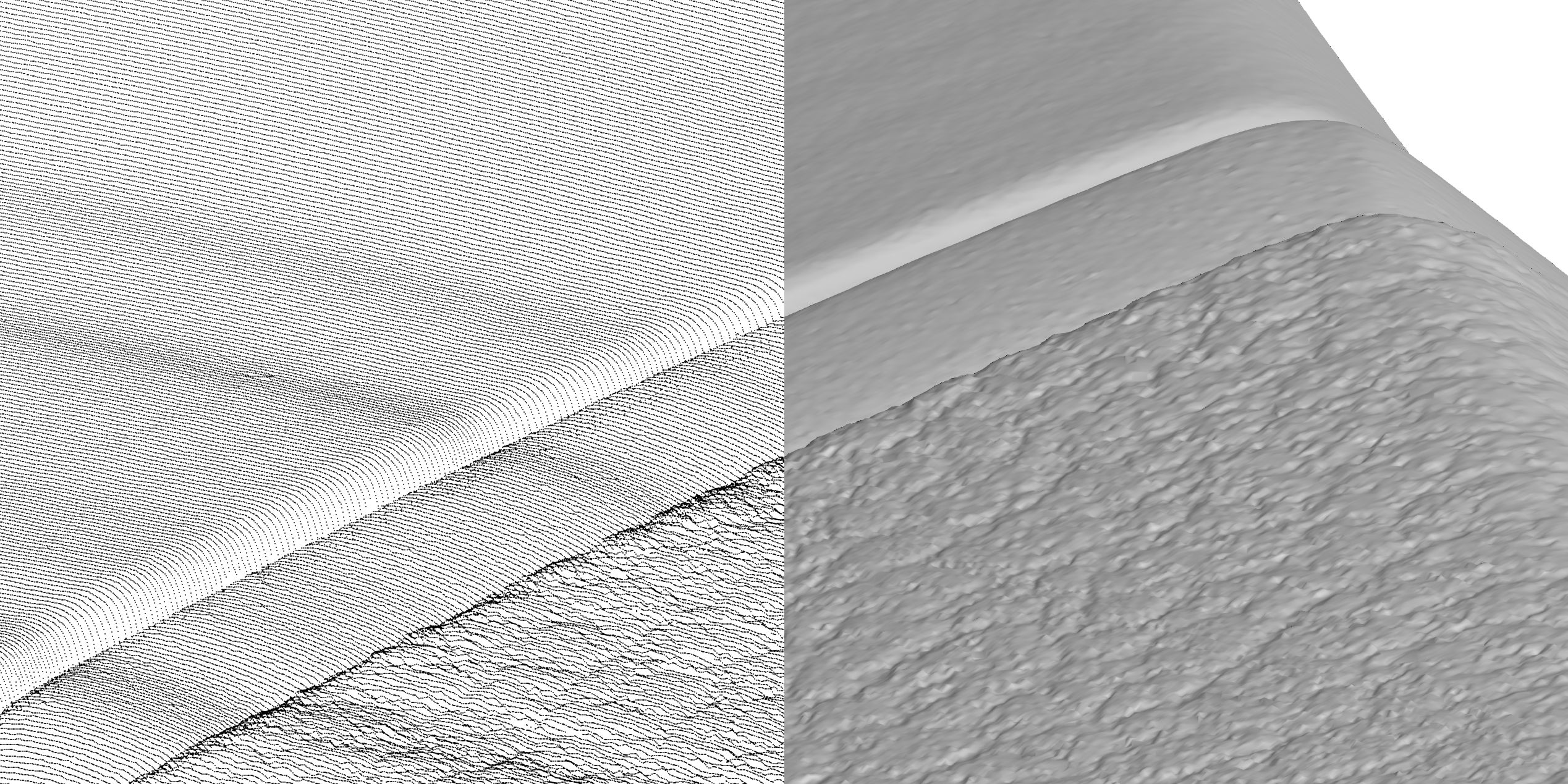
Editor’s notes
To discuss this topic, we invited two companies that specialize in the development and commercialization of 3D scanning solutions.
Creaform: Founded in 2002, experts from this Canadian company have seen significant improvement in the 3D scanning market during the past ten years. Over time, 3D scanning solutions are getting better and better at capturing virtually any physical object in a matter of minutes, enabling digital twin analyses and improvement across different manufacturing processes. The company provides a range of portable and easy-to-use 3D scanning solutions that cater to various needs and budgets. Its product lineup includes everything from affordable entry-level scanners to high-end, metrology-grade 3D scanners that provide the highest level of accuracy and precision. In addition to its portable options, it also provides automated 3D scanning solutions designed to enhance efficiency and consistency in large-scale manufacturing and quality control processes. For those involved in Additive Manufacturing, its scanners are equipped to handle the complexities of 3D printing, ensuring precise measurement and quality control throughout the additive manufacturing workflow.
Nikon: First known as an optics and photographic equipment manufacturer, Nikon has over the years diversified into new areas like 3D printing and regenerative medicine to compensate for the shrinking digital camera market. In the AM industry, it offers a comprehensive portfolio of laser triangulation scanners in both handheld and automated versions. The automated laser scanners, including the LC15Dx model for high-accuracy applications and the L100 model for high-productivity applications, can be integrated directly onto an AM machine. These scanners are ideal for fully automated production and inspection processes. In its latest development, they have introduced wireless data communication technology for these automated laser scanners, facilitating easier integration into manufacturing machines. Further enhancements to enable their usage in a CNC and AM production environment are on the way.
Additionally, they provide a handheld laser scanning solution featuring the company’s H120 laser scanner combined with the MCAx S articulated arm. This flexible solution allows for quick part inspection in or near the AM machine.
Nikon believes that integrating metrology directly into the manufacturing process is essential for enhancing the quality of produced parts and improving cost efficiency. As an active player in the AM market now, the company focuses on the synergy between 3D laser scanning and AM. Consequently, it is actively investing in 3D scanning solutions tailored for AM.