In the field of ceramic 3D printing, there are still few players. This lack of experts is not necessarily linked to a question of demand on the market, but rather a lack of knowledge of the processes and their benefit in production.
One of the companies we met at formnext 2021 that has decided to stand out in this niche market is Pollen AM. The developer of PAM technology – an acronym for ‘Pellet Additive Manufacturing’ – has recently added technical ceramics to the range of materials that can be processed by its technology.
At formnext, a conversation with Didier Fonta, Managing Director of Pollen AM, explains how the additive manufacturing process with technical ceramics is much simpler with PAM and financially more interesting compared to other ceramic production processes.
As a reminder, PAM allows manufacturers to use raw materials – in granular form. It enables users to have “the most widespread materials, available at the lowest price with the best chemistry. Those materials break all consumption costs in the system as they are the standard for mass production”.
Just as the processing of elastomeric thermoplastics is inspired by MIM for metal 3D printing applications, Pollen AM is here inspired by CIM to develop its range of technical ceramics.
Indeed, CIM allows the design and production of ceramic parts with the design and productivity modes of plastic injection. “The challenge in the manufacture of ceramic parts is porosity. You must obtain a part that is dense enough to have the desired characteristics,” Fonta explains.
So, instead of systematically making a tool for injection, additive manufacturing directly makes a so-called “green” part. The latter is then unbonded – to remove the binder – and the new ‘brown’ part is then sintered in a high-temperature oven to obtain the final part.
According to Pollen AM’s explanations, the manufacturing itself remains relatively fast (about 15mn depending on the size of the part). The sintering on the other hand, is the stage which takes the most time (about 24h) whereas the debinding requires about 4h for 1mm thickness.
In the same vein, the properties of parts made with ceramic 3D printing are equivalent to those of ceramic injection moulding due to the use of the same raw material.
However, Fonta draws attention to the choice of pellets from the outset: unlike FDM processes which may require polishing and colouring as a post-processing step, it is crucial in this process to choose the right pellets from the beginning, as the colour of the final part depends on it.
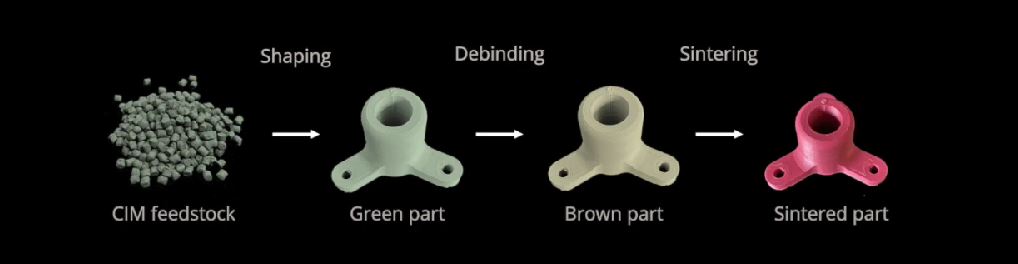
As far as applications are concerned, the production of technical ceramic parts via AM is ideal for small series, prototyping and very complex parts, in all vertical industries that can also leverage metal 3D printing.
Pollen AM has been active in the AM industry for almost 8 years now, and so far, its strategy of focusing on the raw granular material issue to develop more applications seems to be working well.
Remember, you can post free of charge job opportunities in the AM Industry on 3D ADEPT Media or look for a job via our job board. Make sure to follow us on our social networks and subscribe to our weekly newsletter : Facebook, Twitter, LinkedIn & Instagram ! If you want to be featured in the next issue of our digital magazine or if you hear a story that needs to be heard, make sure to send it to contact@3dadept.com