“The company that attracts with magnets is go-to-market focused”
We are so used to talk about Composite 3D printing from a “deposition-based approach” that we tend to forget that as composite materials are available in various forms, their AM technologies can also be liquid-based processes.
The truth is, nobody knew that photopolymer composites could be uniquely positioned to fill the gap in functional material properties observed in composite additive manufacturing; nobody except Fortify.
The company’s journey started in 2016 on the heels of research on composite 3D printing led by Randall Erb and Joshua Martin at Northeastern University. In five years of activity, a lot has happened in the startup’s roadmap. From awards, several fundraising activities to a recent expansion of the production line, Fortify has been quite busy.
With the goal of “bringing high performance materials to market with an application specific focus”, the US-based manufacturer has been developing patented CKM and Fluxprint technologies. These technologies can process highly filled resins that deliver ideal properties for thermally resistant moulds, tools, and fixtures applications.
Joshua Martin, the CEO and cofounder, told us that Fortify has also launched “a low-loss dielectric material targeted towards microwave and electronic devices that mitigates the need for lengthy and expensive manufacturing processes (such as molding or casting followed by machining).”
In this Opinion of the Week, we discussed with Martin the reasons why liquid-based processes such as CKM (Continuous Kinetic Mixing) and Fluxprint technologies could be a stronger and viable alternative for composite 3D printed parts.
The difference with deposition-based approaches
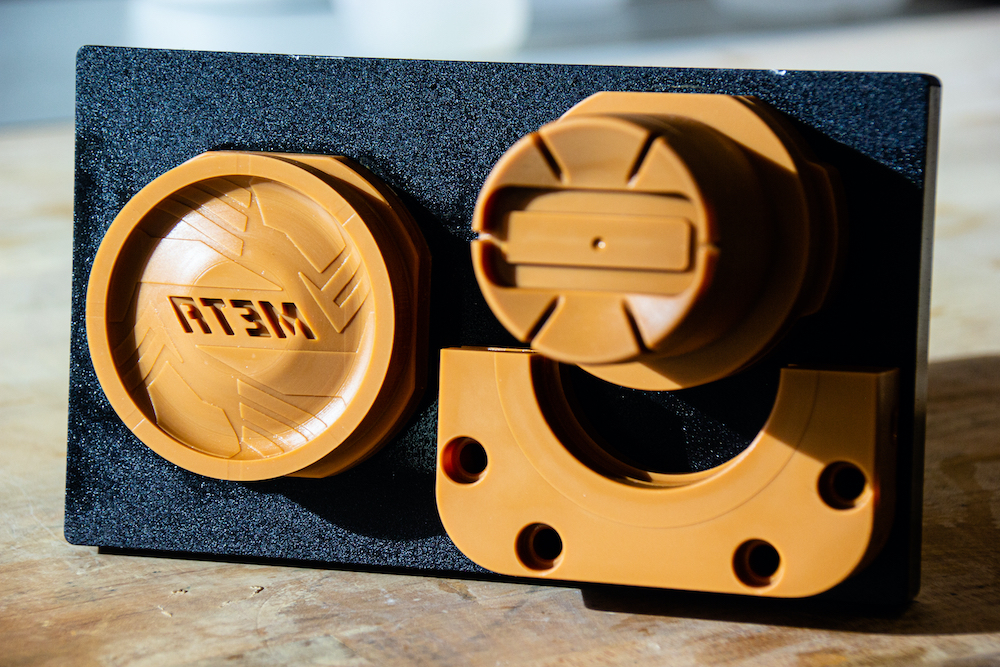
To produce custom microstructures in 3D printed composite components, Fortify’s patented Fluxprint uses magnetic fields and digital light processing (DLP).
In such a process, a layer of feed material is supplied to the plate with reinforcement aligned. Interestingly, while magnetic field is applied to align this reinforcement, active voxels are exposed to UV light, cementing this way the reinforcement orientation in those voxels. As the process evolves, the magnetic field moves to define a new orientation of reinforcement. Following several repeated UV exposure steps, there is an automatic adjustment to bring in uncured feed material matrix for the next print layer, until the part is formed.
If this “voxel-by-voxel printing” is certainly the key feature that enables to achieve high resolution in parts, we should also recognize the fact that the process opens up new possibilities in terms of materials. And these are two advantages that play to the strengths of Fortify.
“Using a short-fiber composite feedstock with a liquid-based process enables Fortify to print the highest-resolution composites on the market. It also enables Fortify to more easily use different types of additives or combinations of materials for tailored performance. The material properties that our thermoset composites enable stand apart from other filament-based processes (which are mostly thermoplastic) because of the chemical crosslinking involved – this leads to greater thermal performance. In addition, our process allows for fiber alignment that is not dictated by shear forces. Deposition based approaches typically can’t align particles in any direction other than the extrusion line. This prevents, for example, alignment in the z-axis, whereas Fortify is able to reinforce parts in the Z”, Martin outlines.
The truth is, for most operators, achieving a distributed reinforcement throughout the matrix of the print is often a Holy Grail. Fortify’s technology can address this issue and can even align the fibers in these parts.
The “CKM (Continuous Kinetic Mixing) process ensures that the composite material is homogenous, while [the] Fluxprint process enables precise fiber alignment and control within each region of a part”, our guest told us.
Thanks to simulation-based techniques that enable to predict the ideal alignment protocol for a given part, the expert in UV-cure of highly-filled technical resins can achieve the desired microstructural control during a production.
The latest additions in the FLUX Series Product Line
The beginning of this month has saw the addition of two new printers and software to the Fortify FLUX Series product lineup.
The new 3D printers, the FLUX CORE and the FLUX 3D complete a portfolio that already includes the FLUX ONE, a 3D printer released last year that adds Fluxprint Z (Z-axis magnetic field) to the baseline CORE 3D printer.
FLUX 3D FLUX CORE FLUX ONE
Ideal for processing viscous particle filled resins where magnetic alignment is not required, the Flux Core enables RF devices and electronic applications.
The FLUX 3D on the other hand, integrates Fluxprint 3D (3-axis magnetic field) to the baseline CORE 3D printer, and enables enhanced control to align fiber in any axis throughout objects as they are printed. Heat sinks, heat exchangers, and high-performance industrial connectors are some examples of applications where the technology can be used.
Speaking of the difference between the two 3D printers, Martin states: “The Flux Core is targeted towards users who are looking to print with one of our heavily filled resins, or are looking to develop their own fiber-filled photopolymer using our Flux Developer software. Our platform is the ideal industrial grade machine for developing photopolymer composites, which might for example be used in ceramic applications. The Flux 3D is an enhanced version of our platform that provides users with full 3D control over particle alignment – allowing for complex orientations within each layer that lead to unique thermomechanical and electrical performance. The Flux One that we announced last fall allows users to benefit from Z-axis orientation, which provides 50% improvements in tensile strength when compared to unaligned systems.”
All these 3D printers can now be supported by Flux Developer, a software platform that allow users to control variables such as exposure time and intensity, material flow, resin temperature and viscosity, and even the build plate mechanics, as they develop and add new materials to their production.
As you can see, a lot is happening at Fortify. The company has focused its development on a number of material reinforcements, which have been developed in collaboration with leading material partners. However, all of this remains a lot of “talk” if applications don’t follow.
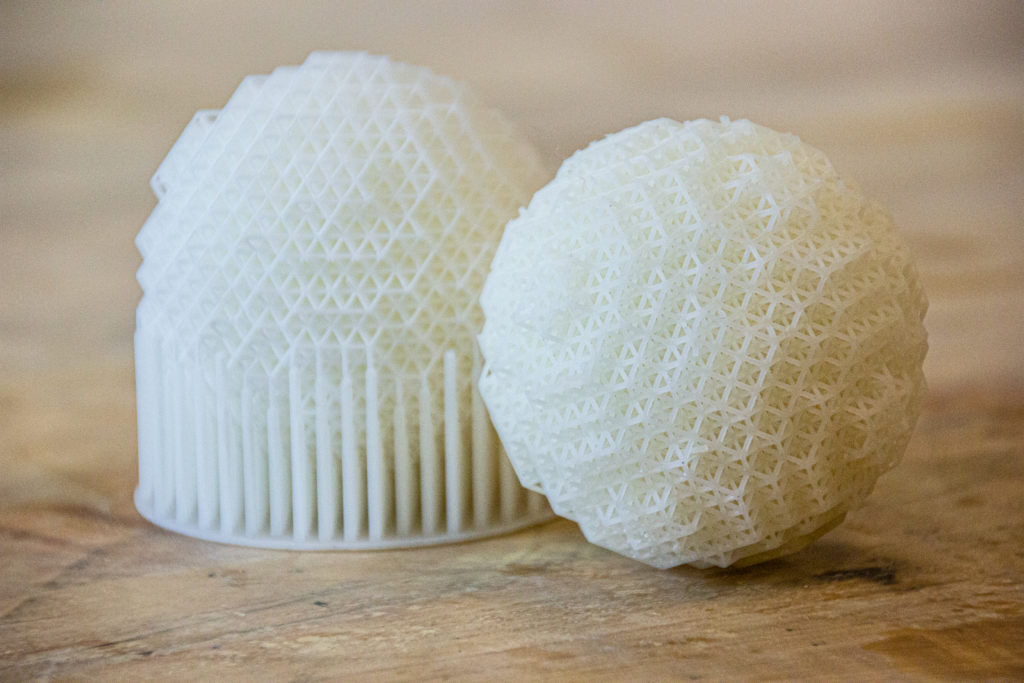
To that, the CEO replies that the company’s more recent material announcement in the low-loss RF space is one in which they are able to replace expensive (both in cost and environmental footprint) conventional materials for RF and microwave devices while providing new degrees of freedom only AM can realize.
“We have a few product announcements underway in the thermal and electronics space that we are excited to share in the near future”, he adds. With the $20M equity round the company recently secured, the team plans to continue redefining advanced manufacturing and to do so, they are “go-to-market focused”.
Remember, you can post job opportunities in the AM Industry on 3D ADEPT Media free of charge or look for a job via our job board. Make sure to follow us on our social networks and subscribe to our weekly newsletter : Facebook, Twitter, LinkedIn & Instagram ! If you want to be featured in the next issue of our digital magazine or if you hear a story that needs to be heard, make sure you send it to contact@3dadept.com