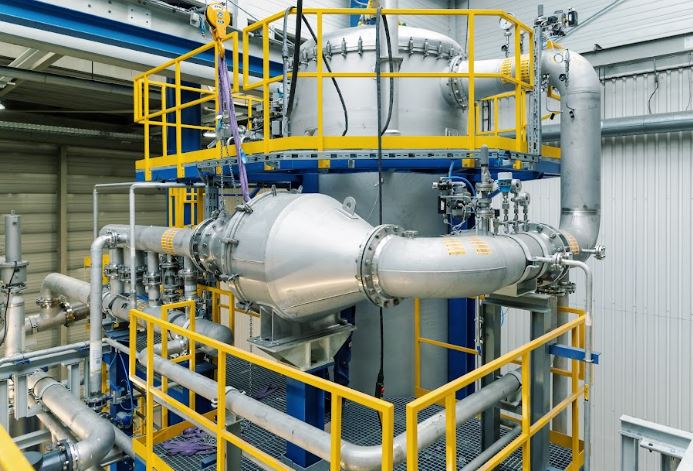
There are a number of reasons why one can select stainless steel for additive manufacturing (AM) processes, including its superior corrosion, mechanical properties compared with other steel types (meaning that the component will last longer), and sustainability character. In the article below, Andoni Sanchez-Valverde Erice, Sales/R&D engineer at Outokumpu metallic powder producer, explains some of the key technical considerations in the production of spherical stainless steel powder feedstock.
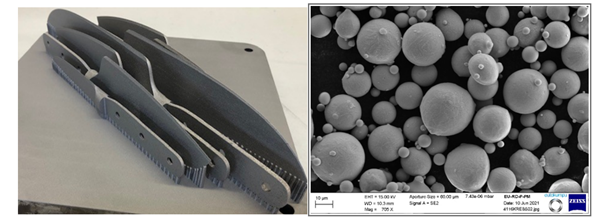
Currently, stainless steel is the third most-preferred feedstock for AM industries behind titanium alloys and nickel alloys. However, according to AMPOWER, by the end of 2027 stainless steel will be the most used feedstock with a market share of 33%.
Producing stainless steel powder
Stainless steel powder is produced by the vacuum induction/inert gas atomization (VIGA) process shown in Figure 2. It produces highly spherical metal powders in a range of diameters between 0-300 µm.
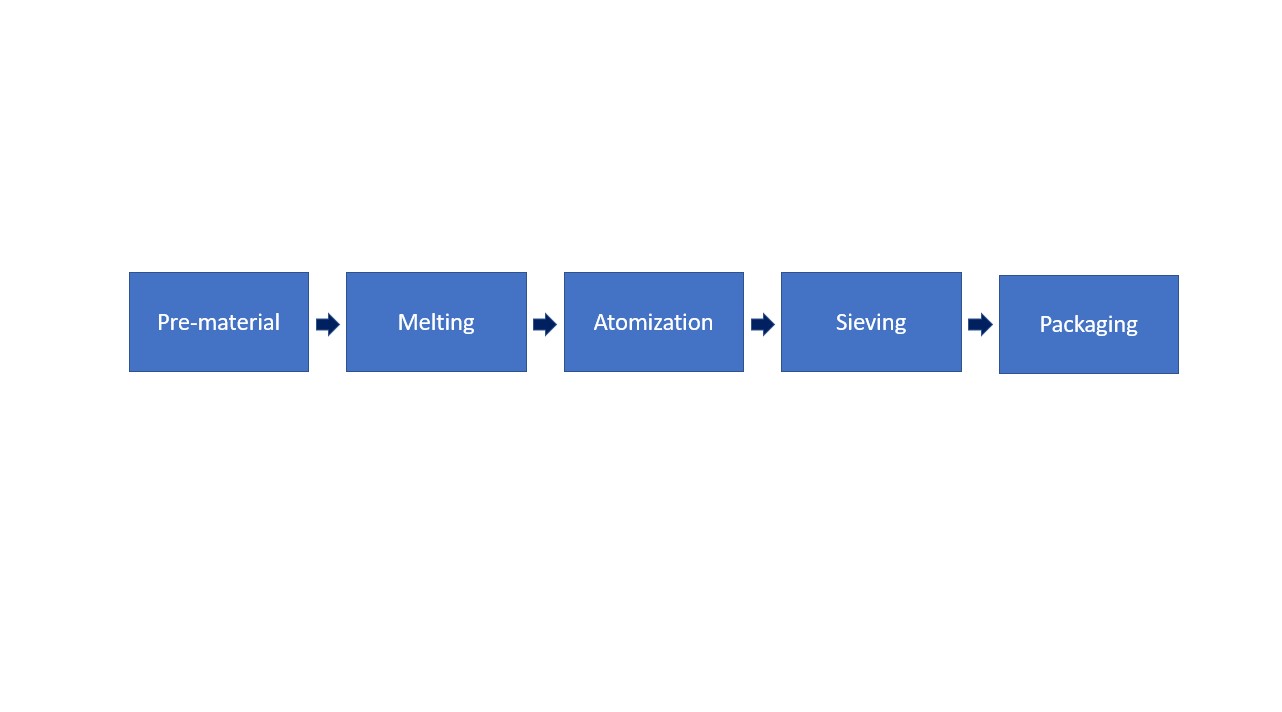
The details of the process equipment are shown in Figure 3.
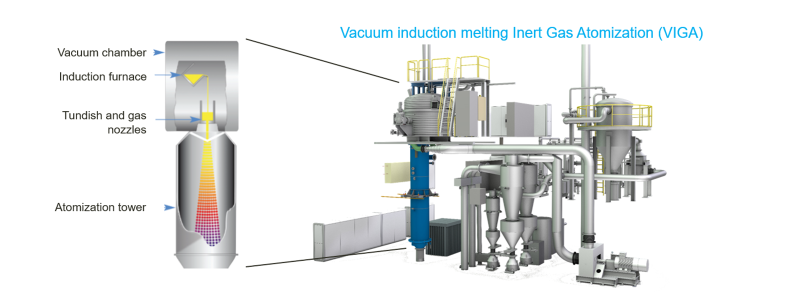
Pre-material: In most cases, the pre-material is scrap from flat product processing. The material is then cut into small pieces suitable for the process – typically 25 x 25 x 1~4 mm. These small pieces are then placed in the furnace crucible.
Melting: This takes place under vacuum conditions to avoid possible oxygen contamination and burning of important elements of the melt. It is possible to measure and control all the important process parameters such as temperature, pressure and vacuum. The melt can also be chemically analyzed to check if further alloying is needed to achieve the correct composition. When the melt is ready, the furnace is flushed with argon or nitrogen and the casting process begins.
Atomization: The melt flows through the tundish and is atomized into very small droplets by nitrogen or argon gas at high pressure and temperatures (up to 32 bar and 450 C°). The small droplets solidify in spherical form and fly through the pipes to the cyclone. Here, the solidified powder is separated from the gas and collected in the collection bins.
Sieving: The powder is separated into different fractions by mechanical sieving and an air classifier to target different powder metallurgy technologies. If, for example, a customer does not want to have more than 5% of their powder smaller than 20 µm, then the air classifier can be used to separate the smaller powders from the batch.
Why is the choice of atomization gas important?
There are four main reasons why a customer might select nitrogen (N) or argon (Ar) as the gas to atomize their powders:
Price: Nitrogen is less expensive than argon. This has an impact on the price of the finished powder. Powder atomized using argon will be more expensive.
Morphology: Argon has a lower heat capacity than nitrogen. Therefore, powder atomized with argon has more time to achieve the desired spherical morphology before solidifying. Powders atomized using nitrogen solidify faster in a more irregular shape, although they are still highly spherical.
Proportion of fine powders: When atomizing a batch under the same temperature and pressure conditions, the proportion of fine powders – which are of interest for some AM technologies – is higher when using nitrogen. The full explanation for this is quite technical. But the simple reason is that nitrogen atoms are smaller, so at the same temperature and pressure, less energy is needed to divide the metal into a higher number of small droplets.
Powder properties: The mechanical and corrosion properties of powders can be influenced by the atomizing gas. For example, nitrogen can increase both the machinability and corrosion properties of printed parts.
Anti-satellite system makes a crucial difference
A crucial feature in powder production is the anti-satellite system. Satellites are small droplets that adhere to the larger spherical particles – see Figure 4. To avoid this, argon or nitrogen is recirculated into the atomization tower. This gas pushes the very small droplets to the bottom and the likelihood of satellites in the solidifying particles is reduced.
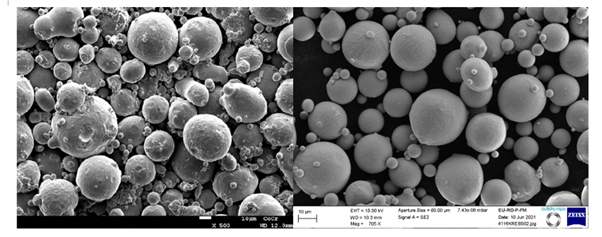
The presence of satellites rather than smooth, round powder will impact the quality of AM components in two ways:
Spreadability: The spreadability of the powder is decreased if it features satellites rather than perfectly spherical powders. This is important for the part of the process where the next layer of powder is spread onto the existing powder layer by the re-coater.
Morphology: Satellites reduce the apparent density and the packing of the powder. If the density of the powder is decreased there is a higher risk of failure in the AM process, due to pores or air gaps between the particles.
The need for a range of powder sizes
Each powder metallurgy technology requires different powder sizes. That is why powders are differentiated not only by the grade and the gas used for atomization but also the size. Powders up to 300 µm suit these AM and PM technologies:
- Binder jetting technology (BJT): <20 µm
- Laser powder bed fusion (PBF-LB): 15 to 45 µm and 20 to 63 µm
- Electron beam powder bed fusion (PBF-EB): 20 to 150 µm
- Direct energy deposition (DED): 20~45 to 150 µm
- Metal injection molding (MIM): <20 µm
- Hot isostatic pressing (HIP): 0-300 µm
Extending the scope of stainless steel grades
Currently, the stainless steel grades used most widely in AM and other powder technologies are 316L and 17-4PH. However, there are a number of new steel grades becoming available to the AM sector that are a closer match for the demanding requirements of high-performance applications.
The “commodity” stainless steels grades used in AM technologies are:
316L (1.4404): a low-carbon alternative to 316. This minimizes carbide precipitation as a result of heat input, for example during welding, giving improved resistance against intergranular corrosion. 316L/4404 is suitable for a wide variety of applications in the automotive, chemical, petrochemical and medical industries. Typical products include flanges, valves, and medical devices.
17-4PH (1.4548): a well-known martensitic precipitation hardening (PH) steel with alloying elements such as chromium or nickel. It has good corrosion properties and excellent mechanical properties up to 300°C. It is used in the aerospace, pulp and paper and nuclear industries for products such as mechanical seals, pumps or turbine blades.
Added-value special stainless steels grades include:
904L (1.4539): Special grade for high-corrosion environments. It is a high-nickel and molybdenum austenitic stainless steel with very high corrosion resistance. It was originally developed for handling sulfuric acid at ambient temperatures and is now used in a broad range of applications in the oil and gas and chemical industries. Typical parts produced from 904L are pumps, valves and flanges.
253MA (1.4835): Special grade for high-temperature applications. This is an austenitic stainless steel with excellent oxidation and creep resistance in cyclic conditions that is best employed in temperatures up to 1150°C. It is used in the oil and gas, aerospace and motorsport industries for parts such as fittings and heat exchangers.
1.4116: Special grade that is a high-hardness martensitic stainless steel with improved corrosion and wear resistance compared to other martensitic stainless steels. It is used in the healthcare and consumer goods industries for products such as medical devices and knives.
Nickel-free austenitic stainless steel powder (modified 1.4678): This specially-developed Ni-free stainless steel powder is an ideal substitute for 316L or Co-Cr alloys. It is also a perfect grade to avoid Ni-allergic reactions in health applications or consumer good applications for products such as watches and other items worn close to the body.
Nickel (Ni) – based alloys are also available:
Alloy 625: For use in very harsh, corrosive environments at high temperatures. Alloy 625 combines nickel, chromium, molybdenum and niobium that give excellent corrosion properties and excellent mechanical properties. When compared with Alloy 718, Alloy 625 has a greater overall resistance to oxidation. It is used in the oil and gas, aerospace and defense industries for components such as fittings, rocket parts, heat exchangers and vessels.
Alloy 718: This Ni-based alloy is also used for high corrosion environments and at high temperatures. It has additions of molybdenum, tantalum, aluminum and titanium that provide higher strength and better weldability, as well as improved stress corrosion cracking (SCC) resistance than alloy 625. It is used in the oil and gas, aerospace and defense industries for components such as fittings, rocket parts, heat exchangers and vessels.
Taking AM to the next level
The increased availability of stainless steel powders will open up new possibilities for designers who want to create AM parts that offer corrosion-resistance, durability and long life.
As a stainless steel manufacturer, Outokumpu is bringing its knowledge to the industry by launching a new business to support AM. This has included the commissioning of an atomization plant at our mill in Krefeld, Germany. This powder plant is effectively a large recycling unit that uses scrap resulting from existing production processes.
This article has first been published in the May/June edition of 3D ADEPT Mag.
Remember, you can post job opportunities in the AM Industry on 3D ADEPT Media free of charge or look for a job via our job board. Make sure to follow us on our social networks and subscribe to our weekly newsletter : Facebook, Twitter, LinkedIn & Instagram ! If you want to be featured in the next issue of our digital magazine or if you hear a story that needs to be heard, make sure to send it to contact@3dadept.com