Machine manufacturer 3DCeram expands its area of expertise with a new 3D printer. The manufacturer that we used to see in the SLA field, will now provide what it calls a Multi Additive Technology (M.A.T) – a simple and explicit name that combines the capabilities of different technologies within the same platform: FFF, machining and extrusion also known as robocasting.
The new machine would process filament albeit with high volumetric loading (around 50 %) of fine ceramic powder dispersed in a thermoplastic matrix. Once the shaping has been done with the FFF printer, the “green” parts are then subjected to debinding (process of elimination of binder) followed by sintering (process of compacting the fine ceramic powder) to obtain a pure part of ceramic, the company explains. The steps that follow the manufacturing process are quite familiar with the ones seen in Pellet AM.
Unlike the standard FFF process where filaments are much more brittle and soft and do not bend so easily, 3DCeram’s M.A.T requires an extruder motor and extrusion mechanism. These options facilitate the extrusion of the filaments while ensuring the possibility to overcome the viscosity and the ability to push the melted liquid out of the fine nozzle; a nozzle that can be as small as 0,3 mm in diameter.
Furthermore, since the filaments of most technical ceramics tend to melt at temperatures that can be lower by 50–100 °C as compared to plastic FFF materials, they soften already at temperatures of 40–50 °C.
This means that while the filament warms up close to nozzle, it has to be cooled everywhere else! In addition, there are numerous other fine points that need to be taken care of like the choice of suitable abrasion resistant material and size of nozzle, extrusion parameters that are significantly different to those of the thermoplastics, slicing algorithms to reduce the internal stress in body during shaping, and so on, 3DCeram explains.
As far as robocasting is concerned, the company explains ceramicists often use it to extrude ceramic slurry though a nozzle. It does not require a precise filament manufacturing process at the cost of reduced extrusion control and higher surface roughness. This means that through the quick swap of head, one can go from FFF to robocasting.
Other worth mentioning features of the 3D printer include water-cooling of the heat-sensitive filament extrusion head, closed-loop motor control for the XYZ drives of the printer, direct radiative heating of the printed parts to enhance layer adhesion.
As far as materials are concerned, the 3D printer can already process ceramics like SiC, alumina, zirconia. This portfolio can be extended to metals like stainless steel, titanium and copper.
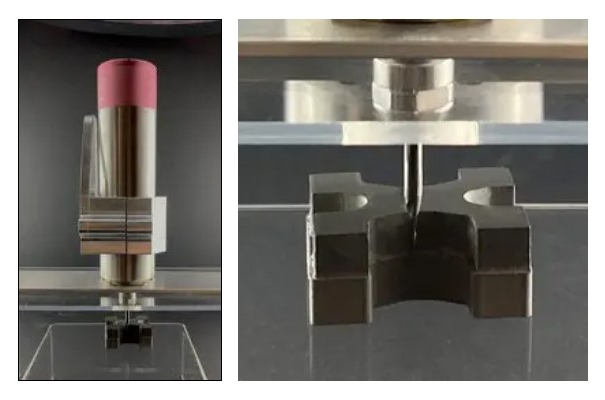
Remember, you can post job opportunities in the AM Industry on 3D ADEPT Media free of charge or look for a job via our job board. Make sure to follow us on our social networks and subscribe to our weekly newsletter : Facebook, Twitter, LinkedIn & Instagram ! If you want to be featured in the next issue of our digital magazine or if you hear a story that needs to be heard, make sure to send it to contact@3dadept.com