Among the companies that can pride themselves on developing a true Large Scale Additive Manufacturing (LSAM) is Thermwood. The secret behind the company’s methodology is a patented Vertical Layer Print (VLP) technology.
As the name implies, Thermwood’s VLP technology produces parts on a vertical plane rather than on a horizontal plane. Logically, this method would deliver 3D printed parts taller than those would be vertically produced. “Parts over 20 feet tall have already been printed on Thermwood’s larger LSAM (L-Sam) systems”, the company said.
“We have over 55 patented features (and over a dozen more pending) that set the LSAM apart from any other large-scale additive system available today”, Dennis Palmer, VP of sales, explained in an interview.
With high walls, a fixed table and moving gantries, Thermwood’s LSAM is a hybrid technology that requires the capabilities of 3D Printing and CNC routers to deliver the desired part.
The company’s new manufacturing approach
The manufacturer’s new approach involves the use of vertical moving table integrated into the printer. Each part is printed on a vertical moving table, reinforced with stainless steel belts that slide on the main table.
However, as a reminder, the printing process is slightly different with the MT machine, the lower cost 3D printer the company launched last year. Indeed, that system has a fixed gantry and a moving table.
“With this new approach, parts are printed on a support structure which is fixed to the back and rides on the moving table. A second 5 foot by 10-foot print table is mounted vertically to the back of the main table. As the part grows, the moving table pulls the part onto the support structure. Using this approach, the LSAM –MT can then print parts up to 5 foot/152 cm (Z Axis) by 10 foot/305 cm (X Axis) by 10 foot/305 cm (Y Axis)”, the company explains in a press communication.
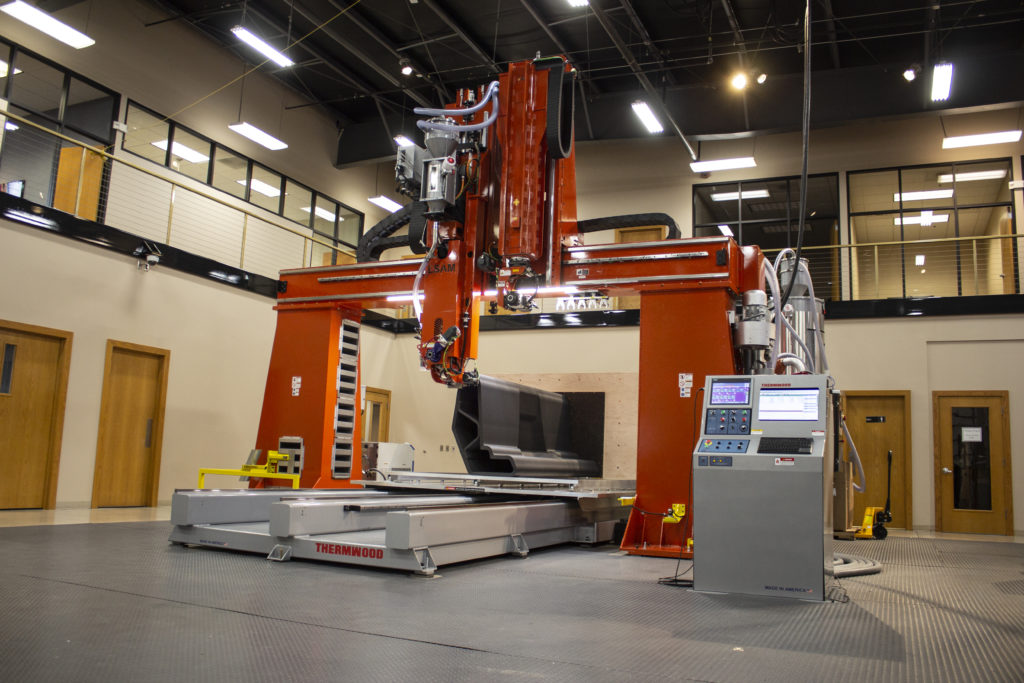
This process has proved out its capabilities as the technology can process both low and high temperature thermoplastic materials. The US-based company tested this approach by producing parts with two materials:
- Carbon fiber reinforced ABS, a material that is acknowledged for the manufacturing of tooling, fixtures, foundry patterns and various structural components.
- A 25% carbon fiber reinforced PSU/PESU, another high-temperature material that is ideal for the fabrication of molds and tooling that operate at elevated temperatures, often in an autoclave using pressure and vacuum. Not only do these parts sustain vacuum to aerospace standards, but they do not require a secondary coating, which is an additional benefit for the operator. As part of the testing process, Thermwood manufactured in 16 hours and 40 minutes, a printed part of 1190 pounds (540 kg).
“Both the MT and Thermwood’s larger LSAM systems can both print and trim on the same machine. Parts are first printed at high speed and then, when cooled, machined to the final size and shape. The larger scale LSAM machines can theoretically vertically print parts that weighed up to 50,000 pounds, which means there is no practical weight limitation and VLP equipped machines up to forty feet long have built and delivered”, the company concludes.
Remember, you can post AM job opportunities for free on 3D ADEPT Media or look for a job via our job board. Make sure to follow us on our social networks and subscribe to our weekly newsletter: Facebook, Twitter, LinkedIn & Instagram! If you want to be featured in the next issue of our digital magazine or if you hear a story that needs to be heard, make sure to send it to contact@3dadept.com