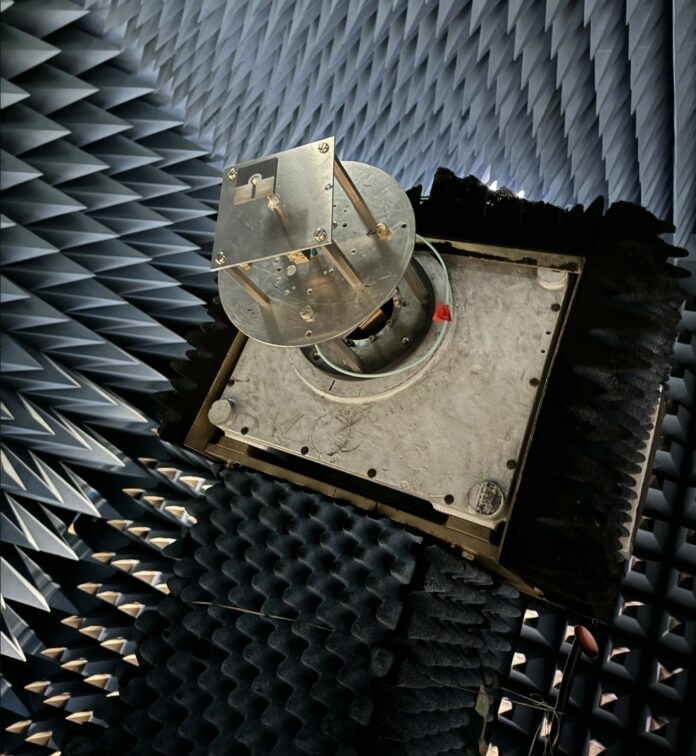
With the goal of demonstrating a low-cost capability to communicate science data to Earth, NASA developed and tested a 3D-printed antenna with the network’s relay satellites and then flew it on a weather balloon in just three months.
For the record, the from NASA’s Near Space Network and Goddard Space Flight Center’s 3D Printing of Electronics group used a 3D printed from Fortify to manufacture the antenna. According to these engineers, the 3D printer was a good candidate to control the electromagnetic and mechanical properties of the antenna. The bulk of the 3D-printed antenna uses a low electrical resistance, tunable, ceramic-filled polymer material.
Following manufacturing, the antenna was assembled and tested at NASA’s Goddard Space Flight Center in Greenbelt, Maryland, in the center’s electromagnetic anechoic chamber.
The anechoic chamber is the quietest room at Goddard — a shielded space designed and constructed to both resist intrusive electromagnetic waves and suppress their emission to the outside world. This chamber eliminates echoes and reflections of electromagnetic waves to simulate the relative “quiet” of space.
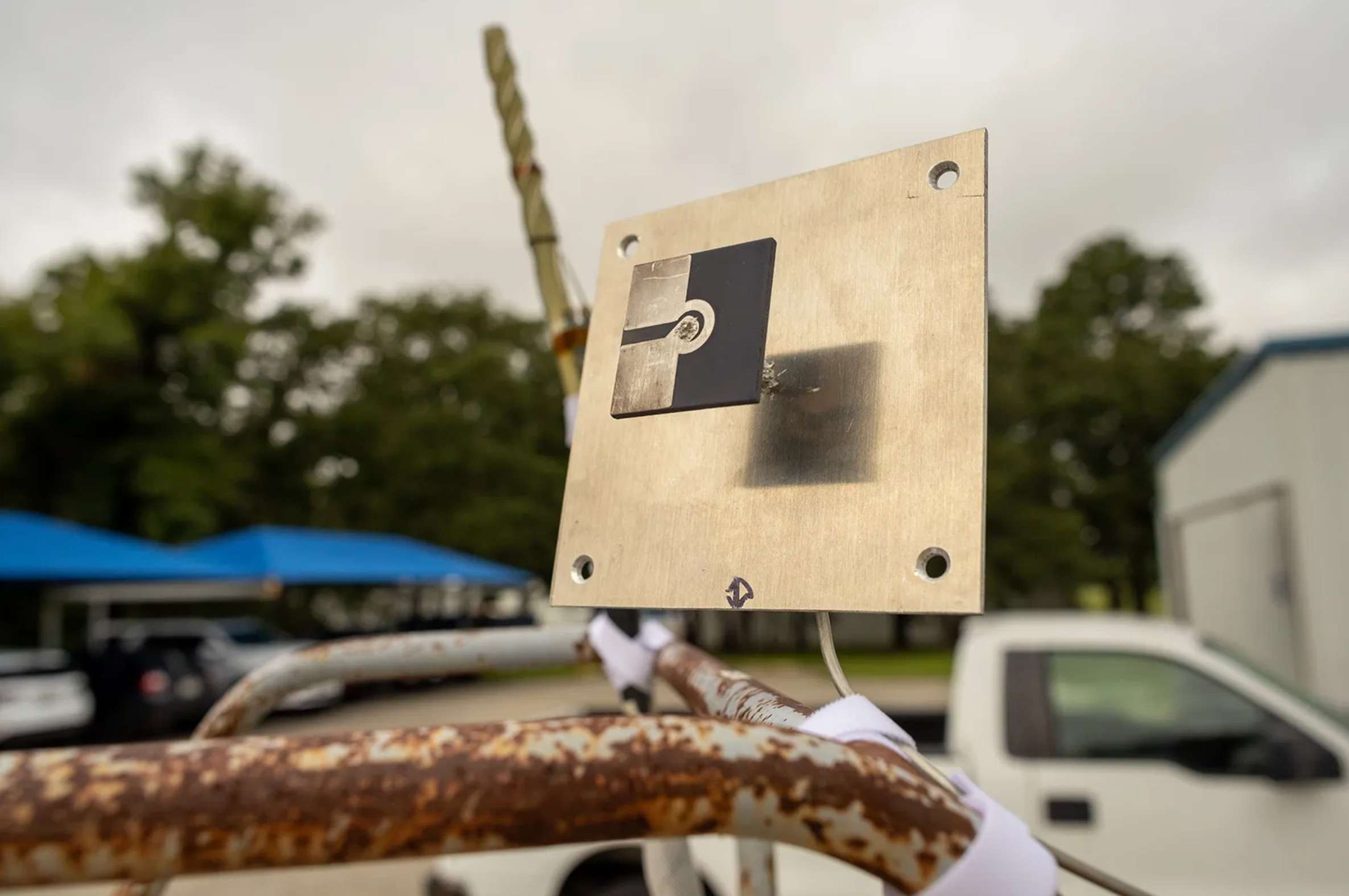
NASA/Peter Moschetti
To prepare for testing, NASA intern Alex Moricette installed the antenna onto the mast of the anechoic chamber. The antenna development team used the chamber to test its performance in a space-like environment and ensure it functioned as intended.
Once completed, NASA antenna engineers conducted final field testing at NASA’s Columbia Scientific Balloon Facility in Palestine, Texas, before liftoff.
The team coordinated links with the Near Space Network’s relay fleet to test the 3D-printed antenna’s ability to send and receive data.
The team monitored performance by sending signals to and from the 3D-printed antenna and the balloon’s planned communications system, a standard satellite antenna. Both antennas were tested at various angles and elevations. By comparing the 3D-printed antenna with the standard antenna, they established a baseline for optimal performance.
During flight, the weather balloon and hosted 3D-printed antenna were tested for environmental survivability at 100,000 feet and were safely recovered.
The testing revealed that AM can help create high-performance communication antennas tailored to mission specifications faster.
Remember, you can post job opportunities in the AM Industry on 3D ADEPT Media free of charge or look for a job via our job board. Make sure to follow us on our social networks and subscribe to our weekly newsletter : Facebook, Twitter, LinkedIn & Instagram ! If you want to be featured in the next issue of our digital magazine or if you hear a story that needs to be heard, make sure to send it to contact@3dadept.com