AMUG saw a number of collaborations between Materialise and other companies. Besides the work they are achieving with Sigma Additive Solutions, the software company will also work on the integration of Phase 3D’s solution Project Fringe into Materialise Process Control software solution.
Materialise Process Control Software solution
Designed for metal 3D printing and available as part of CO-AM, the process control software solution enables AM users to take full control of the 3D printing process by using automated quality control and customizing their 3D printer parameters. The solution is introduced alongside the Build Processor Software Development Kit (BP SDK).
By analyzing and correlating layer data from the 3D printing process, users can identify defective parts before they are sent to post-processing and quality inspection, which can account for 30 percent to 70 percent of a part’s total manufacturing cost. Analyzing the layer data also enables users to find the root cause of defects faster, allowing them to optimize the process and adapt their 3D printing parameters. Early scrap detection and root cause analysis help lower the cost per part by reducing both scrap rates and expensive quality control efforts during post-processing.
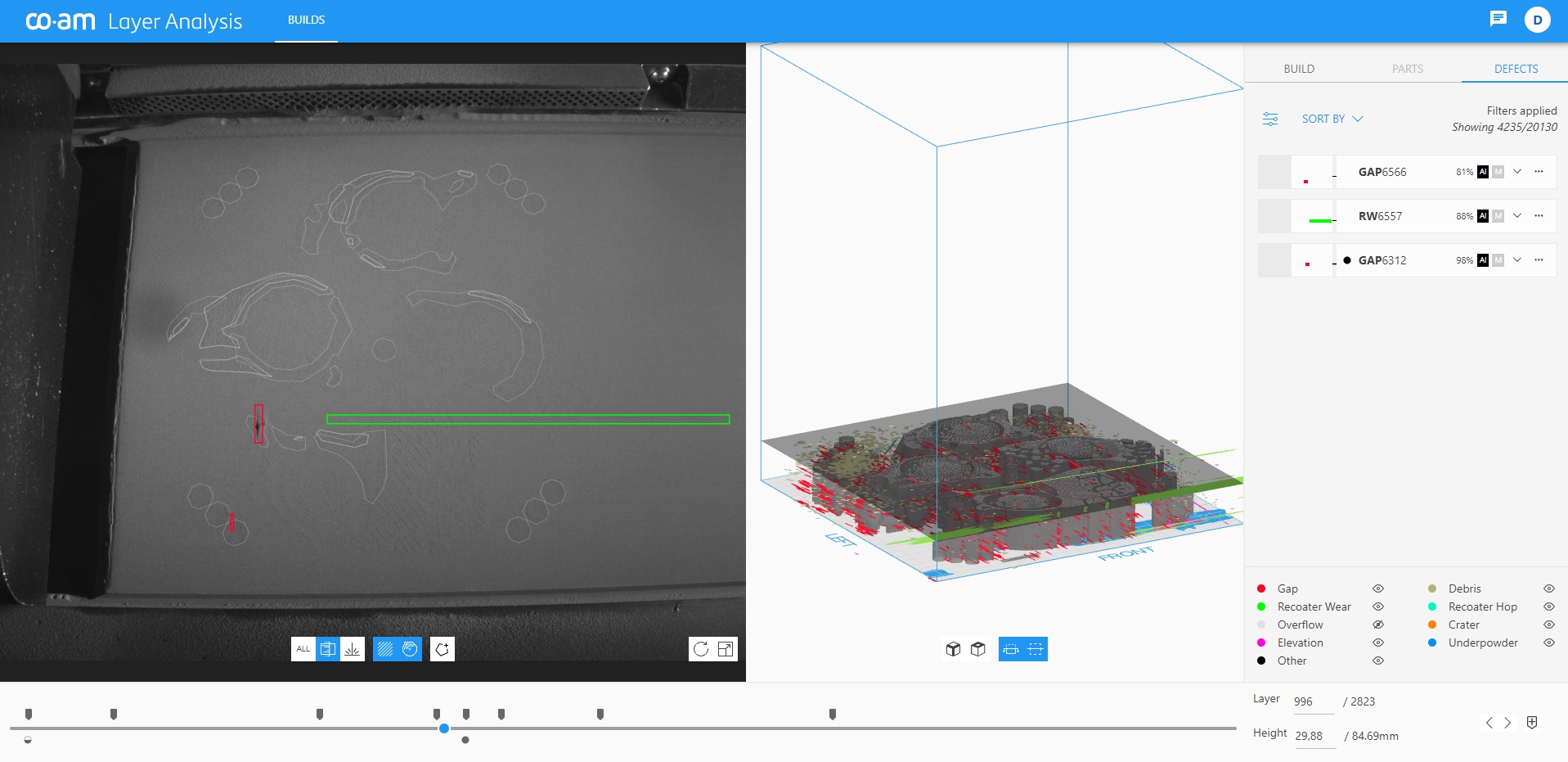
As for the build processor (BP), it connects 3D printers with software for data preparation such as Materialise Magics. It manages 3D printer-specific information and enables users to influence build parameters, which influence how fast a 3D print job is done and determine part properties such as density and surface quality. Suboptimal build parameters increase the cost per part by causing long build jobs, high efforts during post-processing, and high scrap rates.
However, until now it was very difficult to create BPs or adapt them for specific applications. The BP SDK offers an agile way to achieve that. Machine vendors and manufacturing companies with R&D capacities can use the development platform as a toolkit on their own, rely on Materialise’s AM expertise or choose a collaborative approach. Using proven BP technology, they can shorten the product development cycle, integrate their own APIs, and generate new intellectual property. This open development process supports collaboration and can drive the diversification and optimization of BPs.
The integration of Phase 3D’s solution Project Fringe
Phase 3D’s solution Project Fringe is an in-situ inspection system for Additive Manufacturing. The solution is a proprietary structured light technology that measures any powder-based AM process. The real-time data creates detailed measurements for where and when a print anomaly occurs. Project Fringe presents data in 3D, enabling users to see a multitude of print anomalies in real-time. The solution allows customers to be confident about their part quality or stop the 3D printing process if a defect has been detected, saving machine time and money.
According to Niall O’Dowd, Founder and CEO of Phase3D says, “real-time inspection using rapid height measurement technology can reduce the cost per part in 3D printing.”
Phase3D collaboration with Materialise allows their customers to combine Project Fringe’s in-situ inspection technology with Materialise Process Control as part of CO-AM.
Remember, you can post job opportunities in the AM Industry on 3D ADEPT Media or look for a job via our job board. Make sure to follow us on our social networks and subscribe to our weekly newsletter : Facebook, Twitter, LinkedIn & Instagram ! If you want to be featured in the next issue of our digital magazine or if you hear a story that needs to be heard, make sure you send it to contact@3dadept.com