Remember when we told you that, sometimes long-time existing processes or technologies can help refine and enhance production processes? Among the wide range of technologies or features that can be used to enhance production with AM, there is ultrasonic. Interestingly, we first discovered ultrasonic Additive Manufacturing as a manufacturing process, but the more we dive into the different usages of ultrasonic, the more we find out that the term can be applied to other applications.
Simply put, “ultrasonic” refers to a frequency greater than the upper limit of the audible range for humans —that is greater than 20 kilohertz. The term “sonic” is applied to ultrasound waves of very high amplitudes. This implies that the term itself is not limited to the manufacturing field. By sticking to this basic definition, Andreas Hartmann, CEO & Cofounder of Solukon Maschinenbau GmbH said “it is therefore always about the stimulation of a substance or material.”
In the AM industry, Hartmann identified two types of ultrasonic usage: “applications where the main purpose is to use ultrasound technology – This is the “Ultrasonic Additive Manufacturing as a fabrication process” but also, for example, ultrasonic cleaning equipment.” “The second area of application is, in my view, where ultrasound is used as a feature or add-on or extension of an existing technology. For example, as with our SFM-AT350-E powder removal system. In LPBF [for instance], ultrasonic excitation is used in various process steps like depowdering, powder recovery, powder preparation (sieving) or final cleaning in ultrasonic fluid baths. Ultrasonics are often required where certain material properties like flowability are challenging,” he adds.
When ultrasonic AM is not a manufacturing process…
Today, ultrasonic technology is utilized in several industrial applications, to measure distances, for parking assistance, flow-rate measurement, level detection, and composition analysis. The development of smart machines and the Internet of Things have paved the way for applications of ultrasonic sensors.
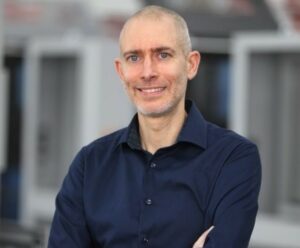
According to Hartmann, if little information is shared about the use of ultrasonic technology as an add-on to an existing technology, it’s probably because “the know-how usually lies with external experts who offer their ultrasound solutions for many industries”, not to mention that developers of ultrasound solutions are keen to protect their “intellectual property”.
We don’t often realize it, but different stages of the AM process chain can benefit from ultrasonics. “First of all, applying ultrasonic in powder removal is beneficial for the overall process chain. With the precise tracking of its parameters and the possibility of fine adjustment, it effortlessly achieves all the sophisticated objectives of process monitoring and therefore quality assurance.
As Ultrasonic works electrically with only little energy consumption it means significant energy-saving potential for the entire production chain and drives sustainability.
Furthermore, thinking of other steps of the production line, ultrasonics can be integrated into the AM process for real-time monitoring and quality control:
Defect Detection: ultrasonic sensors can detect internal defects such as porosity, cracks, and delamination during the build process. This allows for immediate correction or rejection of defective parts. Process Optimization: real-time feedback from ultrasonic sensors can help optimize process parameters, such as laser power and scanning speed, to improve part quality,” Hartmann explains.
Key examples
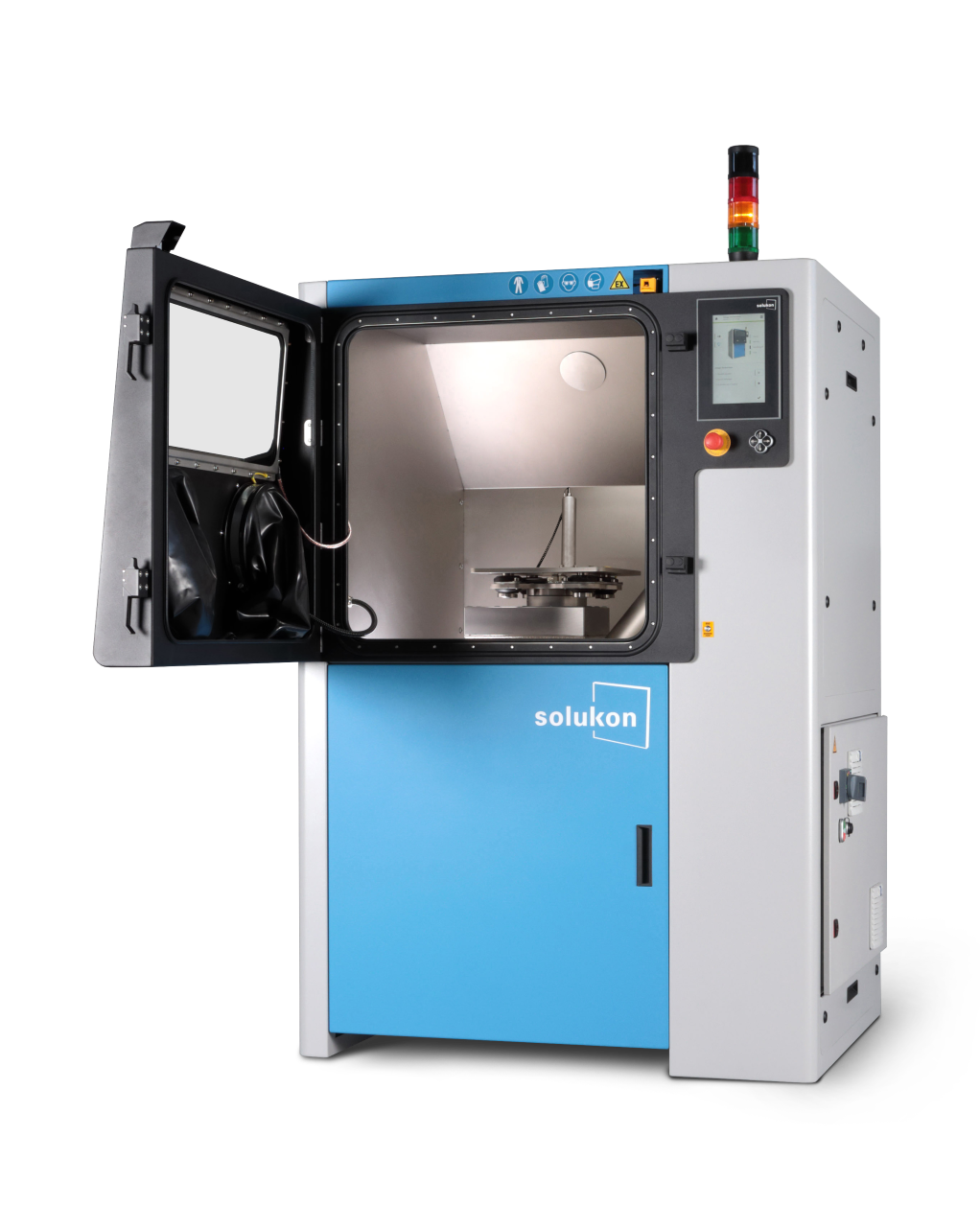
The experts from Zetec are using ultrasonics to support nondestructive testing (NDT) methods for 3D printed parts. Ultrasonic NDT Methods consist of using various ultrasonic imaging methods to detect porosity and other flaws in 3D printed metals.
In the same vein, researchers at University of Bristol recently developed ultrasonic sensors for AM quality control. This process employs non-contact ultrasonic array sensors, akin to those used in medical imaging. The team created a mathematical model that incorporates the physics of ultrasonic wave propagation through layered metallic materials produced by AM. With some adjustment of the input parameters, this model enhances the information output, which is essential for evaluating the mechanical integrity of the 3D printed parts.
“There is a potential sensing method using a laser-based ultrasonic array and we are using mathematical modeling to inform the design of this equipment ahead of its in situ deployment,” said Professor Anthony Mulholland, head of the School of Engineering Maths and Technology.
As he anticipates rapid adoption within the industry, the professor is exploring collaborations to integrate this technology into AM processes. This integration could lead to streamlined production, innovative designs, and bolstered economic competitiveness for UK manufacturing.
In the materials segment, we have seen AMAZEMET, a developer of laboratory-scale units for the in-house manufacturing of powders, use ultrasonic vibration for metal atomization. With its rePowder machine, metal is poured or melted directly on the vibrating part resulting in tiny droplets being ejected from the surface. Droplets solidify in the surrounding inert gas atmosphere forming powder particles. This leads to highly spherical metal powders with narrow particle size distribution – up to 80% is good to use in desired processes, the company explains.
In the depowdering phase, ultrasonic is a key add-on to Solukon’s automated powder removal.
“From nearly a decade experience in depowdering, we saw that for certain geometries pneumatic excitation reaches its limits. This is especially the case for delicate structures like long winded channels or lattice structures like in medical industry. The main aim of ultrasonic excitation is to excite the component above the damaging natural frequency of the part. Initially, we had several tests with external ultrasonic exicators integrated into a depowdering machine. They proved to be successful and appeared to be a game-changer in some specific applications – for instance, copper. So, we decided to launch a dedicated depowdering system, the SFM-AT350-E with piezoelectric (=ultrasonic) excitation.
Ultrasonic depowdering solutions will not replace the well-established and proven solution with pneumatic excitation and an optional knocker. Pneumatic turbines are simple, robust and depowder very efficiently; especially for large and heavy parts, this is the way. Launching an ultrasonic depowdering solution, we have rather created a wealth of variants to adapt even better to the individual requirements of our customers. It is like a new dedicated tool in our big toolbox for powder fluidization,” Hartmann points out.
For Solukon’s CEO/CTO, the use case of ultrasound shows that there is always a need to further develop core technologies and exchange ideas with experts from other fields.
When ultrasonic AM is a manufacturing process…
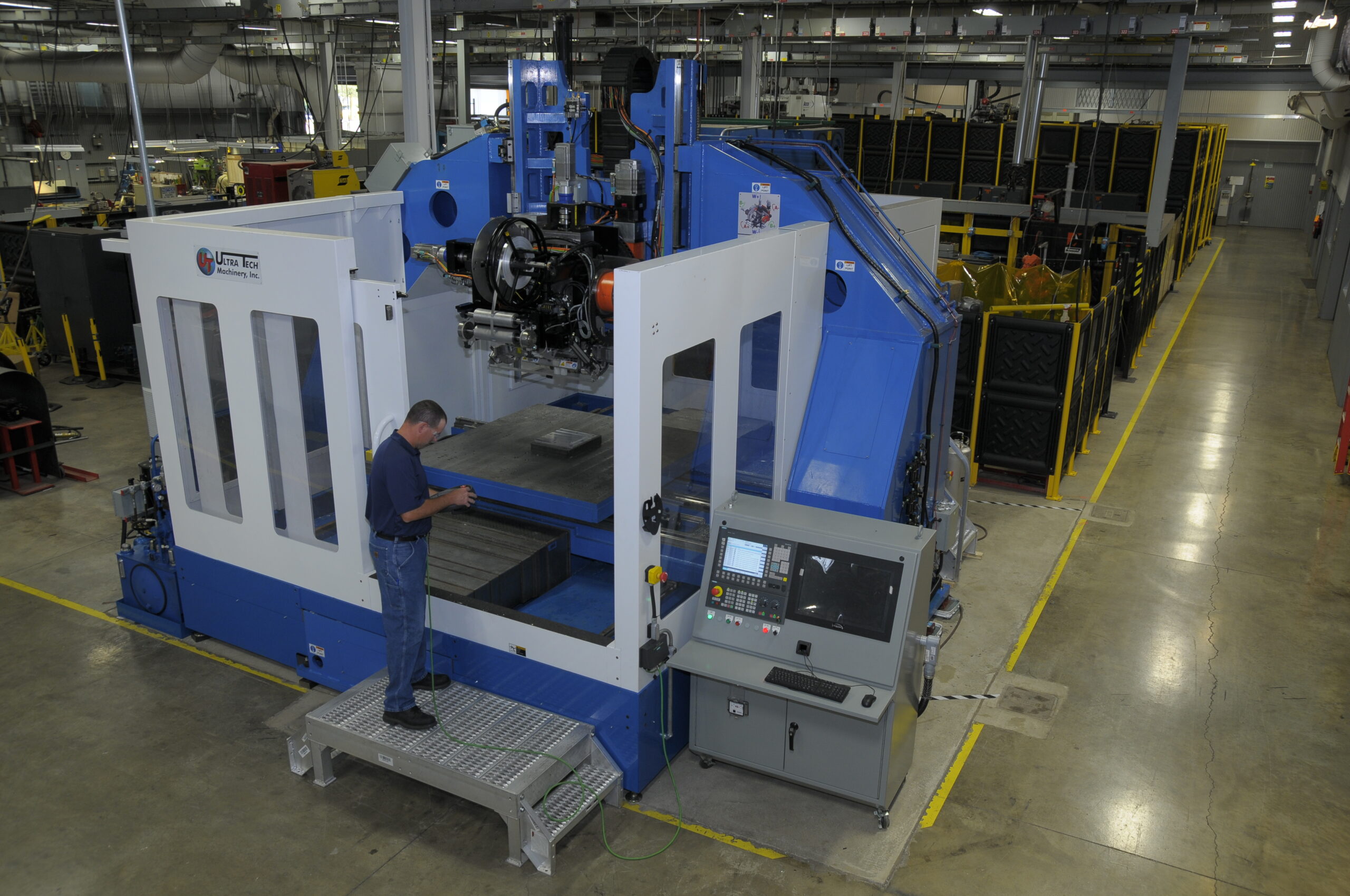
Ultrasonic additive manufacturing (UAM) also known as ultrasonic consolidation (UC), is a solid-state additive manufacturing process invented in 1999 by Dawn White. This hybrid sheet lamination process brings together ultrasonic welding and computer numerically controlled (CNC) milling. The process is described as a low-temperature metal 3D printing solution, because materials are not melted during the process. They are rather joined through ultrasonic welding. This welding technique employs high-frequency vibrations to join surfaces while the metal stays solid. By repeatedly welding layer upon layer, the process fabricates solid, dense metal parts.
In the short list of manufacturers who have made UAM their core business, one counts Fabrisonic, a small tech startup headquartered in the USA that patented this process in the USA and in Europe.
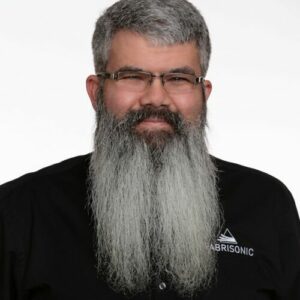
According to Mark Norfolk, President & CEO, the process always works as explained above. However, applications that can be achieved with this process can be of different sizes, depending on the size of the machine one uses. “It’s a matter of scale,” he says.
As you can understand from the definition, UAM can be combined with other processes.
“One problem in the AM industry is people feel like they have to 3D print the entire part and nothing could be further from the truth”, Norfolk said. “We have customers who provide us cast aluminum heat exchangers, and then we print additional features onto a casting. We have customers who send us preexisting weldments and we add features to those weldments.”
“Our process is not ideal for very organic, cellular-looking structures but powder bed fusion is fantastic at that. So, our partners can manufacture very complex organic shapes that we will embed in our product, through ultrasonic additive,” he adds.
These possible combinations with manufacturing techniques such as DED and LPBF facilitate the transition between materials or the creation of dissimilar metal joints that enhance said manufacturing technique.
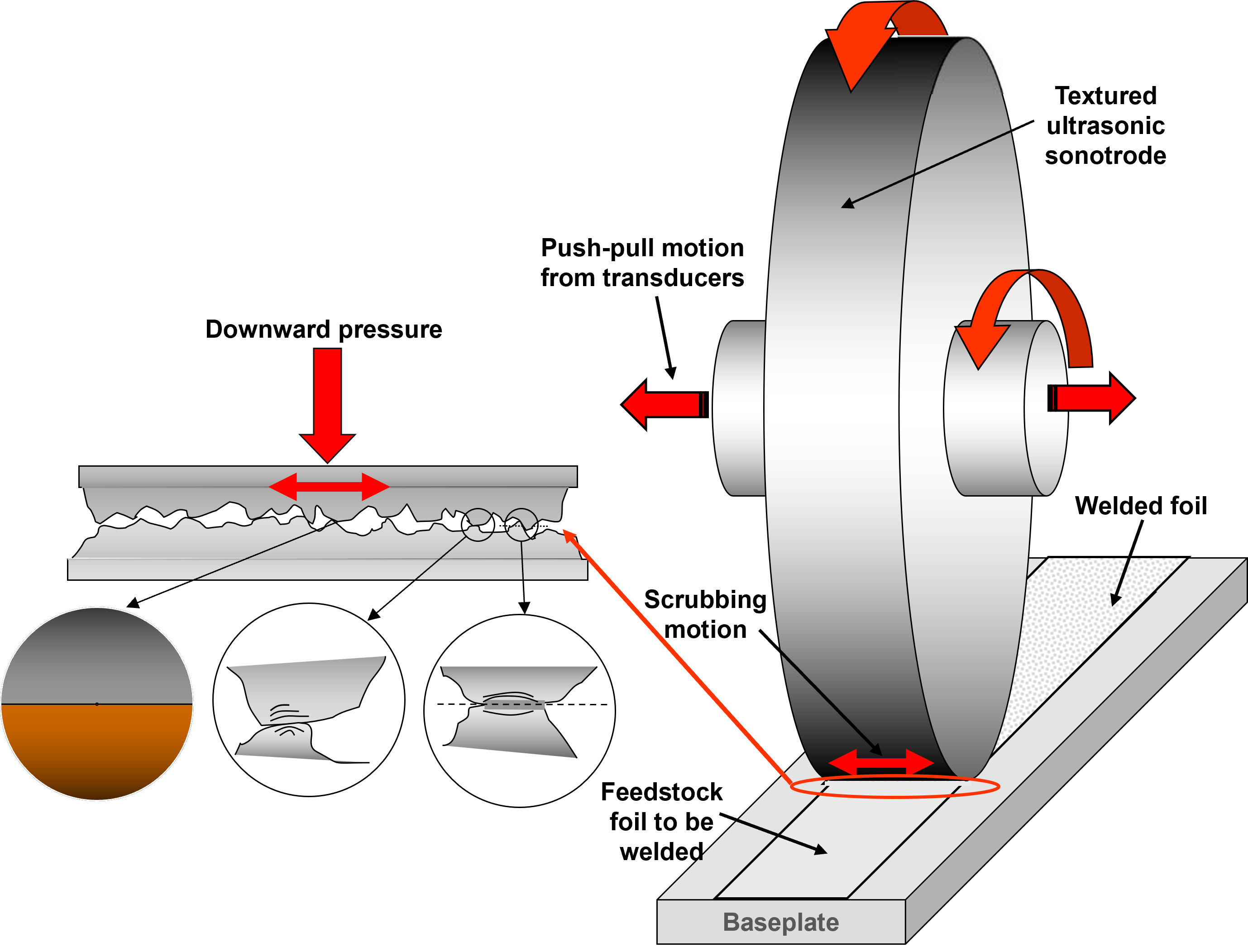
As a matter of fact, dissimilar metals are the first area where the company sees a greater use of its technology. “We can combine titanium with tantalum, aluminum, or nickel, all in the same part without having to worry about metallurgical problems”, the CEO explains.
While Norfolk lays emphasis on the fact that UAM is just another manufacturing tool, we couldn’t help but think that the process is already serving emerging industries where AM applications are yet to be discovered. Those industries include energy and electrification – in addition to well-known sectors such as space and aerospace.
“The second area that highlights the benefits of our technology is embedded electronics”, Norfolk enthuses while remembering that one of their customers made 35 million parts last year in the electric vehicle space. “Our technology which uses foil as a feedstock lends itself to EV construction.” [The low-temperature process makes it easy to embed a sensor, a tracking device, etc. forever in solid metal or parts. The build is paused to insert the embedded object, and then it resumes to seal it inside. The bonding temperature for all metals remains below the melting point, preventing issues with thermal deformation.]
Furthermore, given the fact that the price point is much lower for foil, UAM does not deal with the same challenges other manufacturing techniques face when it comes to material accessibility. Indeed, while one can hear prices that vary from $100 to $200 per kilogram for powder, it’s possible to pay $10 per kilogram for metal foil typically – “unless it’s something like gold”, Norfolk warns us.
Legend: Embedded tubes. To avoid sealing issues, tubes can be embedded in place of machined channels. Credit: Fabrisonic.
So, how can we explain the slow adoption of UAM?
On paper, UAM has everything to be propelled in the AM industry: the possibility to achieve coveted applications such as heat exchangers, embedded sensors, dissimilar metals, selective reinforcement, to name a few; a wide range of opportunities in terms of materials and a low-temperature point which plays to the strengths of this process.
As no technology is perfect, Norfolk recognizes that they still need to work on their ability to deal with fine geometries: “We can’t weld on very delicate structures. The higher the strength of the metal, the harder it is to weld. We still need to do more research and development to get into production in this area.”
Despite these slight adjustments to make, the process strives to position itself as a strong force in the industry.
In the case of Fabrisonic, one reason that may explain this slower adoption compared to LPBF for instance, is their business model. The startup is owned by a non-profit – therefore “exists for the benefit of mankind”. This means that resources are limited to invest in large marketing campaigns as other businesses do to grow in this market.
That being said, the company’s technology is distributed globally. Fabrisonic’s UAM is CE-certified and is already being used in the UK, Spain and France. If it has firm intentions to expand its geographical scope, one should appreciate Fabrisonic for its ability to focus its strength on areas where they have a strong advantage.
This dossier has first been published in the July/August edition of 3D ADEPT Mag.