Parmi le large éventail d’applications que permet la fabrication additive, un intérêt majeur est consacré au traitement des superalliages pour l’aérospatiale, l’automobile et même le nucléaire ; des industries en bref, qui nécessitent une combinaison exceptionnelle de propriétés mécaniques supérieures et de résistance à l’usure. Dans ce contexte, l’Inconel 718 suscite un intérêt croissant.
Rappel rapide : les superalliages sont un type de matériaux qui peuvent conserver une grande résistance à des températures élevées. Ces matériaux revêtent la plus haute importance pour les industries qui ont besoin de fabriquer des composants à partir de métaux de haute performance. Les superalliages à base de nickel sont le type d’alliages compatibles avec la fabrication additive. L’un de ces superalliages est l’Inconel 718.
À ce jour, de nombreux opérateurs ne connaissent pas le type de technologies de FA qui permettent de traiter cet alliage ainsi que ses principales applications et caractéristiques. Cet article vise à faire la lumière sur ce matériau et son utilisation dans l’industrie de la FA.
Présentation de l’Inconel 718
L’Inconel 718 (IN718) est un superalliage à faible coût à base de nickel qui est principalement utilisé comme matériau pour les disques de turbine. Le superalliage a été utilisé pour la première fois dans les années 1960 pour pallier la mauvaise soudabilité des superalliages. Comme les procédés de FA et de soudage sont assez similaires, les opérateurs utilisent depuis lors l’IN718 avec les procédés de FA métallique, afin de faciliter la compréhension des relations procédé-microstructure-propriété. Cela pourrait expliquer les raisons pour lesquelles l’IN718 est principalement associé à la technologie d’impression 3D/FA.
En termes de propriétés mécaniques, l’IN718 offre une résistance thermique exceptionnelle – jusqu’à 700°C – et une grande résistance à l’oxydation et à la corrosion. Il est également reconnu pour son excellente résistance, son haut rendement, ses propriétés de traction et de fluage-rupture. Lorsqu’il est fabriqué de manière additive, l’Inconel offre une résistance sur une large gamme de températures, ce qui en fait un bon candidat pour les applications à haute température ou à basse température.
Avec un point de fusion de 1430°C par exemple, le matériau démontre une résistance efficace à la chaleur et aux températures élevées, il convient donc bien aux conditions cryogéniques. À température ambiante, en revanche, il présente une limite d’élasticité minimale de 725 MPa et une résistance à la traction de 1035 MPa. Lorsqu’il est soumis à un traitement de mise en solution et de précipitation, ces chiffres passent à 1035 MPa et 1240 MPa, respectivement.
La composition de l’IN718 inclue environ 50-55 % de nickel, 17-21 % de chrome, 4,75-5,5 % de niobium et de tantale, et des traces de molybdène, de titane, de cobalt, d’aluminium, de manganèse, de cuivre, de silicium et d’autres éléments.
Il convient de noter que l’Inconel 718 suscite souvent la confusion avec un autre superalliage populaire à base de nickel, l’Inconel 625. L’ajout de fer dans l’IN625, associé à une teneur en nickel plus faible, permet au prix de l’Inconel 718 d’être inférieur à celui de l’Inconel 625. Ces éléments constituent principalement les différences entre les deux matériaux. Voyons maintenant comment il fonctionne lors de sa transformation.
Traitement de l’Inconel 718
L’Inconel 718 est principalement traité par des procédés en lit de poudre. Les technologies de FA qui peuvent traiter ce matériau sont en général la fusion par faisceau d’électrons (EBM), le frittage laser sélectif et, depuis peu, le jet de liant.
Comme chaque procédé de fusion des métaux est unique, la façon dont il traitera l’Inconel 718 modifiera sans aucun doute la structure – les propriétés – le traitement et les performances de la pièce fabriquée.
Nous avons posé à Kyle Myers, le directeur de la R&D d’ExOne, un certain nombre de questions sur ce matériau et sur la façon dont il est traité avant d’être utilisé par un client quelconque. Pour rappel, la récente qualification de l’Inconel 718 porte à 22 le nombre total de matériaux qu’ExOne peut traiter.
Avec plusieurs décennies d’expertise dans le domaine de la FA par jet de liant et de l’industrie en général, on peut dire sans risque de se tromper qu’ExOne connaît une chose ou deux du marché et de la façon dont les entreprises des industries verticales adoptent ces nouvelles technologies.
Le fabricant de systèmes de projection de liant ne développe pas ses propres produits chimiques et poudres. Selon les termes de Myers, ils « développent principalement des paramètres de traitement qui fonctionnent pour les matériaux traditionnels et les poudres couramment utilisées ». « Ces matériaux traditionnels sont qualifiés selon des normes connues que la plupart de nos clients connaissent bien, ce qui leur permet d’adopter plus rapidement notre procédé de fabrication pour leur application. Par conséquent, tout client qui conçoit déjà une pièce, pour son application avec les propriétés physiques et mécaniques inhérentes à cette spécification, peut insérer le jet de liant dans son processus de fabrication. D’autres clients peuvent vouloir profiter de la FA, mais travailler avec un alliage similaire à celui de l’In718. Ils devront faire leurs devoirs pour s’assurer que les spécifications de l’In718 peuvent s’adapter à leur application spécifique », a déclaré Myers à 3D ADEPT Media.
Pour les chercheurs, la microstructure de l’IN718 fabriqué de manière additive dépend largement de l’historique du processus spécifique. Avec des paramètres de processus différents, tels que la stratégie de numérisation et la géométrie des composants, il est possible d’obtenir des microstructures d’IN718 telles qu’elles sont fabriquées, même avec la même méthode de fabrication, sans parler des méthodes de fabrication différentes. Par conséquent, le traitement thermique de la FA de l’IN718 doit être personnalisé en fonction de l’historique spécifique du processus. La spécification standard ASTM F3055 recommande un traitement thermique pour la FA de fusion en lit de poudre de l’IN718 fabriqué.
Toutefois, cette norme ne fournit que des lignes directrices pour les traitements de détente et de pressage isostatique à chaud. La détermination du traitement thermique proprement dit doit faire l’objet d’un accord entre le fournisseur du composant et l’acheteur.
Applications de l’Inconel 718
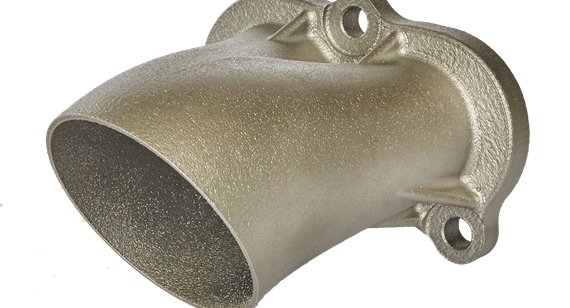
L’Inconel 718 convient parfaitement aux applications de chaleur extrême telles que le moulage de métaux sous pression.
Comme mentionné précédemment, l’IN718 est principalement utilisé comme matériau pour les disques de turbine. En raison de sa soudabilité efficace et de sa résistance à la chaleur, il est devenu un composant intégral des moteurs à turbine à gaz et des pièces de turboréacteurs telles que les carters de compresseurs, les disques et les aubes de soufflante.
Une étude récente de l’Université d’État de Pennsylvanie met en évidence la dégradation des extrémités des aubes de turbines dans l’aérospatiale d’aujourd’hui : « lorsque la dégradation dépasse un point défini, l’aube entière doit être mise hors service et remplacée par une nouvelle aube. Le matériau mis hors service est considéré comme un rebut et est jeté. Ce gaspillage a un impact financier important pour l’industrie aéronautique et constitue une nuisance dans la recherche d’une terre plus durable ».
La combinaison de la fabrication additive (FA) et de l’Inconel 718 pour la fabrication de ces aubes de turbine offrirait une solution possible à ce problème en permettant le remplacement ou la réparation progressive de la pièce usée ou cassée.
Le superalliage a également trouvé sa place dans la production de moteurs de fusée et dans l’industrie nucléaire.
Westinghouse Electric Company a installé un dispositif de branchement de dé à coudre imprimé en 3D dans la centrale nucléaire Byron Unit 1 d’Exelon. L’installation a été faite lors de leur arrêt de ravitaillement au printemps.
Westinghouse Electric Company fournit une large gamme de produits et de services pour les centrales nucléaires aux services publics du monde entier. Les produits et services de l’entreprise comprennent des conceptions avancées de centrales nucléaires, du combustible nucléaire, des services et de la maintenance ainsi que des systèmes d’instrumentation et de contrôle. Exelon, en revanche, est un fournisseur d’énergie basé aux États-Unis.
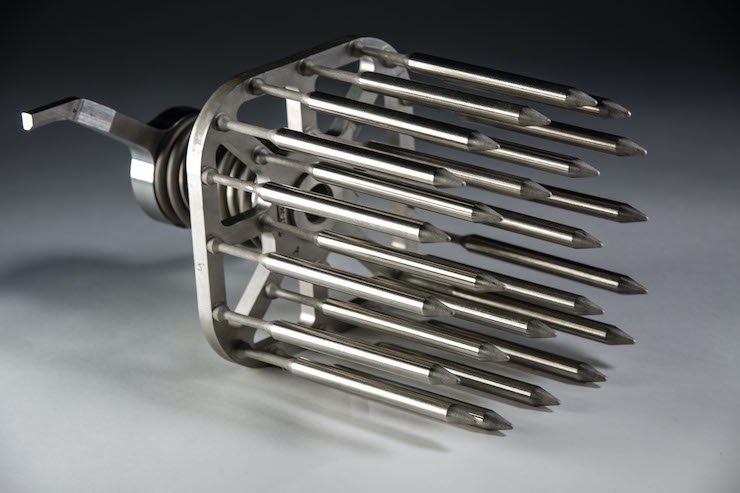
La collaboration entre les deux entreprises est le résultat de trois années de travail de développement. Selon nos collègues de Nuclear Engineering, lorsque Westinghouse s’est lancée dans cette mission, l’industrie nucléaire n’avait pas d’expérience directe des rayonnements avec les matériaux de la fabrication additive. Westinghouse a donc été l’un des premiers à faire ces premiers pas dans la production d’un composant imprimé en 3D destiné à un réacteur nucléaire commercial. L’entreprise a fait fabriquer des mini-échantillons de l’alliage d’acier inoxydable 316L et de l’alliage d’Inconel A718 conçus pour la FA dans le cadre de ces essais. Ces alliages étaient le matériau idéal pour le passage aux applications nucléaires.
Un système de lit de poudre laser a été mis à profit pour la production, car il permet de fusionner des couches de poudre de métal entre elles.
Au fil du temps, l’entreprise a conçu et fabriqué de manière additive d’autres composants du combustible, tels qu’un embout inférieur et une grille tubulaire avancée. Les conceptions tirent pleinement profit de la fabrication additive. Cela affecte également la liberté dont disposent les concepteurs de composants dans l’application des avantages du processus pour penser différemment. Cette technologie leur a permis de mieux aborder les problèmes de débit, de pression et autres liés aux performances du carburant grâce à des conceptions améliorées ; des problèmes en bref qu’ils n’ont pas été en mesure d’aborder en utilisant les méthodes de fabrication traditionnelles.
Ce dossier a été initialement publié dans le numéro de Septembre – Octobre de 3D ADEPT Mag.
N’oubliez pas que vous pouvez poster gratuitement les offres d’emploi de l’industrie de la FA sur 3D ADEPT Media ou rechercher un emploi via notre tableau d’offres d’emploi. N’hésitez pas à nous suivre sur nos réseaux sociaux et à vous inscrire à notre newsletter hebdomadaire : Facebook, Twitter, LinkedIn & Instagram !