Dans le cadre du projet BioStruct, la chaire de production additive numérique de l’université RWTH d’Aix-la-Chapelle (DAP) développe un processus de fabrication additive pour une nouvelle composition d’alliage de zinc-magnésium en combinaison avec des structures en treillis innovantes qui ne peuvent être produites qu’en utilisant la fusion de lit de poudre laser (LPBF). L’objectif du projet est de rechercher des implants qui peuvent être résorbés par le corps et qui sont adaptés aux besoins individuels du patient, favorisant ainsi un processus de guérison optimisé.
Les résultats du projet seront transférés à l’Alliance reACT, qui a déjà commencé ses recherches interdisciplinaires sur les implants du futur au second semestre 2022.
Les implants permanents en titane ou en acier chirurgical et les greffes osseuses autologues, qui sont des greffes réalisées à partir des os du patient, sont parmi les solutions les plus couramment utilisées pour traiter les défauts osseux. Cependant, elles ne peuvent répondre que partiellement aux exigences complexes d’un processus de guérison favorable au patient. Les propriétés mécaniques des implants permanents réduisent la pression exercée sur le tissu osseux environnant, ce qui l’affaiblit et augmente le risque de réfraction, et le tissu osseux lui-même ne guérit pas. En outre, la rétention prolongée des implants dans le corps augmente le risque d’une nouvelle intervention chirurgicale, en particulier dans une population vieillissante. Même si les greffes osseuses autologues favorisent l’auto-guérison du tissu osseux environnant et conduisent donc à des résultats optimaux, elles ne peuvent être utilisées que pour un certain volume de défauts. À ce jour, les défauts osseux dits de taille critique posent un problème médical complexe : en raison de l’importance du volume osseux manquant et de la distance entre les extrémités osseuses libres, l’os ne peut pas cicatriser de lui-même dans ces défauts. C’est pourquoi les partenaires du consortium BioStruct développent un concept d’implant biorésorbable dont les propriétés des matériaux et la conception géométrique répondent aux exigences complexes d’une cicatrisation osseuse favorable au patient. Le défi consiste à sélectionner des matériaux et des géométries appropriés et transformables, à la fois pour le corps et pour le traitement à l’aide de la technologie de fabrication additive LPBF (Laser Powder Bed Fusion), qui rend le concept réalisable en premier lieu.
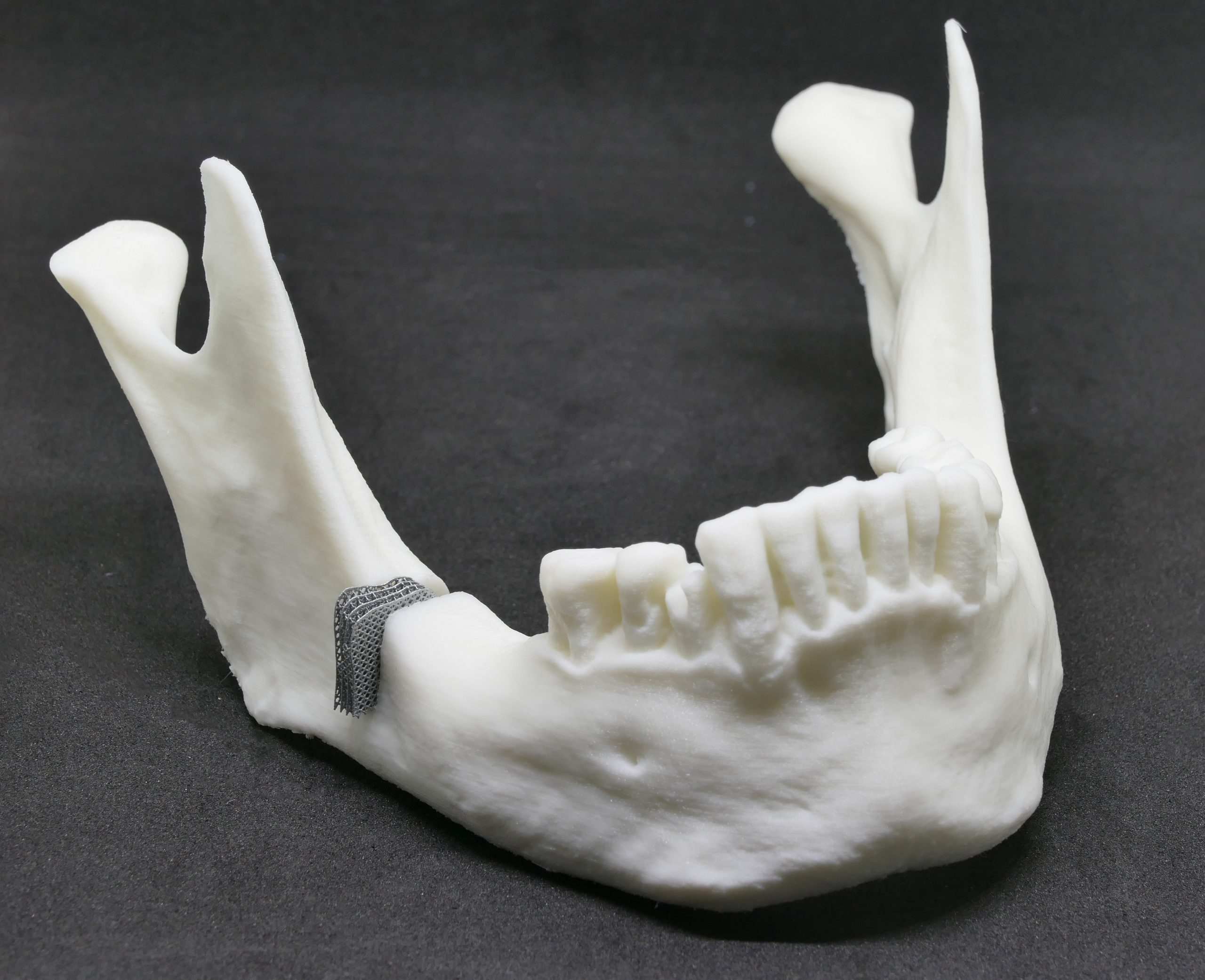
Modèle mandibulaire en PLA avec implant adapté aux défauts en ZnMg, fabriqué de manière additive sur la base du nouveau concept de conception et d’alliage.
Credit: RWTH DAP.
Zinc, magnésium ou les deux ?
Les alliages de zinc et de magnésium, en particulier, présentent des résultats prometteurs dans le domaine des implants osseux résorbables. Dans le contexte du développement d’alliages métalliques biorésorbables, le zinc pur (Zn) se caractérise par de bonnes propriétés de dégradation dans le corps humain. Cependant, sa résistance mécanique n’est pas suffisante pour être utilisée comme implant. Le magnésium (Mg), quant à lui, est déjà utilisé comme matériau pour la fabrication d’implants, notamment en chirurgie du pied, en raison de ses propriétés mécaniques proches de celles de l’os. Cependant, il se dégrade trop rapidement dans le corps dans des applications spéciales, et la formation de gaz peut se produire dans l’environnement humide du tissu. C’est pourquoi les chercheurs étudient différentes compositions d’alliages de ces métaux purs afin de combiner efficacement les propriétés de ces deux métaux pour une utilisation dans le corps et la possibilité de les traiter par LPBF.
Conception algorithmique d’implants spécifiques au patient
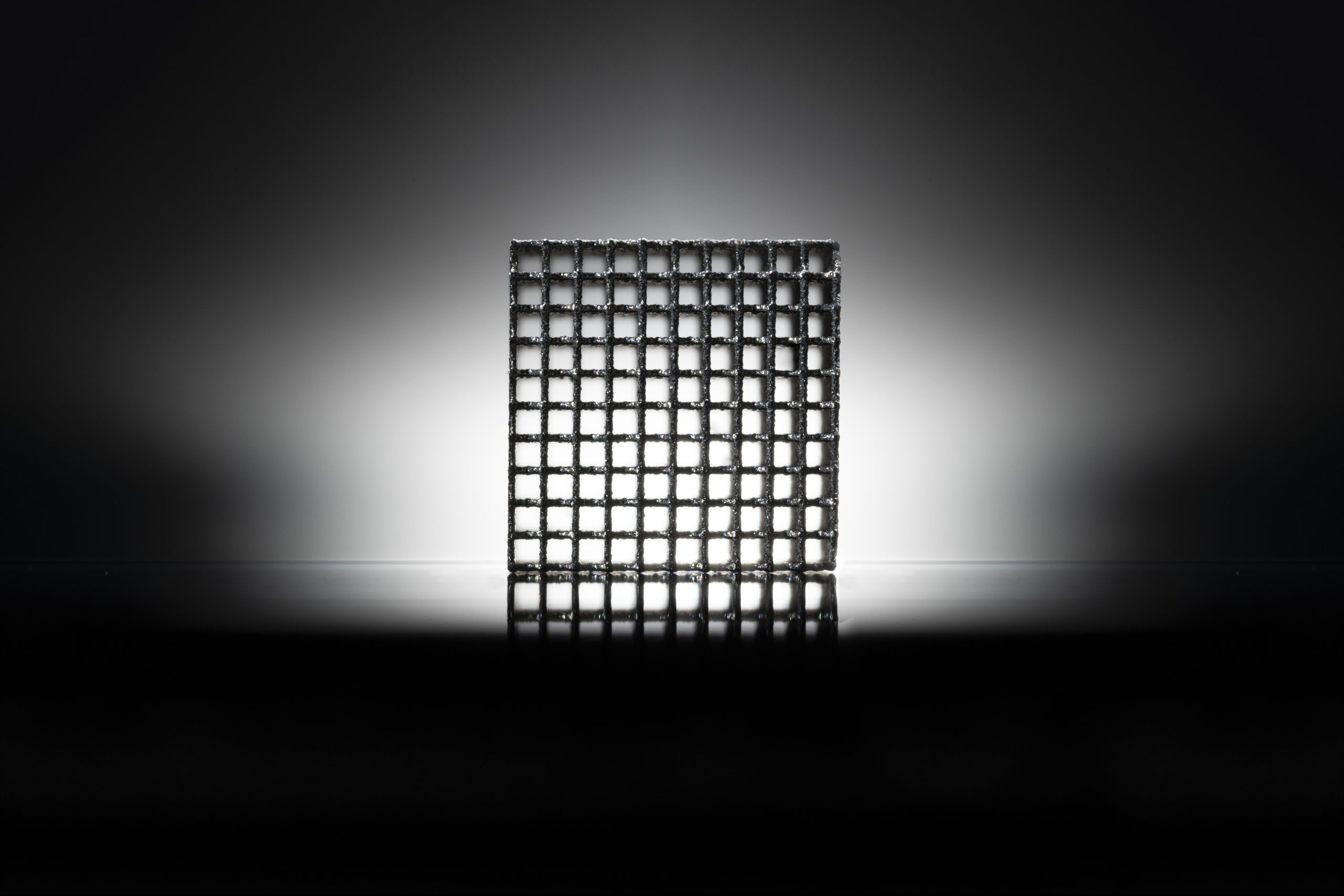
RWTH DAP / Irrmischer.
Le procédé LPBF offre des possibilités de conception entièrement nouvelles pour la conception d’implants afin de mieux répondre aux exigences spécifiques des patients, telles que les contraintes mécaniques et le comportement à la corrosion sur le site d’application. L’approche innovante réside dans la conception algorithmique d’une structure en treillis : Sur la base des exigences définies, la géométrie et la disposition des différents piliers ou des cellules du treillis sont générées de manière paramétrique, la structure du treillis qui en résulte est adaptée au site du défaut osseux et préparée pour la production à l’aide de la technologie LPBF. Le diamètre de l’entretoise est un paramètre important dans ce contexte. Les ajustements apportés à la conception de la structure en treillis permettent une corrosion uniforme sur l’ensemble du composant, ainsi que l’évacuation des produits de dégradation et la croissance simultanée des tissus au fur et à mesure que l’implant est absorbé par l’organisme.
Première production de démonstrateurs réussie
Dans le cadre de leurs recherches, les scientifiques sont parvenus à affiner le grain et à ajuster la microstructure de manière ciblée en ajoutant de petites quantités de magnésium au zinc. Lors d’une vaste sélection d’alliages de différentes compositions, allant du zinc pur à un alliage Zn8Mg, l’alliage ZnMg avec ≤ 1 wt-% de magnésium a montré les meilleures propriétés pour une utilisation en tant que produit de remplacement osseux. Un premier démonstrateur sous la forme d’un implant de mâchoire à structure en treillis a été fabriqué avec succès et de manière reproductible à partir de cet alliage ZnMg. Le diamètre de l’entretoise de la structure en treillis utilisée dans le démonstrateur est de 200 μm. Des structures supplémentaires ont été fabriquées par le procédé LPBF pour étudier la biocompatibilité du ZnMg. À l’avenir, ces structures sont destinées à former un cadre stable pour l’infiltration de matériaux tels que le collagène ou la fibroïne, permettant une croissance osseuse dirigée.
N’oubliez pas que vous pouvez poster gratuitement les offres d’emploi de l’industrie de la FA sur 3D ADEPT Media ou rechercher un emploi via notre tableau d’offres d’emploi. N’hésitez pas à nous suivre sur nos réseaux sociaux et à vous inscrire à notre newsletter hebdomadaire : Facebook, Twitter, LinkedIn & Instagram !