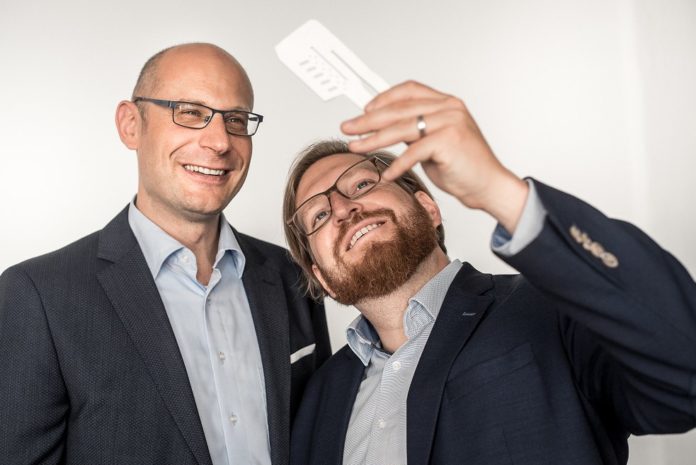
I’ve spent enough years in this industry to know that if a company develops a quality product, you’ll find out eventually without asking or looking for it. That’s how I knew Lithoz was developing and commercializing a reliable technology. In March 2019, at the last trade fair I attended before the pandemic hit and shut down everything, I had a very informal conversation with other attendees who discussed the good and the bad of AM. From one argument to another, Lithoz’ technology was quickly mentioned as one of the most advanced solutions of the market for high-performance ceramics. I immediately checked that my interlocutor was not one of the company representatives trying to indirectly encourage me to write an article about them – (job conditioning!). He was not. He was a real user and enthusiast who had explored various AM processes. Therefore, I kept this conversation in mind and decided to see how things turn out myself. And I believe time has proven him right because if you celebrate ten years of activity on such a niche market, you’ve certainly come a long way; most importantly, you have got something worth exploring for industries.
To find out what that “thing” is, I have asked Lithoz’ CEO & co-founder, Dr Johannes Homa to kick-off this new season of our Opinion of the Week series.
How Lithoz’ journey started…
The whole story started at the Vienna University of Technology. Homa and his co-founder, Dr. Johannes Benedikt, current CTO of Lithoz, developed Lithoz’ proprietary technology in 2006. In 2010, when they realized they were able to 3D print ceramics with the same material properties as in conventional forming technology, they decided to become a standalone company. 2011 therefore saw the creation of Lithoz as a spin-off from the TU Vienna.
Over time, the company has developed a comprehensive range of solutions (machines, software and materials) for 3D printing high-performance ceramics. On the other hand, the team also supports industries in applications development. At the heart of this expertise lies the company’s proprietary lithography-based ceramic manufacturing process. A fabrication process where ceramic particles are dispersed in a photosensitive resin and this dispersion is thereafter solidified by light layer-by-layer to form a part. Then the part undergoes a sintering process to develop its ceramic properties and can be used for its final purpose.
Lithoz’ technology has been validated in three main vertical industries: medical, aerospace & space, and energy. Needless to say, other sectors including luxury goods can leverage high-performance ceramics in production, but as I pointed out before, the lack of applications in ceramic 3D printing is often due to the lack of knowledge of the processes and their benefits. So far, the evolution of this niche market is often compared to the evolution of metals or plastics.
“When we started Lithoz, the AM market of plastics and metals was already more mature than ceramics. Nobody was really able to deliver the quality needed and expected in ceramics. However, we knew we were ready to enter the market when we successfully performed our proof of concept: delivering 3D printed ceramic parts with the same material properties than conventional forming technology. People were impressed by the parts they saw at that time. Obviously, as in any new technology, everything must be developed; expectations must be adapted and managed. It was essential for us to keep feet on the ground, despite the challenges we encountered”, the CEO told 3D ADEPT Media.
Furthermore, imagine how difficult the AM market was at the beginning; this difficulty increased tenfold for players who wanted to make ceramic 3D printing their core business, it was certainly worse for those who wanted to explore applications with this process. That’s the reason why it was essential for Lithoz “to be seen as a partner – and not only as a machine manufacturer”. “We are not really a marketing-driven company, and we are still an engineering-driven company. A decade later, we can see that this approach led us really fast towards industrial production”, Homa adds.
The current state of the ceramic 3D printing market
From a manufacturing standpoint, it’s pivotal to firstly understand the unique challenges that industrials can encounter when processing ceramics as compared to metals and polymers. To this concern, our expert reminds that ceramics are utilized in high-temperature environments, that are often subject to high chemical corrosion. The straightforward analysis is that engineers choose ceramics when other materials are not an option. The challenge here therefore remains to deliver the same or equal material properties as the conventionally formed while in plastic, for instance, which is often used for prototyping, the part does not necessarily need to have the exact same properties.
That being said, ceramic 3D printing is slowly but surely being adopted. One of the measuring elements for Homa and its team is the quality of leads they receive on industry events where they exhibit. “Until 2018, people were just amazed by the capabilities of the company’s technology, and the parts they saw on our booth”, the CEO explains. The understanding of professionals became much clearer over time and 2018 saw a wide range of collaborations for solid and clear projects.
Furthermore, serial production has always been the ultimate dream for industrials adopting AM. For few years now, AM companies have been saying: “we’ll get there”. Today, Lithoz can pride itself on being in the exhaustive list of players who can do it. “We can strongly affirm today that we achieve serial production because we’ve built up our capabilities based on user feedback. Thanks to our partnerships with our customers, we continuously focus on quality and therefore expand our area of expertise”, our guest outlines.
On another note, when assessing the state of a particular market, we tend to forget the people behind the main players driving it. Homa pays tribute to these people today as they are the key enablers of Lithoz’ growth.
“If we’ve reached the level we have today, we owe it to people who saw the potential of ceramic 3D printing rather than just a hype. We owe this success to young people who do not have so much experience of AM, which encourages them to think outside the box and outperform themselves – as compared to a ceramic engineer who will always think the way he has been taught to. Bear with me, this way of thinking is not bad, but it is not enough if you want to innovate. Lastly, we also owe this success to academics we closely work with. They are solutions-oriented which enables us to focus on and deliver quality, rather than focusing on a sales perspective”, Homa outlines.
How Lithoz’ journey is going
The company rang in the new year with the dispatch of the first shipment from its new second production site. As a reminder, the second semester of 2021 was marked by the opening of a production center in Austria whose planning and implementation focused on sustainability, scalability and reliability. It is the fourth location worldwide after the headquarters in Vienna and bases in America and China.
Moving forward, “we can expect a new 3D printer in addition to the LCM technology – which is just for small and precise parts. We will be busy keeping up the demand of customers. Industrialization will remain a top priority and we will continue developing our existing markets”, Homa concludes.
Lastly, we’ve spent the past few years describing ceramic 3D printing as a “relatively new” market. After this conversation with Lithoz’ CEO Dr Johannes Homa, I have no doubt that ceramic 3D printing is now a very strong market. Not (only) because of the decade Lithoz just celebrated, but because of where the company is heading to.
Remember, you can post job opportunities in the AM Industry on 3D ADEPT Media free of charge or look for a job via our job board. Make sure to follow us on our social networks and subscribe to our weekly newsletter : Facebook, Twitter, LinkedIn & Instagram ! If you want to be featured in the next issue of our digital magazine or if you hear a story that needs to be heard, make sure you send it to contact@3dadept.com