Copper 3D printed parts production gets a new lease of life as gas and engineering company Linde shows the capabilities of its ADDvance® Laser230 gas supply solution at Formnext 2023.
Featured last year at Formnext, the ADDvance® Laser230 gas supply solution optimizes copper 3D printing by addressing key issues at the manufacturing level of parts in highly regulated industries.
The company is also showcasing its powder atomization test laboratory facility and next-generation cold spraying gas supply solutions at the Frankfurt event.
The ADDvance® Laser230 gas supply solution
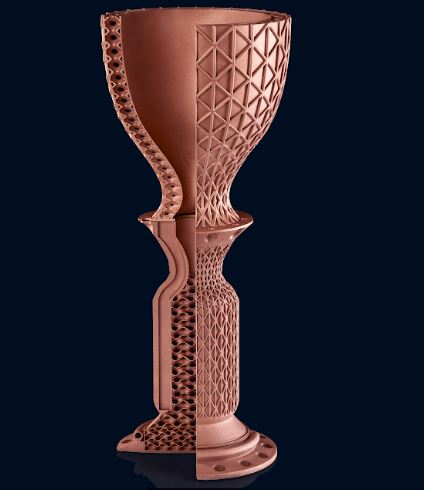
The ADDvance® Laser230 system developed by Linde uses a higher laser intensity which can’t be disrupted by the reflective property of copper, preventing the loss of power in the Additive Manufacturing process.
The new gas mixture has an oxygen control system called ADDvance® O2 precision developed in collaboration with Ariane which can make high-quality copper AM parts consistently. The two companies recently announced that they are working to improve 3D printing of copper for future space rockets.
At the heart of their collaboration lies the ADDvance Laser230 which has helped to optimize printing outcomes in the laser powder bed fusion (LPBF) process. With its blend of argon and helium, it helps mitigate fumes and spatter formation and accelerate cycle times, making the printing process more reliable and lowering the cost per part. It is alloy agnostic and ideal for additive manufacturing of complex or lattice-type structures.
The addition of ADDvance O2 precision in the printing process will ensure that a maximum oxygen level as low as 10 ppm will only remain in the print chamber. This extremely low residual oxygen level ensures that overheating and oxidation are mitigated, enabling more efficient printing, without the need to wait for layers to cool down. It also has the added benefit that non-oxidized powder can be reused, reducing material costs.
“To ensure the competitiveness of future launcher engines, improved additive manufacturing processes are a key factor, enabling reduced manufacturing costs and improved lead times while maintaining the non-negotiable quality and reliability that has made Ariane an industry leader,” said Mathias Palm, Process Specialist, Ariane Group. “We are confident that Linde’s gas expertise will contribute to optimising the additive manufacturing process.”
Hot Gas Atomization & Atomic test bench demonstration
The company also demonstrated its Hot Gases Atomization technology through a 3D object
which showed how the system works by injecting high pressure through the nozzles while producing metal powders. The process can be sped up to create finer powders if a gas heater increases the temperature to several hundred degrees, resulting in faster gas movement through the nozzle. This is often retrofitted with Linde gas supply solutions and control panels for better results.
Through the atomization test bench, Linde has achieved “real world” nozzle design and gas parameters which enhances the metal powder atomization as it has specially adapted windows, lighting, high-speed cameras and schlieren imaging (In case you do not know, chlieren photography is a visual process that is used to photograph the flow of fluids of varying density). This helps in better surveillance and data capture of each change of gas parameter as the test bench relies on the gas structure of the atomization, not molten metal. Within minutes hundreds of combinations of parameters like pressure, temperature, gas volume and type can be checked by the atomizer
Other systems displayed
The company is also highlighting LINSPRAY® Connect gas supply solution launched in March which enhances the safety of the cold spraying process because of high-quality gas flow with minimal variation. With this technology, the AM companies can monitor the parameters of the additive manufacturing process including the level of nitrogen tank, temperature and pressure.
Linde’s ADDvance® Sinter250 solution which optimizes sintering atmospheres to prevent oxidation in metal fused deposition modeling (FDM) is also highlighted at Formnext. This system ensures the structural integrity and strength of stainless steel 3D printed parts as it has advanced atmosphere control created from argon and hydrogen gas mixtures.
AM industry enthusiasts can visit booth C82 in Hall 11 where Linde is demonstrating its gas supply solutions.
Featured image credit: Linde. Remember, you can post job opportunities in the AM Industry on 3D ADEPT Media free of charge or look for a job via our job board. Make sure to follow us on our social networks and subscribe to our weekly newsletter : Facebook, Twitter, LinkedIn & Instagram ! If you want to be featured in the next issue of our digital magazine or if you hear a story that needs to be heard, make sure to send it to contact@3dadept.com