Des données du patient au dispositif prothétique final chez Quorum Prosthetics
À 12 ans, Joe Johnson a perdu sa jambe dans un accident de moto. Il a d’abord dû faire face à des difficultés avec une prothèse de base, jusqu’à ce qu’il découvre comment la FA pouvait l’aider à produire une prothèse sur mesure et plus confortable, imprimée en 3D. L’histoire de Johnson aurait pu s’arrêter après l’obtention de sa première prothèse, mais il ne voyait personne prêt à prendre des risques pour aider les amputés. Son parcours l’a donc conduit à fonder Quorum Prosthetics, une entreprise de prothèses qui fabrique des bras et des jambes prothétiques, des attelles sur mesure et les emboîtures réglables imprimées en 3D Quatro. Au fil du temps, l’entreprise n’a cessé d’explorer l’utilisation des technologies de fabrication numérique pour offrir aux amputés une prothèse adaptée à leurs besoins. Si nous en parlons aujourd’hui, c’est parce que l’expérience de Johnson nous a permis de comprendre les étapes de la fabrication numérique de dispositifs spécifiques aux patients imprimés en 3D.
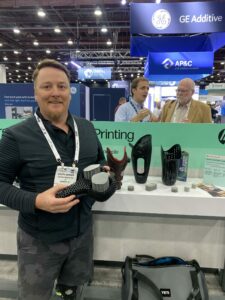
L’histoire de Quorum Prosthetics est en elle-même un parcours de résilience. Nous partageons son histoire aujourd’hui parce que « la fabrication additive est un véhicule pour [ses] idées », pour reprendre les termes de Johnson. Cependant, en 1998, lorsque l’entreprise a été fondée, ce n’était pas le cas. Il a fallu à Johnson beaucoup d’investissement, d’énergie et de confiance dans l’expertise en ingénierie pour amener son entreprise là où elle est aujourd’hui – oui, parce que Johnson n’est pas ingénieur de formation.
« Il y a huit ans, j’avais une idée de ce que je voulais que Quorum réalise. Nous voulions normaliser une bonne conception pour les prothèses, car il était difficile de reproduire soigneusement les prothèses existantes. [Des techniques de fabrication conventionnelles telles que la résine de stratification et le plâtre, nous avons franchi le pas vers la FA en 2019. Aujourd’hui, avec un modèle de fabrication distribuée, nous pouvons aider les amputés au-delà de nos frontières] », ajoute le fondateur.
D’un point de vue plus pratique, il est important de comprendre que retrouver la mobilité passe par une prothèse à la fois fonctionnelle et bien adaptée. Un processus de fabrication conventionnel nécessiterait l’utilisation d’un moulage en plâtre personnalisé pour le patient et une stratification à l’aide de carbone et de résine. « Le problème est que, même si l’emboîture finale est confortable, le processus de fabrication est imprécis pour la reproduction », a déclaré Johnson à 3D ADEPT Media. Sans compter que la forme et le volume peuvent changer avec le temps, provoquant une sorte de pression ou d’inconfort pour le porteur.
L’emboîture Quatro de Quorum Prosthetics est basée sur une conception brevetée qui permet aux porteurs d’adapter le volume et la compression à l’aide de bobines réglables et de cellules de confort interchangeables. La vérité est que le processus pour y parvenir exige un flux de travail numérique méticuleux et complet. Commentant le développement de tels dispositifs spécifiques au patient dans le domaine des prothèses et des orthèses, Johnson explique que chaque étape du flux de travail numérique est « impérative pour garantir la création d’emboîtures prothétiques, telles que l’emboîture Quatro, qui s’intègrent parfaitement à l’anatomie du patient, optimisent le confort et améliorent la fonctionnalité ».
Quelles sont ces étapes ?
D’un point de vue très technique, les étapes de la fabrication numérique peuvent être regroupées en 3 étapes principales :
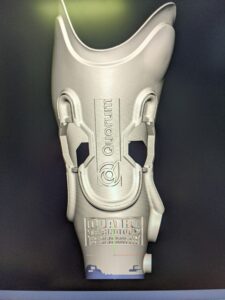
- Numérisation 3D et création d’un modèle numérique
- Impression et traitement
- Ajustement du patient
Chez Quorum Prosthetics, l’ensemble du processus de fabrication, de l’évaluation du patient à l’évaluation des résultats, se déroule en 10 étapes. Ces étapes sont les suivantes :
- L’évaluation du patient : Tout prestataire de soins de santé conviendra que cette étape est évidente car elle permet de mieux comprendre les besoins et les exigences spécifiques du patient et de recueillir des données médicales pertinentes telles que les mesures du membre résiduel, l’état de la peau et les capacités fonctionnelles.
- Numérisation 3D : Cette étape permet de saisir avec précision la forme et les contours du membre résiduel. En général, la tomographie informatisée (CT), l’imagerie par résonance magnétique (IRM), les rayons X et les scanners 3D portables peuvent être utilisés pour saisir les détails de l’anatomie du patient. Cette représentation numérique devient la base des étapes suivantes du processus de FA.
- Quorum utilise un scanner 3D Artec pour effectuer cette tâche.
- Création d’un modèle numérique : Le concepteur utilise ensuite un logiciel spécifique pour convertir les données du scanner 3D en un modèle numérique. Certains ajustements basés sur l’anatomie du patient peuvent également être effectués à ce stade.
- Conception de l’emboîture : Le niveau de sophistication du logiciel de conception est crucial à ce stade, car il détermine si le processus reste manuel ou s’il évolue vers une automatisation partielle ou complète. Cette phase de modélisation numérique permet une précision inégalée, garantissant que la prothèse finale se conforme parfaitement à l’anatomie individuelle et aux exigences du patient.
Avec l’aide de Geomagic Freeform, ils peuvent concevoir l’emboîture et intégrer des caractéristiques telles que des zones de soulagement de la pression, des mécanismes de suspension et des renforts. Johnson a expliqué qu’il détenait un brevet pour l’emboîture Quatro, qui répondait à des exigences précises en matière de conception, et que Freeform était la solution idéale pour répondre à ces exigences. Freeform permet essentiellement de créer des emboîtures sur mesure pour chaque patient, ce qui donne des formes uniques pour chacun d’entre eux. Cependant, la disposition standardisée des lignes d’ajustement et l’ensemble du système Quatro dans Freeform rationalisent le processus de conception, le rendant efficace et simple. Plus important encore, avec les méthodes conventionnelles, le développement d’un design d’emboîture de cette nature pourrait prendre jusqu’à 12 heures. Or, l’équipe de Quorum peut finaliser une conception en une fraction de ce temps, généralement en quatre à six heures.
-
Légende : Les ajustements peuvent être effectués avec une grande précision. Crédit : Quorum Prosthetics La préparation de la fabrication nécessite, par exemple, de confirmer que tous les modèles numériques se trouvent dans les limites du lit d’impression.
- Fabrication : Quorum s’appuie sur HP Multi-Jet Fusion pour fabriquer ses prises de courant. Tout autre procédé de FA pourrait être évalué pour s’assurer que la pièce finale est biocompatible et qu’elle offre la résistance et le poids idéaux. Cela dit, il existe des différences importantes au niveau de la géométrie lorsqu’on compare une emboîture fabriquée de manière traditionnelle et une emboîture fabriquée avec le procédé MJF. D’autres différences concernent les points de connexion et l’épaisseur (la fibre de carbone doit avoir une épaisseur uniforme de 6 mm en s’appuyant sur 4 couches de fibres tissées et 2 bases de résine).
- Contrôle de la qualité :Au-delà du respect des normes de qualité et des spécifications, il s’agit de garantir la précision et le confort de l’utilisateur. Il convient de noter qu’il n’existe pas de protocole d’essai officiel pour tester les performances des emboîtures. C’est pourquoi les prestataires de soins de santé s’appuient souvent sur diverses méthodologies d’essai. La norme ISO 10328:2016, par exemple, spécifie des procédures pour les essais de résistance statique et cyclique sur les prothèses de membres inférieurs.
Les charges composées dans l’échantillon d’essai se rapportent aux valeurs maximales des composantes de la charge qui se produisent normalement à différents moments pendant la phase d’appui de la marche.
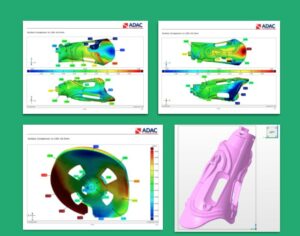
- Assemblage et personnalisation :Les exigences esthétiques et fonctionnelles doivent être satisfaites à ce niveau.
- Mise en place et réglage : Après avoir installé l’emboîture sur le membre résiduel du patient, il est encore possible de procéder à quelques ajustements. Si nécessaire, Quorum ajoute par exemple des cellules de confort dans les perforations de l’embout intérieur flexible afin de fournir au patient un coussin supplémentaire.
- Évaluation des résultats : tout au long du processus, l’équipe Quorum suit le patient pour évaluer les performances de l’appareil dans des scénarios réels.
Conclusion?
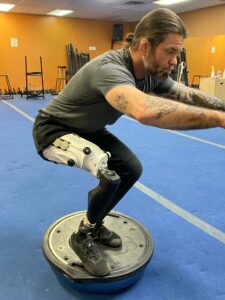
Si les prestataires de soins de santé peuvent être confrontés à des pénuries de main-d’œuvre et à des problèmes de capacité de production lorsqu’ils recourent à la FA, les avantages de l’utilisation de la technologie pour les prothèses imprimées en 3D sont ceux que vous connaissez déjà, si vous connaissez la technologie : personnalisation, amélioration du confort, réduction du temps de production et de la rentabilité.
D’ailleurs, en ce qui concerne le facteur coût, les emboîtures réglables de Quorum peuvent désormais être prises en charge par les compagnies d’assurance dans le cadre de l’ajustement du volume des prothèses.
Au fur et à mesure de son évolution, la FA continuera à remodeler le paysage des prothèses, en offrant une nouvelle accessibilité et en améliorant le bien-être général des personnes dans le besoin. Avec plus de 57,7 millions de personnes vivant avec une amputation de membre due à des causes traumatiques dans le monde, j’espère voir émerger davantage de « prothèses Quorum » à travers le monde.