Aperçu d’un test de dépoudrage avec une plaque de construction de pièces médicales imprimées en 3D
Une fois que vous avez décidé qu’une machine d’enlèvement de poudre automatisée est le bon appareil pour vos pièces (médicales) imprimées en 3D, l’étape suivante peut être assez stressante : prendre la bonne décision lorsqu’il s’agit d’acheter une machine qui garantira la sécurité de vos produits et de votre personnel, réduira le risque de défaillance des produits et, plus important encore, sera conforme aux normes de l’industrie. C’est la raison pour laquelle, dans un autre article, nous avons examiné les caractéristiques techniques indispensables d’un système automatisé d’élimination des poudres. Le fait est que plus le marché progresse, plus de nouvelles fonctionnalités sont développées et plus les exigences des clients deviennent complexes et rigoureuses. À ce stade, une expérience personnalisée résultant d’un test d’enlèvement de poudre peut contribuer à faire pencher la balance en faveur d’une machine ou d’une autre et à confirmer la certification pour une utilisation dans une industrie donnée ou pour une application donnée. Pour comprendre comment un tel test est réalisé, nous avons demandé à Solukon Maschinenbau GmbH quelque chose d’inhabituel : partager des informations sur un test d’enlèvement de poudre réalisé pour l’un de ses clients actifs dans les secteurs de la médecine et des soins de santé.
L’expertise principale de Solukon reste l’enlèvement de poudre automatisé pour la FA. Pour cet article, le test de dépoudrage a été réalisé sur le dernier système de la société – le SFM-AT350-E pour les pièces de taille moyenne jusqu’à 60 kg – en collaboration avec le Swiss m4m Center, un centre de transfert de technologie qui exploite la FA pour les industries médicales et dentaires. En tant que défenseur des technologies de FA, nous avons suivi le parcours de Swiss m4m dans le domaine de la FA depuis ses débuts.
Aperçu du tout nouveau SFM-AT350-E et des applications au cœur du test
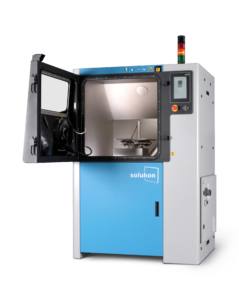
Conçue pour les pièces métalliques imprimées en 3D, la SFM-AT350-E est une version améliorée de la machine de dépoudrage automatisée SFM-AT350. Dévoilée l’année dernière lors du salon Formnext 2023, la nouvelle machine est dotée de trois améliorations clés : une compatibilité totale avec le logiciel intelligent d’enlèvement de poudre SPR-Pathfinder®, des fonctions améliorées de l’outil d’usine numérique ainsi qu’une excitation piézoélectrique.
Si le logiciel SPR-Pathfinder® et le Digital Factory Tool sont désormais des caractéristiques bien connues des systèmes d’enlèvement de poudre de Solukon et sont également disponibles pour la machine standard SFM-AT350, l’outil d’excitation piézoélectrique reste pour la plupart des utilisateurs une solution unique et spéciale sur le terrain.
Lors du lancement, Solukon a expliqué que l’excitation provient directement de la table rotative du système de dépoudrage automatisé, ce qui permet de déplacer la pièce dans la plage de vibration optimale avec une grande précision. Les hautes fréquences de l’excitation électronique sont considérablement plus élevées que la fréquence naturelle nocive de la pièce. Comme la fréquence se contrôle et se régule en permanence, le risque d’exciter la fréquence de résonance et d’endommager des structures sensibles est évité.
Le test a été réalisé avec plusieurs pièces médicales imprimées en 3D fournies par Swiss m4m : des cotyles de hanche, des cages vertébrales et des instruments médicaux.
« Les cotyles de hanche sont une application très typique. Les structures en treillis caractéristiques permettent la croissance des tissus. De même, les cages vertébrales permettent de rigidifier la colonne vertébrale en cas d’instabilité (hernie discale, par exemple). Les instruments médicaux sont utilisés comme prototypes pour les essais en salle humide. Leurs structures de support complexes avec de nombreux canaux longs et étroits sont les plus difficiles à dépoussiérer », explique Marco Flury, chef de projet chez Swiss m4M. Comme vous le verrez ci-dessous, Swiss m4M a fourni à Solukon différentes données sur ces pièces.
Globalement, le test a permis d’identifier les considérations spécifiques à prendre en compte pour ces applications ainsi que les spécifications clés liées à l’outil d’excitation piézoélectrique.
Le test d’enlèvement de poudre: 6 étapes clés
Selon Hemank Raj, ingénieur en développement de processus chez Solukon, le test d’enlèvement de poudre nécessite d’évaluer les données de la machine, les données des composants, le contrôle visuel avant le nettoyage, d’exécuter la procédure de nettoyage, d’évaluer les résultats du nettoyage et d’assurer un contrôle visuel après l’étape de nettoyage.
- En ce qui concerne les données machine, il est important de noter que l’alliage utilisé pendant le test n’est pas classé comme réactif. Le processus a été réalisé dans une atmosphère non inerte.
- En ce qui concerne les données relatives aux composants, Swiss m4m a partagé des informations relatives aux mesures des pièces (L x L x H), à la plaque de construction, à l’épaisseur de la plaque de construction, au poids (y compris la plaque de construction), à la configuration des trous et au matériau. Les chiffres se traduisent comme suit :
Mesures de la pièce |
|
|
Mesures de la plaque de construction | Plaque de construction ronde. Diamètre 204 mm. | |
Épaisseur de la plaque de construction | 23 mm | |
Poids y compris le poids de la plaque de construction | Approx. 13 kg | |
Schéma des trous de la plaque de construction | Plaque de construction TRUMPF TruPrint 2000. Pas de trous traversants. | |
Matériau | Acier inoxydable 17-4 PH |
- Le contrôle visuel a révélé qu’il n’y avait pas de dommage visuel, ni de morceaux de poudre sur la plaque de construction, ce qui signifie que le matériau peut résister à l’absorption d’humidité. Cependant, les structures des pièces semblaient entièrement remplies de poudre.
Pendant la phase de nettoyage, la plaque de construction a été montée sur le plateau rotatif à l’aide de quatre pinces.
Chaque partie de ce processus a été bien chronométrée et dure environ 17,5 minutes – depuis le chargement de la pièce, le nettoyage en mode automatique, le nettoyage de la pièce à l’aide d’un pistolet à air, la vérification des résultats du nettoyage jusqu’au déchargement de la pièce.
Pour ceux qui connaissent le processus de dépoussiérage basé sur l’excitation pneumatique, il est important de noter que les étapes de nettoyage sont similaires à celles d’un processus de dépoussiérage basé sur les ultrasons.
Raj a toutefois attiré notre attention sur un avantage essentiel : « Il n’est pas nécessaire de définir des paramètres d’excitation, car le système d’enlèvement de poudre définit automatiquement la meilleure excitation (= fréquence autorégulatrice). En outre, le processus s’est déroulé dans un volume maximal de 53,6 dB (pour référence : une conversation normale = 60 dB), ce qui est très silencieux. Le processus d’excitation ultrasonique s’accompagne d’une consommation minimale d’air comprimé ».
(Cela dit, en termes de caractéristiques technologiques, un processus de dépoussiérage basé sur l’excitation pneumatique est accompagné d’un cogneur à haute fréquence programmable pour dissoudre les amas de poudre et la technologie SPR intègre une combinaison de rotation et de vibration).
Comme expliqué ci-dessus, le test a confirmé que l’outil d’excitation piézoélectrique excite la pièce imprimée en 3D à une fréquence ultra-élevée. Selon Raj, cette accélération est énorme alors que l’amplitude est minime. En raison de l’accélération à cette fréquence, la poudre perd son adhérence et glisse de la surface.
L’équipe a réalisé que le SFM-AT350-E s’est avéré être le candidat idéal pour le dépoussiérage des structures délicates et fragiles. Sans oublier qu’avec « l’outil numérique de l’usine, nous avons accès à toutes les données de dépowdering pertinentes (par exemple, la température dans la chambre de la machine, l’humidité et tous les préréglages spécifiés par le client) – ce qui est crucial pour les industries sensibles aux données telles que MedTech », ajoute Raj.
- Après la phase de nettoyage, l’équipe a vérifié les résultats du nettoyage par contrôle visuel et en soufflant dans l’ouverture des pièces avec de l’air comprimé.
Non seulement ils n’ont trouvé aucun résidu de poudre dans les structures complexes, mais la poudre recouvrant la surface du composant a été enlevée par soufflage. Toutefois, pour éviter tout résidu de poudre mineur qui pourrait avoir été laissé à l’intérieur des structures complexes, ils recommandent de procéder à un nettoyage final (par ultrasons) avant d’utiliser la pièce imprimée en 3D ou avant l’étape suivante du processus de fabrication.
Au total, Flury de Swiss m4m a récupéré 977 grammes de poudre lors de ce test.
- Enfin, l’inspection visuelle n’a révélé aucun dommage ni aucun reste de poudre. Toutes les pièces étaient encore bien fixées à la plaque de substrat.
Conclusions
Tout d’abord, il est essentiel de garder à l’esprit que le temps et les chiffres décrits dans cet article ne concernent que le processus de dépoussiérage des pièces médicales imprimées en 3D réalisé dans le cadre de ce test. Cela signifie que les opérateurs doivent être attentifs aux données et aux spécifications de chaque pièce imprimée en 3D qu’ils devront dépoussiérer. En fin de compte, même si le SFM-AT350-E et son outil d’excitation piézoélectrique présentent des avantages avérés par rapport à l’enlèvement de poudre conventionnel avec excitation pneumatique, quelques nuances peuvent être observées pour les pièces imprimées en 3D produites dans d’autres industries ou pour d’autres applications médicales.
Comme le note Raj par exemple, « par rapport à l’excitation pneumatique avec une turbine ou un heurtoir, l’accélération et la fréquence sont plusieurs fois plus élevées et l’amplitude beaucoup plus faible. (C’est pourquoi on ne constate aucune vibration/mouvement du composant pendant l’excitation). La fréquence d’excitation se situe entre 30 kHz et 38 kHz. Cela signifie que nous sommes bien au-delà des fréquences naturelles des composants. Cela permet d’éviter les oscillations et les dommages à la fréquence de résonance ».
Entre sa capacité à assurer un processus d’enlèvement de poudre peu bruyant, son mode d’excitation autorégulé et sa consommation d’air comprimé minimisée, ce test révèle des atouts qui jouent en faveur de cette machine d’enlèvement de poudre automatisée dans le cadre de sa certification pour un environnement de production médical. Sans oublier que, même si le Digital-Factory-Tool et le logiciel SPR-Pathfinder® sont des outils optionnels, ils restent intéressants pour tirer le meilleur parti de cette machine. « Grâce à une technologie spécialement développée, nous avons pu mettre en place une rotation sans fin de la table tournante dans le SFM-AT350-E et ainsi permettre l’utilisation illimitée du logiciel SPR-Pathfinder », explique Andreas Hartmann, CEO/CTO chez Solukon.
Dans l’ensemble, « les résultats suggèrent que le processus fonctionne aussi bien avec les alliages de titane. La forme d’excitation du SFM-AT350-E est idéale pour ce type de composants sensibles. Le processus de nettoyage est très court et il est possible d’atteindre un taux de cycle très élevé, puisqu’un seul nettoyage est effectué en moins de 7,5 minutes. Si nous supposons que le chargement et le déchargement prennent ensemble 10 minutes, vous pouvez viser quatre nettoyages par heure avec un seul système d’enlèvement de poudre (étant donné qu’aucune atmosphère inerte n’est nécessaire et que le temps d’inertage et le temps de maintien de la porte doivent être pris en compte) », conclut M. Raj.
*Toutes les images : Avec l’aimable autorisation de Solukon.
Ce dossier a été initialement publié dans le numéro de mars – avril 2024 de 3D ADEPT MAG