Thermwood a mis en place une nouvelle méthode de fabrication qui associe son expérience en matière de routage CNC et ses travaux dans le domaine de la fabrication additive grand format. Baptisé Cut Layer Additive, le nouveau processus de fabrication n’imprime pas de pièces en 3D, mais reste un processus additif. Comment cela est-il possible ? Ken Susnjara, CEO de l’entreprise, nous explique le pourquoi et le comment de ce nouveau développement.
Thermwood, basée à Dale, dans l’Indiana, est l’une des premières entreprises à avoir développé des technologies de routeur CNC. Ces dernières années, l’entreprise s’est fait un nom dans le monde de la fabrication additive avec ses machines de fabrication additive à grande échelle.
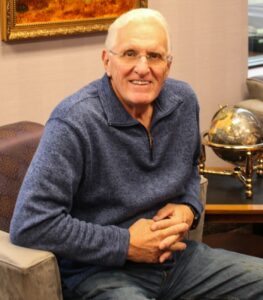
Comme vous le savez peut-être, l’impression 3D consiste généralement à extruder un matériau souple en plusieurs couches. « C’est ainsi que fonctionne le LSAM, mais pas le Cut Layer Additive, et il serait donc déroutant de les appeler tous les deux « pièces imprimées en 3D » », explique Susnjara. « Par conséquent, le procédé ‘Cut Layer Additive’ n’imprime pas, il découpe des pièces. Il s’agit toujours d’un processus additif puisqu’il fabrique des pièces en ajoutant des couches, mais il ne s’agit pas d’un processus d' »impression » au sens habituel du terme », ajoute-t-il.
Ces premières différences entre une imprimante 3D LSAM et une machine Cut Layer Additive pourraient facilement inciter un utilisateur à penser que la machine Cut Layer Additive a été créée pour résoudre des problèmes que la LSAM ne pouvait pas résoudre. Je suis moi-même tombé dans ce piège jusqu’à ce que Susnjara mette l’accent sur la raison pour laquelle ce processus a été créé :
D’abord et avant tout, « ce processus visait à créer quelque chose de nouveau » : donner aux utilisateurs la possibilité de produire des pièces avec les avantages du processus additif en utilisant des matériaux que l’on ne peut pas imprimer.
« L’une des façons d’y parvenir est de fabriquer une pièce en laminant des couches de matériaux découpés dans des feuilles. Nous avons décidé d’essayer de faire cela, mais aussi de faire en sorte que le produit final ait une structure similaire à celle des pièces imprimées grand format que nos clients fabriquent actuellement et qui connaissent un grand succès. Cela signifie que les pièces qui composent chaque couche, bien qu’épaisses, ne seraient pas très larges, avec des parois, tout comme les couches imprimées.
Cela signifie qu’elles peuvent être emboîtées sur des feuilles et découpées sur une défonceuse à commande numérique. Le seul problème, c’est que la programmation de toutes ces pièces serait un cauchemar. Nous avons donc mis au point une approche unique qui consiste à ne pas nécessairement programmer, mais à définir la pièce que l’on veut et à l’envoyer à une machine intelligente qui la programme pour nous. Les procédés LSAM et Cut Layer Additive sont des processus différents qui utilisent des types de matériaux différents pour produire des pièces destinées à des applications différentes. Les deux fonctionnent bien, ils produisent simplement des pièces à partir de matériaux différents », explique le CEO.
Un regard plus approfondi le procédé Cut Layer Additive : comment cela fonctionne-t-il ?
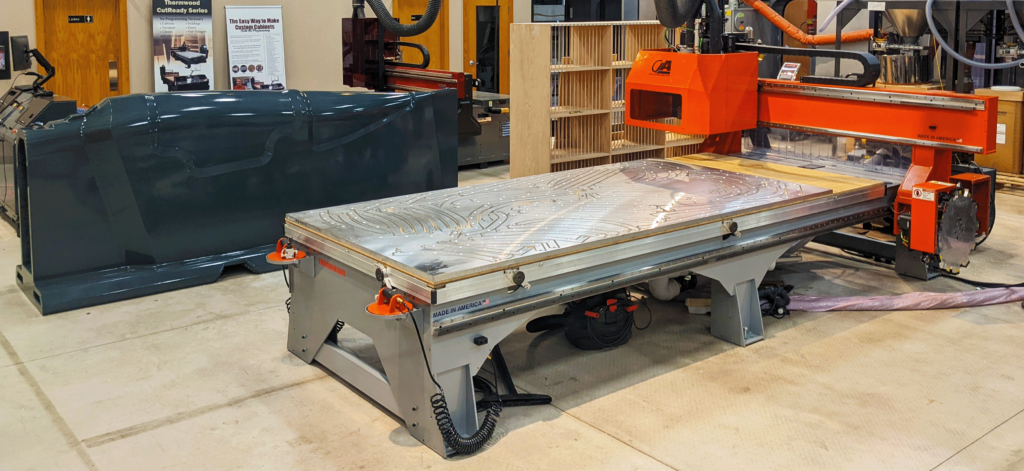
La machine découpe chaque couche de la pièce, en séparant les couches en différents segments afin d’optimiser l’imbrication sur la feuille dans laquelle les pièces sont découpées. Les segments sont ensuite assemblés à l’aide de joints puzzle pour former chaque couche de la pièce, qui est généralement assemblée à la main, couche par couche, à l’aide de trous d’alignement pour un assemblage plus rapide.
Thermwood affirme que ce processus peut être réalisé avec presque tous les matériaux pouvant être usinés par CNC, y compris les métaux et les matériaux poreux qui peuvent être traités avec de la résine pour obtenir une pièce en composite thermodurcissable.
Dans l’une des premières vidéos publiées sur Cut Layer Additive, le chef de produit Jody Wilmes explique que le système peut accélérer la fabrication en commandant la découpe pour permettre aux utilisateurs de commencer l’assemblage pendant que le reste de la fabrication s’imprime, s’il nécessite plusieurs feuilles.
Cependant, « la vitesse de fabrication dépend du matériau traité », souligne Susnjara. « Sur un gros outil aérospatial qui a été à la fois imprimé à l’aide de LSAM et fabriqué à l’aide du procédé Cut Layer Additive, le procédé Cut Layer a été plus rapide de plusieurs heures pour créer la pièce de forme presque nette, mais il y avait des opérations de post-traitement nécessaires, pour en faire une pièce composite thermodurcie, ce qui rend les deux processus assez similaires. En règle générale, si vous traitez des matériaux qui se coupent facilement, tels que le contreplaqué, le MDF, les feuilles de mousse ou autres, le procédé Cut Layer Additive sera nettement plus rapide, même si vous ajoutez le temps d’assemblage. Si vous traitez de l’aluminium, ce sera plus lent, mais toujours plus rapide que n’importe quelle autre méthode de fabrication de la même pièce en aluminium », poursuit-il.
Comparé au LSAM, le procédé Cut Additive Layer prendrait le même temps et la même main d’œuvre que l’impression additive de la même pièce, et il peut même être plus rapide avec certains matériaux.
De plus, l’ensemble du processus est rendu possible par un logiciel de programmation, qui permet aux utilisateurs d’éviter les heures de travail nécessaires à la programmation des spécifications CNC pour chaque segment de chaque couche de la construction.
Cela signifie que les utilisateurs n’ont qu’à fournir à la machine un fichier CAO de la forme de la pièce et des détails sur sa fabrication, notamment le matériau utilisé et l’épaisseur de la paroi. Dans une interview accordée à 3D ADEPT Media, Susnjara souligne également que les capacités de cette solution logicielle constituent l’un des principaux atouts du progiciel de fabrication :
« Le logiciel et le traitement des pièces sont en fait la clé du processus. Il s’agit non seulement d’une solution très avancée, mais aussi d’une approche fondamentalement différente. Au lieu d’essayer de programmer tous les éléments qui composent la pièce, nous disons simplement à la machine ce que nous voulons et elle le fait. Cela se fait essentiellement en deux étapes. Tout d’abord, vous lui montrez la forme. Pour ce faire, vous lui envoyez un fichier CAO de la forme de base que vous souhaitez. Ensuite, vous lui indiquez comment vous voulez qu’elle soit fabriquée. Pour ce faire, vous devez répondre à des questions telles que les dimensions du matériau que vous souhaitez utiliser et l’épaisseur des parois que vous souhaitez. Le type de joint que vous souhaitez entre les segments de la couche, etc. La machine découpe ensuite la pièce, crée les segments de couche individuels, les emboîte sur votre matériau, crée le programme et découpe le tout. Le processus est rapide et prend souvent quelques minutes au lieu d’heures ou de jours. Cette capacité s’étend à la fabrication de pièces dont je ne suis pas sûr qu’elles puissent être fabriquées d’une autre manière. Nous publierons bientôt des informations à ce sujet. »
Alors, applications de prototypage ou de production ?
Une solution de fabrication qui peut aider à créer une pièce additive à partir d’un modèle CAO, découper la pièce en couches, diviser chaque couche en segments, ajouter une géométrie de connexion entre les segments, des décalages pour les découpes, des décalages de joints entre les couches, ajouter des trous d’alignement pour les chevilles, imbriquer efficacement toutes les pièces sur votre feuille de matériau et créer un programme CNC multi-outils – tout cela ressemble automatiquement à un rêve devenu réalité, mais pour quel objectif final : prototypage ou applications de production ? En fin de compte, la réponse à cette question est ce que les OEM recherchent.
Image : Drone produit par CLA. Avec l’aimable autorisation de Thermwood
« Des pièces grand format à forme nette », répond le CEO. « Ces pièces peuvent être utilisées comme n’importe quelle pièce additive de grand format. Le processus additif est normalement utilisé pour produire un seul exemple, un outil de production, un modèle initial ou un prototype, par exemple. Il permet normalement de produire une nouvelle conception plus rapidement et à moindre coût que toute autre méthode de fabrication. Si une pièce doit être produite en volume, il est normalement préférable de construire un outillage de production et de l’utiliser pour fabriquer des pièces.
L’obtention de pièces grand format de forme presque nette qui ne sont pas imprimées en 3D est le résultat de la combinaison de plusieurs compétences : leur CNC et leurs approches additives d’une part, et d’autre part, leur CNC et leur « intelligence de la machine », sur laquelle ils travaillent depuis près d’une dizaine d’années.
Interrogé sur les facteurs clés qui inciteraient un client à opter pour le nouveau produit Cut Layer Additive plutôt que pour la gamme LSAM de Thermwood, Ken Susnjara répond : « Si vous voulez fabriquer des pièces de grand format en matériau composite thermoplastique, le LSAM est le choix logique. Il fonctionne très bien pour cette application en utilisant ce type de matériau. Si vous souhaitez fabriquer des pièces à partir d’autres matériaux, tels que le bois ou l’aluminium, que vous ne pouvez pas imprimer, vous avez besoin de la technologie Cut Layer Additive ».
Cela dit, même s’il n’a pas de réelle limitation en termes de volume de construction pour la technologie Cut Layer Additive – puisque chaque couche peut être décomposée en un certain nombre de segments à placer sur la table de découpe -, il convient de noter qu’une fois que la pièce de forme presque nette est assemblée, l’opérateur aura besoin d’une machine à cinq axes pour la découper jusqu’à la surface finale. Cette machine doit être suffisamment grande pour accueillir la pièce assemblée.
Le nouveau produit est disponible dès maintenant, partout dans le monde où Thermwood est présent. Thermwood est convaincu que l’application de cette idée simple à une technologie de pointe peut avoir un impact profond sur le monde de la fabrication à grande échelle, en permettant aux producteurs de concevoir de nouveaux modèles plus rapidement et à moindre coût.
Co-écrit par Kety Sindze et Cameron Constanzo.