Vous souvenez-vous quand nous vous disions que le véritable succès d’une application dépendait généralement d’un élément sous-estimé : le matériau ? Eh bien, plus la fabrication additive progresse, plus nous réalisons que l’éventail des possibilités offertes par les matériaux reste à découvrir. Dans ce cas précis, je pense aux possibilités qui associent nécessairement des méthodes de conception novatrices et la FA pour garantir que des fonctionnalités optimales et des comportements ciblés sont intégrés dans une nouvelle gamme de matériaux spécialisés. Alors que beaucoup de choses se font au niveau de la recherche, une startup suisse donne de l’espoir pour la commercialisation future des métamatériaux.
Pour être honnête, la première fois que j’ai entendu parler des métamatériaux, également connus sous le nom de matériaux en treillis, j’ai pensé qu’ils étaient trop beaux pour être vrais. Même s’il y a encore une certaine controverse sur leur définition exacte, les scientifiques semblent s’accorder sur le fait qu’il s’agit de matériaux cellulaires architecturés qui peuvent être inspirés par la nature ou par l’intuition de l’ingénierie humaine et qui subissent des modifications afin de posséder des propriétés qu’ils n’ont pas naturellement.
Si le concept de métamatériaux a été introduit pour la première fois en 1967 par Victor Vesalago, il convient de noter que leur capacité à se généraliser pourrait largement dépendre de l’adoption croissante de la FA dans tous les secteurs et des considérations de coût de la technologie qui les rendra possibles.
La FA étant plus mature aujourd’hui qu’il y a dix ans, il est temps d’attirer l’attention de l’industrie sur ce qui pourrait être le prochain matériau à l’origine du développement de nouvelles applications.
À l’intersection de la conception de logiciels et du développement de matériaux
Le développement des métamatériaux devrait logiquement faire appel à tant de compétences interdisciplinaires qu’il pourrait être difficile de définir les personnes à l’origine de leur création comme des producteurs de matériaux exclusifs. Après une conversation avec Daniel Bachmann, directeur de l’innovation de la startup suisse Spherene Ltd, je suis tentée de définir les développeurs de métamatériaux comme des organisations/entreprises à l’intersection de la conception de logiciels et du développement de matériaux.
Bachmann explique qu’en 2018, en travaillant sur une recherche, l’équipe de Spherene a exploré le développement d’une nouvelle classe de surface minimale qui l’a conduite à la création d’un algorithme spécifique. Basé sur une API basée sur le cloud, cet algorithme peut remplir un volume de conception avec une surface minimale à densité adaptative (en anglais Adaptive Density Minimal Surface « ADMS »), qui suit des surfaces sphériques inversées pour créer un cadre solide mais ouvert au sein d’un objet donné. En d’autres termes, ils développent des treillis à l’aide d’un algorithme basé sur une surface minimale qui permet de créer des formes précises avec une géométrie optimale.
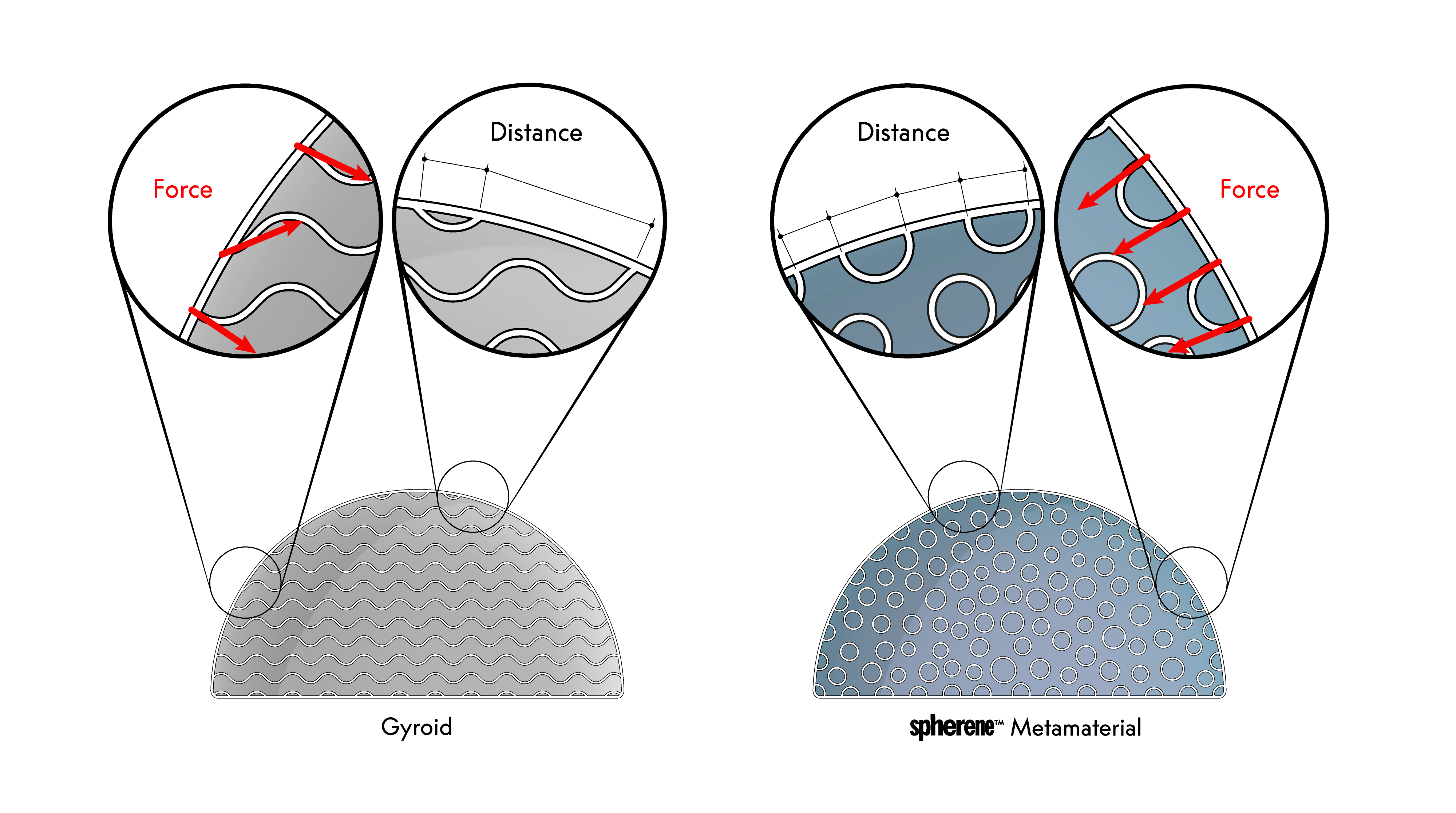
L’un des points forts de Spherene réside probablement dans la répartition des forces dans la zone souhaitée. Selon Bachmann, alors qu’une sphère peut répartir les forces autour d’un volume vide, une « spherene » permet de répartir les forces à l’intérieur de manière idéale.
« Notre technologie nous permet d’appliquer des forces dans n’importe quelle direction de la sphère. Ces capacités isotropes et de conformation de la surface permettent, par exemple, de rendre une pièce d’acier aussi légère que de l’aluminium et d’économiser beaucoup d’énergie pour produire le matériau final », explique Bachmann.
La solution de Spherene permet de développer des métamatériaux à base de plastiques (filaments), de métaux ou même de résines. Malgré cette variété de matériaux, le directeur de l’innovation confirme que la solution est la plus avancée pour produire des pièces dans des matériaux à base de poudre. « Peu importe qu’il s’agisse de plastique ou de métal. La résine arrive en 2ème position alors que le procédé FDM peut prendre plus de temps pour imprimer de nouveaux matériaux développés avec notre technologie », ajoute-t-il.
À ce jour, Spherene octroie des licences pour sa solution logicielle afin que les organisations puissent créer la forme dont elles ont besoin pour chaque matériau. Elle fournit également le service nécessaire pour le faire si le client ne le souhaite pas.
Si la solution de Spherene est déjà prête à toucher un public plus large, une autre approche mérite d’être mentionnée : la méthode de conception basée sur l’IA développée par Rayne Zheng, professeur associé de science et d’ingénierie des matériaux à Berkeley Engineering, et son équipe d’ingénieurs.
Zheng et son équipe ont utilisé l’apprentissage automatique pour concevoir inversement les comportements mécaniques complexes d’un matériau et d’un produit d’ingénierie qui peuvent être imprimés par une imprimante 3D de bureau.
« Avec notre méthode, un utilisateur peut saisir le comportement mécanique souhaité, décrit par une courbe, et ces données sont ensuite introduites dans le code d’apprentissage automatique pour générer une conception – un processus qui ne prend que quelques secondes. Et une fois que cette conception est imprimée en 3D, elle reproduit le comportement mécanique souhaité », a déclaré M. Zheng. « Même si elle en est encore à ses débuts, notre méthode de conception basée sur l’apprentissage automatique peut produire presque n’importe quel type de comportement des matériaux avec une précision de près de 90 %. »
Pour créer leur approche de conception basée sur l’IA, les chercheurs ont d’abord dû développer et mettre en œuvre un cadre intégré d’apprentissage automatique, qui se compose d’un module de prédiction inverse et d’un module de validation directe.
« Le module inverse utilise les comportements mécaniques souhaités pour concevoir la micro-structure du matériau, et le matériau conçu est transmis au module de validation pour l’évaluation de ses comportements mécaniques », explique Chansoo Ha, co-auteur principal de cette étude et ancien chercheur postdoctoral à Virginia Tech dans le laboratoire de Zheng.« Cela permet de s’assurer que les propriétés souhaitées se reflètent avec précision dans le produit fini ».
Ensuite, ils ont développé une famille de cellules à symétrie cubique, basées sur des piliers, pour entraîner le modèle d’apprentissage automatique. La structure en treillis des cellules permet d’obtenir presque n’importe quel comportement mécanique et la courbe contrainte-déformation correspondante. Les chercheurs ont ensuite imprimé les cellules en 3D et les ont testées pour générer des ensembles de données d’apprentissage.
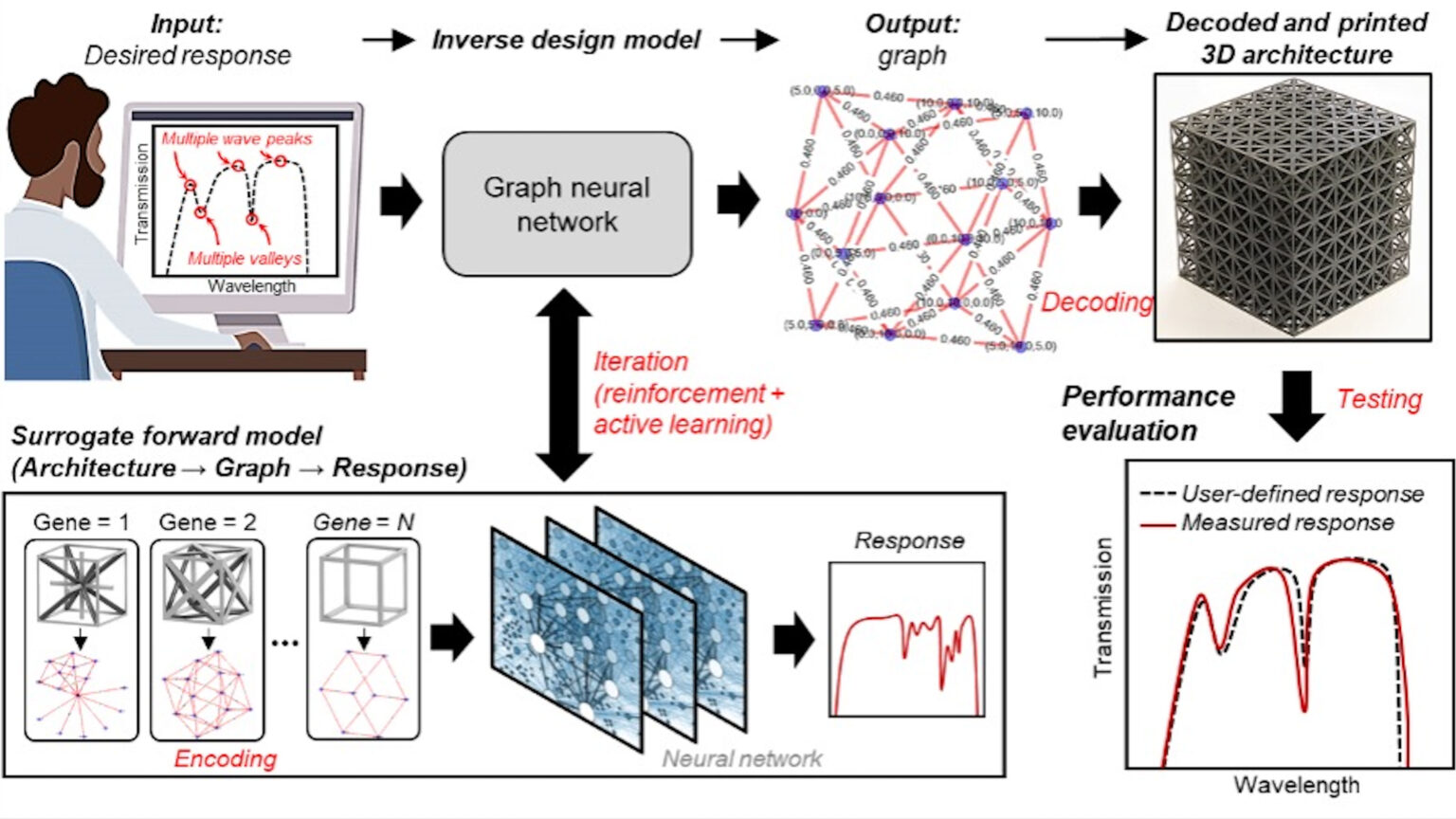
Quelles sont les considérations à prendre en compte pour développer des métamatériaux ?
Comme pour toute nouvelle technologie, l’utilisation de l’API Spherene nécessitera une courbe d’apprentissage. D’abord et avant tout, puisque « notre technologie est relativement nouvelle sur le marché. Il est crucial pour l’ingénieur d’opérer un passage de l’ingénierie traditionnelle à l’ingénierie moderne », explique le directeur de l’innovation. Le même argument a été avancé à plusieurs reprises lorsque la technologie de FA n’était pas assez mature. L’exploration du développement des métamatériaux nécessite un changement d’état d’esprit.
Deuxièmement, il est important de prendre en compte le flux de travail existant. L’utilisation de l’API Spherene permet d’adapter facilement le flux de travail et d’insérer toutes les variables pour le tester sur une imprimante 3D.
Troisièmement, le coût est un facteur qui pourrait faire pencher la balance. Tout en prévoyant que les organisations pourraient trouver le coût de la licence assez élevé (ce qui est logique compte tenu de la nouveauté de la solution), Bachmann aimerait exhorter les industriels à garder à l’esprit les avantages dont ils peuvent bénéficier :
- Gains de temps et de matériaux : les nouveaux designs créés avec les structures exactes permettent de créer des matériaux qui sont rapidement traités par les imprimantes 3D, ce qui se traduit par des gains de temps. Prenant l’exemple d’une application satellite, Bachmann explique qu’en 5 minutes, ils ont pu économiser 20 heures de travail d’ingénierie ;
- Une méthode autoportante qui permet d’imprimer sans support ;
- Allègement : le métamatériau sphérique peut éliminer les matériaux en vrac quelle que soit leur densité, réduisant ainsi le poids du composant ;
- Personnalisation au niveau de la conception : la géométrie des sphères peut être positionnée à côté de sections solides pour sceller des zones spécifiques, incorporer des trous de vis ou former des vides intérieurs. Les gradients peuvent également être utilisés pour réduire l’utilisation de matériaux, ajuster le centre de gravité ou gérer l’élasticité.
Applications des métamatériaux
Les chercheurs ont exploré le potentiel des métamatériaux dans les domaines de l’électronique, des communications et de la défense. Parmi le large éventail d’applications susceptibles de valider les capacités de sa technologie, Spherene Ltd. compte un support de satellite de l’ESA, un guide d’ondes pour un satellite de communication et un implant biocéramique testé pour la croissance osseuse. Elle travaille actuellement à tester les capacités de sa technologie sur des chaussures pour diabétiques.
De plus amples informations sur l’implant sont disponibles ici.
Ce dossier a été initialement publié dans le numéro de mars – avril 2024 de 3D ADEPT MAG