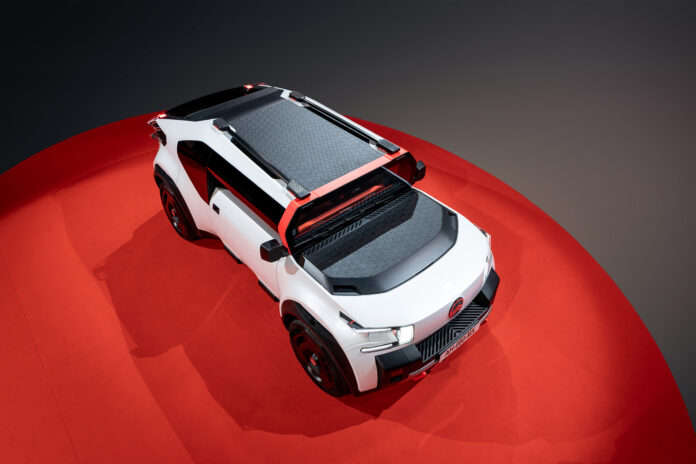
Dans le but de démontrer combien il est possible d’économiser en réduisant le poids et l’utilisation des ressources, la marque automobile Citroën a travaillé au développement d’un concept-car électrique en collaboration avec le producteur de matériaux BASF et le fournisseur de services d’impression 3D Sculpteo.
Baptisé oli, le nouveau véhicule a une vitesse limitée à 110 km/h (68 mph) et bénéficie d’une plus grande autonomie et d’une durée de vie de la batterie nettement améliorée. Comme la plupart des conducteurs disposent d’un téléphone portable et d’une enceinte portable, qui peuvent être branchés sur le tableau de bord et automatiquement connectés au véhicule, l’équipe de fabrication a décidé de ne pas équiper le véhicule d’un système de sonorisation ou de navigation.
Une approche de fabrication moins complexe, plus durable et au design attrayant
L’approche minimaliste a ouvert la voie à un design rafraîchissant et innovant. Divers composants ont été radicalement réinterprétés et construits en utilisant des matériaux dans un contexte différent. Par exemple, le dossier complet est fabriqué dans un matériau plastique flexible imprimé en 3D (Ultrasint® TPU88A). La structure en treillis ouverte permet une circulation naturelle de l’air, remplaçant ainsi tous les ventilateurs du siège.
En plus de son expertise en matière de produits et d’ingénierie, BASF a également pu apporter son expertise en matière de design par le biais du centre de création. « C‘est ici que le projet est né« , a déclaré Alex Horisberger, responsable du design industriel chez BASF. « Lors d’une visite au studio de création de Citroën, nous avons pu convaincre leurs designers avec nos analyses des matériaux et des tendances. Travailler au même niveau avec les designers intérieurs et extérieurs de Citroën a été un moment fort pour moi. »
Sculpteo a pris en charge la production de ces pièces ainsi que la production d’une vingtaine de pièces dans son usine basée en France.
Autre fait marquant, nombre de ces nouveaux composants sont conçus et fabriqués à partir de matériaux issus de la même famille de produits chimiques. Les composants collés et soudés à partir de matériaux différents constituent un défi dans le domaine du recyclage mécanique. C’est pourquoi les concepteurs ont créé autant de composants que possible à partir d’un seul matériau.
Ce principe de simplicité a également été mis en œuvre lors de la production. Les portes du conducteur et du passager avant étant identiques, cela permet d’économiser des outils de pressage et de réduire la complexité. Il en va de même pour les passages de roue et les pare-chocs. Le concept car oli est la preuve que la durabilité et un design attrayant ne sont pas contradictoires.
La couleur de la carrosserie traduit parfaitement le concept de la voiture. À première vue, elle semble être d’un blanc pur, mais des particules de mica ont été ajoutées pour souligner la forme de la voiture. Contrairement à l’extérieur, les matériaux de l’intérieur – tels que les sièges et le plancher – ont été recouverts d’une couleur orange intense.
Laurence Hansen, directeur des produits et de la stratégie de Citroën, voit cette collaboration sous un angle similaire. « La collaboration avec BASF a été un facteur clé dans la conception d’oli et dans le développement d’un véhicule électrique aussi amusant et efficace que possible pour le futur proche. Cette voiture électrique innovante va à l’encontre de la tendance à construire des véhicules de plus en plus lourds et complexes, en privilégiant la facilité et la simplicité. Elle démontre comment réduire au minimum l’impact sur l’environnement, tout en redonnant le plaisir d’un véhicule électrique fonctionnel« , a déclaré Hansen.
N’oubliez pas que vous pouvez poster gratuitement les offres d’emploi de l’industrie de la FA sur 3D ADEPT Media ou rechercher un emploi via notre tableau d’offres d’emploi. N’hésitez pas à nous suivre sur nos réseaux sociaux et à vous inscrire à notre newsletter hebdomadaire : Facebook, Twitter, LinkedIn & Instagram !