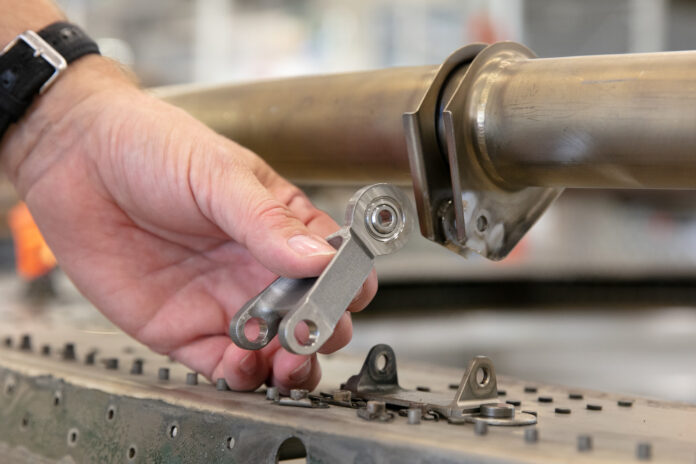
Lufthansa Technik, une entreprise qui fournit des services de maintenance et des services techniques à des clients VIP et gouvernementaux depuis plus de 60 ans, et Premium AEROTEC ont récemment uni leurs forces pour réaliser le développement et la production d'une pièce de rechange destinée à être utilisée sur des avions. Conçue pour le système d'antigivrage du moteur IAE-V2500, la pièce métallique imprimée en 3D vient d'obtenir sa certification aéronautique officielle de l'EASA.
Cela signifie qu'à partir de maintenant, Premium AEROTEC produira le "A-Link" pour Lufthansa Technik sur son site de Varel (Allemagne) à l'aide d'une imprimante 3D.
Connue pour l'utilisation d'imprimantes 3D métal avancées de fabricants de machines comme GE Additive, et pour sa participation au projet NextGenAM, Premium AEROTEC a acquis une expertise dans le développement et la production d'aérostructures en métal et en composites de fibres de carbone.
Neuf de ces A-Links fixent un conduit d'air chaud en forme d'anneau dans le capot d'entrée du moteur, qui est ainsi protégé de l'accumulation de glace pendant les opérations de vol. Cependant, les vibrations qui se produisent à cet endroit pendant le vol entraînent une usure des trous de fixation des A-Links, de sorte qu'après quelques années, il est souvent temps de les remplacer.
Comme les A-Links peuvent être exposés à des températures allant jusqu'à 300 degrés Celsius, ils sont fabriqués en titane. A la base, le composant est fabriqué par un processus de forgeage pour répondre aux exigences les plus élevées en matière de propriétés du matériau. Dans la nouvelle solution de fabrication développée par Premium AEROTEC et Lufthansa Technik, en revanche, il est imprimé 3D avec le procédé Laser Power Bed Fusion (LPBF), et présente l'avantage, par rapport au forgeage, de ne pas nécessiter de gabarits ou de moules pour la production. En outre, le processus permet d'économiser un matériau précieux, car après l'impression 3D, un enlèvement de matériau n'est nécessaire que dans une très faible mesure sur certaines surfaces fonctionnelles.
Cependant, les propriétés des composants produits de cette manière, par exemple leur résistance, dépendent fortement du processus de fabrication additive correspondant, dont la qualification doit donc être prouvée dans une procédure complexe. À cette fin, Premium AEROTEC a réalisé un grand nombre d'"impressions" avec des spécimens d'essai, avec des réglages constants de tous les paramètres pertinents pour le processus. Ainsi, il a été possible d'établir un processus constant et fiable et de prouver que les exigences les plus élevées en termes de propriétés des matériaux sont également atteintes ici. En termes de résistance à la traction, le « A-Link » fabriqué de manière additive est même supérieur à la pièce d'origine.
Dans le cadre de ce processus de certification, Lufthansa Technik a étendu l'expertise de son centre de développement EASA Part 21/J aux composants métalliques fabriqués de manière additive. Pour Premium AEROTEC, la coopération avec Lufthansa Technik est une étape importante dans le domaine de la fabrication additive, car c'est la première fois que l'entreprise fournit des composants imprimés en série à un client extérieur à Airbus Group. Les premiers A-Links issus de cette coopération seront utilisés dans la flotte de Lufthansa, où une expérience à long terme avec les nouveaux composants doit être acquise au-delà de la certification.
« Cela fait des années que nous produisons des composants pour la cabine des avions, dont la grande majorité est en plastique, en utilisant l'impression 3D. Aujourd'hui, nous sommes en mesure de démontrer que des pièces métalliques structurellement pertinentes destinées à être utilisées en dehors de la cabine peuvent également être fabriquées de manière additive et approuvées pour les opérations de vol », a déclaré Soeren Stark, directeur de l'exploitation de Lufthansa Technik. « De cette façon, nous avons non seulement réalisé une économie de coûts pour le composant en question, mais aussi défini et qualifié tous les processus nécessaires à l'application de cette méthode de fabrication révolutionnaire pour les pièces métalliques structurellement pertinentes. »
Toutefois, la première certification aéronautique d'une pièce de rechange métallique porteuse ne représente actuellement qu'une première étape pour les deux partenaires, car sa géométrie correspond encore largement à la pièce d'origine. Les développements futurs de la technologie permettront également d'utiliser les avantages de la fabrication additive pour une optimisation ciblée de la géométrie. En théorie, il n'y a pas de limites à la mise en forme des composants fabriqués de manière additive, de sorte qu'ils peuvent être produits beaucoup plus facilement et avec moins de matériau tout en conservant la même résistance et la même fonction. Les deux partenaires ont l'intention de développer davantage ces possibilités dans un avenir proche.
N’oubliez pas que vous pouvez poster gratuitement les offres d’emploi de l’industrie de la FA sur 3D ADEPT Media ou rechercher un emploi via notre tableau d’offres d’emploi. N’hésitez pas à nous suivre sur nos réseaux sociaux et à vous inscrire à notre newsletter hebdomadaire : Facebook, Twitter, LinkedIn & Instagram !