Among the post-processing tasks that have often been considered modest priorities by OEMs, there is depowdering. The thing is, a lot of consideration has always been given to depowdering of metal 3D printed parts, letting vertical industries adopting Additive Manufacturing (AM) with little information on how to properly handle this process with plastic 3D printed parts. The article below ambitions to change that by discussing 4 key considerations to take into account for this specific post-processing task. To do so, we have given the floor to Andreas Hartman, founder and CEO/CTO of Solukon and Philipp Kramer, CTO & Co-founder of DyeMansion.
It is no secret that 3D printed parts that are coming straight away from the 3D printer can already be utilized. However, for those parts to deliver value and achieve the desired performance, other post-processing steps need to be undertaken. For Andreas Hartman, founder and CEO/CTO of Solukon, these post-processing steps can “be divided into four categories: unpacking, cleaning (= depowdering / removing residual powder sticking (sintered) on the part surface), surface finishing (chemical or mechanical smoothing, polishing, blasting, infiltrating or milling, [coating and spray painting]) and coloring/dyeing.”
“Compared to Metal AM, there are even more processes for surface treatment and finishing in the post-processing of polymer components. This is because often the main goal of post-processing for polymer parts is a perfect resolution, look and color (automotive interior, glasses etc.) in addition to optimal functionality,” Hartmann adds.
When it comes to depowdering of parts, the concept is often interchangeably used with unpacking and cleaning – which is not entirely correct. This terminology may vary from one machine manufacturer to another depending on what their machine can do. For most manufacturers, depowdering which is the removal of powder from 3D printed parts is directly followed by cleaning, and can be done within the same machine. However, cleaning can also be done manually after the depowdering phase using brushes or in an automated way, using glass bead blasting. Unpacking the part on the other hand, means freeing the part from the powder cake; it often involves vacuuming and clearing away powder. This step occurs right before the depowdering and cleaning processes.
Interestingly, the depowdering of plastic 3D printed parts can easily be understood by comparing the same process performed with metal 3D printed parts. That’s why, we have identified 4 key considerations that may help part manufacturers to better understand this process.
1- The AM processes that work with depowdering
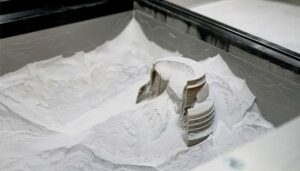
This is quite obvious, right? What AM process may require a depowdering of a plastic 3D printed part? For Philipp Kramer, CTO & Co-founder of DyeMansion, plastic parts manufactured in powder-bed technologies like Multi-Jet Fusion, Selective Laser Sintering (SLS), Selective Absorption Fusion [SAF™] and High Speed Sintering (HSS) are best suited for cleaning and surface finishing. “With those technologies the post-processing consists in removing excess powder in a cleaning step, delivering the right surface finish through blasting or vapor smoothing and coloring the parts in the desired color,” he adds.
2- The depowdering technique
Here again, the depowdering technique is quite different from what one uses to see with metals. Two differentiating factors shared by Hartmann and Kramer are quantity and weight:
3D printed plastic parts need to be depowdered in quantity whereas in metal depowdering only one or a few parts are mounted on one build plate. A plastic build box (e.g. of an EOS P7) often contains many different components of various shapes, structures and sizes that need to be unpacked and depowdered simultaneously.
The main challenge in post-processing of polymer parts is not getting complex inner structures powder-free (like in metal) but carefully and automatically loosening the parts from the powder cake and targeted blasting with glass beads without damaging the fragile and filigree parts. Especially because the plastic parts are not firmly attached to a build plate like in metal, but jumbled up in the build box and later in the rotation basked they need to be handled very carefully to avoid part damage.
In other terms, metal parts that are usually fixed on a large built plate, are depowdered before being removed. Therefore, either the built platform is rotated, or manual blasting is used. Plastic parts are lighter, more flexible and produced without support structures or a built plate. So, automated batch blasting processes in a basket or continuous belt are very well suited.
Another challenge may come with the use of glass beads. Solukon’s spokesperson warns that during the depowdering process, the glass beads get statically charged and adhere to the component. These adhesions must be released again with ionized air. Furthermore, during the process, more and more powder gets into the blasting material which can result in an undesirable discoloration of the parts due to thermal processes (the surface gets hot when plastic particles hit the surface). Therefore, when depowdering polymers, special care must be taken to ensure that the glass bead quality remains high (as little powder residue as possible in the blasting material). To keep glass beads quality high and refreshing rates low, some systems like the Solukon system use ultrasonic screening.
In any cases, one should keep in mind that “depowdering in the polymer sector is normally the final cleaning process in postprocessing, whereas in metal processes the part may be contaminated again during support removal, for example, and must be fine-cleaned again at the end,” Hartmann outlines.
3- The ideal machine
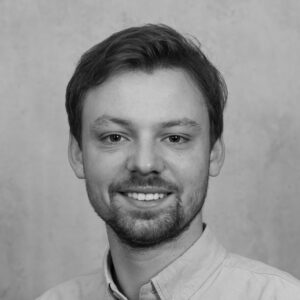
This is probably the most difficult consideration as there are a lot of options on the market and this article does not aim to study the unique features that set them apart. If each solution comes with its share of strengths and limitations, it’s important to keep in mind that applications, volume production, and costs are the key factors that may drive your choice for one solution or another.
Philipp Kramer
“Some basic manual blasters might be suitable for both metal and plastic parts. Once you use automated solutions, there are major differences in the machine setup and the process as well. So, it is recommended for users to [rely on] systems that have been designed and dedicated to either metal or plastic. Handling metal or plastic powder requires quite different technological setups,” DyeMansion CTO outlines.
4- The safety measures
Eliminating all risks related to health and safety has often been one of the major goals of machine manufacturers developing automated solutions. This goal has become a top priority given the fact powder handling of metal 3D printed parts could be explosive, and simply toxic for the operator.
Such hazardous dust can also be a risk for the operator’s health during the unpacking of plastic 3D printed parts due to the fact that they often manually uncover the parts from the powder cake.
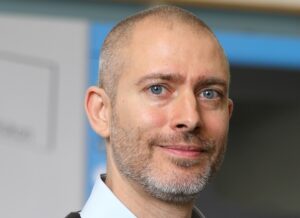
“The creation of clouds of powder that could be inhaled is unavoidable [hence the need of] respiratory protections or dust-extraction units. Since the dimensions of the build job can be very large, manual unpacking in protected gloveboxes is difficult or impossible due to the limited accessibility.
Since a high throughput of components is required in large production facilities, a lot of powder is also processed. Reducing human contact with hazardous powder is an even more pressing concern in the polymer field than in the metal field. The dust-free production must be the goal with regard to occupational safety and health protection. This calls for automated, sealed and consistent postprocessing of polymers without any manual intervention,” Hartmann alerts.
In the same vein, sustained inert material handling is often required for metals to avoid contamination with oxygen. Since polymer powders are not as reactive as certain metal powders, protective gas inertization is not usually used.
“Gentle cleaning processes with a low risk of dust formation and charging of the powder, a system design free of ignition sources and suitable dust extraction can sufficiently reduce the explosion hazard of polymer powders. Unpacking and depowdering only take place when the polymer parts have cooled down and therefore no inert gas is required. Oxidative processes only play a role in the build process and cooling, not in unpacking or depowdering,” Hartmann concludes.
This article has first been published in the July/August edition of 3D ADEPT Mag.
A few words on the contributing companies
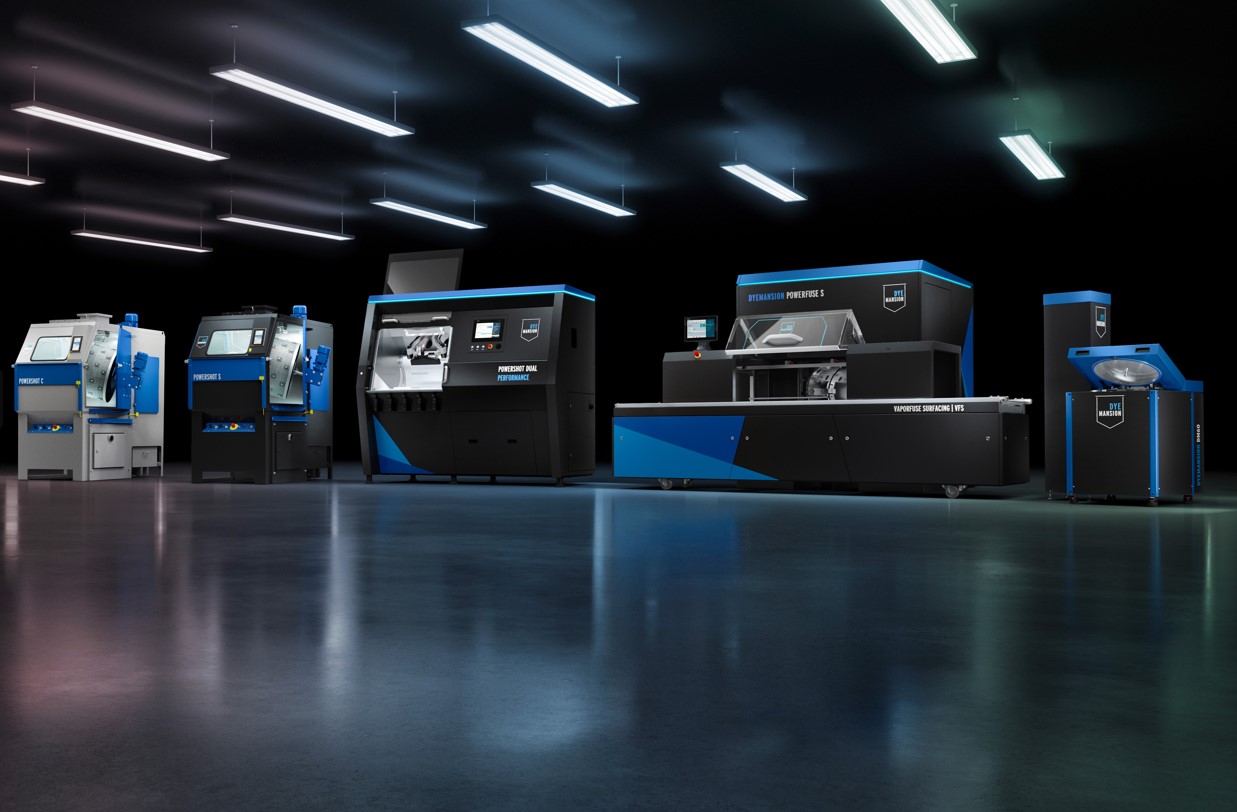
DyeMansion GmbH provides connected & fully integrated end-to-end solutions for all finishing steps for 3D-printed polymer parts. They specifically offer two different systems for the depowdering step. The classic Powershot C, which is an automated solution for handling small to medium batches, and the Powershot Performance C/Dual, which is dedicated to larger batches, digitally and physically integrated production setups. The latter comes with all digital interfaces and process control that is required for a full traceable manufacturing and can combine the cleaning and surfacing in one system. Both systems can also work with the PolyShot Cleaning process, which offers several advantages over traditional depowdering with glass and has been developed specifically for 3D printed plastic parts. The company believes that the right gentle depowdering plays a vital role in achieving reproducible results in surface smoothing and coloring.
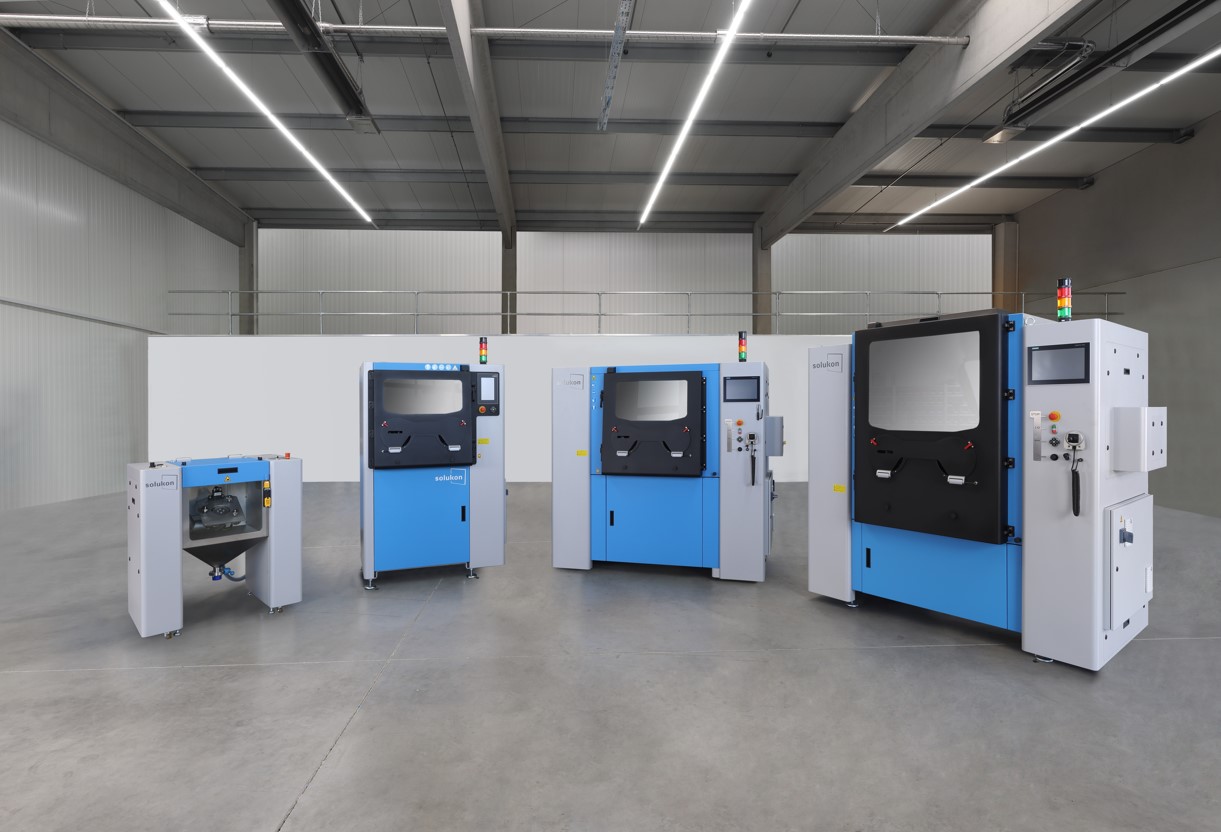
Solukon Maschinenbau GmbH provides automated depowdering solutions for Additive Manufacturing. The company believes that what differentiates polymer depowdering from metal depowdering systems is the need for a particularly gentle part handling. For the depowdering of polymer parts, they offer the SFP770 for parts printed on an EOS P 7, P1 and P5. Globally, the SFP770 is a one-of-a-kind post-processing system. It is the only one on the market to include both an automated unpacking station and a cleaning station for SLS components in just one system. What makes the system unique is not only the combination of the two process steps unpacking and cleaning but also the fact that the system is able to accommodate the whole build box of a polymer printer. The SFP770’s process includes the loading, unpacking, transferring and cleaning (depowdering). To ensure optimum cleaning results, the powder material is not separated from the blasting material by gravity separation in a cyclone, as is usual in standard blasting systems. Instead, Solukon uses a very compact ultrasonic sieve to clean the powder precisely from the blasting material (glass beads). Thus, practically no blasting material is lost and only very clean glass beads are used for cleaning.
Solukon thus enables a closed cleaning process and for the first time gets significantly closer to the idea of a dust-free shopfloor. In addition to economic efficiency, occupational health and safety is significantly improved and the acceptance of 3D printing in the industry is once again increased.