With contributions from EOS, SOLUKON & RÖSLER
Post-production, somehow, is the part of the manufacturing process that intimidates professionals most. The industry shows a certain lack of skills and control throughout the entire production chain for a finished 3D printed part – especially when it comes to a metal 3D printed part. It also shows a lack of reliable source when it comes to develop a proof of concept for a safe and reliable process that can remove and reclaim residual powder.
That’s the reason why we have decided to tackle this issue. In order to fully analyze the outlines of a powder removal process, we invited players that manufacture additive manufacturing systems, manufacturers of post-productions technologies and 3D printing service providers in order to have a user point of view in post-production technologies. Eduardo Alonso, Regional Manager France, EOS, Vincent Raman, specialist of Mass Finishing Technology at Rösler and Andreas Hartmann, Co-founder and technical director of Solukon share their respective expertise in this dossier. Other conversations and analyses from various experts including Lawrence Livermore National Laboratories will be brought throughout the dossier to highlight or give further precisions on some points.
Rösler is a surface finishing supplier that offers two essential finishing technologies, mass finishing and shot blasting, as well as industrial washing systems and in-house production and development. Due to the fact that a 3D printed part manufactured using DMLS, EBM, FDM, PolyJet, SL, SLM and SLS often comes out with corners, edges, burrs and rough spots, grinding, smoothing and polishing technologies of mass finishing are supplied by Rösler to enable manufacturers to get the expected rendering. Last year, the company partnered with PostProcess, another specialist in post-production technologies to complete its portfolio.
EOS is a manufacturer of industrial 3D Printing systems. Founded in 1989, the company provides a wide range of holistic solutions in additive manufacturing. Their participation in this dossier is quite atypical to the extent that they often discuss powder removal as part of the general topic powder process or material management.
Lastly, Solukon is a German manufacturer of peripheral post-processing equipment for additive manufacturing technologies. The company lays emphasis on automatic depowdering units and unpacking stations for laser-melted metal and plastic parts.
The post production stage consists in a series of additional manufacturing processes such as heat treatment to achieve desirable properties. The removal of excess powder from the internal cavities and complex geometries of the printed parts is a crucial part of this stage. The lack of accurate skills regarding this stage of the AM process often results in outsourcing the postprocessing stage to achieve better results for the finished part. This might therefore explain the fact that single-source production of high-value functional AM parts remains out of reach for several manufacturers, in addition to the multiple steps the manufacturing requires.
Speaking of additive manufacturing (AM) technologies themselves, basically, a powder removal process is required for all technologies that melt a powder, for example powder bed fusion, powder-based direct energy deposition, binder jetting, etc. Vincent Raman from Rösler and Andreas Hartmann from Solukon precise that powder bed fusion processes like Laser-Melting or Laser Sintering mainly require a powder removal process. This process raises several post-production challenges that we aim to demystify.
Challenges encountered during a metallic powder removal process
As a reminder, metal powder-bed fusion is an AM technology that melts layers of metallic powders together to quickly generate new parts. The only thing is that, at the end of the manufacturing process, one observes that excess powder covers newly printed parts, which poses a risk not only for future manufacturing processes but also for human health.
Furthermore, the removal of this powder is time-consuming since it is removed manually, therefore, creates a bottleneck for large-scale productions hence the need of a system that requires a minimal user input before the next stage.
Although Vincent Raman from Rösler explains that AM systems provide solutions for surface treatment & support removal, Eduardo Alonso on his side adds that “the main challenge is getting the powder completely out of the part, especially out of channels and small spaces where it is more difficult. Another important point is worker safety meaning to minimize powder contact during removal.”
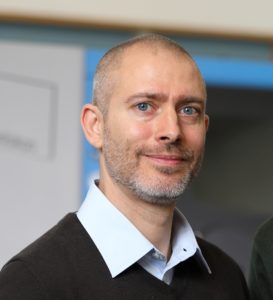
Moreover, according to an expert from Lawrence Livermore National Laboratories “another challenge is being able to tell when all the powder has been removed” on the one hand,
on the other hand, as per Andreas Hartmann’s words, to “remove residual powder safely, efficiently, economically, with reproducible cleaning results and providing the residual powder contamination free for recycling.”
The first observation is that these challenges may vary from one user or manufacturer to another because of the type of removal processes they use.
Types of current removal processes
Current removal processes can usually be divided into three categories: manual processes, liquid immersion, and ultrasonic cleaning.
Nowadays, the most used process remains the manual one, that sometimes, requires the use of compressed air to clear out cavities. It consists in physically shaking parts, using brushes, pipe cleaners, or build plate with a mallet to remove the powder. Furthermore, the process is framed by a strict regulation due to the safety requirements of the machine. Indeed, risks related to this process, mostly concern uncontrolled and airborne metallic powder.
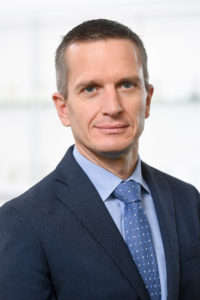
Although it is referred by others as time-consuming, EOS believes that the “manual process is usually fully flexible because it can be done at any time on any 3D printing machine.” This would certainly be the biggest advantage of this process. However, in the constant quest for rapidity, the company also recognizes the importance of automation in post-processing. Indeed, Eduardo Alonso states that “the automation of the powder removal process is in pilot testing at EOS and selected pilot customers: automation in order to remove the majority of the powder for instance by rotating the exchangeable within the 3D printing system frame by 180° or by a robotic arm with a suction nozzle.”
As far as liquid immersion is concerned, a research explains that success of the removal process of powder using this technique often varies from one to another. Devices used in this case are typically made in-house and typically use fluid flow to sweep debris away. A good example of such type of solution is the recently unveiled soluble support material of XJET, manufacturer of the metal and ceramic 3D printing technology CARMEL. Only intended for metal, the Israel-based manufacturer explained that it requires a few seconds to perfect the whole picture and facilitate the end of the manufacturing process. The solution reduces manual labor requirements while improving the process. Dissolving rapidly in a water-based, hazard-free solution, the advantages of soluble support materials can be striking.
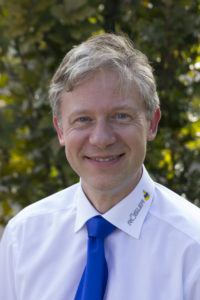
Speaking of the liquid immersion process, Vincent Raman said “the liquid immersion removes support structures for different print techniques in both large batches but also on a single piece, without manually action needed.” However, for the Mass Finishing Technology specialist, “a lot of customers use a shot-blasting process which requires a lot of manual labor most of the times, hence the automation feature that Rösler integrated for smaller parts.”
As far as the ultrasonic cleaning process is concerned, it consists in immerging the part into a fluid bath (water or solvent), and thereafter, using a transducer to create ultrasound waves. These waves lead to cavitation and once the formed bubbles collapse, they remove debris from the part. One disadvantage of this process is the fact that the immersion of a part into a liquid part makes the removed powder useless while for economic reasons, manufacturers often tend to reuse the removed powder.
The Co-founder and CEO of Solukon, Andreas Hartmann, provides a general view on the three categories of metallic removal processes:
“At first sight manual processes don´t need much know how and can be performed by using blowing or brushing devices. But looking at it closely, manual powder removal is very risky as the operator unavoidably comes into contact with particulate matter.
This metal material is very fine, and is light enough to be airborne in many cases. It is generally harmful to health and there is a risk that it may enter the body via the respiratory tract or through the skin. If the powder is released into the air it can create clouds of dust that may result in a dangerously explosive atmosphere.
At the same time, manual powder removal is also time-consuming, and the cleaning results are unpredictable with variable reproducibility compromising the quality.
All these factors carry risks for health, safety, quality and high costs.
Liquid immersion works very well for cleaning surfaces without leaving a residue but the parts should be pre-cleaned with a dry process as residual powder which often raises issues when internal channels are full of powder.
The powder gets stuck and the part is damaged. Ultrasonic can be very helpful but clogged channels are also here possible.
In general, when using immersion, the residual powder cannot be reused and has to be disposed.
Immersion with chemical solvents or electro chemical pulse methods-are perfect solutions as they can remove support structures and improve the part surfaces.
But also, in this case it is helpful to remove most of the powder in a dry process as the powder cannot be reused.”
Other (patent-pending) powder removal devices and methods are not always intended for AM technologies. Some of them include the use of vibration whereas others use vacuums or magnetic forces to remove powder.
A close look at each company’s technique to remove metallic powders during a post-production process
EOS
As announced earlier, the German manufacturer EOS provides a whole system for powder management. Called, IPCM M pro, it enables to convey out of the AM system, material that is not fused during the building process– without opening the process chamber door and therefore without the operator coming into direct contact with the material.
“A vacuum pump conveys the powder out of the system and into the IPCM M pro, where it is sieved under inert gas within the module at a throughput of 120 kilograms of material in 30 minutes – 50 percent faster than previous solutions. Powder treated in this way can be used for a new building process, the powder cycle starts anew.”
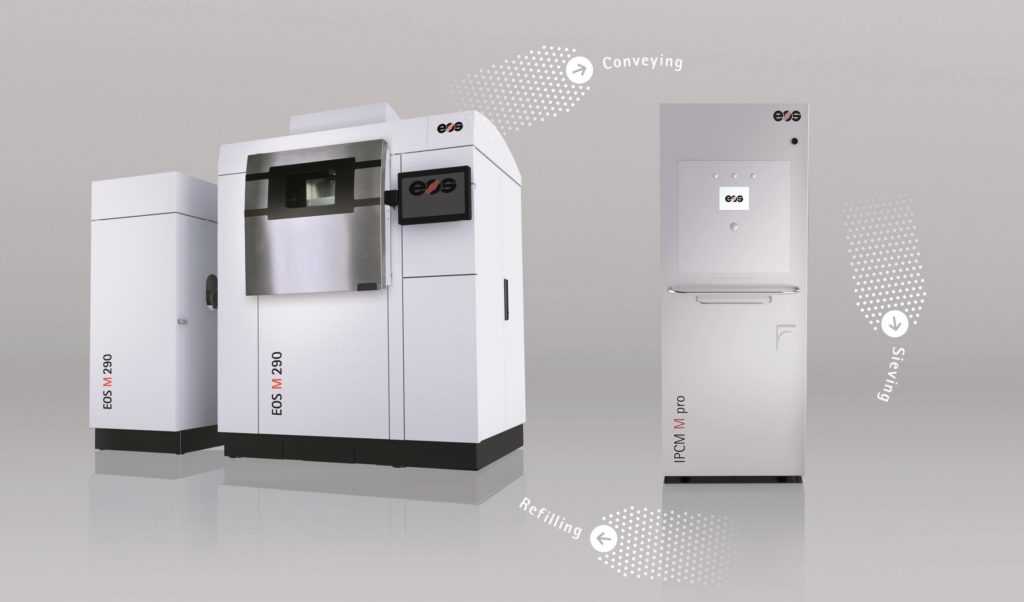
According to the company, it is a comfortable protective equipment due to its advantages in terms of health and safety as well as operability, as the risk of powder contact is minimized.
Rösler
Rösler does not only provide post-production technologies for metal additive manufacturing.
“We supply post printing & sintering processes. These processes are defined as removal of support structures (both metal and plastic parts) and aim to improve the surface (both metal & plastic parts). Our biggest advantage is the automated feature as well as the long experience the company has as surface specialists”, explains Vincent Raman.
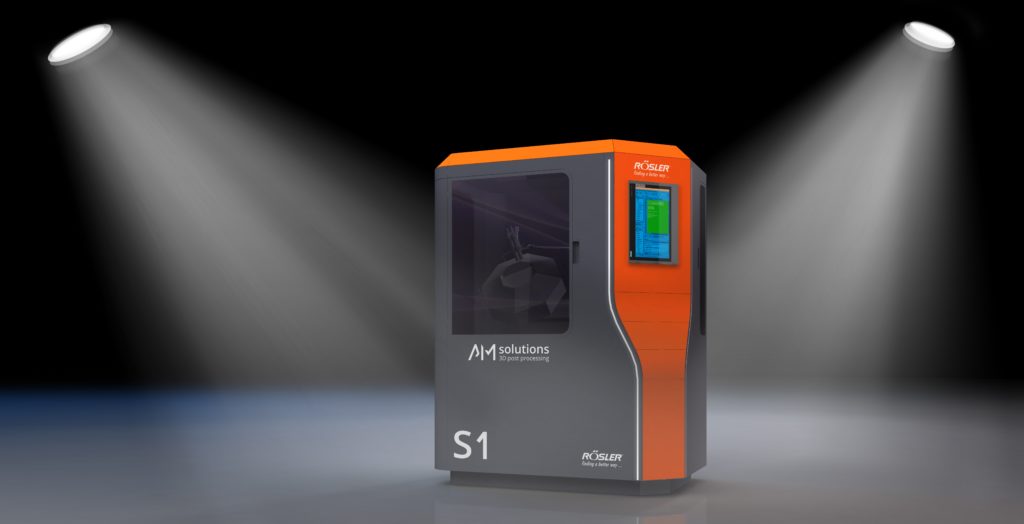
Solukon
As for Solukon, the company has recently unveiled its SFM-AT800-S depowdering equipment following the SFM-AT800.
Speaking of these equipment, Andreas Hartmann said that the “automated depowdering units remove and collect residual powder from complex laser melted parts with targeted vibration and programmable two-axis rotation within a protected atmosphere. The adjustable and high frequency vibration makes the powder flowable so that it can run out easily of very small gaps and intricate channels.
The flowing of the powder is supported by moving the part automated around two axis to all possible 3D positions continuously or to individually programmed positions. In addition to this, the systems are equipped with manual or automated blowing devices. To prevent explosive atmospheres for reactive materials like Titanium and Aluminium the process chamber can be rendered inert due to a safety controlled inert-gas-infusion.
The residual powder can be collected contamination free for recycling in special containers or directly recycled in a connected sieving system. In addition to mitigating the health and safety risks, users are able to significantly reduce cleaning time and improve the collection and recycling of expensive unused powders. Some users have reported labor reduction of up to 90% over manual powder removal processes.”
The company adds that, “due to adjustable vibration, the process is very gentle and does not influence the mechanical properties of the part or surface.”
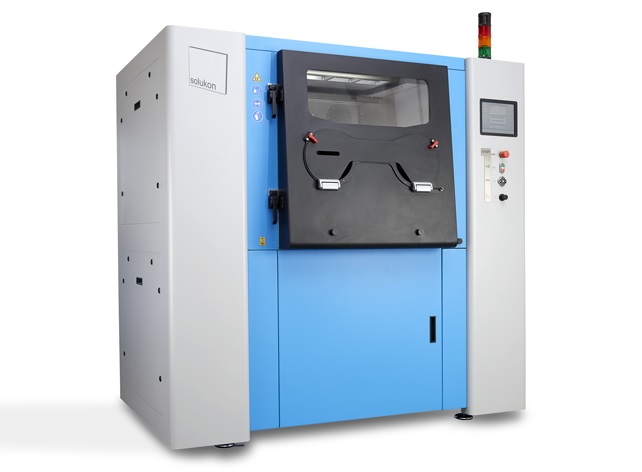
Getting the desired finished part
At a seminar of GE Additive, one of the company’s engineer states that out of all of the stages that are integrated into the final cost of a part—labor, operating expenses, scrap costs, machining costs, part material costs, solid material waste, powder waste etc.—postprocessing or postproduction often represents nearly 30 percent, which can constitute a big deal for companies. Therefore, handling the postprocessing operations of a production the good way, might result in significant advantages for companies.
Obviously managing these operations requires to consider all the contours of the idea: the environment, the appropriate equipment and even the final purpose after the removal of powders.