
La plupart des enjeux de la fabrication additive concerne très souvent les logiciels ou les matériaux. Cela peut se comprendre, ces éléments jouent un rôle déterminant dans l’amélioration du flux de production d’une pièce, mais une fabrication additive réussie d’une pièce fonctionnelle dépend aussi d’autres éléments externes dans l’environnement : les gaz.
Pour plusieurs raisons (et souvent de façon inconsciente), les professionnels n’y accordent pas souvent d’importance et pourtant, les gaz contenus dans l’environnement de production peuvent avoir un impact pendant et même après la production d’une pièce fabriquée par fabrication additive.
Alors que nous n’avons (presqu’) aucun contrôle sur l’air que nous respirons chaque jour, dans l’industrie de la fabrication additive, des entreprises telles que Linde tentent de « contrôler l’incontrôlable » afin de permettre aux fabricants d’avoir une « fabrication additive réussie ».
Comment le font– elles ? Nous en avons discuté avec Pierre Forêt, spécialiste de la Fabrication Additive chez Linde. #OpiniondelaSemaine
Linde est un groupe international allemand qui s’est spécialisé dans les domaines des gaz et de l’ingénierie. Sur le marché de la fabrication additive, la société propose des gaz industriels et se positionne dans cette arène au même titre qu’Air Liquide ou encore Praxair.
Si l’entreprise a été créée en 1879, Pierre Forêt nous confie que cela fait plus de 10 ans qu’il y travaille, et depuis les 4 dernières années, il dirige l’équipe de fabrication additive, qui se consacre à la recherche et au développement des gaz pour ce marché. En plus de filiales en Europe et en Amérique, l’entreprise de Munich a une usine qui est constituée d’équipements et de technologies nécessaires sur lesquels l’unité que dirige Pierre Forêt travaille pour proposer des solutions à l’industrie de la fabrication additive.
Quand et pourquoi Linde est-elle entrée dans l’industrie de la FA ?
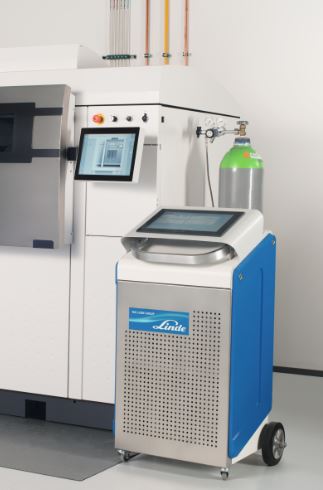
Linde produit des molécules de gaz (oxygène, argon, etc.) qui sont utilisées dans de nombreux procédés. Dans le cas de la fabrication additive (FA), des gaz inertes comme l’argon ou l’azote sont souvent utilisés dans l’environnement de production.
Ce qui est intéressant, c’est que, lorsque nous examinons l’ensemble de la chaîne de valeur, le rôle des gaz n’est pas souvent bien perçu et pourtant le processus de production les implique. Par exemple, la poudre utilisée comme matériau dans l’imprimante 3D a été produite avec une grande quantité de gaz. Le processus de production lui-même implique la présence de gaz dans l’environnement de production et même pendant l’étape de post-traitement, un processus appelé pressage isostatique à chaud utilise des températures dans une atmosphère confinée à haute pression pour éliminer la porosité interne et les vides dans les matériaux et composants métalliques coulés. Fondamentalement, le procédé de pressage isostatique à chaud est utilisé dans les applications haut de gamme pour compacter la pièce.
Comme les gaz jouent un rôle clé dans les différentes étapes du processus de production, notre rôle est de développer des technologies qui compléteront les systèmes de FA afin de permettre une bonne aptitude à la fabrication.
Le développement de gaz pour différents secteurs d’activité est notre cœur de métier depuis des décennies, mais depuis 2016, compte tenu de la croissance du marché de la FA, nous avons décidé d’engager des experts internes et de consacrer une unité complète à ce secteur afin de mieux accompagner nos clients.
Comment expliquer le rôle des gaz dans la FA ?
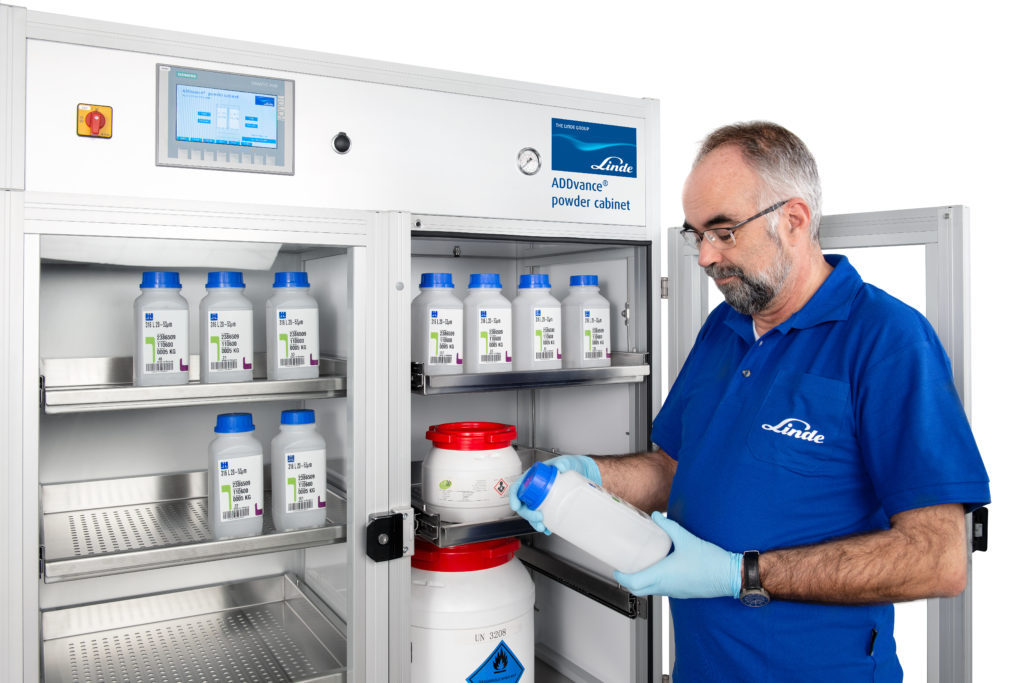
La FA est une technologie encore jeune. De nombreux clients de l’industrie automobile, de l’aérospatiale et même de l’industrie médicale ont réussi leurs applications grâce à la fabrication additive, mais l’utilisation de cette technologie reste très limitée par rapport aux applications réalisées avec des procédés traditionnels.
Il y a un siècle, les gens étaient enthousiastes à l’idée d’utiliser le procédé de soudage. Au tout début, ils ne se souciaient pas de la qualité des gaz qu’ils utilisaient ; des gaz bon marché avec beaucoup d’impuretés. Avec le temps, ils se sont rendu compte que s’ils utilisaient le mélange de gaz approprié, ils pourraient augmenter la productivité et la qualité de ce processus.
Le même phénomène peut être observé dans l’industrie de la FA. La FA est utilisée depuis plusieurs années, mais depuis peu, les professionnels ont pris conscience de l’influence des gaz sur l’aspect de la pièce finale. Notre rôle n’est donc pas seulement de faire prendre conscience de la présence de molécules de gaz, mais de développer des solutions qui pourraient faciliter leur utilisation.
Pourriez-vous nous en dire plus sur votre système de poudre ADDvance® et comment il assure l’intégrité des poudres métalliques pour la fabrication additive ?
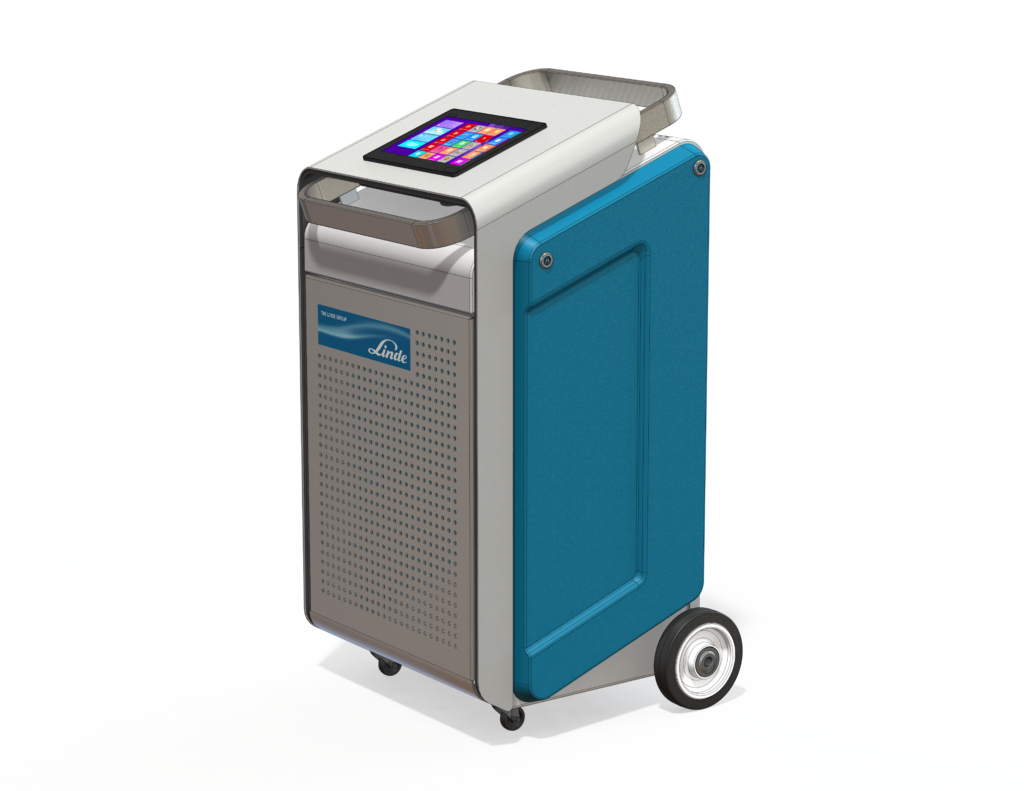
ADDvance®
Un de nos clients s’inquiétait de l’achat d’une poudre extrêmement chère, le titane (son prix peut aller jusqu’à 300€ par kg) et il lui fallait beaucoup de poudre pour un procédé. Le bémol est qu’en plus d’être chère, la poudre est très sensible à l’humidité, ce qui signifie qu’il est facile de perdre l’essence de la poudre ; et cela aura certainement un impact sur le processus d’impression.
Afin d’éviter ce gaspillage d’argent, la solution idéale était de développer un système qui pourrait à la fois stimuler la poudre et éliminer l’humidité. C’est ainsi que nous avons développé le système ADDvance® qui ne contient ni air ni humidité.
La solution de stockage fonctionne avec une fonction de contrôle et de surveillance de l’humidité qui permet de mesurer en continu les niveaux d’humidité. Il libère une grande quantité de gaz de purge dès que les portes sont fermées pour éliminer rapidement l’humidité de l’air. Il applique ensuite un flux de gaz plus faible afin d’assurer un niveau d’humidité constamment bas. Il n’y a donc pas de perte de qualité.
Vous avez récemment signé un partenariat avec GEFERTEC. Quel sera votre rôle dans ce partenariat ? Quel est le but du projet ?
Nous avons commencé ce projet l’année dernière avec GEFERTEC et d’autres partenaires. Ce projet est basé sur le procédé d’impression 3D métal de Gefertec (qui utilise un fil et un arc par rapport au laser et à la poudre dans le procédé Laser-Powder Bed Fusion). L’objectif est de permettre la production de grandes pièces en un temps record.
Dans ce projet, nous examinerons la production de pièces en titane et, comme expliqué précédemment, les gaz jouent un rôle clé dans l’utilisation de ce fil. En effet, c’est un matériau dont l’utilisation est pratique lorsqu’il est associé à des mélanges gazeux appropriés. Et Linde entre en jeu à ce stade.
Votre dernier mot ?
Nous communiquerons davantage sur nos activités de R&D et montrerons à la communauté nos résultats sur l’influence de l’oxygène dans une imprimante 3D. Nous avons plusieurs projets en cours avec du titane, des alliages à base de nickel et d’autres matériaux. Je crois que notre opinion à ce sujet aidera la communauté à amener la FA à un niveau plus solide.
Pour des informations exclusives sur l’impression 3D, abonnez-vous à notre newsletter et suivez-nous sur les réseaux sociaux ! – Toutes les images ont été reçues de Linde
Vous souhaitez-vous abonner à 3D ADEPT Mag ? Ou vous voulez figurer dans le prochain numéro de notre magazine numérique ? Envoyez-nous un email à contact@3dadept.com
//pagead2.googlesyndication.com/pagead/js/adsbygoogle.js (adsbygoogle = window.adsbygoogle || []).push({});