Remember this exclusive feature on Cold Spray Additive Manufacturing (CSAM)? One of the reasons why the process is an interesting production candidate is that since there is no heat, operators can easily explore the use of reactive materials such as titanium, aluminium, and magnesium.
When compared to other 3D printing processes such as powder bed fusion, Impact Innovations GmbH, a machine manufacturer that develops industrial cold spray systems and processes, adds that CSAM remains attractive since it does not have equipment size limitations, nor require protective atmosphere especially when depositing reactive materials such as Ti-6-4.
Speaking of titanium, the company explains that Ti-6Al-4V was considered as one of the most challenging materials, due to the high critical velocities of the materials to overcome during the deposition process, which resulted porosities in the cold spray deposits of 3% and higher.
To address this issue, Impact Innovations has combined cold spray hardware, process parameters & post treatment procedure. The result of the research led to porosity levels <0,5% and final mechanical properties exceeding the requirements given by the ASTM F3001, ISO 5832-3 and AMS 4930 standards.
Another comparison Impact Innovations GmbH highlighted is that, powder particles are not melted during the Cold Spray process. The bonding occurs due to plastic deformation. Since Cold Spray does not require high temperatures, unlike other common technologies such as laser, electron beam or wire-arc based processes, it enables deposit components without the necessity of using any protective atmosphere with almost no dimensional limitation and in the absence of thermal residual stresses. The Ti-6-4 material efficiency from powder to deposit is more than 98%.
Impact Innovations GmbH decided to demonstrate its new CSAM process by building a Ti-6Al-4V freestanding turbojet aircraft engine fan shaft. The fan shaft is 380mm long and has in its widest place 223mm diameter. It was deposited in about 2h at deposition rate of 2,7kg/h. the net weight of the fan shaft after final machining is 3,2kg.
The fan shaft was deposited onto a pre-machined Al alloy mandrel, which was removed after the Ti-6Al-4V deposition by chemical dissolution. Subsequently the fan shaft demonstrator underwent dedicated post treatment processes to achieve the desired mechanical properties followed by turning to the final outer design and creating the additional features by other conventional subtractive manufacturing processes.
The Ti-6Al-4V alloy is typically used in marine and defence applications, for manufacturing aerospace structural parts, gas turbine components and biomedical implants and prostheses.
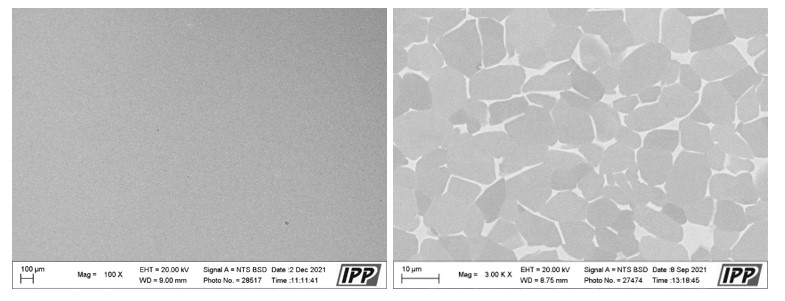
Remember, you can post job opportunities in the AM Industry on 3D ADEPT Media free of charge or look for a job via our job board. Make sure to follow us on our social networks and subscribe to our weekly newsletter : Facebook, Twitter, LinkedIn & Instagram ! If you want to be featured in the next issue of our digital magazine or if you hear a story that needs to be heard, make sure you send it to contact@3dadept.com