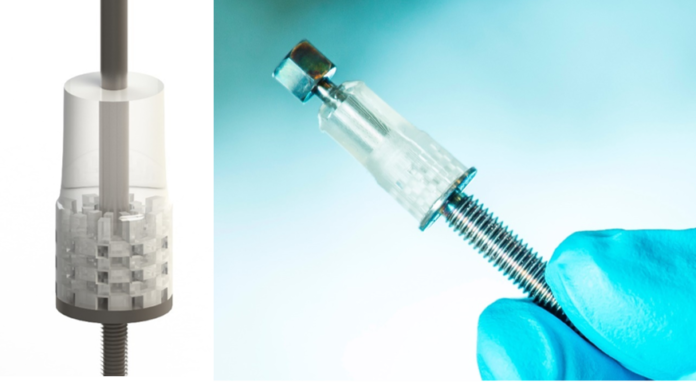
As far as applications are concerned, the interest in exploring a new material that is not available for 3D printing usually drives the choice for FIM.
In seven years of activity, AddiFab’s relocation to new and larger facilities was a bigger step for the Danish 3D printer manufacturer to date. This step forward is the sign that the company is growing and is going into the right direction for its purpose. On the other hand, for the industry, what’s important is to know the range of applications that the company’s technology enables and how to implement them.
As a reminder, AddiFab develops both “an additive manufacturing technology and an injection moulding technology” called Freeform Injection Molding (FIM). The hybrid process aims to fill the gap between prototyping and production by delivering the freedom of additive manufacturing with the volumes of injection molding within the same platform.
With its recent fund raising, AddiFab assured that the investment will help the team demonstrates the capabilities of their technology through tangible applications. In this vein, FIM seems to be an ideal production candidate for several applications including medical devices. The company’s CEO Lasse G. Staal explains:
“Freeform Injection Molding has already demonstrated applicability in fields as diverse as anti-hypothermia treatment, implantable bone screws, COVID-19 protective equipment, faeces sampling and eye-drop dispensing. The reason why FIM is becoming a preferred tool for medical device developers is simple:
Medical device manufacturers work in a heavily regulated field, and have to demonstrate that the materials they use for their devices are safe to use. Therefore, most device manufacturers stick to a limited number of specific polymer grades, that are sourced from specific suppliers having the necessary quality assurance systems in place. More often than not, these grades are not available in versions than can be 3D-printed. And even if they are, materials that are 3D-printed will not exhibit the same performance as materials that are injection-molded. Therefore, medical device manufacturers who want to introduce a device featuring injection-molded components into the market, will invariably have to start injection-molding before they can verify and validate the safety and performance of that device. And Freeform Injection Molding is the fastest and cheapest way to get injection mold tooling in place, especially for hard-to-mold materials and complex geometries.”
However, experience reveals that medical devices’ manufacturers share similar challenges than other manufacturing industries. For this reason, although the primary area of interest in terms of applications remains the medical industry, it should be noted that AddiFab provides other industries with the same offering: “3D-printed injection mold tooling that is compatible with virtually the entire range of thermoplastic materials, and that offers a design freedom on a level with 3D-printing.”
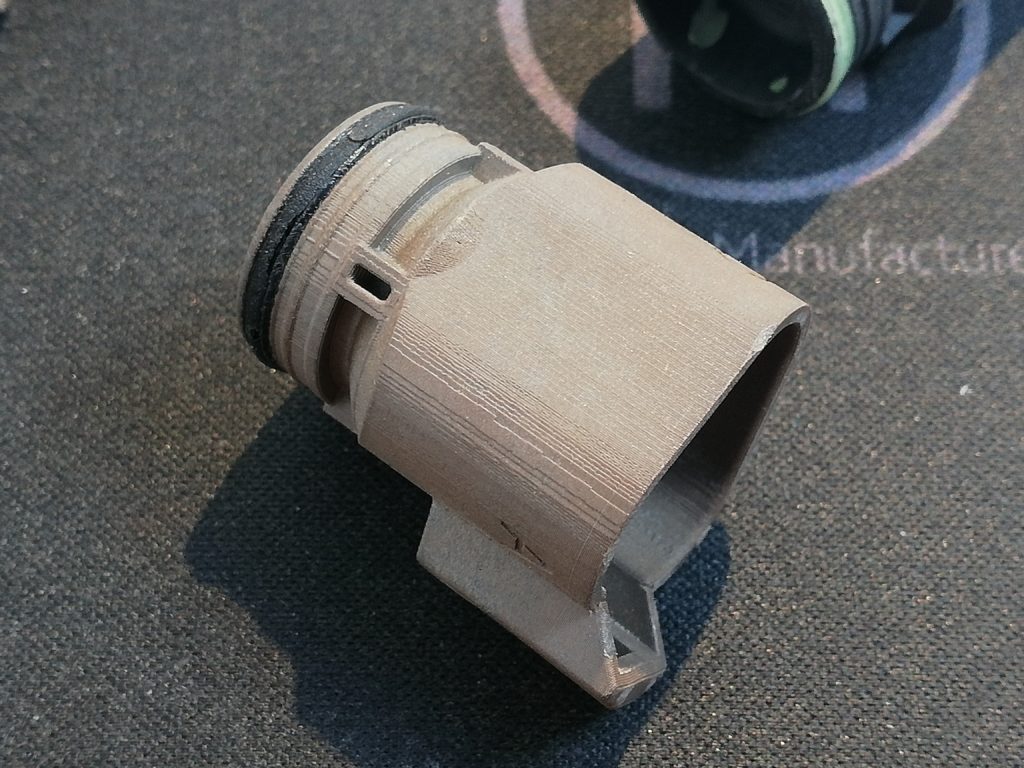
So, how does one define FIM for production applications?
When it comes to AM, there are no standard guidelines that enable to determine whether or not the technology is the ideal production candidate process to leverage. In a recent dossier, we’ve identified three different frameworks that are usually explored before going down the AM route for series production. However, in the case of FIM, whether the customer is familiar with AM or injection moulding, the transition towards FIM is quite smooth due to the ability of FIM to integrate the characteristics of both processes.
As far as applications are concerned, the interest in exploring a new material that is not available for 3D printing usually drives the choice for FIM.
“Most of our customers are pretty sophisticated users of conventional 3D-printing, and they typically get in touch when they want to use a material that is not available for 3D-printing. But we see an increasing number of injection molders get in touch because they want to speed the transition from 3D-printing to injection molding”, Staal notes.
Exploring FIM candidacy for an application therefore follows a three-step process that consists in:
- Determining at what degree FIM will meet a customer’s request
- Implementing mold-flow analyses
- Identifying the best implementation model of Freeform Injection Molding for the customer’s specific project
According to Lasse, during the trial phase – the first step -, their team assesses key product features and key reference materials that could be used for a given application.
“As an example, the first thing we did when kicking off evaluations of FIM for the manufacturing of flip caps – was to zoom in on the hinge portion itself. We stripped away the 90% of the cap that had nothing to do with the hinge function, and did a number of iterations with stand-alone molded hinges in the customer’s reference material until being satisfied with the hinge performance. This “zoom-in” approach is extremely fast and cost-efficient – and one of the first things that differentiates FIM from conventional “get-everything-right-the-first-time” injection mold tooling”, the expert points out.
Once they have ascertained how to do each new feature of a given application, the fabrication process of printed tools begins. At this stage, the mold-flow analyses help to ensure that they do not waste no shots on faulty designs. It also helps to decide what the ideal option is when it comes to closed single-part tools or open multi-part tool designs.
Staal states that the closed single-part tools are often the most cost-efficient and easy to design, but a component may have features (most often overhangs) that require them to split a tool into multiple components.
“We also frequently face customers wanting to get as many shots as possible out of a single tool. While the “Freeform” part of Freeform Injection Molding requires that tools be dissolved, the inserts we print are pretty sturdy. And if we have to support higher-volume applications we typically work with the customer to develop hybrid tooling concepts – where 3D-printed sacrificial inserts are combined with conventional metal tool cavities”, he adds.
When there is no doubt that FIM can effectively be used for a given application, the next step consists of implementing the process. At this level, it should be noted that the customer does not necessarily always have a FIM process in-house. Depending on the volumes they need to produce, they can either work with AddiFab’s partners – Mitsubishi Chemical Advanced Materials – or they can explore different acquisition options with the team at AddiFab.
With Mitsubishi Chemical Advanced Materials (MCAM) as a partner,AddiFab does not only benefit from an array of materials compatible with its FIM solution. It also benefits from a partner who can support its Freeform Injection Molding-as-a-service offering. With AddiFab systems at facilities in the US (Arizona), EU (Belgium) and APAC (Japan), MCAM has been providing customers across key demanding verticals with high-performance, metal-replacing KyronMAX® line of materials since mid-2020.
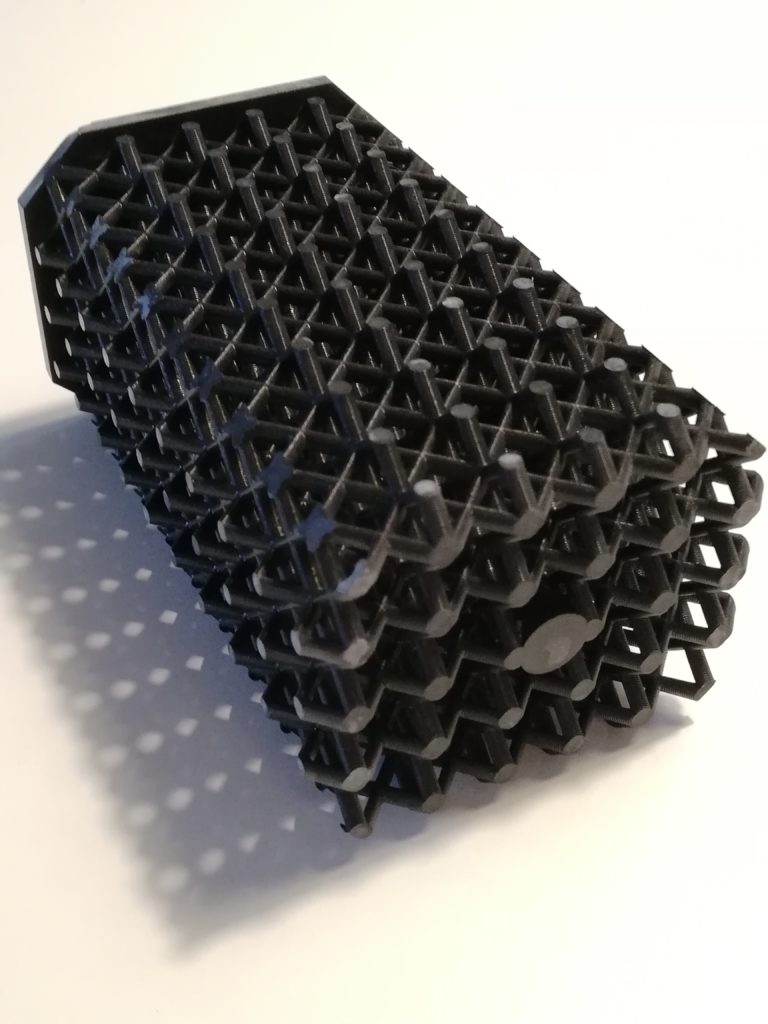
According to the company, combining FIM printed inserts with heavy-duty metal elements enables to get the best of both 3D printing and injection molding worlds.
To date, one thing is certain, they “benefit from being able to aggregate a lot of demand on very few resin variants. Freeform Injection Molding – like other printed tooling technologies – wins by leveraging the vast catalogues of legacy materials from the injection molding industry, instead of having to develop new materials that mimic the capabilities of those already invented”.
Insights into the FIM process: current developments and areas for improvement
Last year, amid the peak of the Covid-19 pandemic, AddiFab unveiled a module that would enable micro injection molders to increase their printer resolution from a very decent 50 µm to a top-of-the-line 10 µm. Named AddLine Micro, its development is the result of the team’s holistic experience with the Micro system which was first utilized on a stand-alone unit. Following several requests from customers, they have explored how they could improve the compatibility of the Micro system with the standard 50 µm set-up. Today, the interchangeable add-on module works with a specialized resin that may be installed and run on an existing AddiFab printer.
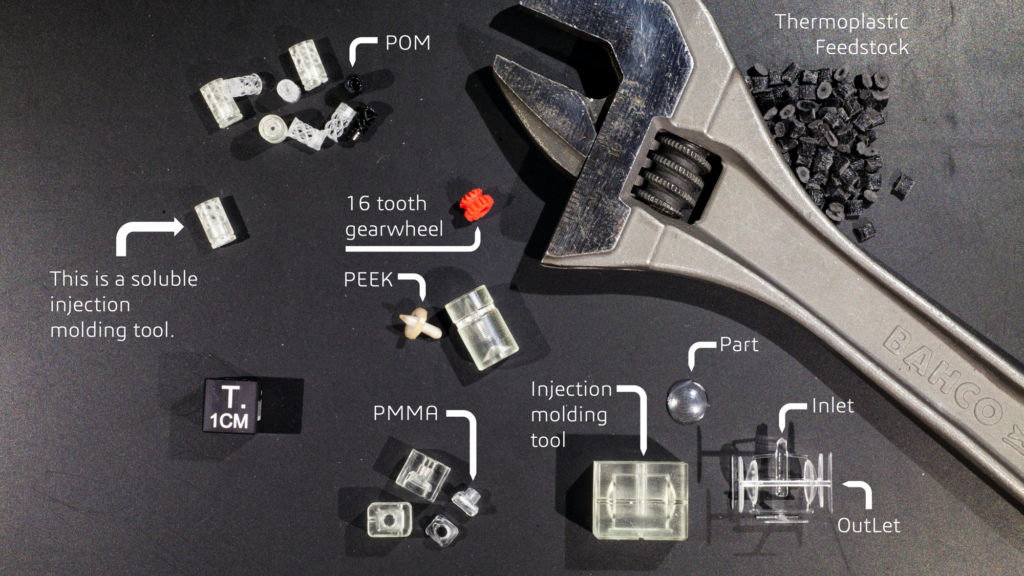
“The AddLine Micro has been quite a bit of an eye-opener for us. When we first decided to set up a printer to do a test job with our 10 µm configuration, we anticipated that the printer would be returned to 50 µm operation as soon as the job was done. But we decided to do informal reach-outs to a couple of customers already familiar with FIM – and the response was overwhelming. In retrospect, I guess we should have realized that micro injection molding is one of the most underserved industries when it comes to prototyping platforms. As a result, we have already had the opportunity to demonstrate the applicability of the Micro with metal injection molding, silicone injection molding, high-performance thermoplastics, light-guides and direct prints. And we see several of these initial dialogues turn into repeat requests almost as soon as we have completed the first studies. I suspect that the Micro set-up is covering a pretty significant unmet need in the market for micro molding”, Staal outlines.
From one single configuration – the 50 µm standard – to applications that go beyond the sweetspot of their first AddLine system, the team at AddiFabrecognizes that customers’ requests have led to the development of better add-on modules for their technology. Not to mention that the demand for bigger parts has led to hybrid solutions that combine printed inserts with metal cavities.
Today, as they are writing their next chapter of their journey in their new facility, they also want to improve the user experience and the usability of their platform.
“Succeeding with Freeform Injection Molding means combining skills from 3D-printing, tool design and injection molding, and we are diligently expanding our range of hardware and software tools to make life easier for our customers” Staal concludes.
All images: courtesy of AddiFab – Remember, you can post job opportunities in the AM Industry on 3D ADEPT Media free of charge or look for a job via our job board. Make sure to follow us on our social networks and subscribe to our weekly newsletter : Facebook, Twitter, LinkedIn & Instagram ! If you want to be featured in the next issue of our digital magazine or if you hear a story that needs to be heard, make sure you send it to contact@3dadept.com