According to Additive Manufacturing Research (AMR), the electronic additive manufacturing market could reach $7.9 billion by 2033. However, the industrialization of additive manufacturing (AM) is still hindered by technical and economic challenges.
Multiphysics simulation, capable of modelling and optimizing the complex interactions between mechanical, thermal, and electromagnetic phenomena, is emerging as a strategic lever to overcome these obstacles. By combining AM and multiphysics simulation, the electronics industry can achieve reliable and cost-effective performance on a large scale.
Multiphysics simulation: A driver for optimizing electronic manufacturing processes
Multiphysics simulation integrates mechanical, thermal, and electromagnetic analyses to optimize each stage of component design and manufacturing:
- Mechanical simulations ensure the structural integrity of materials, whether they are conductive, semi-conductive, or insulating, and ensure the robustness of miniaturized devices. 3D-printed enclosures benefit from this optimization to meet requirements for lightness, durability, and precision.
- Thermal simulations identify hot spots and optimize heat dissipation, preventing deformations due to temperature fluctuations and thus improving component reliability. They extend the lifespan of critical components, such as medical sensors or high-precision devices.
- Electromagnetic simulations optimize electromagnetic compatibility (EMC) and high-frequency performance, avoiding unwanted interference. This is crucial in the development of antennas and active devices, ensuring high performance while integrating a miniaturized architecture.

Material management focused on economy and sustainability
One of the main challenges for engineers is the choice of conductive inks and polymers, which must combine conductivity, thermal stability, and compatibility with various substrates. Thanks to thermal simulations, it is possible to test and select high-performance formulations even before production, allowing substantial savings in physical testing and development time.
Optimizing printing parameters, such as deposition speed and temperature, maximizes print quality while controlling material consumption, which is valuable in a context of resource scarcity and high costs. Simulation thus enables savings while contributing to the sustainability of industrial processes.
Improved precision and reliability of processes
Electronic additive manufacturing still has limitations in terms of precision, particularly for multilayer printed circuits and miniaturized components. Multiphysics simulation is essential for anticipating and correcting mechanical and thermal deformations induced during printing, thus ensuring better reproducibility of components. By modelling the stresses induced by ink cooling, engineers can compensate for dimensional variations upstream, reducing scrap rates and increasing the quality of manufactured parts. This increased precision is essential to meet the high standards of aerospace, medical, and consumer electronics.
Reduction of costs and development time
Multiphysics simulation facilitates virtual prototyping, replacing some physical iterations with numerical simulations. By limiting the need for prototypes, this approach reduces costs and shortens development times, allowing companies to respond more quickly to market changes and launch innovative products in competitive timeframes. The ability to quickly adapt designs improves agility and flexibility, especially in the face of short production runs. R&D teams can virtually validate performance and adjust their designs upstream, thus optimizing the time between design and market launch.
Concrete Example:
3D Printing Corporation, specializing in 3D printing of electronic components, managed to reduce its production costs by 20% and its scrap rates by 15% by using simulation to optimize its material combinations and printing processes. These efficiency gains, combined with waste reduction, are a major asset for an industry seeking sobriety and sustainability.
Towards new use cases and optimized integration
Beyond optimizing current processes, multiphysics simulation promotes the exploration of new electronic applications by testing the viability of innovative designs in environments subject to extreme constraints. AM opens up new perspectives for demanding sectors such as telecommunications, with the development of antennas for 5G and 6G. According to an AMR report, 3D-printed millimeter-wave antennas, produced in a few hours for less than ten dollars, show performance comparable to conventional models but at a drastically reduced cost. The ability to produce such devices at low cost while maintaining high efficiency could revolutionize coverage in underserved rural areas.
In addition to telecommunications, electronic 3D printing benefits medical devices, smart sensors, and consumer electronics, meeting the growing needs for customization and miniaturization. By integrating multiphysics simulation into CAD software, engineers validating AM specifications from the design stage facilitate its adoption in established production lines and secure returns on investment for manufacturers.
This article has been written by Sebastian Stahn, Lead AE, Product Manager – Structural Optimization chez Ansys.
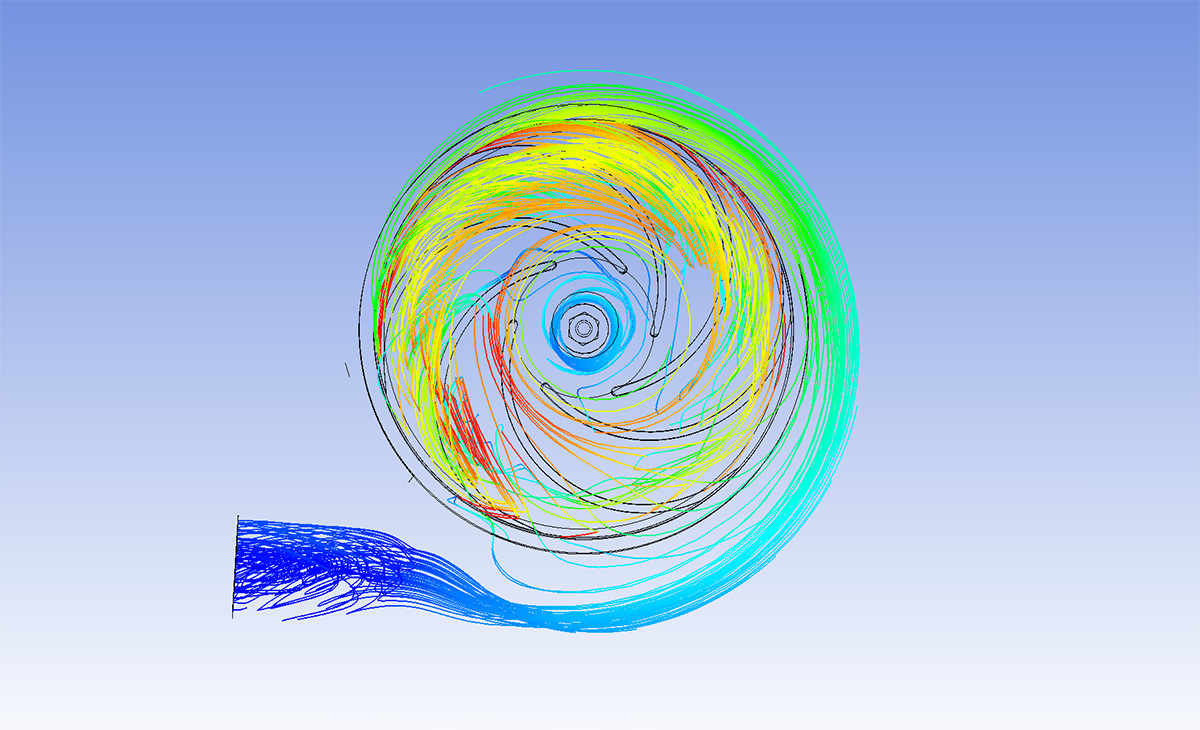