It is no secret that an aircraft is a complex system that involves a long list of interior and exterior components designed to maintain safety, meet certification standards, ensure functionality, and enhance comfort. Given the competitive and demanding requirements of such a large industry, production optimization and efficiency are continuously of paramount importance – hence the increasing push for manufacturing processes such as Additive Manufacturing (AM). Since the very first use of the technology in the 1989s, there has been an increasing shift in how aerospace parts are conceptualized, designed and produced. The article below aims to understand how the technology has evolved and how it’s being adopted today by aerospace companies and part manufacturers.
As one of the first industries to adopt AM and given the number of growing applications achieved in the field, one can legitimately say aerospace has successfully integrated the technology into its production operations. If design and manufacturing are two different aspects of a part production; one cannot truly work without the other. They reinforce each other to generate the biggest impact and it’s important to see how they evolve with the current advancements of the technologies.
Therefore, the article below ambitions to understand:
- The current state of design in aerospace parts production – and applications revealing the greatest impact of AM
- Which AM processes are transforming aircraft production the most and why?
- How far can AM be taken in the aerospace industry?
The current state of design in aerospace parts production
When you look at a wing rib for example – a structural part inside an aircraft that helps to carry some of the flight loads and maintain the smooth shape of the wing. With 2 metre long and 20 kg, this part has a complex shape that needs to be as light as possible to be the most functional. It used to be manufactured using machining in a single block of aluminum until engineers explored the AM route. With AM, they imagine a new design – a metal plate that is used as a base to build the part on. Where possible the part is designed so that the plate can be incorporated into the final part. Using WAAM, the AM part came out with a slightly wavy surface that still needs to be machined to deliver the final part.
This example shows that the right design must go hand-in-hand with the right production process. In aerospace, parts are complex and made up of intricate geometric structures. They form small parts that must fit together with other small parts. If the ability to produce several parts at once is one of the most cited benefits of “design for AM” – especially in the aerospace industry, one should note that the result of these designs often comes down to the use of the right design strategy.
The only thing the design toolbox includes more and more complex techniques that require taking into account the business case perspective of the part being produced. Based on the example shared above, one can say “part consolidation” is one of the design techniques that is widely used in aerospace design to help save weight and assembly costs, while increasing the structural integrity of an AM part.
In general, “AM design techniques and design strategies for aircrafts are being adopted differently in sectors like civil aviation, space, and ultralight aircraft vehicles in the context of urban air mobility and eVTOL.
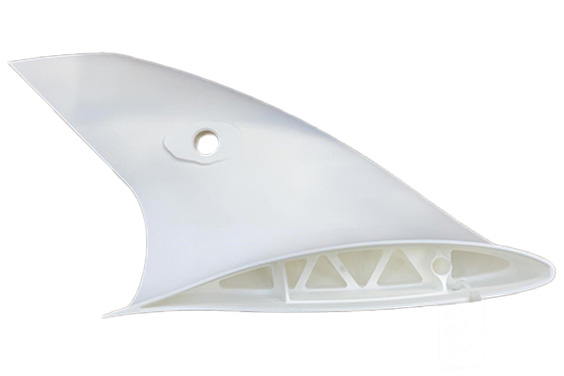
For ultralight aircraft vehicles, saving weight is, of course, a crucial element. AM supports this with proven design techniques like topology optimization, and all of AM’s design opportunities are considered for components, including structural parts, and in different materials. AM is being utilized exhaustively for structural optimization and lightweighting. We see a similar situation for space applications. In both areas, making optimal use of the design space while optimizing weight to functionality is essential. An interesting approach in this context is to switch to a lighter material or composite during the design exploration phase and compensate for its deviating material properties with geometric changes to the part design. In essence, AM is considered a valid manufacturing technology and is used as a complementary technology for a limited number of sophisticated solutions.
Looking at civil aviation the situation is different. Currently, the majority of the 3D-printed parts are not designed for AM. AM is ideal for sourcing low-criticality polymer parts for aircraft in civil aviation because parts can be printed off the virtual shelf, there’s no waste, and no stock languishing in warehouses. However, existing designs are used and produced with AM, because it makes sense from a lead time or minimum order quantity point of view.
Nonetheless, AM offers a new approach to designing for aerospace by providing an economical alternative for damage-prone parts on planes. AM can provide tailored repair solutions for such parts, offering a path other than replacement and minimizing the time planes would otherwise be grounded.
This shows it’s not always about finding the complex parts that require a complete redesign but the parts that make sense from a business case perspective. The right design approach is essential in this regard. Entirely redesigning a part is an investment, and the new design will require additional efforts to be accepted as a flying part. MROs and airlines are implementing Materialise’s AM software to digitalize the production process and use the data available of thousands of builds from Materialise manufacturing to standardize designs and comply with safety regulations. Redesigning existing parts often doesn’t have to rely on highly complex AM design technologies and only requires minor part changes. In civil aviation, safety is the primary concern, and the aerospace and AM industry must advance the standardization of 3D printing to raise its profile for civil aviation,” Erik de Zeeuw, Market Manager Aerospace, Materialise explains.
Two other techniques that have also helped aerospace design evolve are Generative Design (GD) & Topology Optimization (TO). Not only have they been around the longest, they also show immediate benefits when it comes to show immediate benefits in terms of saving weight and increasing value when using AM.
AM processes that are transforming aircraft production the most – and applications revealing the greatest impact of AM
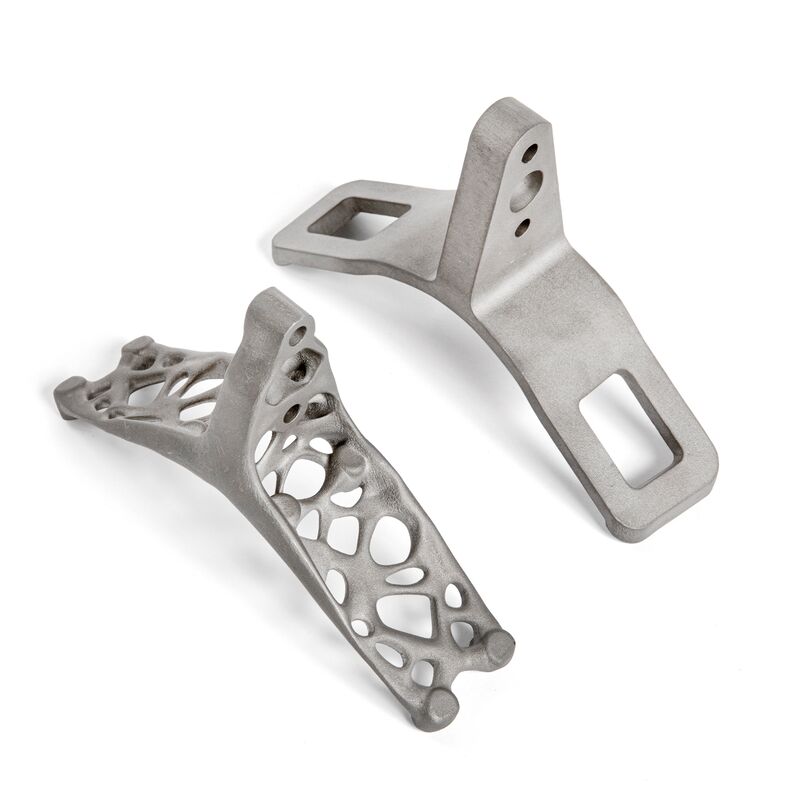
The number of aerospace parts flying today varies from one aerospace company to another and depends on several factors including the period when they start using the technology. Boeing for instance, one of the key industrial players driving the advancement of AM, has already produced over 70 000 3D printed parts, compared to space company Maxar which has already sent over 2,500 additively manufactured parts on orbit, compared to Collins Aerospace, another relatively new entrant who has already produced over 75 production 3D printed parts and opened a $14 million Additive Manufacturing center last year.
When we look at these stats, it is clear that aerospace companies using AM have clearly understood the value proposition AM brings to lightweight parts, functional prototypes and tooling. It is also clear that they are willing to push the use of AM beyond prototyping, to focus on functional parts that can directly be used in an aircraft.
From a technology perspective, materials associated with aerospace parts are both metallic and polymer, depending on the criticality of the part. If polymer materials can be used across different AM processes, their selection still depends on how much they can achieve lightweight requirements with high strength in order to reduce emissions, save fuel, and adhere to the safety requirements. That’s the reason why, SLA and FDM will remain ideal production candidates for producing prototypes. In the same vein, although SLS 3D printing, and LFAM can be used to produce respectively components like air ducts, and other forms of aerospace tooling, an increasing focus remains on the use of metal 3D printing technologies to achieve production parts.
With over 18 different metal AM processes known to date, laser-based powder bed fusion technologies remain the most widely used AM processes. New metal 3D printing technologies continue to pop up on the market every day, and they come with great expectations in terms of cost reduction and production time. Furthermore, since the development of new technologies is faster than the applications they can enable – this makes it difficult to assess the maturity of other metal AM processes that are transforming aircraft production today.
GKN Aerospace, a multi-technology tier 1 aerospace supplier relies on an AM technology that involves layer-by-layer construction using metal wire or powder fused together with lasers. Large-scale laser metal deposition with wire (LMD-w) enables the production of complex and lightweight structures. These structures optimize the overall performance of aircraft components, contributing significantly to weight reduction, fuel efficiency, and the ability to create intricate geometries that were previously challenging with traditional manufacturing methods.
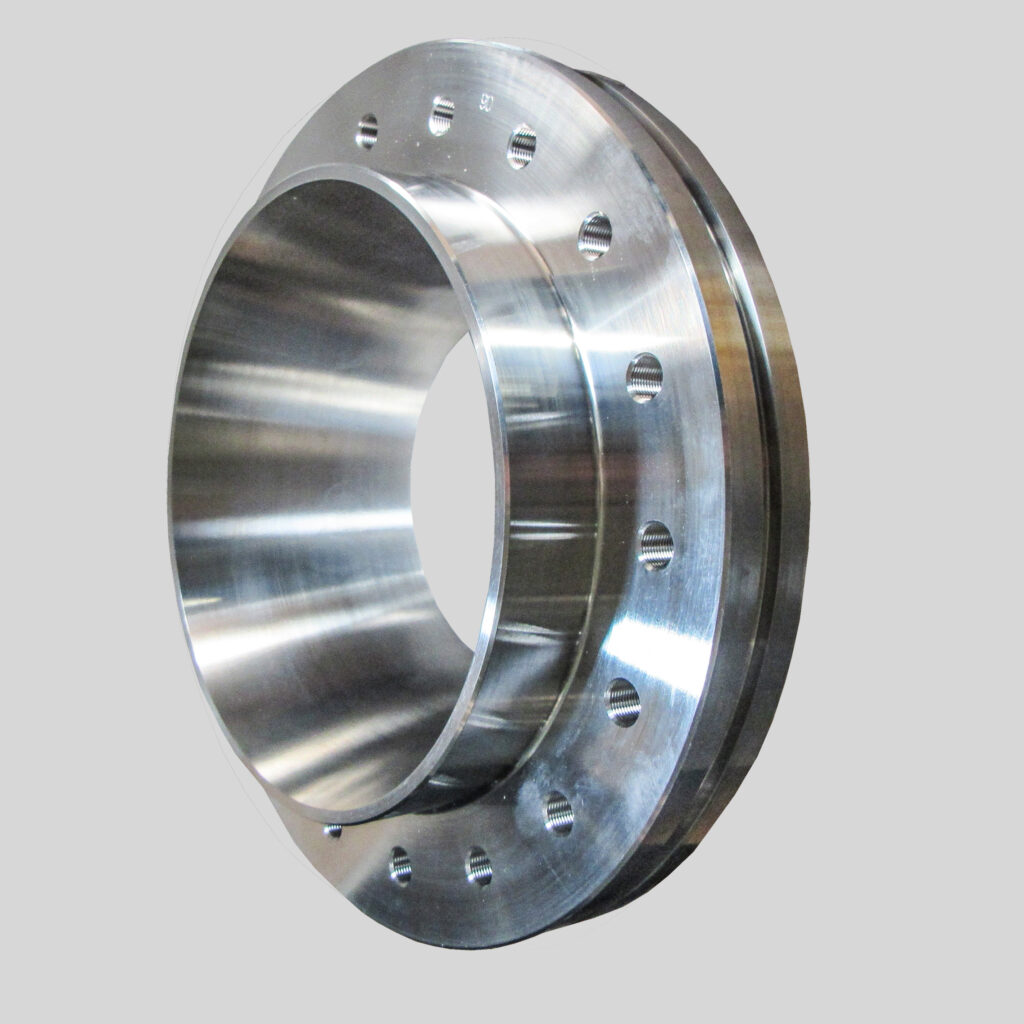
According to Sébastien Aknouche, Responsible for Material Solutions at GKN Aerospace in Sweden, today when we look at aircraft engines especially, no what AM process one leverages, to appreciate the impact of the technology on aircraft production, one must be able to identify in the short term, the following transformation factors:
- The lead-time of demand – design – make – deliver. It is probably down to 5%, maybe even less, of the traditional approach for a new demand.
- There are fewer steps in the process than the traditional manufacturing of aircraft parts
- AM allows us to utilize the already limited global availability of super alloys significantly more efficiently. We may produce 2 to 10 times as many engines with the same amount of metal. This again reduces the amount of waste material (carvings)
- Through AM, the lead time for industrialized production is just a fraction of traditional productions lead-time, where any change in demand may take over 2 years to meet.
- AM allows for rapid changes in demand and a much more flexible supply situation. This will allow for much smaller inventory and unlock a huge amount of cash currently tied to inventory
- AM allows for less cost to the customer through higher flexibility of supply, less cash tied to inventory, higher security of supply with less under-absorption and much faster process from new product to industrialized process
- Any AM production process provides for a significant and positive environmental factor. The CO2 emission is substantially less through less energy-demanding processes and less shipping, and the utilization of our global resources is significantly more effective
That being said, aircraft parts must undergo a certification process to be deemed suitable for flight operations. These certifications may come from FAA, EASA, IASA depending on the region where the part will be used. The paradox is, although metal AM technologies are the processes that drive the most the growth of AM in aerospace, the validation process for any metal component remains quite long. This may take 7 to 10 years compared to plastic 3D-printed parts.
When asked if there are lessons one can learn and replicate from plastic 3D printed parts to advance the use of metal 3D printed parts, Aknouche said these lessons could be “adopting a more iterative testing approach, leveraging simulation tools for virtual testing, and establishing standardized testing protocols. By incorporating these practices, the aerospace industry can potentially reduce the validation timeline for metal components, ensuring safety and compliance without compromising efficiency.”
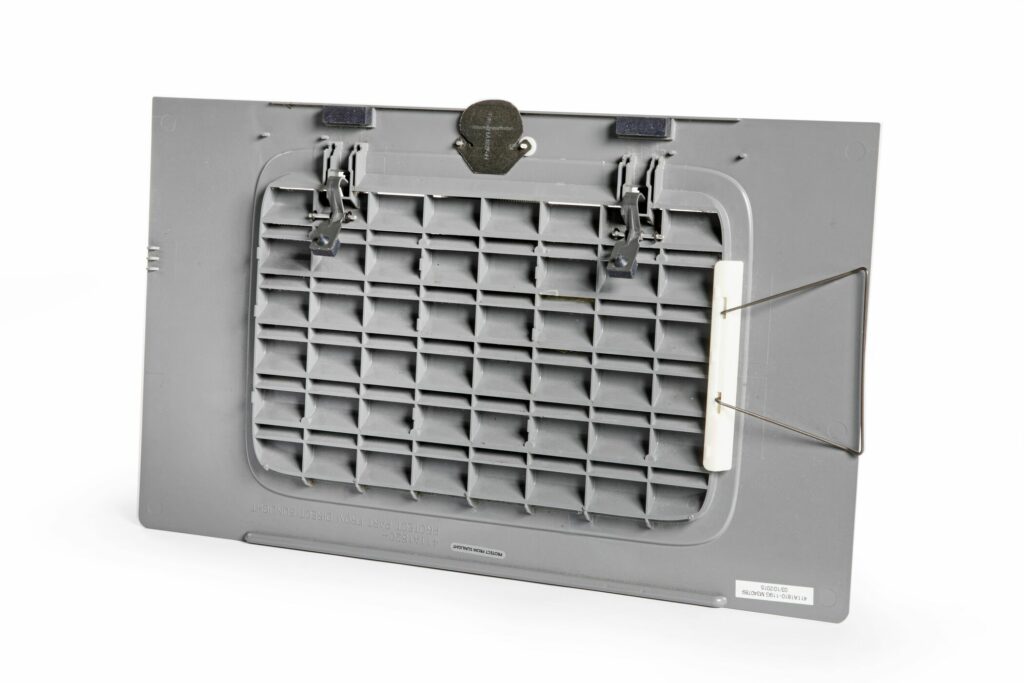
Nevertheless, the applications revealing the greatest impact of AM remain those complex, lightweight components such as engine components. “These parts benefit from the design freedom offered by AM processes, resulting in improved performance, fuel efficiency, and reduced environmental impact. Moreover, the ability to consolidate multiple components into a single, intricately designed AM part contributes to overall weight reduction and increased aircraft efficiency,” GKN Aerospace expert adds.
Outside of the metal AM segment, Erik de Zeeuw notes that “low-criticality polymer parts or parts prone to breakage in and around the aircraft are perhaps where AM stands out the most in terms of impact. One such example is the cabin decompression panel on the Boeing B737. The latches and pins on the panel tend to break frequently. Stirling Dynamics worked with Materialise to design a reinforced panel that had the same functionality but was stronger and less likely to break than the original part.
These low-criticality parts are not just the bread and butter of AM for aerospace. They also provide the data required to work on high-criticality parts. This data is being used by aerospace companies today to ensure repeatability in their manufacturing processes.”
How further can AM be taken in the aerospace industry?
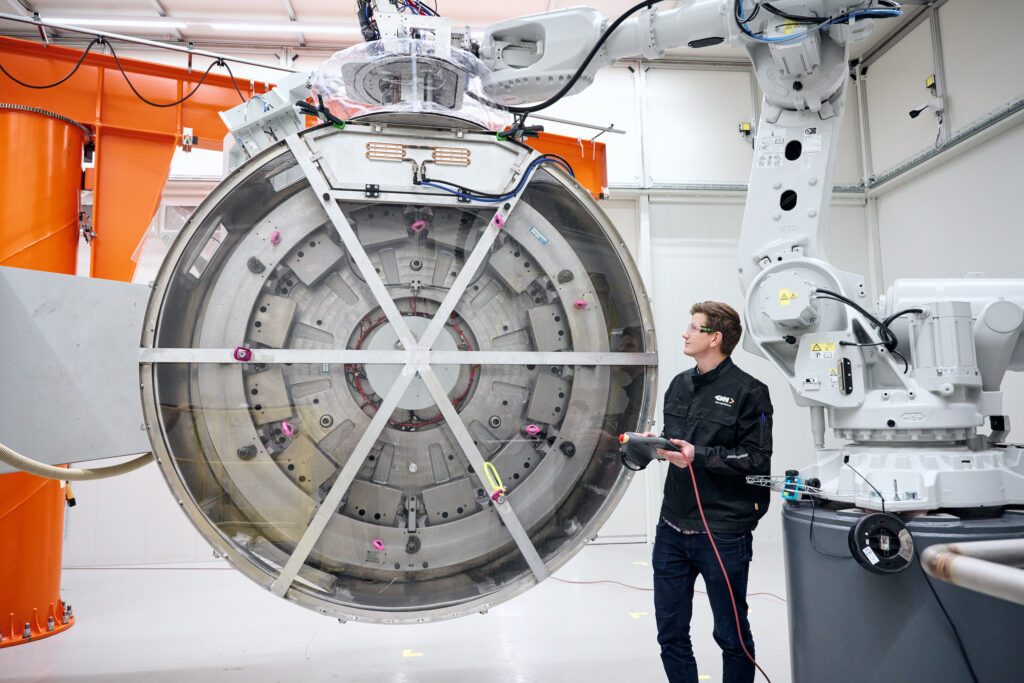
Based on our conversations with experts invited to share insights into this topic, one would like to keep in mind three main areas of interest: new designs, aircraft structural components, and the buy-to-fly ratio.
When we look at design, the most important transformation factor that will help propel the adoption of AM in aerospace is new designs. According to Aknouche, “new designs of jet engines, for example, will make them lighter and more effective and thus save CO2 emissions every minute the airplane flies. “Even though we have been able to design and calculate the advantages of a future vision of new engines, we have not been able to realize them until metal-based AM was introduced,” he outlines.
As far as aircraft structural components are concerned, we have seen examples of 3D printed parts whose design is the perfect replica of the same part previously produced through machining. One of the challenges we often see is that, sometimes, the complete redesign of the part to achieve the well-known advantages of AM makes it complicated or “impossible” to achieve a part with intricate 3D-printed forms that could be certified. Indeed, given its stringent regulatory requirements, it’s easier for the aerospace industry to certify a part design and maintain that design throughout the entire lifespan of the aircraft. Add the problem of quality assurance, you reach another level of complexity to demystify. For this reason, despite the potential of AM for structural parts, we might need to wait a bit longer, for new parts, with new designs for new aircrafts to pop up before saying we’ve reached a new level of maturation of the technology.
“AM and Materialise haven’t rushed to tackle the high-criticality metal structural components market. Part of that is due to the strict safety regulations that are necessary in the aerospace industry, but some of it has to do with the readiness of the 3D printing technology itself. However, with Materialise’s track record of providing low-criticality polymer parts, the data now available through our work, and the investments by major aerospace companies such as GKN, AM is being considered for structural aircraft components. The winglet of the Aviation Alice aircraft designed by GKN is just one example of work in this space. In parallel, Materialise and other partners are working to create a path to qualify the process of producing metal AM parts. The group consisting of aerospace and AM experts will provide a whitepaper as a first effort to author an SAE Aerospace Recommended Practice for using in-situ process monitoring to validate an AM process. Such efforts will drive the technological readiness of AM and motivate more aerospace companies to consider AM for high-criticality parts in airlines”, de Zeeuw comments.
As for the buy-to-fly ratio, GKN Aerospace’s expert confirmed “improved buy-to-fly ratio” could be a key transformation factor in the industry in the long run: “the weight ratio between a substrate and a completed part) will enable us to utilize available metal even more efficiently with even less waste. Indeed, there is a reduced waste of material the more the AM process becomes efficient, and the more the “buy-to-fly” ratio moves closer to 1,0.”
“There is probably no clear border to where we may end up, but we will not be able to make parts with no material, but maybe parts with a “buy to fly ratio close to 1,0”, and will not have lead-times down to zero, but very short, and the production will probably not have zero emission, but very little. The question is more how close to that ideal stage will we get? The answer to that one will have to follow the development to find out”, he concludes.
Obviously, other areas of interest could have been mentioned. In the end, let us not forget that the way AM advances, depends on the player that is making use of it.
This dossier has first been published in the 2024 January/February edition of 3D ADEPT Mag. Featured image credit: GKN Aerospace.
Editor’s notes
GKN Aerospace and Materialise are collaborating on several projects to address certification and additive production of functional and flight-critical aerostructures. However, none of the companies was aware the other one was participating in this dossier.
GKN Aerospace has been invited to share insights into this topic as its expertise lies in leveraging AM to optimize aircraft design and production processes. The company said its latest project involves the development of advanced AM techniques for critical structural components, showcasing the profound impact on both design flexibility and manufacturing efficiency. By integrating AM into our workflow, we have achieved notable advancements in weight reduction, part consolidation, and overall system performance.
As for Materialise, it has now fully matured its aftermarket offering for low-criticality cabin parts. Over the last 10 years, they have gained an enormous data lake proving the consistency of the technology, process, material, and machines we operate. Although we certified the process some five years ago, getting printed parts on an existing aircraft is not as easy as it may sound given the strict requirements of the industry. The company continues to collaborate with aerospace companies to advance key areas of improvement in the aerospace industry. Apart from GKN Aerospace, one of its recent partnerships was signed with Stirling Dynamics.