Lors d’une conversation récente, Brian Baughman et Curtis Swift de Honeywell Aerospace, ont partagé avec 3D ADEPT Media que leur équipe s’appuyait sur l’impression 3D céramique pour créer des moules. L’équipe d’ingénieurs a continué à approfondir son expertise de cette technologie et fournit aujourd’hui des informations supplémentaires sur leur processus.
« Traditionnellement, les pales de turbine sont fabriquées par un processus de moulage à la cire perdue que seules quelques fonderies dans le monde peuvent gérer », a déclaré Brian Baughman, ingénieur en chef de la fabrication chez Honeywell. « Il s’agit d’usiner des matrices et des outils métalliques extrêmement complexes pour créer des moules en céramique, qui sont ensuite coulés avec un superalliage en fusion pour former les pales. »
Grâce à l’impression 3D haute résolution par photopolymérisation VAT, il est possible de traiter la boue céramique et d’imprimer directement les moules. L’imprimante 3D développée par l’équipementier Prodways est basée sur la technologie propriétaire de l’entreprise appelée MovingLight et aurait déjà servi à la fabrication de plusieurs composants de moteurs d’avion dans l’industrie aérospatiale.
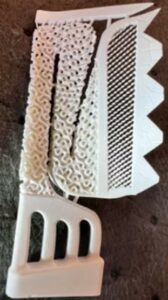
« Avec le processus conventionnel de moulage à la cire perdue, la production des aubes de turbine nécessaires au processus de développement peut prendre un à deux ans », a déclaré Mike Baldwin, chercheur principal en R&D. « La fabrication additive nous permet d’accélérer le processus de production et de réduire les coûts de production. La fabrication additive nous permet de prendre la conception, d’imprimer le moule, de le couler, de le tester et d’obtenir des chiffres réels pour valider nos modèles, le tout en seulement sept à huit semaines. Si nous devons modifier la conception, nous pouvons le faire électroniquement et obtenir une nouvelle lame en six semaines environ. Avant l’impression 3D, toute modification, même mineure, de la conception des pales pouvait s’avérer très coûteuse. « La fabrication additive permet un prototypage rapide et nous donne une plus grande flexibilité pour accélérer le développement, gérer les coûts et créer le meilleur produit possible pour nos clients. La réduction de la durée du cycle de développement est notre principal objectif, mais nous prévoyons également d’économiser plusieurs millions de dollars en coûts de développement par rapport à l’utilisation du processus traditionnel de moulage des pales. »
Alors que l’équipe d’Honeywell Aerospace utilise la ProMaker Ceram Pro 365 – une imprimante 3D installée l’année dernière sur leur site, le groupe Prodways a déclaré que malgré les progrès récents qui ouvrent des opportunités commerciales sur un marché adressable très important pour l’impression 3D de pièces en céramique, à court terme, ils restent prudents quant aux perspectives de ventes d’imprimantes pour cette application.
« Les faibles volumes posent souvent problème, car le coût initial de l’outillage pour une pale de turbine est très élevé et la fabrication nécessite un long délai. La fabrication additive a beaucoup de sens dans des cas comme celui-ci », rassure Baughman.
N’oubliez pas que vous pouvez poster gratuitement les offres d’emploi de l’industrie de la FA sur 3D ADEPT Media ou rechercher un emploi via notre tableau d’offres d’emploi. N’hésitez pas à nous suivre sur nos réseaux sociaux et à vous inscrire à notre newsletter hebdomadaire : Facebook, Twitter, LinkedIn & Instagram !