Thanks to the use of 3D printing, GKN Driveline Florence reports 70% reduction in production time of certain tools, eliminating costly downtime of the production line and ensuring business continuity.
The specialist in additive technology solutions makes use of Stratasys’ 3D printing technologies and will expand its deployment across the manufacturing floor to replace several traditional production processes. Once more, the manufacturer proves its ability to be efficient in a wide range of sectors.
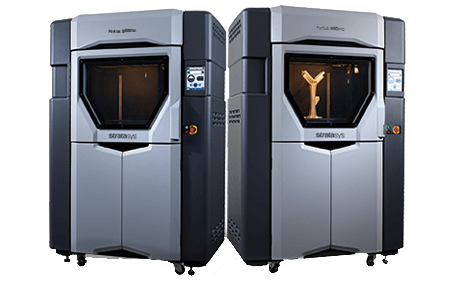
As far as this reduction in production time is concerned, notice is to be made that 3D printing customized assembly tools in place of traditional plastic and several low-loaded metal tools.
GKN Driveline provides its services to over 90% of the world’s car manufacturers. With a portfolio which includes clients such as luxury vehicles from the likes of Maserati and Ferrari or the Fiat Chrysler Automobiles Group, business competition is rude in the services.
To give a specific illustration on a project, Carlo Cavallini, GKN Lead Process Engineer and Team Leader at the Florence plant, said: “utilizing our 3D printer, we developed a tool that dramatically improves grease distribution and eradicates the need to clean up time-consuming spillages. This has been crucial to streamlining the production cycle of the half shaft, enabling us to provide customers with premium quality final parts.”
“As we continue to design parts specifically for additive manufacturing, we are finding more and more applications that are delivering value. In the future, I believe that FDM 3D printing will become an integral part of our entire tool development cycle and help us further improve business performance,” he adds.
For further information about 3D Printing, follow us on our social networks and subscribe to our newsletter!
//pagead2.googlesyndication.com/pagead/js/adsbygoogle.js
(adsbygoogle = window.adsbygoogle || []).push({});