GKN Aerospace just signed a five-year research agreement for $17.8 million with Oak Ridge National Laboratory (ORNL).
Both parties will make use of ORNL’s Manufacturing Demonstration Facility (MDF) to develop research on the industrialization of additive manufacturing. The research has two main goals:
- the first one consists in developing the laser metal deposition with wire (LMD-w). This process aims at creating a prototype capable of manufacturing complex, medium- to large-scale titanium aircraft structures by melting metal wire into beads to obtain an object layer by layer.
- The second goal concerns the advancement of electron beam melting (EBM). It will not only support work that is already in progress; but will also improve volume aerospace production.
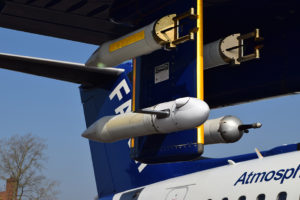
Mike Grunza, CEO of GKN Aerospace’s Aerostructures North America business shares his joy: “We are extremely proud to work with the world-renowned Oak Ridge National Laboratory to speed progress towards fully industrializing these processes. Additive manufacturing will continue to increase its vital role in engineering design spanning civil and defense aviation, revolutionizing the design and manufacture of structures across the entire airframe and engine. Additive processes could cut material waste by as much as 90 percent and manufacturing times by around 50 percent and will unlock new manufacturing horizons, allowing us to create complex components with no performance compromise.”
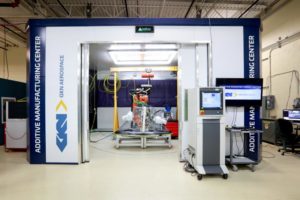
As far as testing 3D printed components are concerned, GKN launched the Optical Ice Detector (OID), an ice protection system, on the Atmospheric Research Aircraft operated by the Facility for Airborne Atmospheric Measurements (FAAM) in Cranfield, UK.
The OID’s small sensor head has been made using additive manufactured titanium. It can be placed into an ice accreting surface on the aircraft, or in the internal areas of gas turbine engines.
The flight is then the first test of GKN’s Type 8 Spraymat Ice Protection heater mats.
This successful first flight of GKN’s OID technology was the result of positive collaboration between our additive manufacturing and ice protection teams and marks a significant milestone in maturing the capability,” declares Russ Dunn, Senior Vice President of Engineering, Technology and Quality for GKN Aerospace.
//pagead2.googlesyndication.com/pagead/js/adsbygoogle.js
(adsbygoogle = window.adsbygoogle || []).push({});