In what has become an annual tradition for the Additive Manufacturing world, Mesago, the organizer of Formnext, hosted this year 864 exhibitors (of whom 61% were international), and 34.404 visitors (of whom 48% were international) in Germany’s financial capital, from November 19 to 22, 2024. These figures show a slight increase compared to the same event last year.
For the first time in many years, I went to Frankfurt without any strict schedule. Many had highlighted the fortuity of encounters as one of the key strengths of Formnext, and I wanted to experience how true it is.
Although we couldn’t tell it by the fancy booths, most of my conversations shed light on the economic downturn AM companies have to overcome – even from those I didn’t expect. I couldn’t help but think that any experienced marketer would say, the more a company struggles, the more it should invest in marketing.
While it is not my place to testify to the veracity of this assertion, my eyes were attracted by a number of manufacturing strategies I found interesting to explore, applications and newcomers, an increasing focus on large-scale manufacturing and the rising presence of Asian companies.
Manufacturing strategies that are worth noting
With over 800 companies, it’s easy to get trapped in the wave of product launches usually highlighted across the different booths. In an effort to do things differently, or let’s say, to see different results obtained with existing processes, we spotted different manufacturing strategies that highlight the importance of combining two manufacturing techniques; we also spotted different solutions to increase productivity and simply new solutions that could enhance part production.
Combination of two manufacturing techniques: AM + traditional manufacturing processes
In the wide range of processes that could be combined, it’s easy to see the combination of metal Additive Manufacturing and CNC Machining. At Formnext, specialty chemicals company Altana drew my attention to applications one can achieve by combining AM with injection molding. Since the split with dp polar, Altana has been focusing on the development of high-performance resin materials suitable for DLP, LCD and SLA 3D printing technologies. At Formnext, the company demonstrated it is possible to save costs in tooling by showcasing a power socket manufactured with injection molding and AM. As per the explanation of Dr. Anne Asmacher, Project Leader in the AM team, the outer part (the frame) of the power socket has been injection-molded as it is a standard design produced in injection molding. The center part, the cardholder or the switch can have tailor-made designs – and thus can be manufactured via AM before the final assembly. In this case, the center part was produced using AM and Altana’s High Performance 4-6700 VP. Ideal for final parts production, the material provides a good balance between toughness and impact resistance.

Another key highlight at their booth was the use of indirect 3D printing to close the gap between small series and high-volume applications. The picture below is a good example of that. The mold has been produced by AM service provider rpm – rapid product manufacturing using Altana’s Mold 3000 VP. The water-breakable cast material is part of the series of One-Shot-Molds (OSMs) for usage in injection molding applications. The enhanced water affinity facilitates easy mold removal in water or aqueous environments. Additionally, it minimizes unwanted swelling, helping to prevent deformation or cracking of the final part. These 3D printed molds were thereafter used for the production of Harting’s connector parts. Ideal for medium and long runs, this type of manufacturing process allows for greater flexibility in engineering designs.
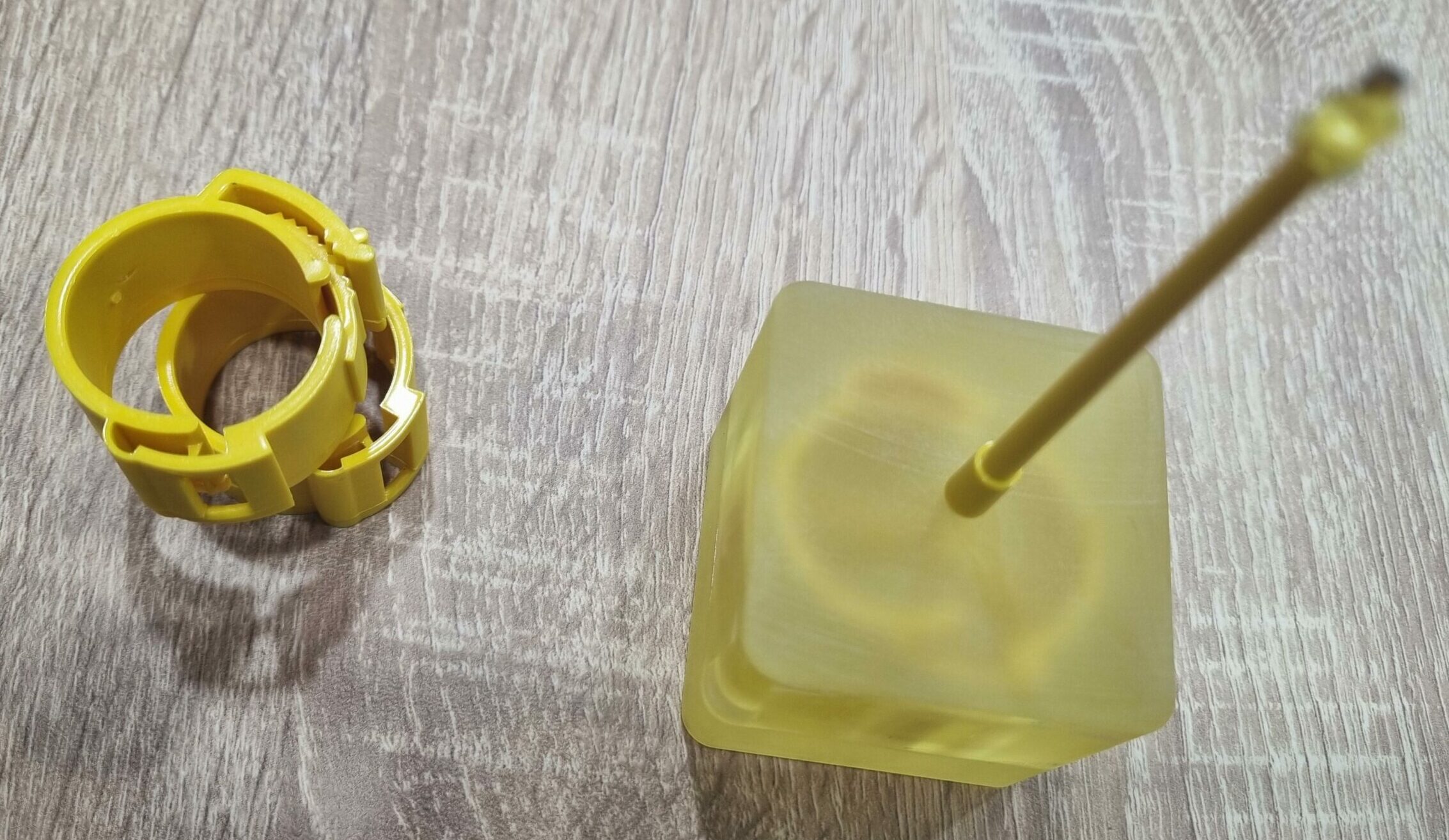
Combination of two AM techniques
When we talk about combining two manufacturing processes, the first idea that comes to anyone’s mind is the combination of AM and a conventional manufacturing process. Graham Matheson, R&D Project Manager at Oerlikon, piqued my interest in the Disco 2030 project. The project involves 9 partners among which Oerlikon and aims to combine the advantages of PBF and DED to enable the manufacturing of multi-material lightweight, complex geometry components that can operate in harsh environments. At the Oerlikon booth at Formnext, one could see a section of the combustion chamber whose parts were printed separately with DED and LPBF before being assembled.
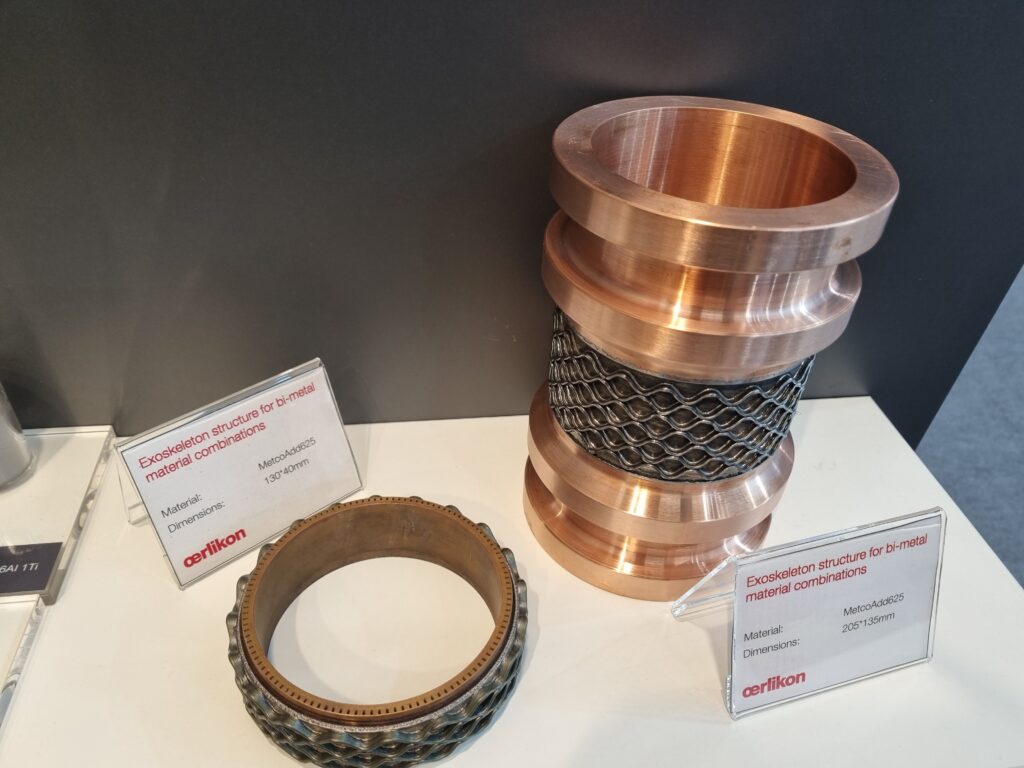
According to Matheson, such manufacturing is all about applying DED on powder bed copper parts. It comes to answer a problem faced by multi-material joining techniques such as brazing, solid-state welding or mechanical joining. With these techniques, industrial designers have to deal with machining the parts first (made of different materials), before joining them with the ideal technique in a second step. The problem in proceeding this way, is that this may negatively affect the design freedom of multimaterial devices and create “dead spaces” in areas where two dissimilar materials are joined, thus negatively impacting the part’s weight. Furthermore, it does not allow “graded” materials to perform at their best. By combining DED and PBF, the research team can deliver locally optimized material properties that can fulfill specific functions. There is still a long road ahead before the DISCO2030 Project becomes a manufacturing standard in Europe, but if it does, it will likely replace traditional methods such as die casting and mechanical assembly of multiple parts.
Increasing productivity with AM
Any production manager will tell you that any time spent on activities other than manufacturing components is viewed as unproductive waiting time. Over the years, OEMs have developed solutions that could enhance productivity inside and outside the build chamber. These solutions are enabled through automation in powder bed processes.
Machine manufacturer pro-beam GmbH showcased at Formnext how it could increase productivity with up to three build units – allowing industrial users to ensure production 24/7h within their facility. This solution will benefit automotive manufacturers and industries that are looking to achieve series production with AM.
Enhancing part production through new post-processing technology
Among the various tools that can be used to enhance part production, I have always found post-processing technologies more tangible as it is easy to assess their capabilities. At Formnext, SUGINO, a Japanese newcomer in the AM market, debuts its CASF solution.This processing solution stands for Cavitation Abrasive Surface Finishing, and helps to remove abnormal layers from the surface of objects, perform surface smoothing and imparting compressive stress due to the cavitation effect by injecting high-pressure water in a tank filled with abrasive suspension.
Akiteru Tsuiji, Managing Director of the German subsidiary told 3D ADEPT Media that abnormal layers such as poor melting and cavities that occur from the surface layer to a depth of 200 um can be removed together with surface smoothing treatment and compressive stress. This results in increased fatigue strength and better fatigue life of the final part.
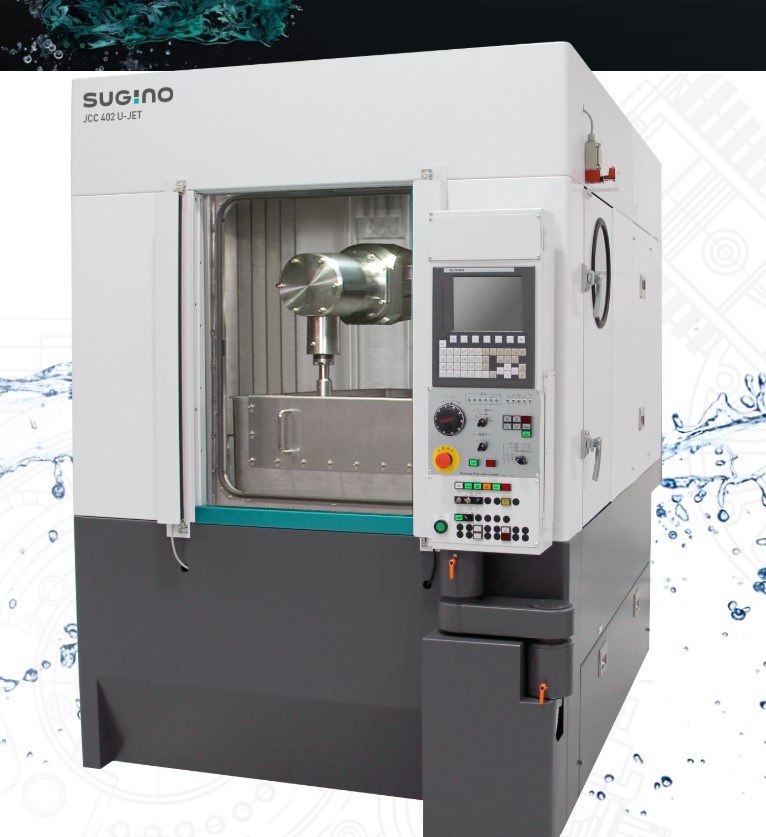
Newcomers and applications
With the wide range of solutions that continuously pop up in the market, we’ve made it a rule to shed light on newcomers that are taking their first steps in our industry. In addition to SUGINO, we also discovered UNIWAY, a Turkey-based resin 3D printer manufacturer who debuted at Formnext. With a key focus on the jewelry industry, Mustafa DULGER, General Manager of Uniway, explains that their wax-based 3D printer can achieve 30% more output in one print job.
Another rare find of the show was Carboganic, a Belgian startup that develops different biocarbon based FGF and filament 3D-printing compounds in various polymer formulations (PET, PP, ABS, PLA,…). These materials are used across different fields, such as orthopedic applications, automotive, yachting, construction, furniture and more. To demonstrate the capabilities of their solutions, the company showcased during the show a mold for an electric racing car and seat shells for wheelchairs.
On a different topic, a variety of applications helped to demonstrate companies’ expertise and solutions. While it is often complicated to shed light on applications delivered for the defense industry, we can’t help but notice that more and more companies are serving that industry.
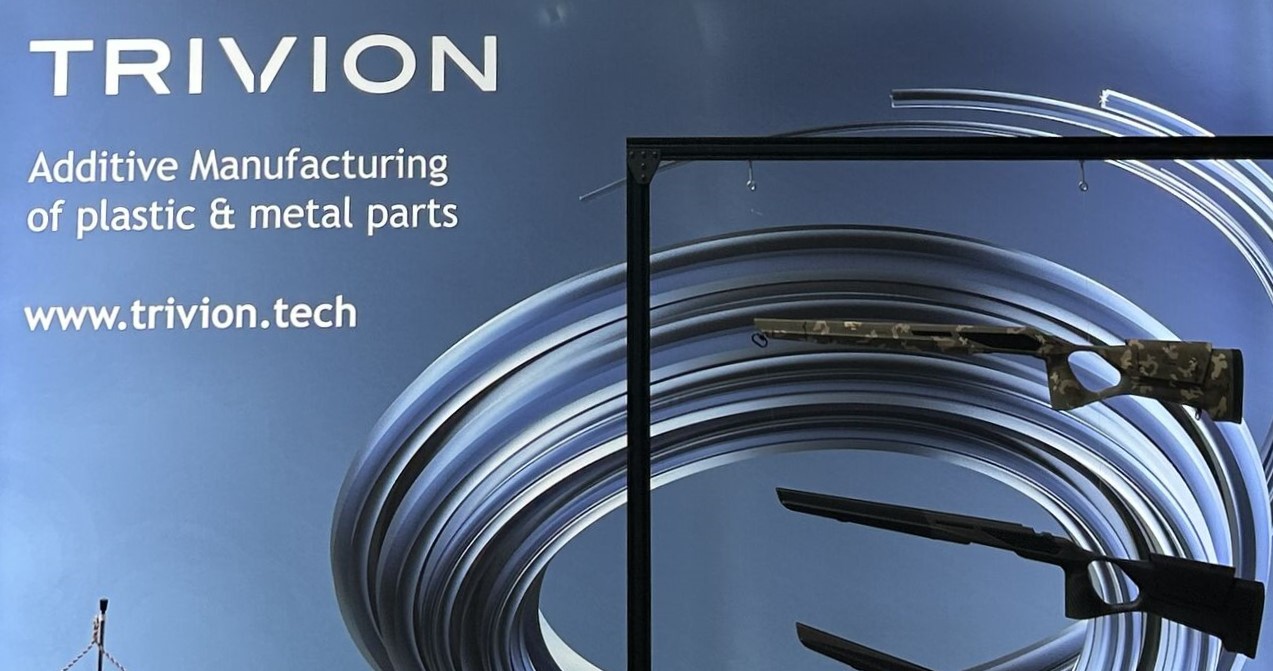
That being said, from medical and dental technology to the packaging, automotive and mechanical engineering industries, and from architecture to aerospace and many other sectors: the broad applicability of Additive Manufacturing across numerous industries was strikingly demonstrated by the multifaceted supporting program and the various showcases.
The bad and the good in the rise of Asian companies
While Australia was the partner country of this Formnext edition, one should note that there was an increasing number of Asian companies in the show. As a matter of fact, among the 864 exhibitors of Formnext, 145 came from Asia – and out of this number, 101 came from China. These numbers encourage to take a closer look at the different expertises that pertain to each region. While we will dedicate more features to this analysis in the coming year, we can already tell that metal 3D printing developments are standing out from the crowd.
Apart from the VoxelDance Raid that occurred on the third day of the show, emphasizing the stereotype of copycat linked to Chinese companies, one should be able to give other OEMs the credit they deserve as they are going the extra mile to stand out from the crowd.
Imagine a company that would like to leverage 3D printing for prototyping purposes… When I look at the quality of prints delivered by FDM 3D printers like those of Bambu Lab, I don’t see any interest in investing in an FDM 3D printer that costs about or more than 10 000€. To date, Asian FDM 3D printer manufacturers are gradually taking the biggest market shares in this area.
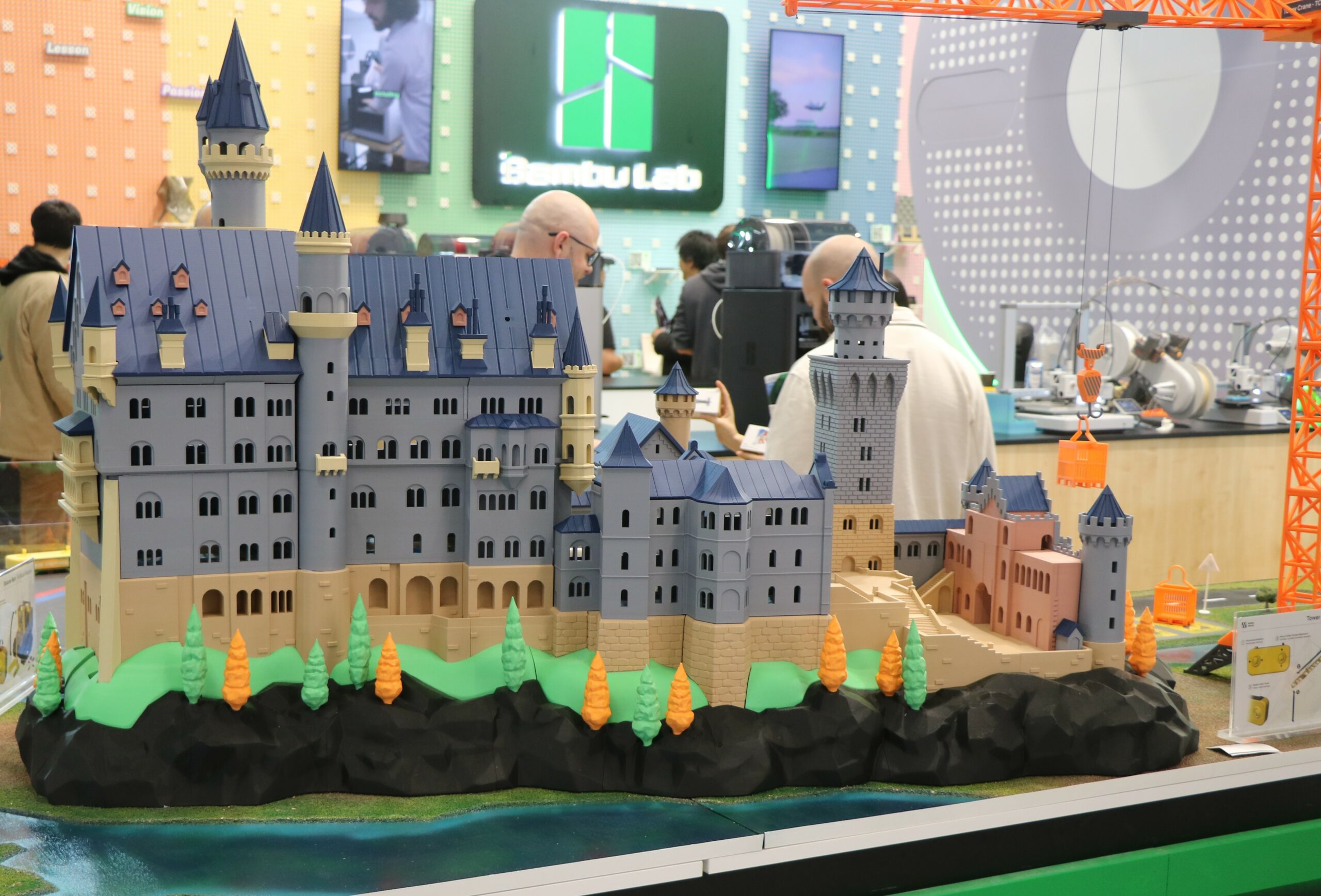
On another note, a quick overview of the profiles of Asian exhibiting companies at Formnext reveals that most companies specialize in the development of industrial machines and materials. With SeeAnn Solution and Aspect, Inc. being the only companies of the continent at the event providing software solutions, we are tempted to think that the development of software solutions is not the greatest strength of Asian companies.
It takes all types to make the world go around, so I guess, if there are not enough software providers in the continent, there are always other solutions elsewhere that could help meet the needs of AM users.
And now?
Innovations at Formnext often made me leave the financial capital with ideas and hope for a better world. I have to admit that I left this 2024 edition of the event with mixed feelings. While the quality of exhibitors and innovations showcased continue to testify to the technology’s potential, the news of KIMYA ceasing filament production and Forward AM filing for insolvency – all of them released during Formnext – highlight a growing uncertainty within our industry.
It’s too soon to provide accurate feedback from all AM companies on this. However, one thing is certain, anything that can help increase faith will continue to help this industry advance, slowly but surely.
Featured image: Mesago / Mathias Kutt. Stay tuned and consult this page for more insights from AM companies exhibiting at Formnext and for all product launches you shouldn’t have missed on the show.