If you went to the dentist in the early 2000s, there is a great chance that you received a crown in metal or gold for your tooth that needed to be restored. Personally, seeing my dentist use a gold or metal material for a crown or a filling is not one of the best memories. A metal crown in the mouth made me feel I was one of these rappers who used to be featured in trending American music videos of the time. Thankfully today, it is possible to have a crown or a filling that perfectly matches the color of our teeth and it took a conversation with Daniel Bomze for me to realize that the secret behind such a solution lies in the use of a glass-ceramic material called Lithium Disilicate.
If you’re a regular reader of 3D ADEPT Media with a keen interest in healthcare 3D printing applications, then the name of Daniel Bomze may be familiar to you. The Director of Medical Solutions at ceramic 3D printing company Lithoz sat down with 3D ADEPT Media last year to discuss the factors to consider when exploring technical ceramics in medical Additive Manufacturing and why they are a good fit for dental applications. One of the key highlights of our conversation was that Zirconia, ATZ and ZTA – all part of Lithoz’ materials portfolio – could be processed with the company’s Lithography-based Ceramic Manufacturing (LCM) technology to achieve the mass production of certain dental applications.
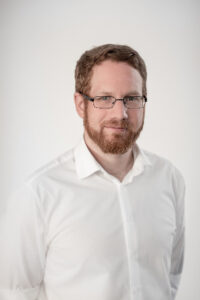
Since our conversation, Lithoz has deepened its collaboration with Metoxit, a Swiss high-tech ceramics company that develops oxide ceramics. Together, they are exploring dental applications with ceramic AM. “With Metoxit, we are currently exploring the use of ATZ (Alumina-Toughened Zirconia) to develop dental implants. Separately, we are also investigating the possibility of producing a wide range of devices such as burrs or milling tools. On the other hand, we are also working with a University on some applications surrounding this topic that we will hopefully release soon. The truth is, a lot of people now go for metal-free solutions when it comes to dental implantology. They pay a lot to have solutions with other materials such as Zirconia and ATZ but their use is often combined with some standard processes. When we realized that some manufacturers also provide some ceramic burrs, we decided to further explore the use of these materials for dental applications achieved with ceramic additive manufacturing – knowing that the advantages of the technology (freedom of design, and the ability to achieve various geometries) will play to our strengths to achieve applications with better results.”
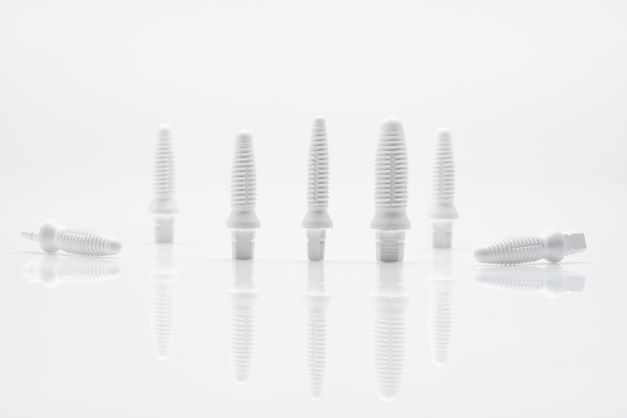
In the same vein, Lithium Disilicate, the glass-ceramic material acknowledged for its translucency (which means it can match the color of one’s natural teeth), is widely used for dental restorations such as crowns and veneers.
The silicate anion (a tetrahedral structure of 4 oxygen atoms around a silicon atom) is the base material of most, if not all glass materials. Lithium is added in form of ions to achieve the desired properties of the dental glass-ceramic compared to standard window glass for example. The developer of the Lithography-based Ceramic Manufacturing (LCM) technology joined forces with Ivoclar, a manufacturer of integrated solutions for aesthetic, high-quality dental applications, to develop this new lithium disilicate material. Based on IPS e.max lithium disilicate powder (IPS e.max meaning it belongs to a family of dental restoration materials used via traditional shaping methods and used because of aesthetics and similar appearance to natural tooth), the material enables the fabrication of veneers as thin as 0.3 mm and crowns with high levels of detail especially at the occlusal surfaces.
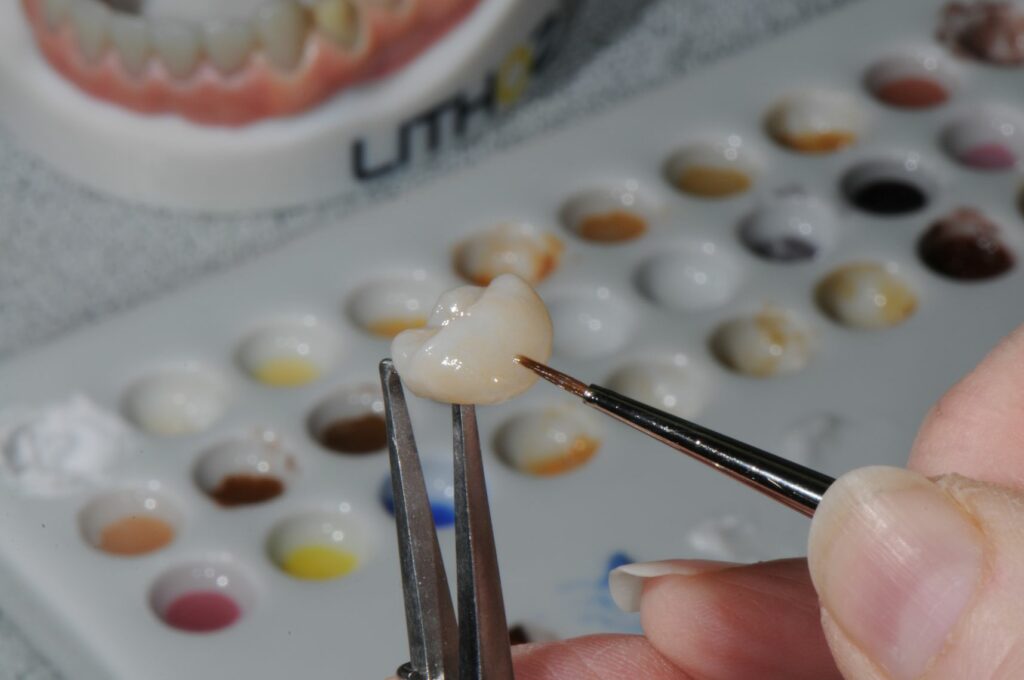
The various manufacturing processes of Lithium Disilicate material
According to Bomze, there are currently three ways of creating restorative dentistry applications with this material –: the most traditional process is heat-pressing. The fabrication process starts with the model of the crown or veneer and relies on the use of a lost-wax technique, a process that is commonly used to cast dental alloys.
Another conventional process that can be used to process this material is milling. It uses diamond burs at high speed to achieve the final restoration shape. Lithium disilicate restorations are milled by hard machining prior to its full crystallization. Heat treatment is thereafter performed to achieve final mechanical and optical characteristics.
And there comes 3D printing. In this specific case, the Lithography-based Ceramic Manufacturing process from Lithoz can fabricate the aforementioned applications using the newly developed Lithium Disilicate material. For those who are not familiar with this process, please note that during this fabrication process, ceramic particles are dispersed in a photosensitive resin and this dispersion is thereafter solidified by light layer-by-layer to form a part. Then the part undergoes a debinding and sintering process to deliver its ceramic properties and can be used for its final purpose.
Our conversation with Bomze enabled us to understand the various pros- and cons- that each manufacturing process brings to the table:
Pros- | Cons- | |
Heat-pressing | There is a chameleon effect that enables to have better optimal properties than zirconia.
Process that relies on the use of a lost-wax technique. Low investment costs for equipment. Known to most dental technicians. Low material costs as ingots are comparably low-priced and several restorations can be made from one ingot. |
.
Limited in terms of accuracy and finishing. |
Milling |
There is a chameleon effect that enables to have better optimal properties than zirconia. The process delivers an improved surface quality to the part. A final flexural strength of approximately 500 MPa. Can be suitable for indirect Class II MOD restorations in various cavity preparation designs. |
According to a research, there is a reduction of about 33% in the characteristic strength of lithium disilicate specimens after milling.
Potential cracks or defects may occur due to stress accumulation or the changing diameter of the burrs. Requires a lot of material during the fabrication process (80% of the material could be wasted here.) Production of one veneer at the time. High material costs of a single restoration. It can take up to five days to get the final restoration. |
Lithography-based Ceramic Manufacturing process |
There is a chameleon effect that enables to have better optimal properties than zirconia. The finishing with AM will be identical to the patient’s teeth.
A lot of material savings. If the milling process wastes up to 80% of “x” amount of material for a given application, ceramic AM loses only less than 10% of material for the same application. Stability of the operation. Better scalability and mass customization: one can produce up to 100 tailor-made veneers at the same time using this material and a CeraFab System S65 Medical 3D printer. Possible to perform a minimum invasive treatment in certain applications. A wide range of applications can be achieved with AM. |
Can take up to two or three days to get the final restoration. |
It is well-known that the nature of ceramic materials suffers from a few problems, such as brittleness, low tensile, bending, and impact strength, which restrict their applications in dental restorations. However, one needs to recognize that 3D printed veneers may deliver the same mechanical properties as pressed and milled lithium disilicate (with a strength that is in the range of 470-530 MPa).
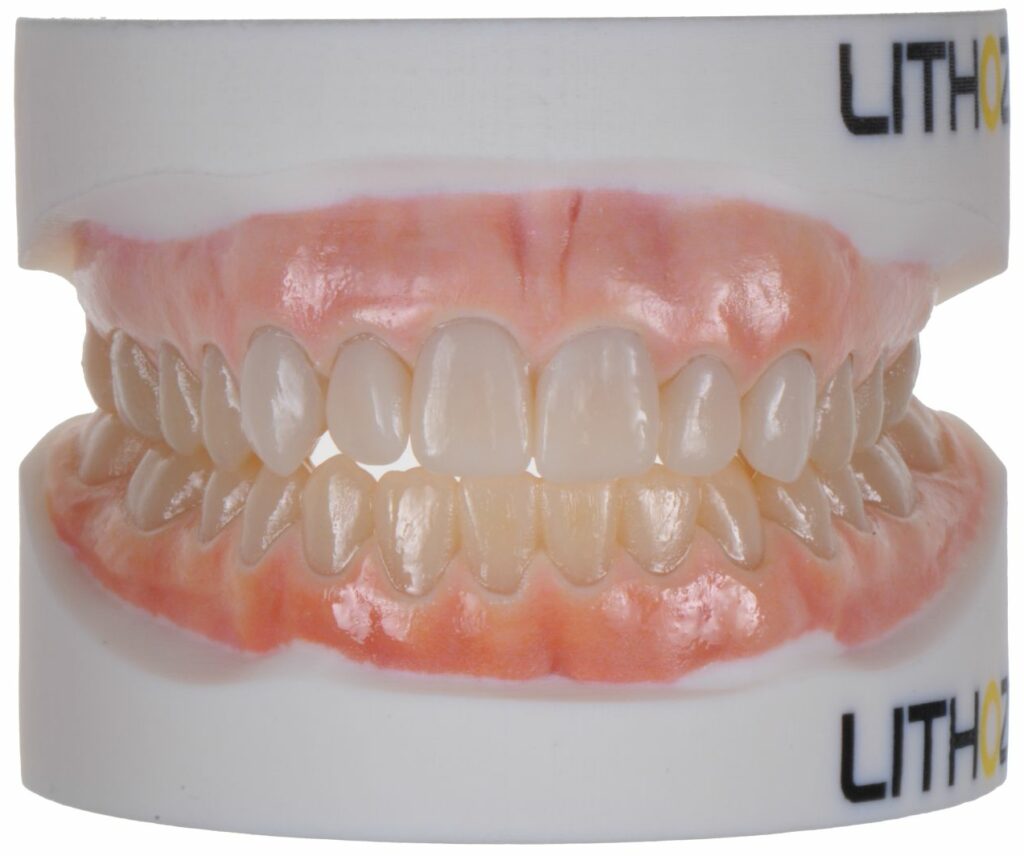
On another note, while most patients aspire to have their dentistry restoration achieved during the same rendez-vous at their dentist’ clinic, this timing is hard to achieve no matter what manufacturing process is leveraged. At present, AM ensures the best performance in terms of timing for veneers and fillings and the best part is, “no maintenance is required. Once the restoration is 3D printed, the success of the treatment depends on the expertise of a dentist,” Bomze outlines.
In addition to the technical advantages that may result from the use of ceramic AM with Lithium Disilicate, I have been impressed with the different cases or scenarios where this technology can add value:
“For people that have diastema for instance [a gap or space between the teeth], a minimum invasive treatment can be performed to address the issue. In this case, no-prep veneers are a great application candidate for ceramic AM,” Bomze explains. Moreover, depending on the patient’s specific requirements, 3D printed veneers can be performed in-situ, after adhesive fixation or based on the intraoral scan, after individualization on the additively produced cast.
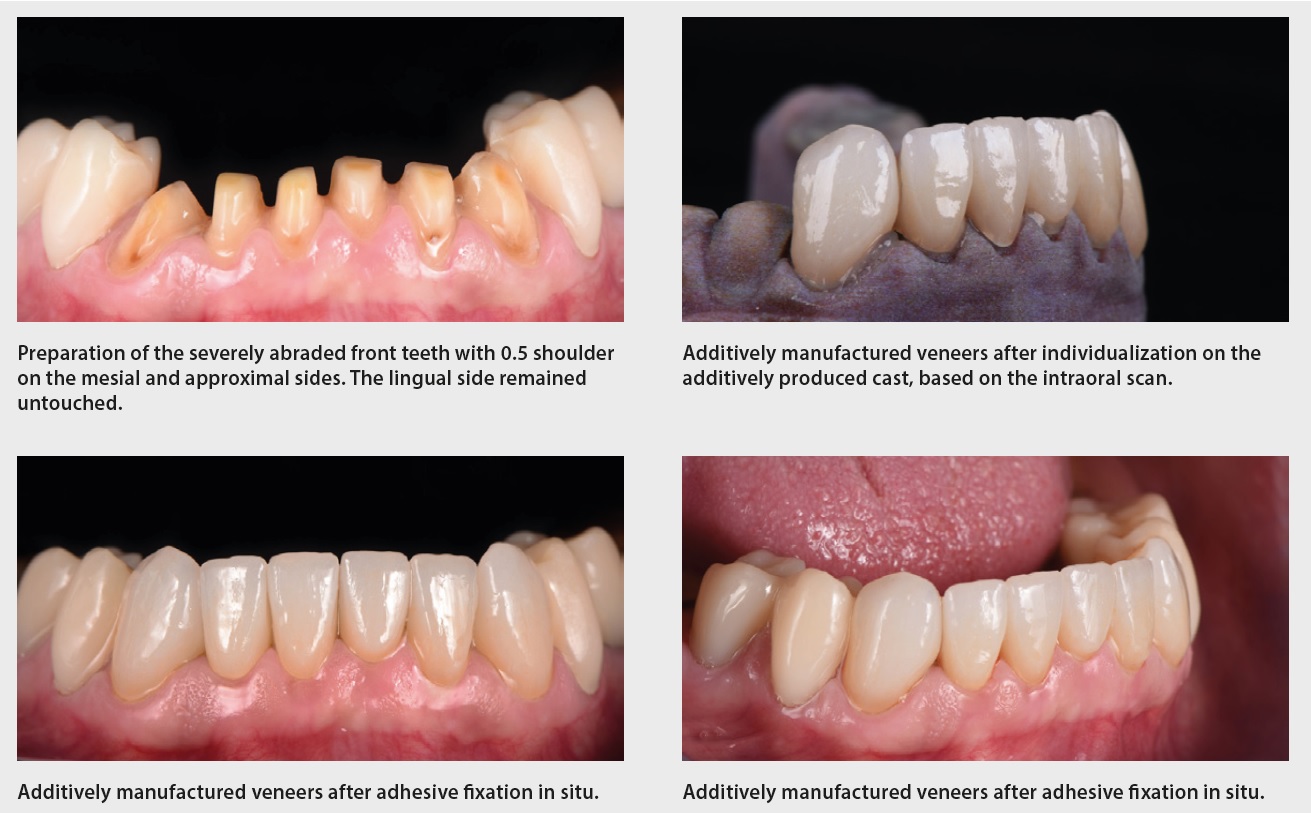
Moving forward…
While the USA will be the first market where lithium disilicate products will be made available to customers, research activities continue at Lithoz to advance the use of this material and its applications within the ceramic 3D printing landscape. The company is currently exploring the combination of two shapes of lithium disilicate to achieve a 3D printed multi-material part. “If the results of this project are conclusive, this application will be a game-changer in the digital dentistry field,” Bomze concludes. And given Lithoz’s installed base and big market share, I have no doubt the company is poised to capitalize on this relatively underdeveloped market opportunity.
This content has been written in collaboration with Lithoz.
A few words on Lithoz & Daniel Bomze
Lithoz is the world and technology leader for high-performance ceramic materials and 3D printers. Founded in 2011, Lithoz is committed to breaking the boundaries of ceramic production and supporting customers in expanding the manufacturing opportunities for the ceramic industry. As an innovative specialist for the high-precision ceramic 3D printing of complex dental and bioresorbable medical applications, Lithoz was also the first system provider worldwide to successfully develop high-end dental ceramics for 3D printing. The company has an export share of almost 100%, 150 employees and 4 different sites worldwide. Since 2016, Lithoz has also been ISO 9001-2015 certified.
Dr. Daniel Bomze is a polymer chemist by training and received his Ph.D. from TU Wien. In his Ph.D. thesis, which was conducted at the Institute of Applied Synthetic Chemistry, Dr. Bomze developed alternative irradiation-based curing methods for epoxy resins. He started his professional career as a freelance web application engineer as well as a project assistant at the TU Wien. Dr. Bomze acquired broad experience in materials research in different areas and is the author of numerous publications and patents. Starting from November 2016, he was employed as a medical business developer at Lithoz. In 2019, he became head of the medical business unit, which also includes dental applications. Starting from 2022, Dr. Bomze is Director of the Medical Solutions division at Lithoz.