With contributions from BigRep & Titomic
As its name implies, large format 3D printing is often used for manufacturing large size objects. The only thing is that manufacturers often use this term to qualify their additive manufacturing machine. Indeed, some of them attribute to their 3D printer the ability to print in large format while unveiling a simple professional 3D printer. So, is there a specific size that defines large-format printing? What are its advantages and disadvantages compared to a standard printing process? What are the different printing processes offered by the market? What can we retain from this market?
To deconstruct these stereotypes, we asked for the opinions of two companies: BigRep, a German manufacturer based in Berlin that develops large-format 3D printers for mass production, and Titomic, an Australian manufacturer that has developed one of the largest metal 3D printers on the market.
Founded in 2014, the Berlin-based company is made up of 90 engineers, developers, designers and experts from 22 different countries. René Gurka, who leads this team, has signed key partnerships with big companies active in mobility (Etihad Airways and Deutsche Bahn) and has secured his business with investments from BASF, Koehler, Klöckner and Körber, who have enabled the company to move forward and to offer complete solutions for integrated additive manufacturing systems, as well as a wide range of 3D printing materials on an open-choice basis.
The company manufactures and commercializes the 3D printers STUDIO and ONE, which, according to the CEO, set new standards in speed, reliability and efficiency.
It’s all about size…
Rules are not clearly outlined when it comes to large format 3D printing. Experts do not agree on dimensions from which one should define large-format printing.
An analysis of the 3D printers available on the market brought out three categories when it comes to volume: 3D printers with a printing volume whose X, Y and Z axes measure less than 197 mm, medium-size 3D printers – which manufacturers also call large volume 3D printers – with a printing volume larger than 197 mm and very large format 3D printers with a printing volume larger than 1000 mm (i.e. > 0.45 m3).
Speaking about this latter category, one thing is certain, the volume of the 3D printed part plays a key role. The bigger the part, the better.
While taking their 3D printers as example, Stephan Beyer, CEO of BigRep and engineer by training, explained the three features that should be taken into account to qualify large format 3D printing: “First and foremost, it’s about the volume the printers can handle. This is the basis for printing large parts for the industry in just one piece.
Secondly, a fast extruder is important as well. For the ONE, we offer an optional Power Extruder with 0.6, 1 & 2 mm nozzles that can print 60% quicker, thus making our printer one of the fastest large-format 3D printers in the market. The 0.6 mm nozzle creates the most detailed and precise prints to date.
Thirdly, print heads [should be specifically] designed for large-format printing. [Our print heads] operate independently, allowing for flexibility when printing in two colors, for example. They can be easily adjusted and replaced without needing tools. During the printing process, the active print head moves downward slightly to avoid any contact with the object. In combination with a large, flexible spool holder (it can hold several spools up to 8 kg), large-format objects can be created more easily.”
What types of technology for large-format 3D printing?
The additive manufacturing of large objects can be achieved via processes similar to those found in professional 3D printers.
However, people usually associate FDM technology (Fused Deposition Modeling) with large format 3D printing. In Europe, 3D printers from WASP and BigRep are often mentioned as reference in this category.
Speaking of BigRep’s 3D printers, three characteristics distinguish them from others of the same range: Size – with a capacity of over one cubic meter, the BigRep ONE provides one of the largest FFF built volume currently available in the market. Know-how – The company lays emphasis on the reliability of German engineering. That’s why, this “Made in Germany” positioning is easily reflected in the company’s communication. Costs – One of the most important point in the user’s eyes.
Stephan Beyer affirms that BigRep printers are highly cost-efficient, both in acquisition costs and in long-term operations.
New printing processes
In addition to FDM 3D printers, metal 3D printers that can print metallic large components can also be found in this category. Among this year’s releases, Titomic has raised the industry’s interest in a printer that integrates the «Kinetic Fusion» process.
Headquartered in Melbourne (Australia), the company is led by Gilbert Michaca, a senior executive with over 25 years of industry experience. He was instrumental in bringing Australian technology to the global market when he launched the first comprehensive inorganic explosive detection system, which is currently being deployed in government agencies, armed forces, embassies and airports around the world.
So, as far as the company is concerned, Titomic specializes in metal 3D printing. Its Kinetic technology Fusion™ has three main features: joining dissimilar metals and composites for engineered properties in a structure, the ability to manufacture stronger structures without welding, folding or bending as well as the facility to reduce time to market: no tooling and industry-leading production speeds.
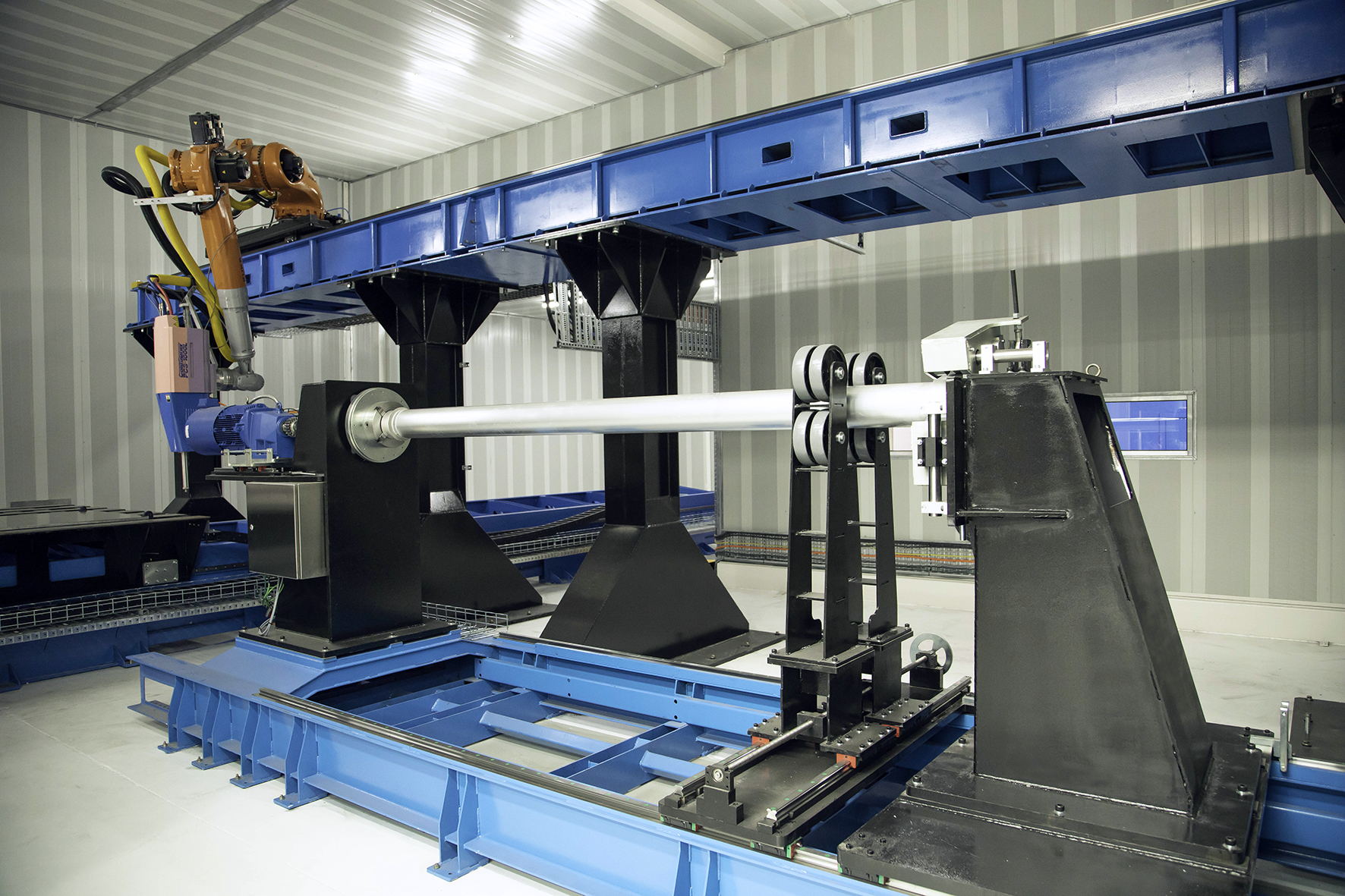
Gilbert Michaca explains that “Titomic Kinetic Fusion™ does not melt metal and there is no heat related oxidation and thermal distortion. This means Titomic’s process does not require a vacuum chamber and is a step change on how metals are manufactured by melting for over 5 000 years. Titomic’s metal 3D printers utilize 6-axis robots to enable truly digital manufacturing solutions that can be customized for industry needs.”
With a build volume of 9m x 3m x 1.5m (40.5m3), the system can manufacture parts from zero point based on CAD data. The company also takes advantage of additive manufacturing for rotational building of parts on our 5m x 2m diameter rotator from either zero point or onto a mandrel.
Limits & prospects of development of large-format 3D printing
In order to determine the advancement of this technology, manufacturers should pay attention to the needs of the industry. As a matter of fact, the market needs will determine the way the market will evolve.
Whether we are talking about large-format FDM or metal printing, the automotive, aviation and mobility industries can benefit from the production of large parts.
Furthermore, production of titanium consumer goods, golf clubs, marine components, drones require the use of large- format metal printing at an industrial scale.
However, the main limitation we should note is that large- format 3D printing systems will also have to become faster and more efficient. They also need to offer interconnectivity and data in order to become a key element in smart factories and IoT applications.
Furthermore, given its ability to manufacture large industrial scale parts, large- format printing is not always the ideal candidate to produce intricate structures that would be used for jewellery or dental implants. Titomic’s metal 3D printer for instance, cannot be used in those sectors that require a very high accuracy.
Lastly, advancements over the past decade have paved the way for the development of 3D printing beyond prototyping. Finding new ways of making the technology and its various processes evolve is still and will remain a key issue for specialists.
While a 20% annual growth is expected in 2020, a McKinsey study “forecasts a market volume of 100-250 billion Euros by then – and one of the driving forces behind this will be large-format 3D printing.”