“Better, faster, cheaper.” These are three words that every manufacturer is looking to use when qualifying their production on an industrial scale – and this, no matter what additive manufacturing processes they leverage. The thing is, the quest for industrialization seems obvious when using certain AM technologies while others do not always get the credit they deserve. In the wide array of AM processes that are gaining in popularity, a conversation with 3DCeram sheds light on the possibilities that stereolithography (SLA) offers to achieve production on an industrial scale.
Acknowledged for the manufacturing of ceramic 3D printers based on stereolithography (SLA), 3DCeram’s offering has evolved to support customers throughout the entire value chain. While we have covered several applications of the company’s technology across the healthcare, aerospace, and energy sectors, SLA 3D printing does not benefit from the same reputation as other widely used AM processes. This lack of knowledge regarding this process makes it difficult to consider it for industrialization or series production – let alone the fact that SLA can enable ceramic 3D printing applications.
“Manufacturers who seek production solutions through 3D printing usually do so under the impetus of a specific project,” the 3DCeram team explains from the outset. “This means that manufacturers who consider additive manufacturing to be a full-fledged production tool are growing in number. But some got a little confused by the diversity of technological offerings. Let’s admit that there is a proliferation of technologies (extrusion, FFF, DLP, Binder Jetting, Stereolithography…) emanating from the academic sector, but this often confuses manufacturers. It makes their journey longer.”
According to the 3DCeram team, SLA has a reputation for being a “slow process”.” In contrast, the technology “offers the possibility of very large printing areas thanks to top-down printing [and] is most easily automated.”
Key considerations to consider when moving toward industrialization
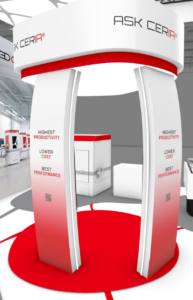
For those who are not familiar with 3DCeram’s technology, it should be noted that in a top-down construction process, the layers are constructed from the bottom up, minimizing the need for numerous supports. Once the printing process is complete, the parts are cleaned, and having fewer supports simplifies and speeds up the process, while also lowering the risk of waste from potential breakage during support removal.
Over time, this process has been enhanced to integrate automation, and artificial intelligence (AI). These features along with the ability to produce large parts have become key considerations to take into account when moving toward industrialization.
“SLA is a technology that offers significantly large production surfaces, with the possibility to add lasers and to enhance the printing speed,” 3DCeram said. Besides this key asset for manufacturers looking for mass production, the company’s systems are large enough to print either small or big parts.
Moreover, process automation is essential if we want to reach manufacturers, and here 3DCeram already offers partial automation of the process. “Our 3D Printers have a formulation feed system with a pressurized pot. At the output of the C1000 FLEXMATIC printer, there is a recycling station that allows the recovery of unpolymerized formulation, which then goes back into the production cycle. The printing surfaces of 3DCeram’s CERAMAKER printers offer the possibility of printing very large parts. For instance, with the C3601 ULTIMATE whose platform is 600*600*300 mm, there is a considerable space to print large [parts] and in ONE PIECE!” the company adds.
As far as AI is concerned, 3DCeram has recently developed a solution that can optimize quality and printing time. Named CERIA, it can be deployed in several stages.
“First, the CERIA Set analyzes the part and the VAT to propose adjustments and generate optimized parameters. This means it will cross-reference incredible amounts of data to make a complete analysis and anticipate all areas of improvement. Once all adjustments are made, CERIA generates ready-to-use printing parameters for CERAMAKER printers. The operator then only has to start the printing.
This new tool is a major asset for a manufacturer as it responds to the need to secure their production process. Indeed, all the knowledge is no longer held by a collaborator who could decide to leave the company. The risk of disruption in the production chain is then eliminated.
Another major contribution of CERIA is the time saved in terms of iterations. We know that, as with any industrial process, there are rejects or failures. The contribution of CERIA here is considerable, as it produces gains in time, raw materials, and machines.
3DCeram will be launching at the end of 2024, a complementary module to its artificial intelligence, CERIA Live. This module is about real-time control during printing. CERIA analyzes the previous 3 layers to anticipate all events that could occur in the next 5 layers and intervene to make necessary adjustments. The idea here is to control all parameters in real-time to optimize printing time.”
With the growing use of artificial intelligence across all areas of the manufacturing chain, 3DCeram demonstrates that it is examining the current evolution of the market to help vertical industries produce at the best cost – better, faster and cheaper.
Non-technical barriers & applications
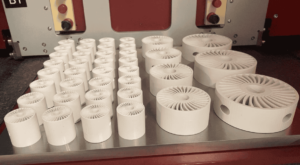
While the focus is often made on technical capabilities, the reality on the production floor also reveals that the knowledge gap in large factories, the uncertainty about what to produce with a given technology or even the transition from small-scale to larger-scale AM are also key challenges to the industrialization of AM – challenges that 3DCeram can help address as in two decades of experience in the field, the company has evolved from part manufacturer to 3D printer manufacturer.
As such it is also well-positioned to testify to the capabilities of its solutions – especially with AI offering the possibility to analyze and control the entire AM process.
“All technical ceramics manufacturers will benefit from optimizing AM processes assisted by artificial intelligence and automation. Manufacturers can finally design parts based on the properties they are seeking, rather than being constrained by the traditional processes available in their workshops. The locks are falling and manufacturers are increasingly attentive. At the forefront are all the productions associated with sovereignty and confidentiality issues. We can see that these issues are more and more numerous and more present than ever,” 3DCeram outlines.
While the company’s solutions can lead to applications in the semiconductor, defense, and aerospace sectors – to name a few, it’s crucial to continue contextualizing each application to make the most of the technology.
Editor’s Notes
Visitors at Formnext 2024 could experience CERIA, the artificial intelligence and 3D printing assistant for technical ceramics from November 19 to 22, 2024 in Hall 11.1 Stand D21.
This content has been created in collaboration with 3DCeram. Quotations have been edited to ensure clarity.
Remember, you can post free-of-charge job opportunities in the AM Industry on 3D ADEPT Media or look for a job via our job board. Make sure to follow us on our social networks and subscribe to our weekly newsletter: Facebook, Twitter, LinkedIn & Instagram! If you want to be featured in the next issue of our digital magazine or if you hear a story that needs to be heard, make sure to send it to contact@3dadept.com.