The story of 3D printer manufacturer Farsoon and materials producer Covestro started when the latter decided to operate the Laser Sintering Systems of the former in its German and Dutch (legacy-DSM) additive manufacturing facilities. The aim was then to test the processing and printing of new materials such as thermoplastic polyurethane (TPU), polypropylene (PP) and polybutylene terephthalate (PBT).
It turns out that the combination of their technologies led to validated parts for end-use applications in automotive, electrical and consumer industries.
Both companies strengthen their collaboration today based on an open systems philosophy. This means that, customers can choose the materials of their choice for their end-use applications. This philosophy also implies that Farsoon machines are open systems so that operators can optimize process parameters for highest productivity at required part qualities for the material of choice.
The manufacturer explains that the High-Temperature- and Super-Temperature-configuration of its machines enable process chamber temperatures of up to 220 °C or 280 °C, respectively. The machines are equipped with high-speed scanners and powerful lasers.
Furthermore, this collaboration will be focused on polymer-based 3D printing materials for Farsoon’s powder-based laser sintering machines.
As a matter of fact, Covestro has already successfully launched TPU and PBT polymer powders developed on Farsoon 252P-series machines. The development of additional powders and the upscaling to larger series applications is part of the strengthened collaboration.
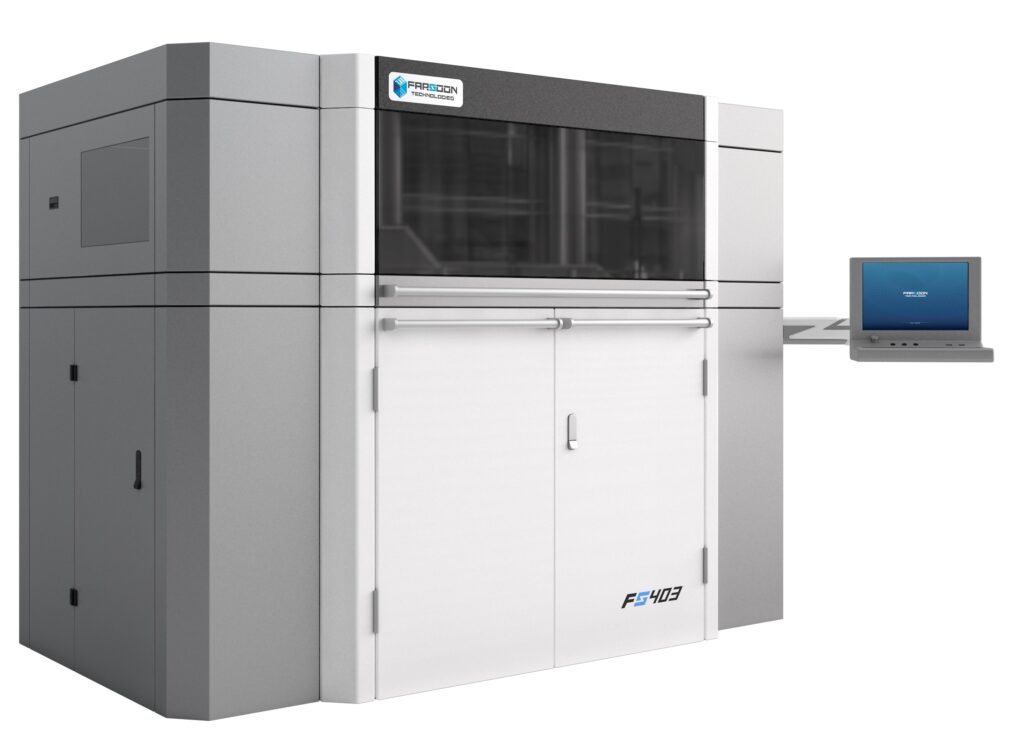
Footwear & Automotive, first applications that result from this strengthened collaboration
Covestro, Farsoon and Seifert Logistics Group (SLG) in Ulm, Germany jointly developed TPU parts for footwear. Seifert Logistics fabricates TPU parts on a Farsoon SS403P at high productivity levels.
Covestro, Farsoon and a partner from the automotive industry collaborated to develop end-use parts for interior car applications using legacy-DSM PBT powder Arnite® T AM1210 (P).
“By collaborating closely with printer manufacturers, we can test materials in the development process and provide customers verified material and printer solutions”, said Geoff Gardner, Innovation Director Additive Manufacturing at Covestro. “Farsoon SL printers and especially their Flight™ Technology can run at standard and high temperatures so we can print PBT, PP and TPU all on the same printer. And with their higher accuracy and productivity, and lower cost per part, they are well suited for industrial production.”
Remember, you can post job opportunities in the AM Industry on 3D ADEPT Media free of charge or look for a job via our job board. Make sure to follow us on our social networks and subscribe to our weekly newsletter: Facebook, Twitter, LinkedIn & Instagram ! If you want to be featured in the next issue of our digital magazine or if you hear a story that needs to be heard, make sure you send it to contact@3dadept.com