For us, generative engineering is not a buzzword. We are learning a lot on the way this technology is reimagining design workflow – of products manufactured via AM of course. One company we are keeping in our loop in this regard is Elise GmbH.
Even since they have discovered lightweight construction of marine plankton organisms, the team at Elise has been developing a software platform that automates the entire development process, from styling and design to simulation. What makes them outstanding? A DNA that contains the blueprint for the ensuing development process.
As per the words of the company, this means that instead of concentrating on the component itself, as was previously the case, engineers define a set of rules for the product, along with basic conditions. This concept features a completely new development process for components and the software tools used. All previously necessary process steps, such as simulations and CAD design and the associated software, must be integrated into the technical DNA and run through automatically.
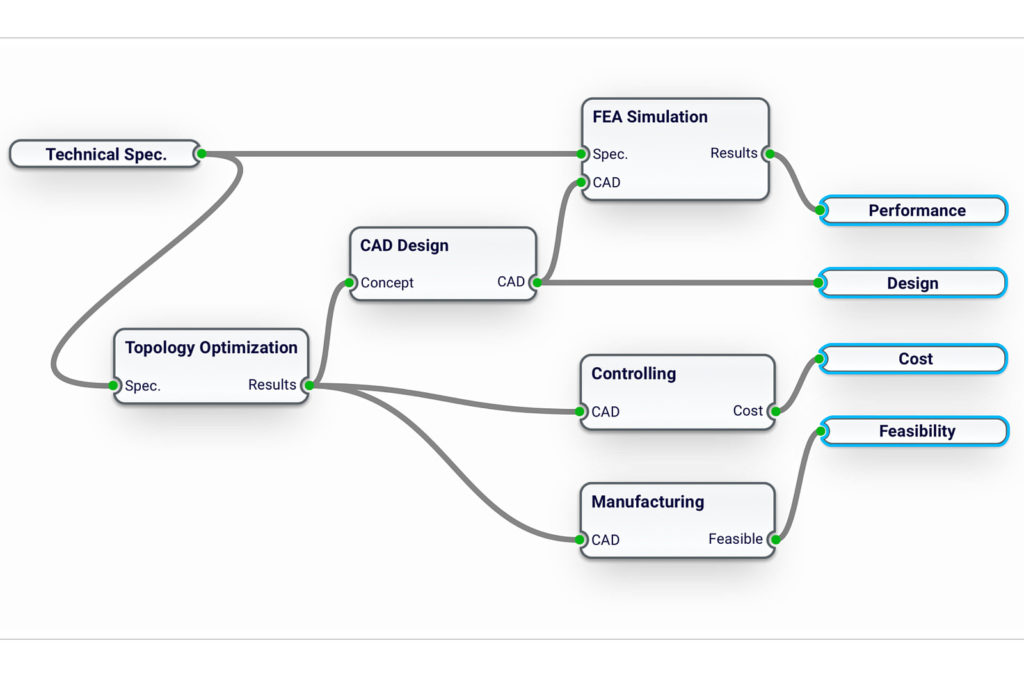
We have already discovered some interesting applications of the German startup’s software platform. Remember this very light 3D printed bike? We also know that BMW Group has been using this technology in product development and today, another company that has debuted a cooperation with the startup is the EDAG Group, a company that specializes in mobility engineering.
With the goal of taking Elise’s software to a more practice-oriented level, the engineering team at EDAG Group is on its way to show the various innovations that can be done in the mobility industry through appropriate rethinking and redesign.
The company is already using the software for one of its projects. It explains that for the “VariKa” research project, for example, generative engineering enabled up to 50 % of the development time for additively manufactured battery nodes to be saved. The result was also 40 % lighter than it would have been using the conventional development process. In a different project, furthermore, the concept design with an optimised ribbed structure for a die-cast strut brace was automatically generated.
Due to the fact that the development steps are continuously mapped in ELISE, the process can be run through automatically whenever basic conditions are changed. An important element here was the automatic transfer of the topology optimisation results to a parametric CAD model using the skeleton algorithm.
To enable the field of application to be expanded and the method to be established with EDAG customers in the future, FEYNSINN, an EDAG Group brand, is working with connected engineering to interconnect ELISE and third party applications, for instance existing CAD systems.
“For the EDAG Group, I see enormous potential for further accelerating the efficiency of the product development process by means of this new engineering concept,” explains Sebastian Flügel, EDAG project leader at the department for Innovation.
Remember, you can post free of charge job opportunities in the AM Industry on 3D ADEPT Media or look for a job via our job board. Make sure to follow us on our social networks and subscribe to our weekly newsletter : Facebook, Twitter, LinkedIn & Instagram ! If you want to be featured in the next issue of our digital magazine or if you hear a story that needs to be heard, make sure to send it to contact@3dadept.com