While they no longer question the potential of AM to be a great tool to meet today’s industry requirements; industries do recognize that process repeatability and material availability issues remain one of the most important hurdles to overcome to achieve desired production results. Interestingly, one way to do that consists in understanding the “geometry-process-structure-property relationships” for additively manufactured parts. In most cases, empirical approaches that seek to leverage data have proven to be effective in identifying material process-structure-property relationships.
The relationships between process, structure, and property in materials require to go beyond the performance of a material as generally acknowledged and explore the structures and properties of components to be manufactured as well as the special variations that may intertwine during the fabrication of these components. The first step to understand these relationships is to acknowledge the importance of materials data which have become a critical resource for manufacturing organizations seeking to enhance products, processes and, ultimately, profitability. Most importantly, if the need for prudent handling of materials—right from their purchase till their ultimate conversion into finished product is crucial, it should be noted that ensuring that the results generated by a materials property analysis is not a wasted investment lies in an efficient use of a materials information management system.
The exclusive feature below ambitions to understand the concept of materials information management systems (MIMS) (aka Materials Data Management Software) in additive manufacturing, a concept that consists in but is not limited to material requirements planning, purchasing, inventory control, material supply management and quality control.
This feature will especially discuss:
- The relationship between material producers and software providers – when it comes to MIMS;
- The reasons why one can leverage a materials data management system;
- How a material information management system works and;
- The various challenges that still need to be addressed to have the ideal material information management system.
We have invited Senvol’s President Zach Simkin and Guillaume Boisot, Head of ICME, Hexagon’s Manufacturing Intelligence division to share key insights into this topic. Senvol provides data to help companies implement AM. The company’s products and services enable industrials to access AM data, generate AM data and analyze data.
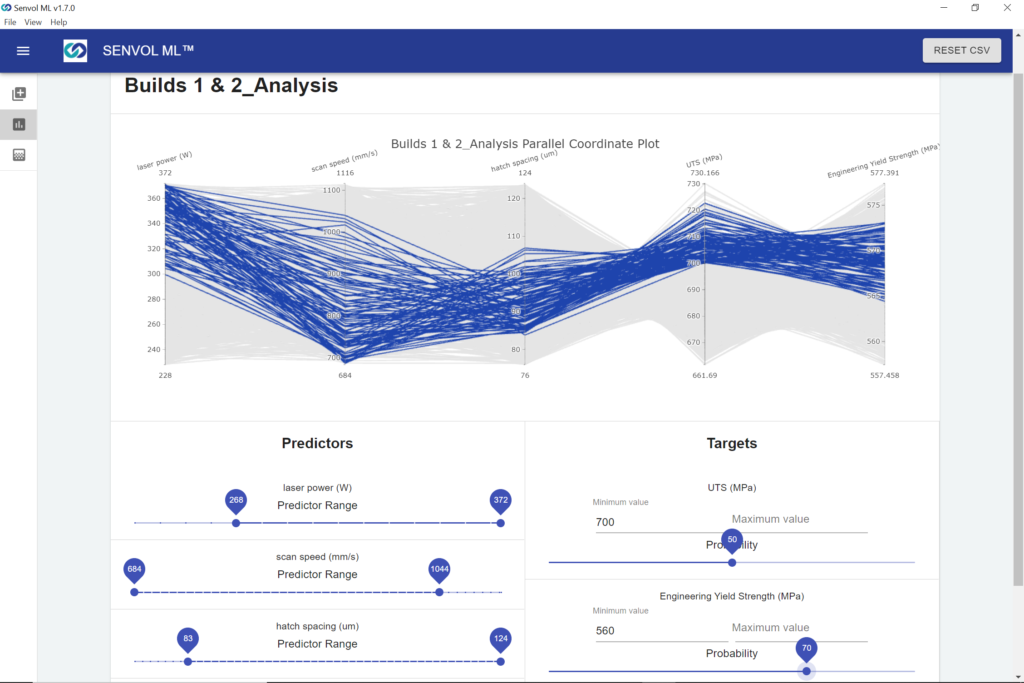
Hexagon is a leader in digital reality solutions, combining sensor, software and autonomous technologies. The company basically puts data to work to boost efficiency, productivity, quality and safety across industrial, manufacturing, infrastructure, public sector, and mobility applications.
In this specific field, Hexagon has the ability to combine materials data management with material modelling and artificial intelligence / machine learning and help industries to take the right decision in terms of material selection.
The relationship between material producers and software providers
Materials data often refer to the properties and processing of materials (metals, alloys, plastics, composite materials, ceramics, etc.) that organizations use. These data may come from a wide range of resources (materials testing, quality assurance, or measurement of product performance).
Is the materials producer the one that should provide these data? For Senvol’s President Zach Simkin, there are several tiers to consider: “First is to understand reference-level data, which is typically (though not always) data that can be found on a spec sheet published by a material producer.At Senvol, we maintain the Senvol Database, which is a comprehensive database of industrial AM machines and materials. We work directly with material producers to catalog their materials data in an easy-to-use, searchable database. The Senvol Database is one of the most-used resources in the industry. It is available for free via our website and can also be accessed through several of our partners. Many of these partners include companies that offer AM materials data management software, such Ansys Granta, MSC Software, and Bassetti.

Reference data is a good starting point, however it is often not sufficient. Once a material has been selected, users typically start to need material characterization data, which is a more in-depth look at how a material will perform. At Senvol we offer this through our Senvol Indexes datasets. This is data that Senvol generates regarding a particular material when processed on a particular machine, and typically includes far more data than is provided on a reference data spec sheet.
To understand how a material will perform, data analysis can be conducted on whatever empirical and/or simulated data that a company has access to. For this we provide Senvol ML, which is data-driven machine learning software specifically for AM. The software is often used to rapidly optimize process parameters and develop materials. This software works hand-in-hand with materials data management solutions. Those solutions store the data, and our software is subsequently used to analyze the data.”
Senvol’s point of view is relevant to the extent that the software company does not provide materials data management software itself but rather databases that might be stored in such software, and machine learning software that analyzes data that might be stored in such software. So, while the company alerts on reference-level data, material characterization data or data analysis, a software provider like Hexagon may receive from a traditional plastic producer a material card with parameters describing important physical characteristics that material engineers can interpret to select a good material for a part. However, this material card might not always be enough: “Understanding how a part 3D printed from that material will perform requires much richer detailed data to predict how its behaviour, because materials are not uniform like a black metal but anisotropic – meaning factors such as the resin type and reinforcement such as glass or carbon fibres significantly affect the behaviour – after all, that’s why we have composites!”
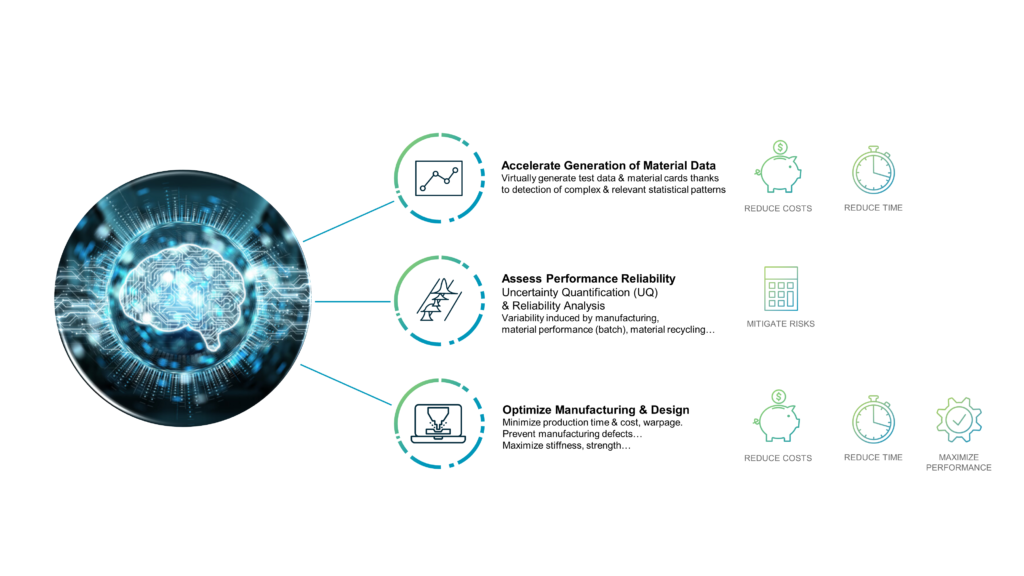
“It’s important to note that the material is affected by the manufacturing process used, so to predict the material performance you must also know how a 3D printer will use it – for example the direction in which fibres are aligned.
Hexagon pioneered multi-scale material modelling with its Digimat software. The accurate material model produced in Digimat can then be embedded in a Computer Aided Engineering (CAE) model so that engineers can accurately predict how a specific material grade will affect the overall performance of a product and optimise the design to make better use of the material and the additive process”, Guillaume Boisot said.
In this case, the relationship between software developers and material producers (understand printer OEM, as most of the time they qualify materials for their machines) strongly depends on collaborations that aim to test and characterise the materials with great detail and “encode” detailed material information to create a proprietary model.
“This highly accurate proprietary model is validated and made available through our Materials Exchange capability. Manufacturers can request this material model directly from the material supplier through Materials Exchange, and they are granted access to this encrypted proprietary information that is ready to use in Digimat.
Many material suppliers also use these material models to support their applications engineering, enabling them to prove that a new material will be suitable for a customer without undertaking costly and lengthy physical materials test campaigns that can prohibit the adoption of new materials and additive methods that offer significant benefits for innovation and cost reduction”, Hexagon’s Boisot explains. To illustrate this argument, the software expert says multi-scale material modelling and simulation enabled 3D printer OEM Stratasys to iterate designs and parameters using simulation instead of devoting time and materials to testing via printing. It also used simulation to anticipate printing problems by evaluating the impact of printing direction and location, and to explore process parameters on process quality and part fidelity. Good correlation was demonstrated when results of warpage simulation were compared to 3D scan measurements of a physically printed composite tool. As a result of material modelling, advanced simulation capabilities helped the company reduce warpage from .5 mm to less than 1 mm, or by about 20 percent.
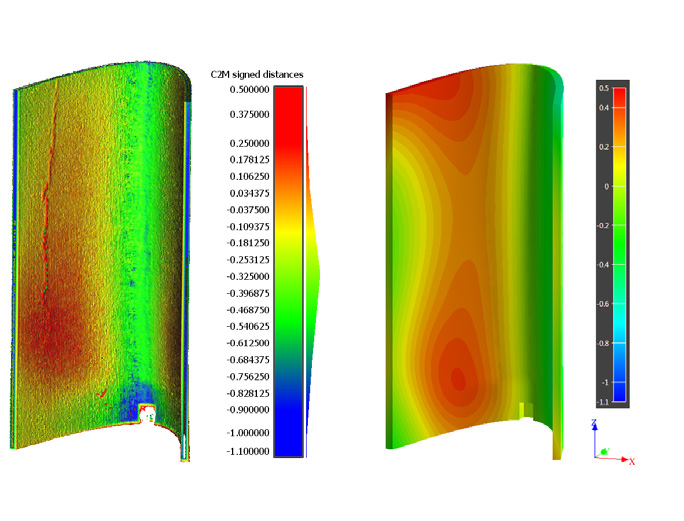
So, what are the reasons that led to the use of a material data management system?
Using a materials data management system is not systematic to each organization. A 3D printing application that doesn’t require very high quality or precision, might not require the use of a materials lifecycle management software either.
Furthermore, Simkin told 3D ADEPT Media that when an organization is just starting out, using e.g. Excel spreadsheets only can be their first resort. Moving forward, this becomes complicated as an Excel sheet will not just be enough for the level of data being stored and accessed.
Beyond the growing number of materials an organization may have, the range of issues that affect productivity and data integrity within production environments may also drive the use of a materials data management software system. These issues may lie in the consolidation of specialized data stored in disparate sources and varied formats, the large amount of time spent in finding property data to support analysis or simulation, the design iteration failures or the generation of data that are not used in the end. All of these challenges ultimately affect traceability, which is pivotal in demanding industries such as aerospace or medical.
According to Boisot, “material data management has a very important role to play in managing material data, but more importantly capturing data about the process and results throughout the lifecycle. In large organizations, the inability to share material data and process insights prevents design teams from confidently applying modern CAE methods to parts that could be additively manufactured. Invaluable lessons can be extracted and shared from additive manufacturing trials, failed prototypes, and testing on materials and quality. Working in silos simply increases the chances of failed prototypes and often leads to wasted investments in materials, time, and money, which prolongs the time required to bring new products to market. We us the term material lifecycle management for this reason – it can’t be just for materials professionals, or the benefits will be limited.
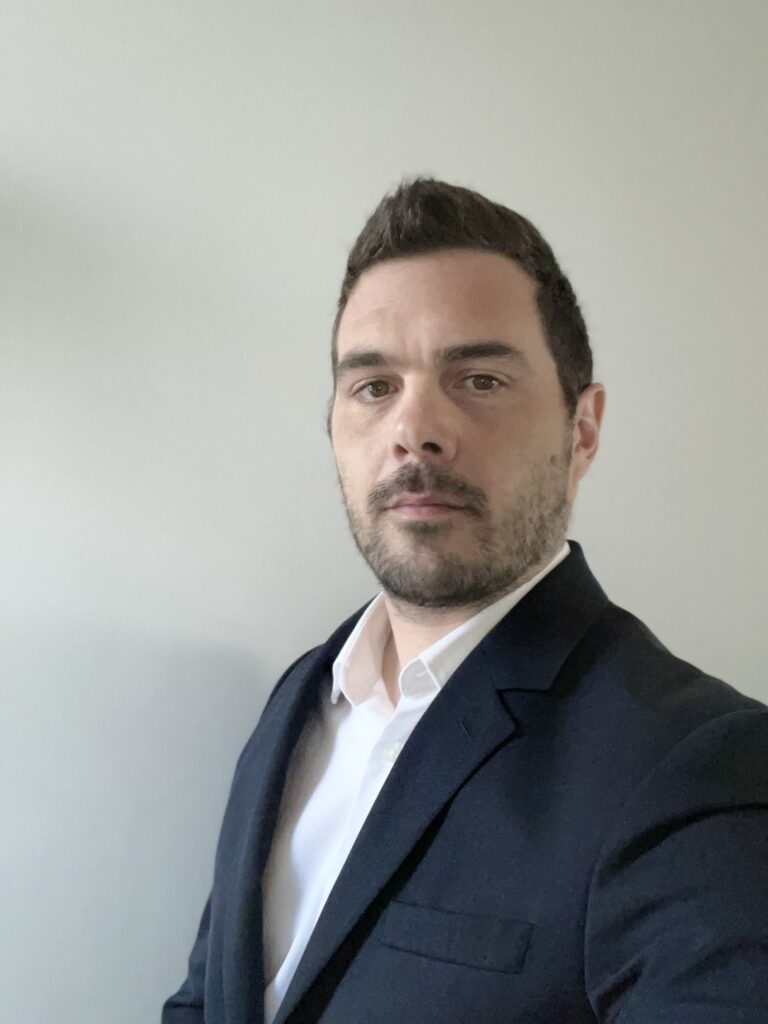
Material data management is also key to enabling the optimal use of materials in product development. Arming design engineers with the best available information involves integrating historically siloed disciplines. Material models are typically approved and validated by materials engineer then published with all relevant information (for example cost, certifications and internal classifications) so that engineers can predict the effects that materials choices and manufacturing processes will have on performance.
The industrialisation of additive manufacturing requires repeatable quality at scale. Material data management plays a crucial role in metal and advanced material printing, providing traceability of material from powder to the quality inspection of the final part. But the available design space for a product is dictated by several complexly intertwined factors, such as material and manufacturing process, budget, desired performance, and even environmental impact. Adopting and integrating the platforms that manage material data, design iterations, simulation results, tooling, and toolpaths throughout the product-development cycle is essential. Managing this data and applying statistical analyses and AI and machine learning will play an important role in improving and optimising these processes over time”.
How does a material data management software solution work?
Given the fact that each software solution has its own modus operandi, one cannot legitimately explain how a material data management solution works. Whether we talk about identifying the right material for an application or developing a new material, it often comes down to the purpose the organization ambitions to achieve.
“Material data management systems enable organizations to seamlessly store all of their materials data in one central repository. This helps with everything from material screening, qualification to material development and characterization”, Senvol’s President notes.

For example, by using Hexagon’s MaterialCenter, Formula 1 team McLaren Racing allows its engineering team to make optimal design decisions for their vehicles quickly and efficiently, with full knowledge of the performance and cost implications at every step. It captures data from material testing and the many tools and processes the team employs to ensure full traceability throughout each component’s lifecycle. Traceability is even more important when we know that basically, every 3D printed part sent into production requires some form of serialization in order to reconstruct provenance hence the necessity to save the right machine’s parameters, and every data linked to its production. In this context, the material lifecycle management concept becomes of paramount importance for additive manufacturing teams.
Existing challenges & concluding thoughts
It’s been a few years that we continuously witness how the focus on process management enables industrials to monitor the full data lifecycle of high-quality data. A few years ago, when the Material Data Management Consortium (MDMC) -a collaboration of leading aerospace, defense, and energy enterprises – started tackling this topic, they laid emphasis on the importance of allowing the right engineers/stakeholders to deploy effectively the results generated by a material property analysis. The stages “capture, analyze, deploy, and maintain” ambition to define each of the steps in this process.
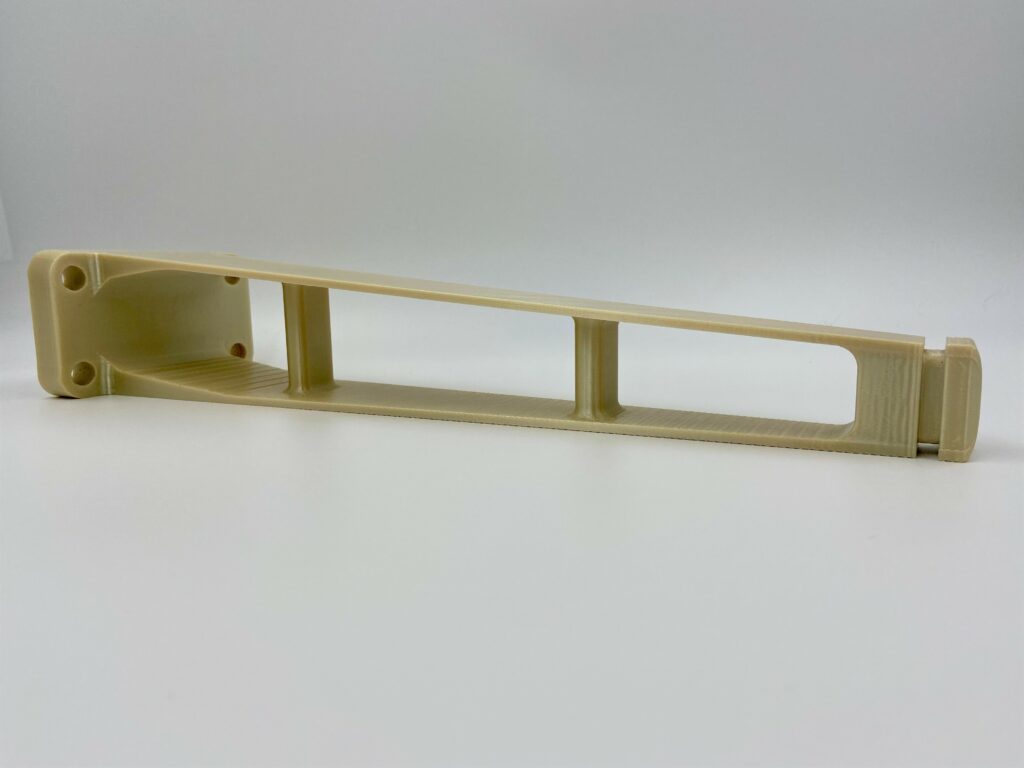
Today, despite the advancements of the various technological capabilities of the market, despite the fact that we should recognize that web-based tools that 100% focus on materials are already a big change forward to manage valuable – and expensive to produce – data, openness remains absolutely vital, because, as Hexagon said, “no single vendor has everything you will need to build the technology stack that will deliver against your specific needs for quality, volume, material, etc.” “You need a platform that can connect in a meaningful way with the best available technologies and help you to use materials to the very best of their potential for a sustainable, compliant, high quality and hopefully innovative final product.
Open means integrating in a deep and meaningful way with material modelling tools, design engineering tools, test and metrology software and tools such as PLM that can help manage some of these processes”, the expert adds.
Moreover, while the potential for material digitization and digital transformation to accelerate product development, especially once combined with additive methods – is no longer a debate, the road is still long to go when we look at the slow pace at which standards related to this topic are being addressed.
“One organization might use and organize the tool differently from another organization, and that can lead to interoperability issues. There are organizations, such as NIST, that are actively working on standards for data in AM, and I believe that these efforts will help mature the industry overall”, Zach Simkin concludes.
This feature has first been published in the March/April edition of 3D ADEPT Mag.
Remember, you can post job opportunities in the AM Industry on 3D ADEPT Media free of charge or look for a job via our job board. Make sure to follow us on our social networks and subscribe to our weekly newsletter : Facebook, Twitter, LinkedIn & Instagram ! If you want to be featured in the next issue of our digital magazine or if you hear a story that needs to be heard, make sure you send it to contact@3dadept.com