To avoid climate disaster, billions of dollars are invested in hydrogen, which should meet a quarter of our energy needs by 2050. To enable this transition, industries that produce carbon dioxide (CO2) have the biggest role to play in this fight. With the power generation sector totalling ~46% of global CO2 emissions from fossil fuels, most organizations are exploring a transition to the use of hydrogen as a zero-carbon gas turbine fuel. What does this renewable energy transition with Additive Manufacturing (AM) look like?
I might be working in a technology-focused trade press, but there are topics that have always sounded utopian for me. Hydrogen is one of them. It has always sounded so fictional…like in The Mysterious Island a novel by French writer Jules Vernes (published in 1875), where an engineer explains to a journalist how water could eventually replace coal as an energy source. We are not very far from this reality today, as hydrogen increasingly receives attention as a possible cross-sectoral energy carrier that could allow emission reductions in several fields of activity, including hard-to-abate ones. And I need to admit it: this is not a Sci-Fi novel. This is happening.
Hydrogen is a clean fuel that, when consumed in a fuel cell, produces water. It can be obtained from water using solar- or wind-generated electricity. Since it does not release any CO2 when used as fuel, it would play a crucial role in the decarbonization of thermal power generation. Interestingly, gas turbines are only one amid several types of thermal power generation. To enable this transition to a hydrogen economy, organizations are rethinking the role of gas turbines while taking into consideration a number of variables unique to hydrogen.
The present dossier ambitions to understand the role of gas turbines in this renewable energy transition and the part AM can play to enable it. To address this topic, we will discuss the following items:
I – The role of gas turbines in a sustainable energy system
II – AM strategies one can explore to bring the hydrogen economy closer to an effective implementation across the entire thermal power generation sector or enable green hydrogen fueled gas turbines to start.
I – The role of gas turbines in a sustainable energy system
A gas turbine is a type of combustion engine that can turn natural gas or other fuels into rotational energy. They are currently part of the cleanest fossil-fuel based power generation solutions, can absorb the fluctuations of renewables and enable emission reductions, using low or carbon-neutral fuels like natural gas, biogas, industry waste gas and hydrogen-enriched fuels.
The discussion about hydrogen fueled gas turbines is brought to several countries’ agenda as most of them are looking to reduce their dependence on fossil fuels. Hydrogen therefore becomes an interesting alternative when other renewable energy sources are available in limited or fluctuating quantity.
“Gas turbines are effective when it comes to balancing volatile renewable energy generation thanks to their flexibility and short ramp-up times. Future carbon-free power generation requires ramping of hydrogen capability in gas turbines with hydrogen produced from water and surplus renewable electricity. Energy generation using hydrogen fueled gas turbines has another huge advantage – this is well-known and well-established energy generation technology, established all around the world, meaning potentially much faster, technically and economically feasible introduction of green energy generation” Eduard Hryha, Professor, division of Materials and manufacturing, Industrial and materials science, Director of CAM2 states.
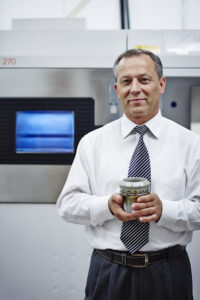
For Vladimir Navrotsky, AM Chief Technology Officer and Senior Principle Key Expert at Siemens Energy, the interest in hydrogen fueled gas turbines is driven by environmental, political, technological and economic considerations that are worth mentioning. Apart from specific country goals on net zero emissions, organizations will very soon deal with “stricter regulations on emissions and use of fossil fuels due to the Paris agreement (COP21), [as well as] other initiatives (e.g. European Green Deal, EU Taxonomy”. From an economic standpoint, one notes an “increasing carbon pricing through CO2 taxes or emissions trading and a customer pressure”: not only companies and utilities have their own requirements to reduce carbon footprint but they also receive requirements from customers, investors and financing institutions (e.g. European Investment Bank (EIB)). From a technological standpoint, Navrotsky notes that e.g. for the chemical industry the “possibility to utilize hydrogen rich off-gas from refinery and chemical processes” is a strong incentive for the use of hydrogen fueled gas turbines. For industrial users and utilities “potential future blending of hydrogen in existing natural gas networks and pipelines requires that existing gas turbines and existing power plants are enabled to cope with a certain share of the hydrogen content in the fuel .”
This means that, to envision a “net zero future”, a power plant might want to use of post-combustion carbon capture – or they might want to leverage green hydrogen in new or upgraded gas turbines in their existing power plant. Hydrogen-ready gas turbines can also operate in combined-cycle power plants. In this case, they would use surplus heat to generate steam that powers a second turbine.
Energy technology company Siemens Energy for instance, has been granted a third-party certification (TÜV SÜD) for its “H2-Ready” power plant concept. According to the company’s representative, it covers the three phases in the life cycle of a plant:
- The Bidding Phase – when the concept of the hydrogen-readiness is established according to the client’s H2-roadmap (Concept Certificate – Generic).
- The Project Phase – when the concept is implemented into the design and construction of a H2-Ready power plant (Project Certificate – Project specific).
- And the Transition Phase – when the plant is converted into H2 fired plant, once hydrogen is available (Transition Certificate – Project specific).
“The “H2-Ready” concept certificate provides a roadmap describing how a new power plant needs to be designed to co-fire hydrogen or even burn pure hydrogen”, Navrotsky completes.
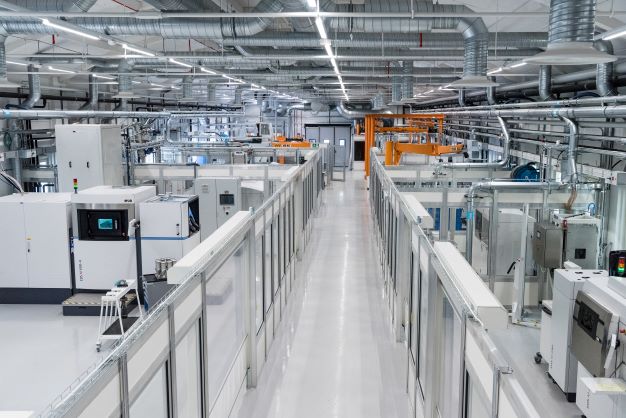
The thing is, despite these benefits, hydrogen is not a perfect chemical element. It currently remains expensive and is not the safest source of energy. “Hydrogen is a highly reactive fuel, with flame temperatures is significantly higher than natural gas flame temperatures. Compared to natural gas its flame speed is more than three times faster and has an auto-ignition delay time more than three times lower”, Navrotsky outlines.
Part of this issue can be addressed through the integration of manufacturing processes that enable the adaption of gas turbine components for hydrogen application. That’s certainly where AM and digitalization come into play.
II – AM strategies one can explore for implementing a hydrogen economy or to enable green hydrogen fueled gas turbines to start.
“AM plays a number of important roles when it comes to both hydrogen generation (e.f. catalysis) as well as utilization of it as a fuel”, Hryha comments.
Let’s make it easy for outsiders and explain how a gas turbine operates to better understand Hryha’s comment. A gas turbine has three main components: a compressor which takes in air from outside of the turbine and increases its pressure; a combustor that burns the fuel and produces high pressure and high velocity gas and a turbine that takes out energy from the gas coming from the combustor.
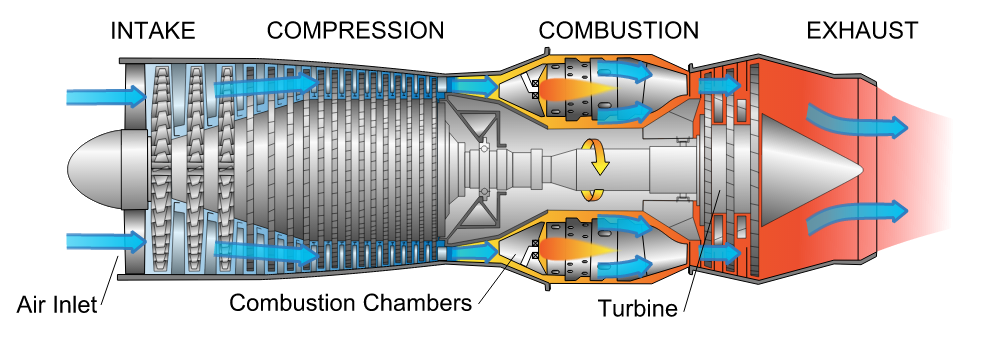
Two of the most important aspects of the AM value chain where industries focus their strategy are design and materials.
The design perspective
“Burning hydrogen gas faces a lot of challenges connected to the high reactivity of the hydrogen gas as well as high temperature flame. Therefore, to facilitate this, novel and significantly more complex design of fuel burners, not feasible or possible to produce using conventional metal forming technologies for modern high-temperature materials, is required to assure proper fuel mix and enable efficient hydrogen burning. Hence, almost unlimited design possibilities, provided by AM, open new ways for manufacturing of complex fuel burners, not possible until now”, Professor Hryha lays emphasis on.
Siemens Energy has specifically worked on these applications. With over 50 industrial 3D printers in-house, Siemens Energy has already achieved several applications of AM and is currently looking to further industrialize their processes. During a conversation with 3D ADEPT Media, Navrotsky highlights how Additive Manufacturing has been pivotal to ensuring the acceleration of design and prototyping of their gas turbines H2 burners:
“In our workshop in Finspong, we did start the extension of H2 capability of medium-size gas turbines with 3rd generation DLE (Dry Low Emission) combustion in 2008. By 2016, we did reach 10% of H2 capability. Implementation of AM for MGT burners design and manufacturing in 2016 significantly speeded up the H2 capability progress. As a result, in 2018, we already achieved 50% H2, and in 2022 75% of H2. In 2023, we are planning to test 100% H2 for certain turbine frames. AM enables design that can manage all mentioned issues related to H2 combustion. Implementation of lattice structure in the burner design does not only enable good mixture of H2 and compressor air, but it also acts as a cooling arrangement – the fuel acts as a coolant. This resulted in the lower metal temperature of the burner during operation. Currently our SGT-600, -700, and -800 gas turbine burners with H2 capability are manufactured with AM technology.”
The materials perspective
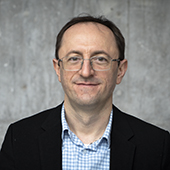
According to Professor Hryha, “[the need for] high-temperature materials, required for such a high-temperature flame, [is] beyond the current state-of-the-art. Here is another advantage of AM: control over solidification and microstructure formation processes during additive manufacturing of the complex component can be used to synthesize novel high-temperature materials.”
As part of a project co-funded by Sweden’s innovation agency Vinnova, Hryha is currently investigating new materials for green hydrogen fueled gas turbines through additive manufacturing. Together with several partners, Hryha will explore critical factors of alloy design, powder characteristics and AM fabrication recipes for successful manufacturing of tailored Ni-based alloys with excellent high-temperature mechanical and corrosion properties. Vinnova said the results of this project will allow Höganäs to introduce new powders on the market for AM, allow Siemens to develop LB-PBF manufacturing of the components for hydrogen fueled gas turbines, and allow to introduce new LB-PBF (EOS) and post-AM (Quintus) processes allowing fabrication of difficult-to-build AM materials.
When asked why the focus is made on Ni-based alloys, Hryha replies that they “are the most suitable material candidates for high-temperature applications thanks to the combination of high strength and stability at high temperatures.” The fact is, “high-performance Ni-base superalloy needed for advanced applications, such as components for hydrogen fueled gas turbines, are very difficult to process by AM without encountering significant cracking issues. We implement a comprehensive and holistic approach to mitigate cracking in advanced high-temperature Ni-base superalloys for high-temperature applications combining three main ingredients: tailored alloy design, dedicated LB-PBF process and post-AM process development. A lot of reported data focus on one of the aspects, however for such a complex material and design, material, AM and post-AM process have to be developed in synergy to assure robust AM manufacturing. LB-PBF provides high freedom of both, design and process control, meaning that smart combination with post-AM HIP process allows us to not only minimize/avoid defects, but also control microstructure and properties by integration of HIP and heat-treatment in one cycle (also, further minimizing manufacturing costs)”, he continues.
While he couldn’t expand much on the project for now, he did share that it is important to clearly understand the physical and technical possibilities and limitations during all three steps to assure successful, economically and technologically feasible AM material, process and post-AM processing.
Other considerations to take into account
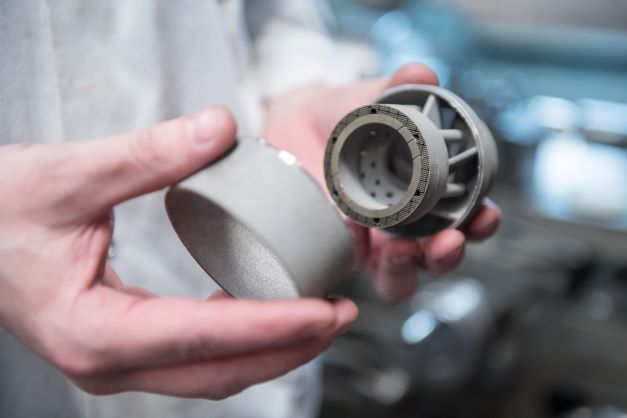
“Many power producers might believe that replacing burners in gas turbines is enough, but whether you’re converting an old plant or building a new one there’s far more to H2-readiness than that. High-hydrogen fuels not only pose challenges for the combustion system of the gas turbine, but also to the gas turbine package and plant as well. The package design must be evaluated to ensure all components and systems are capable of safely running with higher hydrogen contents in the fuel. Upstream of the combustion system, hydrogen fuels can require changes to component materials, pipe sizes, as well as sensors and safety systems. Downstream, the exhaust path must be evaluated. Varying exhaust gas properties can impact heat transfer and corrosion rates, possibly impacting the life of components”, Navrotsky warns us.
As you can see, we have only tackled a tiny part of the problem. Not only is hydrogen still in its infancy, but the use of AM as a technology that can foster its adoption and its effective implementation across the gas turbine industry also requires to take into account the complexity of the technology and its maturity at the current state of the market. As Navrotsky implies, there is still a long way to go given the current considerations to take into account at the design, materials, machines and most importantly standards levels. And the latter can only be effective through cooperation with universities on the one hand, and cooperation with machine and powder suppliers on the other hand.
Concluding thoughts
High expectations are currently placed on hydrogen and its advantages for a climate-safe energy future. In the midst of this media hype, it is fair to say that it is green hydrogen, generated from renewable sources, that will probably deliver the most significant environmental benefits as long as industries and governments can prove its profitability – this may only be the beginning of a new era but the tiny little part of Additive Manufacturing should not be neglected.
This dossier has first been published in the 2022 September/October edition of 3D ADEPT Mag.
Remember, you can post job opportunities in the AM Industry on 3D ADEPT Media or look for a job via our job board. Make sure to follow us on our social networks and subscribe to our weekly newsletter : Facebook, Twitter, LinkedIn & Instagram ! If you want to be featured in the next issue of our digital magazine or if you hear a story that needs to be heard, make sure you send it to contact@3dadept.com