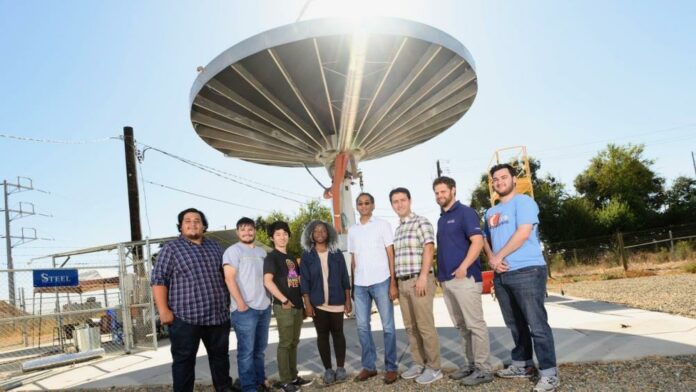
While harnessing energy from the sun is key to a decarbonized world, getting to those higher temperatures needed in industry is often the Holy Grail for industrials. To reach them, they should either use electricity from renewables or high-temperature solar energy.
As part of a three-year, $4.6 million, multi-institution project funded by the U.S. Department of Energy (DOE), Mechanical and Aerospace Engineering Professor Vinod Narayanan will explore green alternatives like solar-thermal power to capture energy while decreasing carbon footprint.
There are two ways to capture energy from the sun: using traditional solar cells, known as photovoltaics, and concentrating solar-thermal energy. Solar-thermal energy uses mirrors to concentrate sunlight onto a receiver, which transfers the energy to a high-temperature working fluid that can generate process heat or run a power cycle. This method can be coupled with less-expensive thermal storage to provide electricity or process heat even at night and is ideal for locations that get a lot of direct sunlight like the Southwestern U.S., Middle East, Northern Africa and Southern Europe.
In the new project, Narayanan and his team will develop 3D-printed high-temperature, high-pressure receivers that can be used to generate power or for renewable industrial process heat. His collaborators include four other universities—Carnegie Mellon University, Pennsylvania State University, the University of Michigan and Utah State University—three companies—Sunvapor Inc., Materials Resources LLC, and AMETEK Specialty Metal Products—and Sandia National Laboratories.
To build a receiver, the team needs something that can withstand extremely high temperatures and pressures, as well as the extreme flux and transients that come as the sun rises and sets every day. They also need a receiver that transfers as much energy as possible to a working fluid.
“You can think about taking sunlight you receive on a summer day and concentrating that 1000 times,” said Narayanan. “If you focus it onto an area of a few inches and you don’t have a mechanism to remove the heat, you can burn through steel. The point of the receiver is to take that heat and transfer it to a working fluid that can do something with that heat—either process heating or power generation.”
Metal AM, a crucial manufacturing process for the project
Making a receiver with metal additive manufacturing is a key component of the project. Because it gets so hot, Narayanan says traditional etching, diffusion and bonding techniques weren’t holding up on previous designs, and the devices would often fail or quickly degrade. Additive manufacturing, commonly known as 3D printing, is a potential solution.
“With additive manufacturing, you can build everything in one go so that you don’t have to do things like welding or brazing to build the component,” said Narayanan. “It also helps you in terms of the longevity, the creep and the fatigue of the receiver, so you’re restricting the amount of failure points.”
“Additive manufacturing allows for freedom of design, use of advanced materials, part consolidation and rapid turn-around from design to net-shape fabrication, in addition to heat exchangers that are ready to test with minimal additional post-processing,” added Tony Rollett, Carnegie Mellon University’s PI for the project.
If successful, he hopes to partner with his colleagues in the College of Engineering to couple his receiver with new thermal storage methods to further decarbonize industry and make these methods viable to industry in new parts of the world.
Remember, you can post free of charge job opportunities in the AM Industry on 3D ADEPT Media or look for a job via our job board. Make sure to follow us on our social networks and subscribe to our weekly newsletter : Facebook, Twitter, LinkedIn & Instagram ! If you want to be featured in the next issue of our digital magazine or if you hear a story that needs to be heard, make sure to send it to contact@3dadept.com