La digiscopie est un néologisme pour la photographie afocale. Le terme consiste à utiliser un appareil photo (numérique) pour enregistrer des images lointaines à travers l’oculaire d’un télescope optique. Les experts en la matière ont souvent besoin d’adaptateurs de digiscopie pour transformer un appareil numérique capable de filmer en caméra numérique. À travers l’exemple de Phone Skope, nous apprenons aujourd’hui que l’impression 3D peut être utilisée dans la production de ces adaptateurs.
Phone Skope, par exemple, est une entreprise dont le siège est aux États-Unis et qui vise à fabriquer des adaptateurs techniques pour presque tous les smartphones, permettant à l’appareil photo d’un smartphone de capturer des images et des vidéos améliorées à travers une lunette pour des applications liées à l’ornithologie, à la faune, à la microbiologie et à l’astrologie. L’expert a fait appel au prestataire de services de fabrication Merit3D, partenaire de Photocentric, qui a utilisé ses 8 imprimantes Photocentric LC Magna et les unités de post-traitement Photocentric, les unités Air Wash L et Cure L1 et Cure L2 pour créer ses adaptateurs de digiscopie moulés sur mesure.
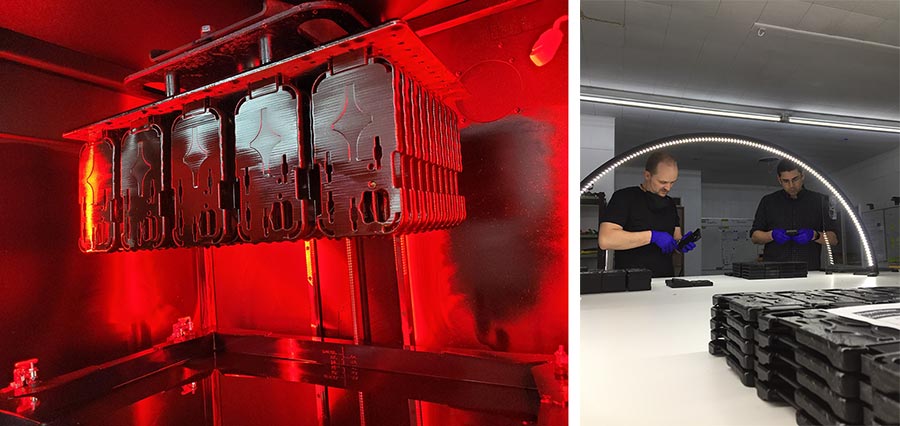
Pour ceux qui ne connaissent pas Photocentric, sachez qu’elle a son siège au Royaume-Uni et qu’elle développe des imprimantes 3D photopolymères basées sur la technologie des écrans LCD. Pour améliorer l’expérience utilisateur de leurs produits, ils s’associent à des entreprises de matériaux comme BASF pour développer de nouveaux matériaux ou CoreTechnologie pour disposer d’un logiciel dédié à leurs imprimantes 3D.
Dans ce cas précis, grâce aux solutions de FA de Photocentric, Merit3D a pu modéliser des adaptateurs et les fabriquer sans avoir recours à un moulage long et coûteux. Merit3D a utilisé la résine Daylight Magna Duramax de Photocentric comme matériau.
Le « design » de Phone Skope est un système simple en deux parties qui est interchangeable et fonctionne avec la plupart des combinaisons de smartphones et d’optiques. Avec seulement quelques petites modifications de conception apportées au modèle 3D, un nouveau boîtier a pu être conçu et imprimé à grande échelle avec un minimum de révisions nécessaires en utilisant la fabrication additive. Cela a permis de réduire les coûts initiaux et d’augmenter considérablement le temps de production, avec une production de qualité constante.
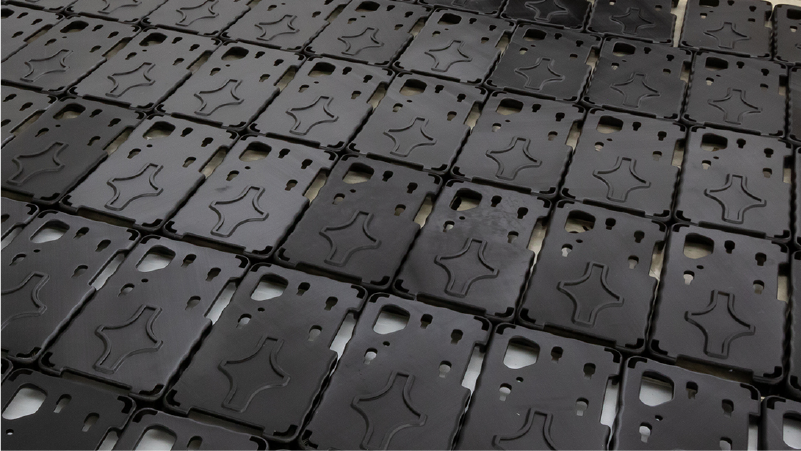
« La fabrication de Phone Skope était confrontée à l’évolution rapide du marché, qui exigeait que ses produits soient compatibles avec un grand nombre de nouveaux modèles de téléphones sortis chaque année« , explique Sally Tipping, directrice commerciale de Photocentric. « Pour créer un adaptateur de digiscopie compatible avec un modèle de téléphone particulier, il fallait créer un moule pour chaque nouveau boîtier, et il y avait toujours un risque que le téléphone lui-même ne soit pas un succès commercial. Phone Skope devait donc choisir les modèles à prendre en charge et créer des moules afin de maintenir sa viabilité. L’impression 3D a été une excellente solution à ce problème, donnant à Phone Skope la flexibilité de mettre rapidement sur le marché une plus grande variété d’adaptateurs sans les implications financières de la création de moules supplémentaires. Les produits Phone Skope sont réputés dans le monde entier pour leur précision et leur durabilité, et il était donc également vital que ces caractéristiques soient conservées sans compromis. »
Photocentric explique également dans un communiqué de presse que la production a nécessité l’utilisation du logiciel Studio et de 4D-additive pour intégrer les supports nécessaires à l’impression dans la conception même des boîtiers.
En fonction de la taille du produit fini, une seule plate-forme Magna pouvait accueillir jusqu’à 52 étuis. Suivant un flux de travail simple au sein de son usine de fabrication, le temps de réalisation de chacune des commandes était de 1 à 2 jours. La nouvelle solution a permis d’économiser des milliers de dollars en frais d’équipement pour la création d’un moulage, et le temps nécessaire à la création d’un nouveau modèle d’étui a également été réduit de 1 à 2 mois à seulement deux semaines. Grâce à la solution de FA, l’ancien minimum de commande de 2000 unités (pour être viable) a également été complètement supprimé.
La LC Magna convient à un large éventail d’applications de fabrication, offrant des avantages significatifs en termes de vitesse d’impression, de volume de fabrication et de coûts. Merit 3D savait également que les impressions de haute qualité produites par la LC Magna réduiraient considérablement le temps consacré à la finition finale, ce qui réduirait encore les coûts et augmenterait la vitesse de mise sur le marché.
« La rapidité et l’agilité de la fabrication additive nous ont permis d’étendre la couverture à un plus grand nombre de téléphones, ce qui nous a ouvert un marché plus vaste« , déclare Jason Bairett, directeur des opérations de Phone Skope.
N’oubliez pas que vous pouvez poster gratuitement les offres d’emploi de l’industrie de la FA sur 3D ADEPT Media ou rechercher un emploi via notre tableau d’offres d’emploi. N’hésitez pas à nous suivre sur nos réseaux sociaux et à vous inscrire à notre newsletter hebdomadaire : Facebook, Twitter, LinkedIn & Instagram !