Ce n’est un secret pour personne qu’un avion est un système complexe qui comprend une longue liste de composants intérieurs et extérieurs conçus pour assurer la sécurité, répondre aux normes de certification, garantir la fonctionnalité et améliorer le confort. Compte tenu des exigences concurrentielles et rigoureuses d’une industrie aussi importante, l’optimisation et l’efficacité de la production revêtent en permanence une importance capitale, d’où l’intérêt croissant pour des procédés de fabrication tels que la fabrication additive (FA). Depuis la toute première utilisation de cette technologie dans les années 1989, la façon dont les pièces aérospatiales sont conceptualisées, conçues et produites a évolué. L’article ci-dessous vise à comprendre comment la technologie a évolué et comment elle est adoptée aujourd’hui par les entreprises aérospatiales et les fabricants de pièces.
L’aérospatiale a été l’une des premières industries à adopter la FA et, compte tenu du nombre croissant d’applications réalisées dans ce domaine, on peut légitimement dire qu’elle a intégré avec succès cette technologie dans ses opérations de production. Si la conception et la fabrication sont deux aspects différents de la production d’une pièce, l’un ne va pas sans l’autre. Ils se renforcent mutuellement pour produire le plus grand impact et il est important de voir comment ils évoluent avec les progrès actuels des technologies.
C’est pourquoi l’article ci-dessous vise à comprendre :
- L’état actuel de la conception dans la production de pièces aérospatiales – et les applications révélant le plus grand impact de la FA
- Quels sont les processus de FA qui transforment le plus la production aéronautique et pourquoi ?
- Jusqu’où la FA peut-elle être poussée dans l’industrie aérospatiale ?
L’état actuel de la conception dans la production de pièces aérospatiales
Prenons l’exemple d’une nervure d’aile : il s’agit d’une pièce structurelle à l’intérieur d’un avion qui aide à supporter une partie des charges de vol et à maintenir la forme lisse de l’aile. Avec ses 2 mètres de long et ses 20 kg, cette pièce a une forme complexe qui doit être aussi légère que possible pour être la plus fonctionnelle possible. Elle était fabriquée par usinage dans un seul bloc d’aluminium jusqu’à ce que les ingénieurs explorent la voie de la FA. Avec la FA, ils imaginent une nouvelle conception – une plaque de métal qui sert de base à la construction de la pièce. Dans la mesure du possible, la pièce est conçue de manière à ce que la plaque puisse être incorporée dans la pièce finale. Grâce à la technologie WAAM, la pièce obtenue par FA présente une surface légèrement ondulée qui doit encore être usinée pour obtenir la pièce finale.
Cet exemple montre que la bonne conception doit aller de pair avec le bon processus de production. Dans l’aérospatiale, les pièces sont complexes et constituées de structures géométriques complexes. Elles forment de petites pièces qui doivent s’emboîter avec d’autres petites pièces. Si la capacité de produire plusieurs pièces à la fois est l’un des avantages les plus cités de la « conception pour la FA » (DfAM), en particulier dans l’industrie aérospatiale, il convient de noter que le résultat de ces conceptions se résume souvent à l’utilisation de la bonne stratégie de conception.
Petit bémol : la boîte à outils de conception comprend des techniques de plus en plus complexes qui nécessitent la prise en compte de la perspective de l’analyse de rentabilité de la pièce à produire. Sur la base de l’exemple ci-dessus, on peut dire que la « consolidation des pièces » est l’une des techniques de conception largement utilisées dans l’aérospatiale pour réduire le poids et les coûts d’assemblage, tout en augmentant l’intégrité structurelle d’une pièce fabriquée de manière additive.
D’une manière générale, « les techniques et stratégies de conception par FA pour les aéronefs sont adoptées différemment dans des secteurs tels que l’aviation civile, l’espace et les véhicules ultralégers dans le contexte de la mobilité aérienne urbaine et de l’eVTOL ».
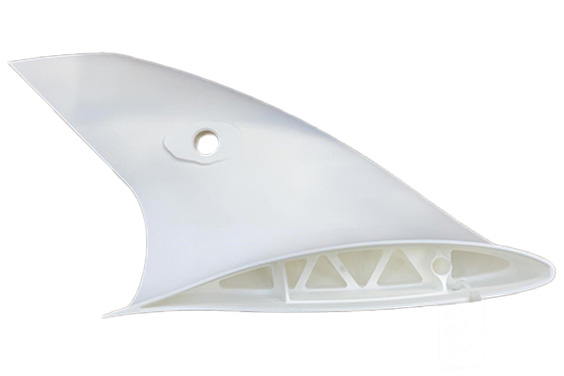
« Pour les véhicules aériens ultralégers, l’économie de poids est, bien entendu, un élément crucial. La FA y contribue grâce à des techniques de conception éprouvées telles que l’optimisation topologique, et toutes les possibilités de conception de FA sont prises en compte pour les composants, y compris les pièces structurelles, et dans différents matériaux. La FA est utilisée de manière exhaustive pour l’optimisation structurelle et l’allègement. La situation est similaire pour les applications spatiales. Dans les deux cas, il est essentiel d’utiliser au mieux l’espace de conception tout en optimisant le rapport entre le poids et la fonctionnalité. Une approche intéressante dans ce contexte consiste à passer à un matériau plus léger ou à un composite au cours de la phase d’exploration de la conception et à compenser ses propriétés matérielles divergentes par des modifications géométriques de la conception de la pièce. Pour l’essentiel, la FA est considérée comme une technologie de fabrication valable et est utilisée comme technologie complémentaire pour un nombre limité de solutions sophistiquées.
En ce qui concerne l’aviation civile, la situation est différente. Actuellement, la majorité des pièces imprimées en 3D ne sont pas conçues pour la FA. La FA est idéale pour l’approvisionnement en pièces polymères à faible criticité pour les avions de l’aviation civile, car les pièces peuvent être imprimées à partir de l’étagère virtuelle, il n’y a pas de gaspillage, et aucun stock ne traîne dans les entrepôts.
Néanmoins, la FA offre une nouvelle approche de la conception pour l’aérospatiale en proposant une alternative économique pour les pièces endommagées des avions. La FA peut fournir des solutions de réparation sur mesure pour ces pièces, en offrant une solution autre que le remplacement et en minimisant la durée d’immobilisation des avions.
Cela montre qu’il ne s’agit pas toujours de trouver les parties complexes qui nécessitent une refonte complète, mais les parties qui ont un sens du point de vue de l’analyse de rentabilité. La bonne approche de la conception est essentielle à cet égard. La refonte complète d’une pièce représente un investissement, et la nouvelle conception nécessitera des efforts supplémentaires pour être acceptée en tant que pièce volante. Les MRO et les compagnies aériennes utilisent le logiciel de FA de Materialise pour numériser le processus de production et utiliser les données disponibles sur des milliers de pièces fabriquées par Materialise pour normaliser les conceptions et se conformer aux règles de sécurité. Souvent, la reconception de pièces existantes n’a pas besoin de recourir à des technologies de conception de FA très complexes et ne nécessite que des modifications mineures des pièces. Dans l’aviation civile, la sécurité est la première priorité, et l’industrie aérospatiale qui utilise la FA doit faire progresser la normalisation de l’impression 3D pour améliorer son profil dans l’aviation civile », explique Erik de Zeeuw, Market Manager Aerospace, Materialise.
Deux autres techniques ont également contribué à l’évolution de la conception aérospatiale : la conception générative (GD) et l’optimisation topologique (TO). Non seulement elles existent depuis longtemps, mais elles présentent également des avantages immédiats en termes de gain de poids et d’augmentation de la valeur lors de l’utilisation de la FA.
Les processus de FA qui transforment le plus la production aéronautique – et les applications qui révèlent le plus grand impact de la FA
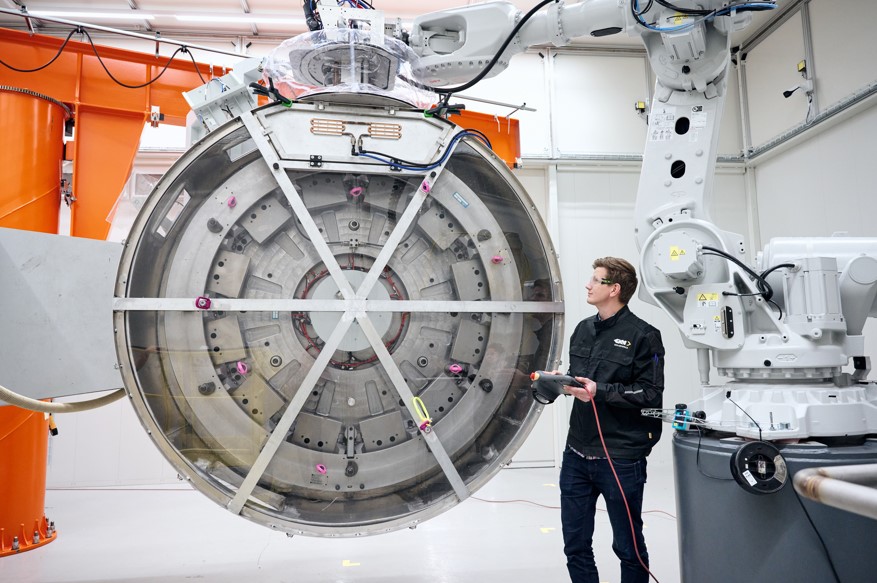
Le nombre de pièces aérospatiales qui volent aujourd’hui varie d’une entreprise aérospatiale à l’autre et dépend de plusieurs facteurs, notamment de la période à laquelle elles commencent à utiliser la technologie. Boeing, par exemple, l’un des principaux acteurs industriels à l’origine des progrès de la fabrication additive, a déjà produit plus de 70 000 pièces imprimées en 3D, tandis que la société spatiale Maxar a déjà envoyé en orbite plus de 2 500 pièces fabriquées de manière additive et que Collins Aerospace, un autre acteur relativement nouveau, a déjà produit plus de 75 pièces imprimées en 3D et a ouvert l’année dernière un centre de fabrication additive d’une valeur de 14 millions de dollars.
Ces statistiques montrent clairement que les entreprises aérospatiales qui utilisent la technologie de FA ont bien compris la valeur ajoutée qu’elle apporte aux pièces légères, aux prototypes fonctionnels et à l’outillage. Il est également clair qu’elles sont prêtes à pousser l’utilisation de la technologie au-delà du prototypage, pour se concentrer sur des pièces fonctionnelles qui peuvent être directement utilisées dans un avion.
D’un point de vue technologique, les matériaux associés aux pièces aérospatiales sont à la fois métalliques et polymères, en fonction de la criticité de la pièce. Si les matériaux polymères peuvent être utilisés dans différents processus de FA, leur sélection dépend toujours de la mesure dans laquelle ils peuvent répondre aux exigences de légèreté avec une résistance élevée afin de réduire les émissions, d’économiser du carburant et d’adhérer aux exigences de sécurité.
C’est la raison pour laquelle les technologies SLA et FDM resteront des candidats idéaux pour la production de prototypes. De même, même si l’impression 3D SLS et la technologie de FA grand format (Large Format Additive Manufacturing – LFAM) puissent être utilisés pour produire respectivement des composants tels que des conduits d’air et d’autres formes d’outillage aérospatial, l’accent est mis de plus en plus sur l’utilisation des technologies d’impression 3D métal pour produire des pièces en série.
Avec plus de 18 processus de FA métal différents connus à ce jour, les technologies de fusion sur lit de poudre basées sur le laser restent les processus de FA les plus largement utilisés. De nouvelles technologies d’impression 3D de métaux continuent de faire leur apparition sur le marché chaque jour, et elles suscitent de grandes attentes en termes de réduction des coûts et de temps de production. En outre, comme le développement de nouvelles technologies est plus rapide que les applications qu’elles peuvent permettre, il est difficile d’évaluer la maturité des autres procédés de FA des métaux qui transforment aujourd’hui la production aéronautique.
GKN Aerospace, un fournisseur aérospatial multitechnologique de niveau 1, s’appuie sur une technologie de FA qui implique la construction couche par couche à l’aide de fils ou de poudres métalliques fusionnés à l’aide de lasers. Le dépôt de métal par laser avec fil (LMD-w) à grande échelle permet de produire des structures complexes et légères. Ces structures optimisent les performances globales des composants aéronautiques, contribuant de manière significative à la réduction du poids, à l’efficacité énergétique et à la capacité de créer des géométries complexes qui étaient auparavant difficiles à réaliser avec les méthodes de fabrication traditionnelles.
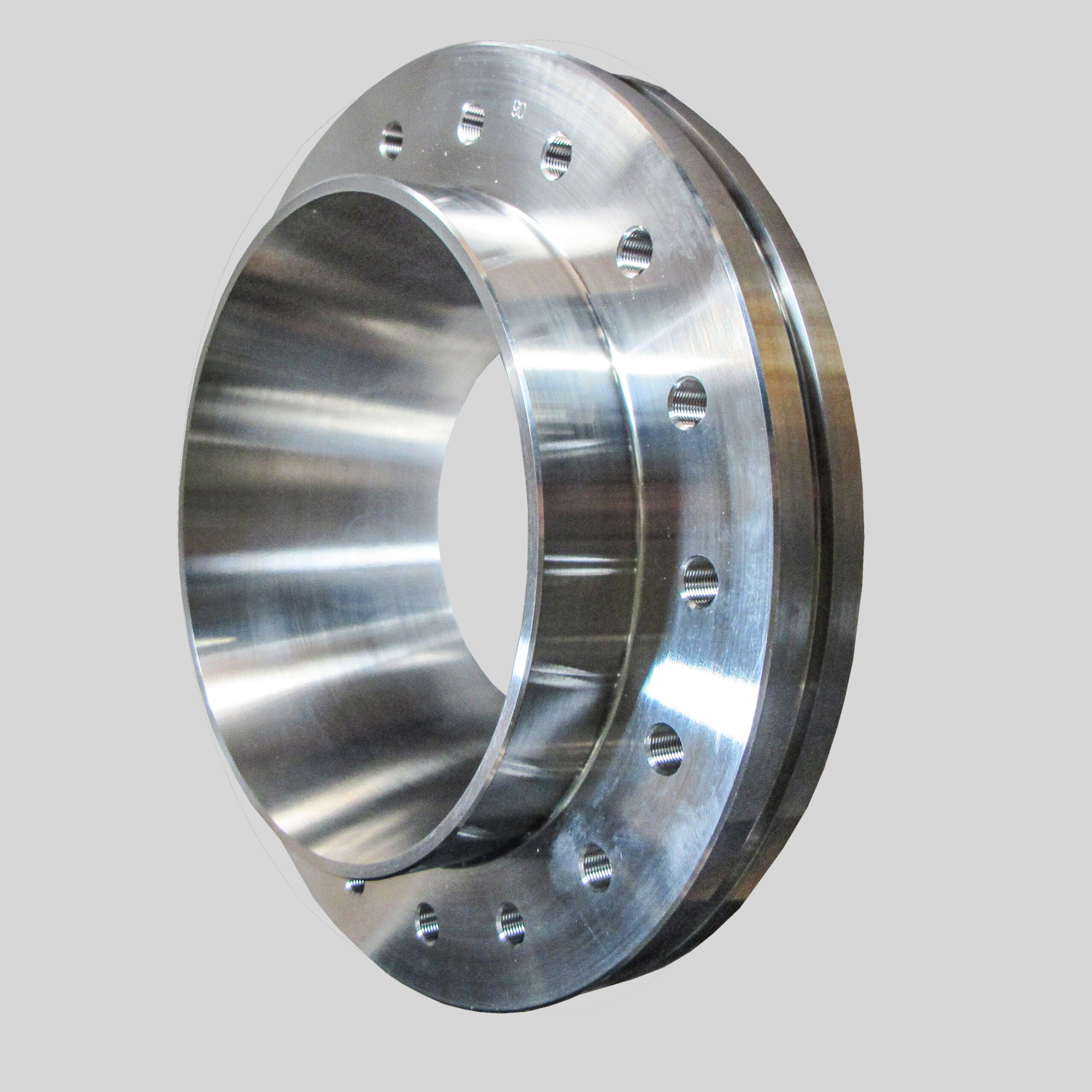
Selon Sébastien Aknouche, responsable des solutions matérielles chez GKN Aerospace en Suède, aujourd’hui, lorsqu’on considère les moteurs d’avion en particulier, quel que soit le procédé de FA utilisé, pour apprécier l’impact de la technologie sur la production aéronautique, il faut être capable d’identifier à court terme les facteurs de transformation suivants :
- Le délai de la demande – conception – fabrication – livraison. Il est probablement réduit à 5 %, voire moins, de l’approche traditionnelle pour une nouvelle demande.
- Le processus comporte moins d’étapes que la fabrication traditionnelle de pièces d’avion.
- La FA nous permet d’utiliser de manière beaucoup plus efficace la disponibilité mondiale déjà limitée des superalliages. Nous pouvons produire 2 à 10 fois plus de moteurs avec la même quantité de métal. Cela réduit à nouveau la quantité de déchets (sculptures).
- Grâce à la FA, le délai de production industrielle n’est qu’une fraction du délai de production traditionnel, où tout changement de la demande peut prendre plus de deux ans à satisfaire.
- La FA permet des changements rapides de la demande et une situation d’approvisionnement beaucoup plus flexible. Cela permettra de réduire considérablement les stocks et de débloquer d’énormes quantités de liquidités actuellement liées aux stocks.
- La FA permet de réduire les coûts pour le client grâce à une plus grande flexibilité de l’approvisionnement, moins de liquidités liées aux stocks, une plus grande sécurité de l’approvisionnement avec moins de sous-absorption et un processus beaucoup plus rapide du nouveau produit au processus industrialisé.
- Tout processus de production de FA constitue un facteur environnemental significatif et positif. Les émissions de CO2 sont considérablement réduites grâce à des processus moins gourmands en énergie et à des transports moins importants, et l’utilisation de nos ressources mondiales est nettement plus efficace.
Cela dit, les pièces d’aéronef doivent être soumises à un processus de certification pour être jugées aptes aux opérations de vol. Ces certifications peuvent provenir de la FAA, de l’EASA ou de l’IASA, en fonction de la région où la pièce sera utilisée. Le paradoxe est que, même si les technologies de FA des métaux sont les processus qui stimulent le plus la croissance de la FA dans l’aérospatiale, le processus de validation pour tout composant métallique reste assez long. Il peut prendre de 7 à 10 ans par rapport aux pièces en plastique imprimées en 3D.
Lorsqu’on lui demande s’il y a des leçons à tirer et à reproduire des pièces imprimées en 3D en plastique pour faire progresser l’utilisation des pièces imprimées en 3D métal, Aknouche répond que ces leçons pourraient être « l’adoption d’une approche de test plus itérative, l’utilisation d’outils de simulation pour les tests virtuels et l’établissement de protocoles de test normalisés ». En intégrant ces pratiques, « l’industrie aérospatiale peut potentiellement réduire le délai de validation des composants métalliques, garantissant ainsi la sécurité et la conformité sans compromettre l’efficacité ».
Plus de 25 systèmes de propulsion de comètes à eau de Bradford Space sont actuellement en orbite. Copyright Bradford Space. Partagé par Materialise.
Néanmoins, les applications qui révèlent l’impact le plus important de la FA restent les composants complexes et légers tels que les pièces de moteur. « Ces pièces bénéficient de la liberté de conception offerte par les procédés de FA, ce qui se traduit par une amélioration des performances, du rendement énergétique et de l’impact sur l’environnement. En outre, la possibilité de regrouper plusieurs composants en une seule pièce imprimée en 3D de conception complexe contribue à la réduction du poids total et à l’amélioration de l’efficacité des avions », ajoute l’expert de GKN Aerospace.
En dehors du segment de la FA métal, Erik de Zeeuw note que « les pièces en polymère à faible criticité ou les pièces susceptibles de se briser à l’intérieur et autour de l’avion sont peut-être celles où la FA se distingue le plus en termes d’impact. Le panneau de décompression de la cabine du Boeing B737 en est un exemple. Les loquets et les goupilles de ce panneau ont tendance à se casser fréquemment. Stirling Dynamics a collaboré avec Materialise pour concevoir un panneau renforcé ayant la même fonctionnalité, mais plus solide et moins susceptible de se casser que la pièce d’origine.
Ces pièces à faible criticité ne sont pas seulement le pain et le beurre de la FA pour l’aérospatiale. Elles fournissent également les données nécessaires pour travailler sur des pièces à haute criticité. Ces données sont utilisées aujourd’hui par les entreprises aérospatiales pour garantir la répétabilité de leurs processus de fabrication. »
Comment l’industrie aérospatiale peut-elle aller plus loin dans l’utilisation de la FA ?

D’après les conversations que nous avons eues avec les experts invités à partager leurs points de vue sur ce sujet, on garde à l’esprit trois domaines d’intérêt principaux : les nouvelles conceptions, les composants structurels des aéronefs et le rapport achat-vol.
En ce qui concerne la conception, le facteur de transformation le plus important qui contribuera à propulser l’adoption de la FA dans l’aérospatiale est celui des nouvelles conceptions. Selon Aknouche, « les nouvelles conceptions de moteurs à réaction, par exemple, les rendront plus légers et plus efficaces, ce qui permettra de réduire les émissions de CO2 à chaque minute de vol de l’avion ». « Même si nous avons pu concevoir et calculer les avantages d’une vision future des nouveaux moteurs, nous n’avons pas été en mesure de les réaliser avant l’introduction de la FA métal », souligne-t-il.
En ce qui concerne les composants structurels des avions, nous avons vu des exemples de pièces imprimées en 3D dont la conception est la réplique parfaite de la même pièce produite précédemment par usinage. L’un des défis que nous rencontrons souvent est que, parfois, la reconception complète de la pièce pour obtenir les avantages bien connus de la FA rend compliquée ou « impossible » la réalisation d’une pièce avec des formes complexes imprimées en 3D qui pourraient être certifiées. En effet, compte tenu de ses exigences réglementaires strictes, il est plus facile pour l’industrie aérospatiale de certifier la conception d’une pièce et de la maintenir pendant toute la durée de vie de l’aéronef. Si on ajoute à cela le problème d’assurance qualité, on atteint un autre niveau de complexité à démystifier. C’est pourquoi, malgré le potentiel de la FA pour les pièces structurelles, nous devrons peut-être attendre un peu plus longtemps, pour que de nouvelles pièces, avec de nouvelles conceptions pour de nouveaux avions, apparaissent avant de dire que nous avons atteint un nouveau niveau de maturation de la technologie.
« Materialise ne se précipite pas pour s’attaquer au marché des composants structurels métalliques à haute criticité. Cela s’explique en partie par les règles de sécurité strictes qui s’imposent dans l’industrie aérospatiale, mais aussi par l’état de préparation de la technologie d’impression 3D elle-même. Cependant, grâce aux antécédents de Materialise en matière de fourniture de pièces en polymère à faible criticité, aux données désormais disponibles grâce à notre travail et aux investissements de grandes entreprises aérospatiales telles que GKN, la FA est envisagée pour les composants structurels des aéronefs. La voilure de l’avion Aviation Alice conçue par GKN n’est qu’un exemple des travaux menés dans ce domaine. Parallèlement, Materialise et d’autres partenaires travaillent à la création d’une voie permettant de qualifier le processus de production de pièces métalliques imprimées 3D. Le groupe composé d’experts de l’aérospatiale et de la FA fournira un livre blanc comme premier effort pour rédiger une pratique recommandée SAE Aerospace pour l’utilisation de la surveillance du processus in situ pour valider un processus de FA. Ces efforts renforceront la maturité technologique de la FA et inciteront un plus grand nombre d’entreprises aérospatiales à envisager la FA pour les pièces hautement critiques des compagnies aériennes », commente de Zeeuw.
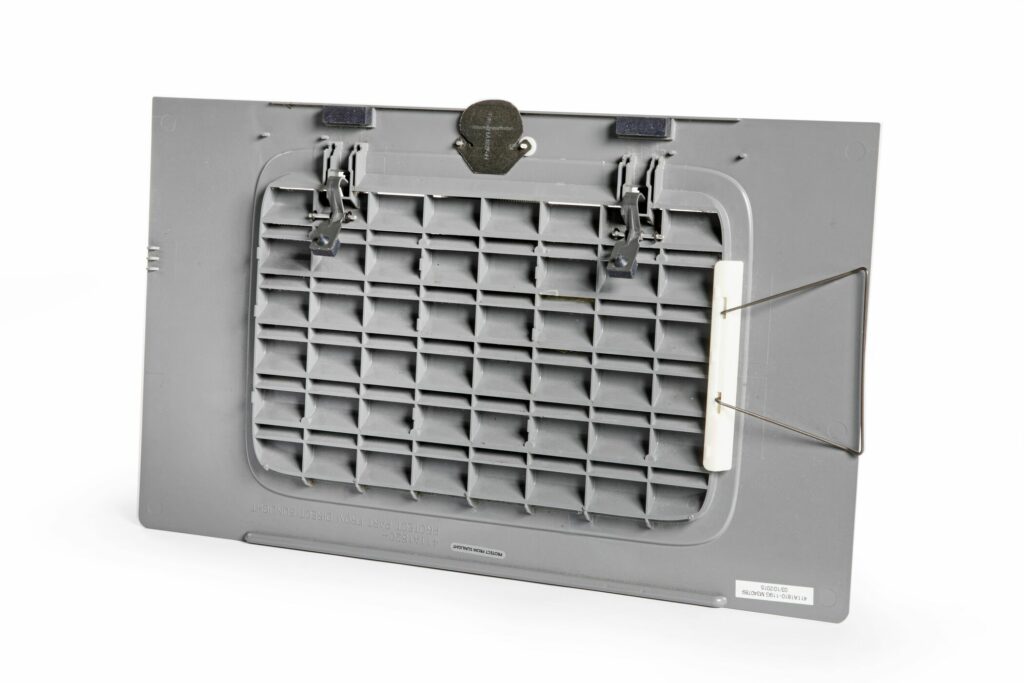
En ce qui concerne le ratio buy-to-fly, l’expert de GKN Aerospace a confirmé que « l’amélioration du ratio buy-to-fly » pourrait être un facteur clé de transformation de l’industrie à long terme : « Le rapport de poids entre un substrat et une pièce finie nous permettra d’utiliser le métal disponible de manière encore plus efficace et de réduire les déchets. En effet, plus le processus de FA devient efficace et plus le ratio « acheter pour voler se rapproche de 1,0, moins il y a de déchets de matériaux. »
« Il n’y a probablement pas de frontière claire quant à notre avenir, mais nous ne serons pas en mesure de fabriquer des pièces sans matériau, mais peut-être des pièces avec un « ratio achat-vol » proche de 1,0, et les délais de livraison ne seront pas nuls, mais très courts, et la production n’aura probablement pas d’émissions nulles, mais très faibles. La question est plutôt de savoir dans quelle mesure nous nous rapprocherons de ce stade idéal. Pour le savoir, il faudra suivre le développement », conclut-il.
Il est évident que d’autres domaines d’intérêt auraient pu être mentionnés. En fin de compte, n’oublions pas que la façon dont la FA progresse dépend de l’acteur qui l’utilise.
Ce dossier a été initialement publié dans le numéro de Janvier/Février de 3D ADEPT Mag.
Notes de l’éditeur
GKN Aerospace et Materialise collaborent sur plusieurs projets concernant la certification et la production additive d’aérostructures fonctionnelles et critiques pour le vol. Cependant, aucune des deux entreprises ne savait que l’autre participait à ce dossier.
GKN Aerospace a été invitée à partager ses connaissances sur ce sujet, car son expertise réside dans l’utilisation de la fabrication additive pour optimiser les processus de conception et de production des aéronefs. L’entreprise a déclaré que son dernier projet concernait le développement de techniques avancées de FA pour des composants structurels critiques, démontrant l’impact profond de ces techniques sur la flexibilité de la conception et l’efficacité de la fabrication. En intégrant la FA dans notre flux de travail, nous avons réalisé des progrès notables en matière de réduction de poids, de consolidation des pièces et de performance globale du système.
Quant à Materialise, elle a maintenant pleinement développé son offre de pièces de rechange pour les cabines à faible criticité. Au cours des dix dernières années, elle a acquis un énorme lac de données qui prouve la cohérence de la technologie, du processus, des matériaux et des machines que nous utilisons. Même si nous ayons certifié le processus il y a environ cinq ans, obtenir des pièces imprimées sur un avion existant n’est pas aussi facile qu’il n’y paraît compte tenu des exigences strictes de l’industrie. L’entreprise continue de collaborer avec des sociétés aérospatiales pour faire progresser les domaines clés de l’industrie aérospatiale. Outre GKN Aerospace, l’un de ses récents partenariats a été signé avec Stirling Dynamics.