Le centre de recherche et de développement Naddcon a récemment intégré l’imprimante 3D multi-matériaux ExAM 255 d’AIM3D dans le logiciel de conception NX de Siemens.
L’outil NX contient des solutions complètes de CAO, de FAO et d’IAO, déjà utilisées pour la fabrication conventionnelle de composants dans l’industrie de l’usinage. Cette intégration de NX n’est que l’une des nombreuses options du concept de machine ouverte des imprimantes 3D multimatériaux d’AIM3D.
Alors, comment ont-ils procédé et, surtout, pourquoi ?
Voici pourquoi.
Naddcon ouvre une nouvelle possibilité pour le fonctionnement des imprimantes 3D et la génération de code G. L’équipe a l’ambition de cartographier un processus d’impression 3D en tant que chaîne de processus numérique continue, de la conception du composant à la production et au post-traitement.
Le pont entre le micrologiciel de la machine AIM3D et l’environnement CAO/FAO de Siemens NX intègre l’imprimante 3D en tant que machine de traitement FAO. Grâce aux approches CAO, FAO et IAO fournies par NX, les composants 3D peuvent être optimisés en termes de bionique, de surfaces de forme libre, de densités sélectives (stratégies de remplissage variables) et de réductions de poids (par exemple, structures en grille).
Les fibres peuvent également être disposées de manière optimisée par rapport au flux de force, qui définit la rigidité ou l’élasticité et la capacité de charge mécanique. En outre, un système de base de données et des modèles de simulation puissants sont disponibles. Cela signifie que l’ensemble du processus d’impression 3D, de la conception à la production, peut être mieux contrôlé, que les composants peuvent être conçus de manière optimale et qu’une reproductibilité très élevée peut être obtenue. En général, on peut dire que NX permet une simulation exacte de la machine. Plus précisément, cela signifie que les vitesses de déplacement, les performances de l’extrudeuse et les températures peuvent être contrôlées avec une précision extrême en fonction de la géométrie du composant.
Un exemple clé d’opportunité désormais possible : l’usinage de surface de forme libre dans l’impression 3D CEM
Le dépôt multiaxial est un mot clé de l’usinage de surface de forme libre. Développé à l’origine par DMG Mori pour le soudage par faisceau laser, cet outil a depuis été étendu au FDM/FFF. Dans le cas de la modélisation par dépôt en fusion, des brins de matériau sont déposés sur une surface. Ces brins sont obtenus en faisant fondre un polymère et en l’extrudant en continu à travers une buse, puis en durcissant le matériau par refroidissement à la position souhaitée du plan de travail. L’assemblage d’un composant s’effectue généralement par la création répétée d’un plan de travail à la fois, ligne par ligne, puis en déplaçant le plan de travail vers le haut de manière à créer une forme couche par couche. NX permet de générer des parcours d’outils le long de surfaces courbes. Il est ainsi possible de générer de véritables trajectoires en 3D, qui créent des plans indépendamment les uns des autres. L’utilisation de cette technologie dans le développement de processus permet d’éliminer l’effet d’escalier typique des processus d’AM. Le résultat est un véritable contour en 3D d’un corps solide.
Voici comment.
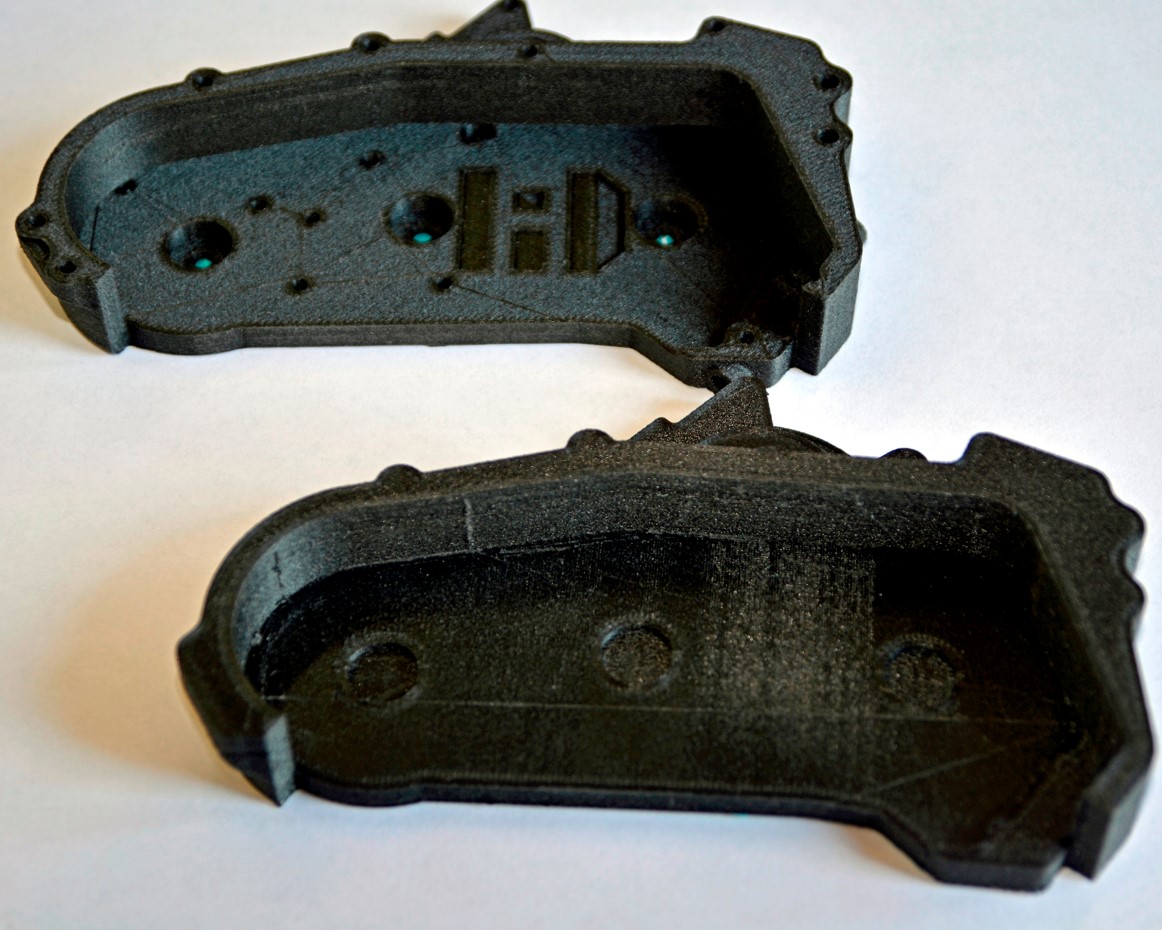
Sebastian Kallenberg de Naddcon a conçu les étapes nécessaires à l’intégration à partir d’un composant standardisé en PA6 GF30 (démonstrateur), dont la conception devait être optimisée à l’aide de NX.
La première étape a consisté à construire un modèle cinématique de l’imprimante 3D en intégrant le modèle CAO de l’ExAM 255 dans NX, ainsi qu’à définir les axes cinématiques et à déterminer le point zéro de la machine. Le modèle cinématique permet de simuler les trajectoires de l’outil avant le processus de production réel.
L’étape suivante a consisté à générer la trajectoire de l’outil pour l’extrudeuse du système AM. Il s’agit de générer des trajectoires en fonction des opérations d’usinage et de la géométrie des composants.
La troisième étape a été la simulation de la machine ExAM 255, c’est-à-dire la simulation de la trajectoire de l’outil avec les mouvements d’axe associés du modèle de machine. L’application du matériau ainsi que les collisions potentielles de la machine peuvent également être simulées. L’aspect principal ici est la programmation d’un post-processeur pour traduire les trajectoires d’outils NX en un code numérique G que l’imprimante 3D peut interpréter.
Un code G se compose de conditions de trajectoire (mot G) et de fonctions supplémentaires (mot M), chacune d’entre elles étant associée à un mouvement ou à une action. La combinaison de ces commandes permet à l’imprimante 3D de comprendre le modèle qu’elle doit suivre pour produire la pièce. Un code G est un langage de programmation utilisé pour programmer les machines-outils à commande numérique.
Dans l’impression 3D, il est généralement généré automatiquement par le logiciel de découpe lorsque la conception est convertie en fichier STL. La programmation post-processeur permet d’effectuer des réglages spécifiques à la machine afin d’améliorer le contrôle du processus. Avec NX, cependant, le format STL n’est plus nécessaire, car le processus utilise des solides qui sont soit directement générés dans NX, soit importés à partir d’un autre système de CAO.
N’oubliez pas que vous pouvez poster gratuitement les offres d’emploi de l’industrie de la FA sur 3D ADEPT Media ou rechercher un emploi via notre tableau d’offres d’emploi. N’hésitez pas à nous suivre sur nos réseaux sociaux et à vous inscrire à notre newsletter hebdomadaire : Facebook, Twitter, LinkedIn & Instagram ! Si vous avez une innovation à partager pour le prochain numéro de notre magazine numérique ou si vous avez un article à faire connaître, n’hésitez pas à nous envoyer un email à contact@3dadept.com.