The announcement marks a key milestone for the Italian AM company that looks back over seven years of continuous improvement, and moves forward in a new facility and with a renewed brand identity.
Additive Manufacturing company Caracol is celebrating several milestones. The company that specializes in Large-Format Additive Manufacturing, recently inaugurated its new facilities, after 7 years of existence. The opening comes alongside the official launch of Heron AM, an integrated hardware and software Large-Format Additive Manufacturing platform completely developed in-house.
Our launch wants to highlight a key moment of change, as Caracol has been transforming behind the scenes. Today we announce we’ve moved into a new home, our HQ has moved to Barlassina (MB) that has allowed us to expand our team and technologies, and we are glad to finally present Heron AM to the world. Our new HQ in Barlassina (MB) is now home to a growing team with over 35 heterogeneous individuals, with a set of very diverse backgrounds, skills and capabilities – which we believe is one of the keys to our growing success. It is also home to over 7 Heron AM platforms in their varied configurations – including insulated cells for high-performing polymers or with the 7th axis structure to extend size up to 15-meter parts. Within our space we have a dedicated post-production area, with robotic CNC, as well as a Quality department, with state-of-the-art equipment to inspect and control both the process and all manufactured parts, in accordance with the AS/EN 9100 standard, Caracol explains in a press release.
As far as Heron AM is concerned, you may already have heard about the technology capabilities through these marine applications. Designed with an approach based on applications in mind, the technology already combines over 29000 hours of printing, and 150 + projects with clients across the most demanding industries: aerospace, automotive, energy, marine and more.
One of the key strengths of the platform is a lightweight and compact extruder, which can process a wide range of polymers and composite materials in pellet form.
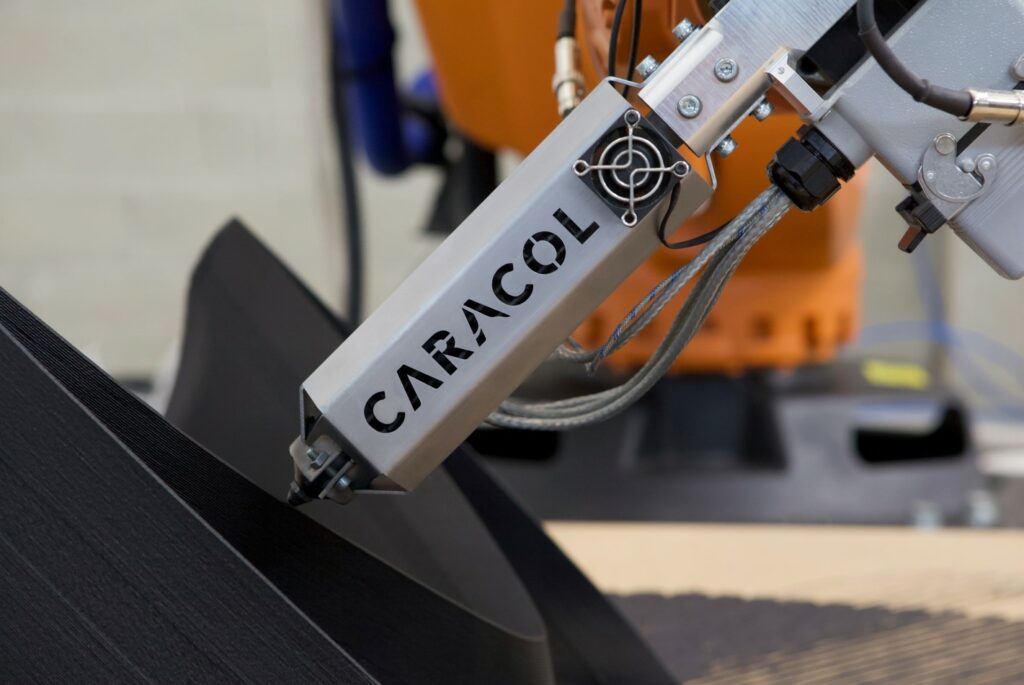
Other specifications include:
Features | Description |
Interchangeable nozzle | Ranges from 1 to 7 mm |
Extruder weight | Less than 20kg |
Max output | <15kg depending on nozzle, materials and other aspects. |
Size | 700 x 280 x 140 mm |
Max extrusion temperature | 350°C |
“We are now ready to launch our international expansion, scaling up to deliver our innovation and the benefits of LFAM across the world. We are extremely excited for what’s ahead”, CEO, Francesco De Stefano concludes.
Remember, you can post job opportunities in the AM Industry on 3D ADEPT Media free of charge or look for a job via our job board. Make sure to follow us on our social networks and subscribe to our weekly newsletter : Facebook, Twitter, LinkedIn & Instagram ! If you want to be featured in the next issue of our digital magazine or if you hear a story that needs to be heard, make sure you send it to contact@3dadept.com